Tabla de contenido
- Detailed explanation of bucket pin types: from standard pins to high-strength alloy pins
- Bushing types and application scenarios
- Bushing wear characteristics and judgment method
- Matching relationship and selection standards between bucket pins and bushings
- Bucket pin and bushing selection guide under different working conditions
The wear resistance and structural integrity of the bucket pins and bushings are directly determined by their matching accuracy, material selection and processing technology. Once abnormal wear occurs, it is not only complicated and costly to replace, but also may affect the stability and safety of the whole machine structure.
From the perspective of project operation, the maintenance status of excavator pins and bushes determines the operating efficiency and downtime frequency of the equipment, which in turn affects the construction cost and schedule progress. Many equipment managers only realize their importance after the failure occurs. By mastering the types, structural differences, selection principles and maintenance methods of bucket pins and bushings in advance, they can effectively reduce maintenance risks and improve the overall performance of the equipment.
GFM systematically analyzes the types, material processes, adaptability to the use environment, selection methods and maintenance techniques of bucket pins and bushings, and combines GFM’s manufacturing plant’s many years of practical experience and customer cases to help you gain a deeper understanding of this “small but critical” mechanical partner.
Detailed explanation of bucket pin types: from standard pins to high-strength alloy pins
The bucket pin is one of the most core components of the excavator connecting the boom, dipper rod, connecting rod and bucket. It not only needs to withstand high-intensity impact loads, but also must maintain high stability and reliability in frequent rotation and swinging. With the diversification of work requirements, the structure, material configuration and surface treatment process of the bucket pin are constantly evolving to meet the use requirements under different working conditions.
Structural classification
Straight Pin: This is the most basic and common type of bucket pin, widely used in small and medium-sized excavators. Its two ends are generally flat or equipped with retaining ring grooves, fixed by bolts, pins or pressure plates. The advantages are easy processing and strong versatility, but its lateral force resistance performance is average under heavy load conditions.
Step Pin: The step pin is designed with a diameter change at one end or the middle section of the pin body, and is often used in situations where one side is required to be firmly positioned, such as the connection between the bucket arm and the connecting rod. The step design can provide a more stable force fulcrum to avoid axial displacement or offset deformation caused by long-term work.
Hollow Pin: This type of bucket pin is hollow inside and can be used to reduce the load of the whole machine, set up lubrication channels or for embedded sensor wiring. It is especially used in intelligent excavators and directional lubrication systems, but its processing accuracy and durability requirements are higher, and it is commonly found in imported or high-end brand equipment.
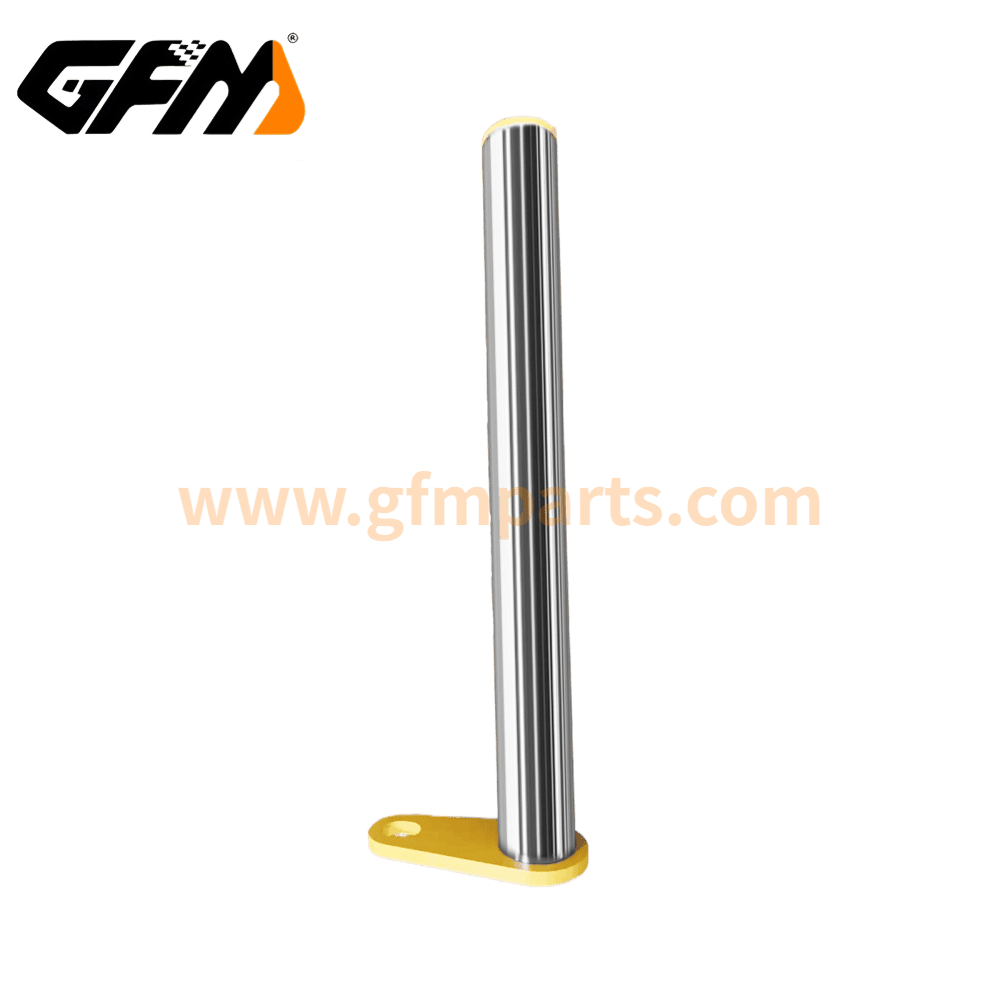
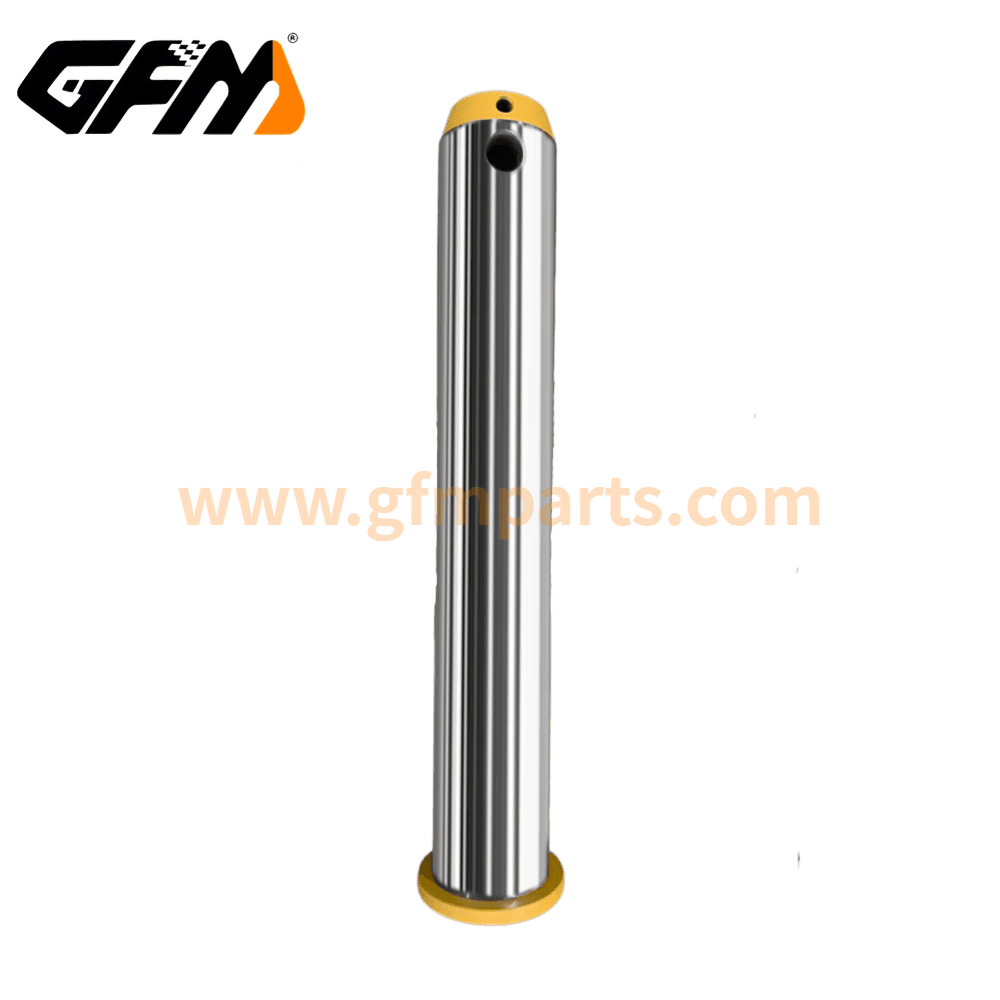
Material analysis
The materials used for bucket pins must take into account strength, toughness and wear resistance at the same time. The current mainstream materials include:
45# steel: a common material in carbon structural steel, with low cost and good processing performance, suitable for scenes with light loads and high replacement frequency. After heat treatment, it can reach HRC40~45, but the wear resistance is medium.
40Cr: widely used in mid-to-high-end bucket pins, with excellent mechanical properties after quenching and tempering, and significantly improved yield strength and bending resistance, suitable for high-frequency and high-load engineering operations.
20CrMnTi alloy steel: This is a carburized steel type. After carburizing, its surface hardness can reach HRC58 or above, while maintaining good toughness in the core, especially suitable for bucket pins that require high wear resistance and impact resistance.
Stainless steel (such as 304/316): Although it is rarely used, it still has application advantages on small excavation equipment in humid, highly corrosive or food and chemical fields.
Surface treatment process
Surface treatment is an important process to improve the durability of bucket pins. Different treatment methods can cope with different environmental challenges:
High-frequency quenching: Use induction current to heat the surface to above 1000°C and quickly quench it to form a martensitic structure, significantly improving the surface hardness. It is commonly used for 40Cr bucket pins with a treatment depth of 1~3mm.
Chrome plating: A hard chrome layer is formed on the surface of the pin shaft by electrochemical means to reduce friction and enhance corrosion resistance. It is suitable for harsh working conditions such as dust and high temperature.
Nitriding: A low-temperature nitriding process with a treatment temperature lower than quenching can effectively improve fatigue strength and surface hardness, and maintain core toughness.
Electrophoretic coating and spraying: Mainly used for appearance beauty and rust prevention. Although it does not improve wear resistance, it can effectively block the oxidation process and extend the storage cycle.
Bucket pin selection recommendations for excavators of different tonnages
The size of the bucket pin is usually closely related to the tonnage level of the excavator. The following are some recommended configurations:
Excavator tonnage | Recommended bucket pin diameter | Recommended material |
6-ton class | φ40~45mm | 45# steel + quenching |
13-ton class | φ60~65mm | 40Cr + high-frequency quenching |
20-ton class | φ80~90mm | 20CrMnTi + carburizing |
Above 30 tons | φ100~110mm | Alloy steel + nitriding treatment |
Special purpose bucket pin
In certain specific operating environments, the bucket pin needs to have stronger impact bearing capacity and special structural design:
Rock bucket bucket pin: suitable for heavy rock buckets, it needs to have extremely high impact resistance, usually made of 40CrNiMo or 42CrMo materials, and deep quenched and anti-corrosion coating treatment.
Hammer bucket pin: The core component connecting the breaker and the mechanical arm, with a thicker diameter and longer length, is designed to resist high-frequency vibration and torsional fatigue.
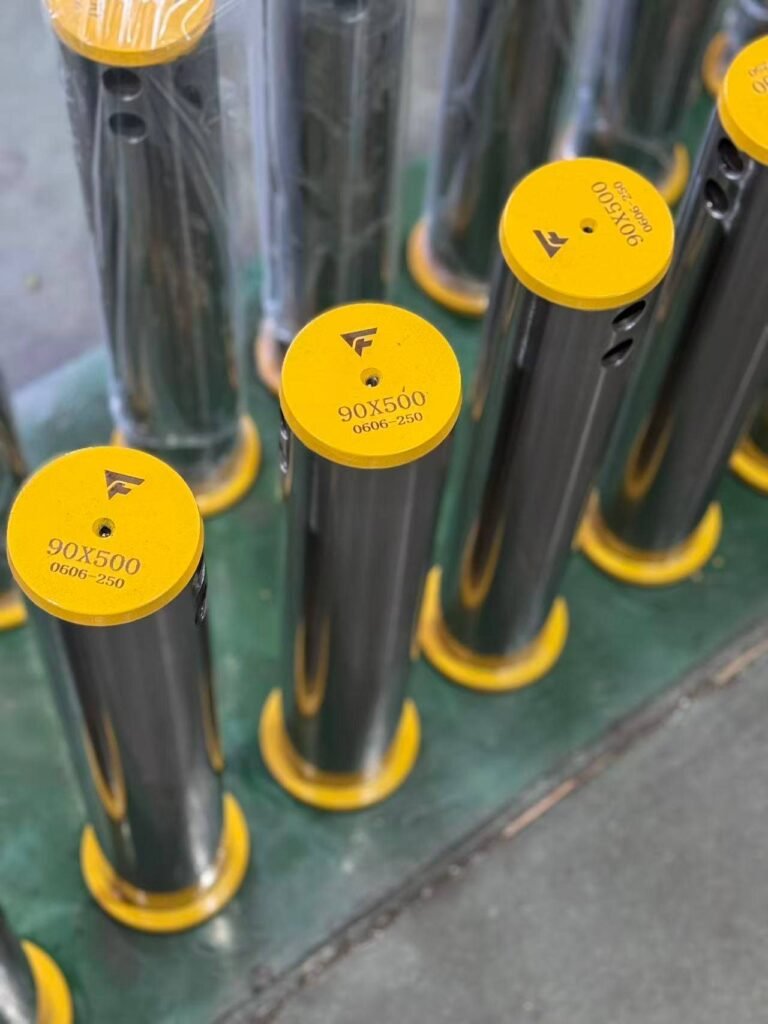
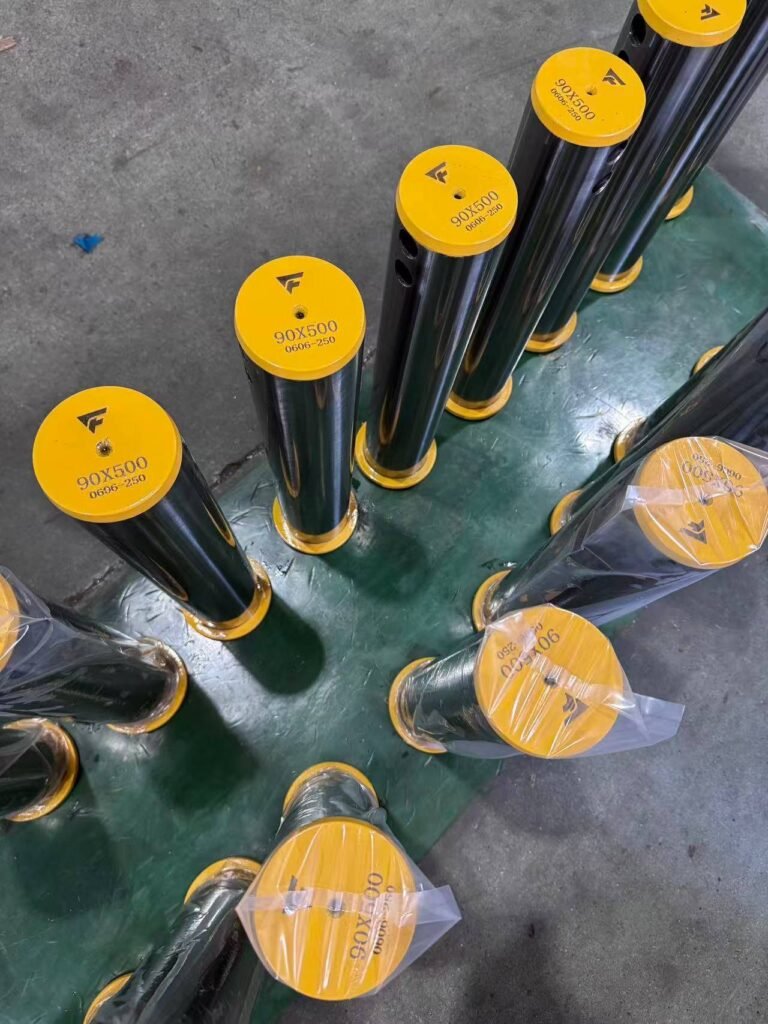
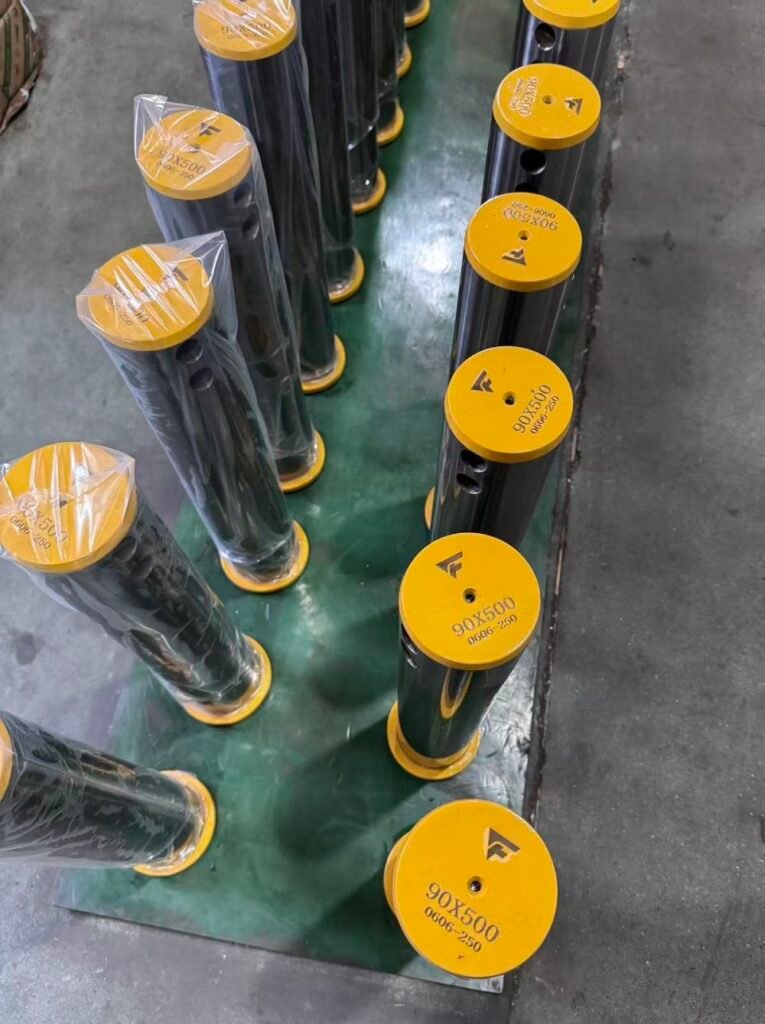
Bushing types and application scenarios
The bushing mainly plays the role of “bearing + protection” in the excavator structure. It is nested in the hole of the connection part to provide support and guidance for the bucket pin or shaft, while preventing the hole from being worn or damaged. High-quality bushings can not only significantly extend the service life of the bucket pin, but also effectively reduce the subsequent maintenance costs and the risk of equipment downtime.
Common structural types
Solid Bushing: Made of solid metal forging or casting, it has high structural strength and is suitable for heavy loads and high impact conditions. Its surface is often quenched, chrome-plated or nitrided to improve wear resistance.
Split Bushing: Also known as a split bushing, it consists of two halves, which is easy to replace and install quickly. It is often used in parts with high maintenance frequency, such as bucket shaft holes.
Self-lubricating Bushing: Embedded with graphite, PTFE, copper powder or lubrication groove design, reducing lubrication frequency or eliminating lubrication, especially suitable for harsh environments with high dust and difficult to maintain grease.
Inlaid Bushing: Use carbide sheets or high-hardness ceramics embedded in the friction surface of the bushing to improve wear resistance and high temperature resistance, commonly used in heavy-duty bucket parts of mines and tunnel engineering.
Differences in materials and performance
The performance characteristics of different bushing materials are as follows:
Material type | Characteristic description | Typical application scenarios |
Gray cast iron (HT250) | Low cost, easy processing, but average strength and wear resistance | Light equipment or auxiliary mechanism |
Bronze (ZCuSn10P1) | Excellent wear resistance, strong friction reduction ability, good lubricity | Slewing platform, connecting rod connection |
Alloy steel (such as 20Cr) | High strength and toughness after heat treatment, strong impact resistance | Heavy-duty bucket arm hinge point |
Copper alloy coated steel back | Bimetallic structure, both pressure bearing and lubricity | Self-lubricating bushing |
Engineering plastics (nylon, POM) | Light weight, suitable for small and medium-sized equipment, good corrosion resistance | Rainforest, wetland environment |
Application location and performance matching
In different structural nodes of the excavator, the size, thickness and surface treatment of the bushing will be designed differently according to the location and load requirements. For example:
- Jointing point between boom and dipper rod → High impact area, it is recommended to use alloy steel integral bushing + high frequency quenching.
- Bucket connecting shaft hole → Considering the convenience of disassembly and assembly, split self-lubricating copper bushing is preferred.
- Dipper rod and cylinder connection → Precise matching tolerance and good lubrication performance are required, and copper alloy bimetallic sleeves are mostly used.
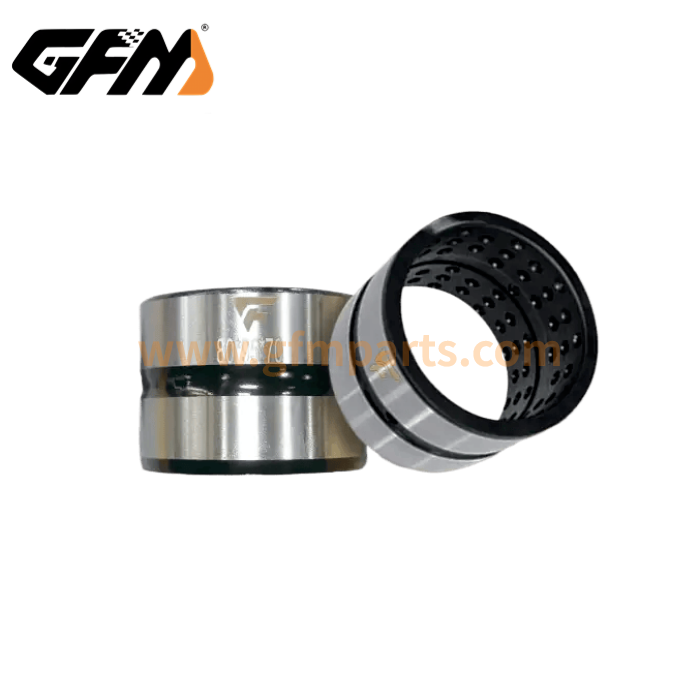
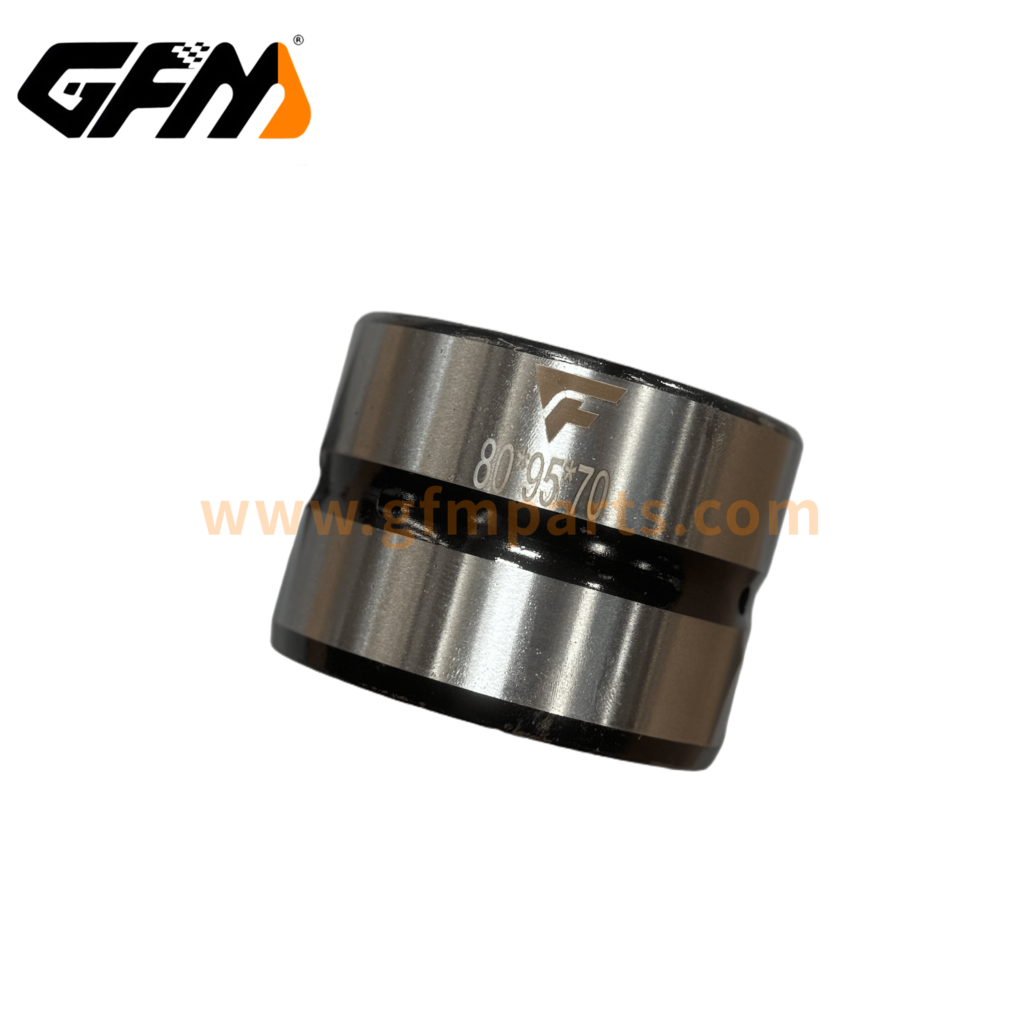
Bushing wear characteristics and judgment method
Although the bushing does not directly carry the work, it is very easy to wear due to continuous friction, and its life is closely related to the bucket pin matching clearance. Common wear forms include:
- Axial deformation: manifested as axial looseness, causing bucket pin to jump;
- Elliptical wear: Deformation of matching hole causes eccentric movement, affecting the accuracy of hydraulic action;
- Metal peeling: Metal particles fall off the surface, often caused by insufficient lubrication or impurity intrusion.
Judgment method:
- Use a vernier caliper to measure the gap between the bucket pin and the bushing. Generally, the gap of the new assembly is 0.1~0.3mm. If it exceeds 0.5mm, it is recommended to replace it.
- On-site experience method: Use an iron rod to pry the end of the bucket pin. If the shaking amplitude exceeds 5mm, it usually indicates that the bushing is severely worn.
Selection suggestions and maintenance tips
- Whenever the bucket pin is replaced, the bushing should be checked and replaced simultaneously to ensure coaxiality and tight fit;
- Use high-quality grease, especially in dusty or humid environments, regularly clean the oil filling port and add grease;
- High-frequency operation equipment can use self-lubricating copper sleeves to reduce maintenance frequency;
Matching relationship and selection standards between bucket pins and bushings
The matching between bucket pins and bushings is not only related to the flexibility and stability of moving parts, but also determines the working efficiency and service life of the whole machine. If the match is too loose, it is easy to cause impact, noise and eccentric wear. If it is too tight, it may cause jamming, heating or even damage.
The importance of matching clearance
The so-called “clearance” refers to the gap between the bucket pin and the bushing. Ideally, this gap should be large enough to accommodate the lubricating oil film to form sliding friction, but not large enough to cause obvious shaking.
Recommended initial installation clearance:
- Small excavator: 0.1mm~0.2mm
- Medium excavator: 0.15mm~0.25mm
- Large excavator: 0.2mm~0.35mm
The clearance should be fine-tuned according to the bucket pin diameter, material thermal expansion coefficient, and usage scenario. For example, in a high temperature and continuous high load environment, a slightly larger clearance is recommended to reserve space for thermal expansion.
Influence of material thermal expansion and matching
Bucket pins and bushings of different materials have different thermal expansion coefficients. For example, when a steel bucket pin is combined with a copper bushing, the thermal expansion coefficient of copper is higher, which may cause the bushing to expand and jam the bucket pin during high temperature operation. Therefore, the material combination should be fully considered at the beginning of the design, the clearance should be adjusted, and the appropriate lubrication method should be selected.
Example: The consequences of improper matching
A customer replaced a batch of bucket pins during use. Although the size was the same, the severely worn bushing was not replaced at the same time, resulting in the new bucket pins quickly showing uneven wear and scratches. After measurement, it was found that the matching clearance exceeded 0.7mm, and the lubricating oil film could not be formed, resulting in accelerated wear due to dry friction. In the end, all the pin sleeves had to be replaced at the same time and the machine had to be shut down for maintenance, resulting in a loss of more than 30,000 yuan.
Experience summary: The use of bucket pins and bushings is “paired logic”, and neither is indispensable. Especially in heavy loads, frequent movements or high temperature and humid environments, material compatibility and matching of matching clearances should be given priority.
On-site inspection and assembly skills
Use an inside micrometer and an outside micrometer to measure the bushing aperture and bucket pin diameter respectively to avoid visual judgment errors;
Before installation, the bucket pin can be frozen (such as below -20℃), and then quickly installed into the heat-expanded bushing to improve the interference fit accuracy;
Apply a thin layer of high-temperature grease to help the initial running-in and reduce early wear;
After installation, the rotation should be smooth and unobstructed, and there should be no looseness in the shaking test.
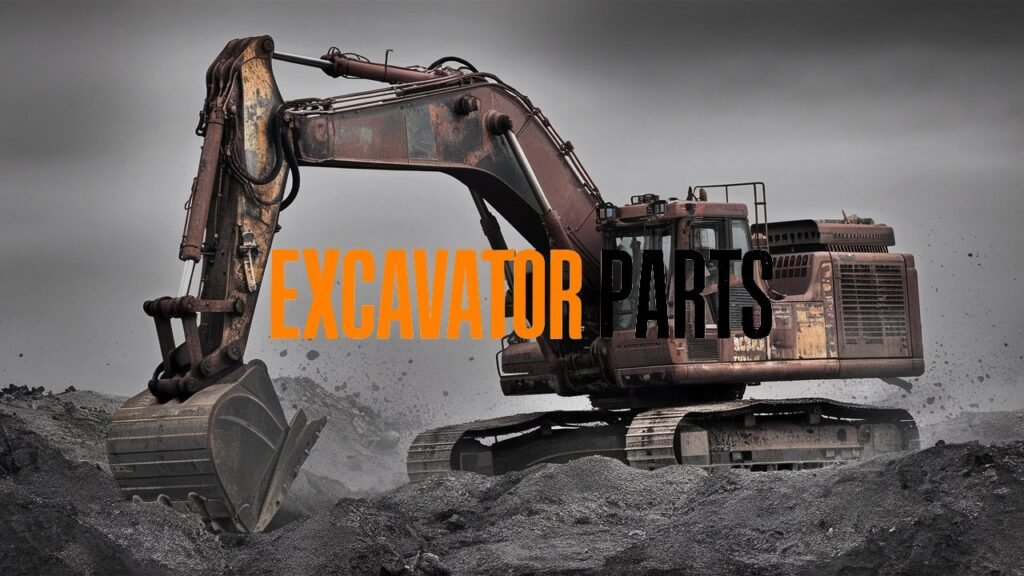
Bucket pin and bushing selection guide under different working conditions
The construction environment faced by excavators around the world is extremely complex, from ice and snow frozen soil in the north to high temperature and humidity in the south, from hard rock in mines to urban drainage construction, each working condition has different technical requirements for bucket pins and bushings. If the selection is improper, it will directly affect the equipment’s operating efficiency, component life and maintenance costs. Therefore, it is particularly important to classify and recommend suitable bucket pins and bushing configurations in combination with typical working environments.
Heavy-load mining and rock operations
Características: high impact strength, high dust in working conditions, and long-term high-load operation of equipment.
Recommended configuration:
- The bucket pin material is 42CrMo or 20CrNiMo, which has high yield strength and good toughness;
- The surface treatment adopts deep carburizing + chrome plating or nitriding treatment to improve impact resistance and corrosion resistance;
- The bushing is recommended to use an integral high-carbon alloy steel bushing + embedded graphite lubrication groove design to enhance wear resistance;
- The lubrication system is equipped with a centralized oil supply structure, and grease is added once every 4 hours to prevent metal dry friction.
Urban municipal and construction construction
Características: frequent equipment operation, high flexibility, and high rotation frequency.
Recommended configuration:
- The bucket pin is made of 40Cr tempered material, taking into account both cost and performance;
- The surface is quenched by high-frequency quenching to improve local hardness;
- The bushing is made of split bronze bushing + double oil groove structure, which is conducive to uniform distribution of grease;
- Emphasis on easy maintenance design to ensure that the bushing can be quickly replaced and reduce downtime.
Wetlands, swamps and water conservancy sites
Características: humid environment, mud wrapping, and high corrosion risk.
Recommended configuration:
- The bucket pin is made of stainless steel composite material or double-layer anti-corrosion coating on the surface;
- The bushing uses POM nylon or bronze bushing + external polyurethane protective layer to prevent water intrusion;
- Focus on strengthening the sealing structure, such as adding dust ring + waterproof oil seal to slow down the corrosion erosion rate;
- After daily construction, the parts need to be rinsed with a high-pressure water gun and re-greased.
Cold environment (such as Northeast China, Russia, and Canada)
Características: Metal materials are prone to embrittlement under low temperature conditions, and the fluidity of grease deteriorates.
Recommended configuration:
- The bucket pin adopts low-temperature toughness reinforced alloy steel + low-temperature tempering heat treatment process to keep it from brittle cracking below -40°C;
- The bushing is recommended to use self-lubricating alloy bushing + lithium-based high-temperature grease;
- The double-layer sealing system specially designed for low-temperature environment is selected to avoid internal frost;
- It is recommended to preheat and start the equipment for 2 to 5 minutes per shift to reduce cold start stress shock.
Desert, high-temperature and arid working conditions (such as the Middle East and Africa)
Características: High ambient temperature, severe wind and sand, and easy drying of grease.
Recommended configuration:
- The bucket pin is made of nickel-chromium alloy steel + surface nitriding treatment, which takes into account heat resistance and wear resistance;
- The bushing is made of self-lubricating copper alloy material + sealing ring anti-sand design;
- Grease needs to be added twice a day, and it is recommended to use high-temperature resistant synthetic grease;
- Add anti-sand cloth cover or multi-layer dustproof structure to prevent sand from embedding.
Special customized scenarios (breaker, high-frequency vibration hammer)
Características: high-frequency vibration working conditions, huge impact load.
Recommended configuration:
- Ultra-high strength quenched and tempered steel (such as 35CrMo) + deep induction quenching is used for bucket pins;
- Bushing adopts carbide nested structure with extremely low surface friction coefficient;
- Add vibration buffer washers or high elastic sealing elements to extend service life.
Obtenga una cotización rápida y gratuita | Correo electrónico: henry@gfmparts.com | WhatsApp: +86 17705953659 |
Although bucket pins and bushings are “small parts” in excavators, they bear great responsibilities. From material selection and design, matching process to adaptability under different working conditions, every link needs to be scientifically judged in combination with the on-site environment and equipment load characteristics. Through this guide, we can see:
- Various types of bucket pins and bushings are not interchangeable, but need to be accurately matched according to the purpose;
- Match clearance and assembly accuracy directly affect the service life and stability of the whole machine;
- Selecting professional materials, sealing methods and lubrication solutions for different working conditions is the core of extending service life;
- Regular inspection, replacement on demand, and scientific lubrication are important guarantees to avoid premature failure and reduce maintenance costs.
As an experienced fabricante de piezas de excavadora, GFM always adheres to high-standard craftsmanship, strict material selection, and practical structural design as its core advantages to provide customers with customized bucket pins and bushing solutions. Whether you are undertaking mining projects, municipal projects or special environment operations, as long as you select the right model and perform standardized maintenance, bucket pins and bushings can always provide stable and reliable support for your equipment.Stable, safe and durable support.
Choosing professionalism means choosing efficiency and long-term value.
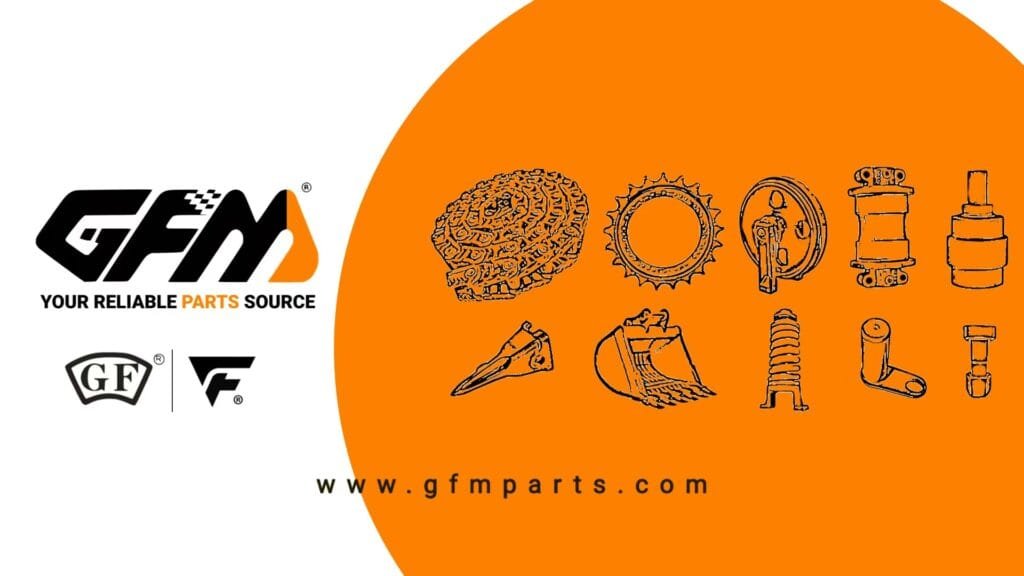