In the work of excavators, track chains are like tires of cars, which undertake the important tasks of equipment movement, power transmission and balance.
The composition and design of cadena de oruga de excavadora
Core components:
Chain plates
The chain plates are the main load-bearing components of the crawler chain, usually made of high-strength alloy steel. They are specially heat-treated to make them more resistant to wear and fatigue. You can think of the chain plates as multiple solid “metal plates” that bite each other to form an integral chain.
Connecting pins
The connecting pins are used to firmly connect the chain plates together to ensure that the entire chain can bend flexibly and not break easily. They can be understood as the “rivets” of the chain, and they need to have extremely high wear resistance and impact resistance.
Rueda loca de la oruga
The drive wheel provides power to the chain and drives the chain to roll, while the guide wheel is responsible for adjusting the movement direction of the chain to prevent the chain from deflecting. Both are usually precision-machined and surface-hardened to ensure stability and reliability during high-speed operation.
Seals and buffer systems
The main function of seals is to prevent lubricating oil leakage and external dirt from entering, while the buffer system can effectively absorb the vibration and impact generated during operation and reduce direct wear between parts.
Design concept:
When designing crawler chains, engineers need to find a balance between “durable” and “sufficiently flexible”. Through precise calculations and finite element analysis, it is ensured that the chain can not only provide sufficient power transmission when subjected to heavy loads and strong impacts, but also prevent fatigue cracks caused by local overloads.
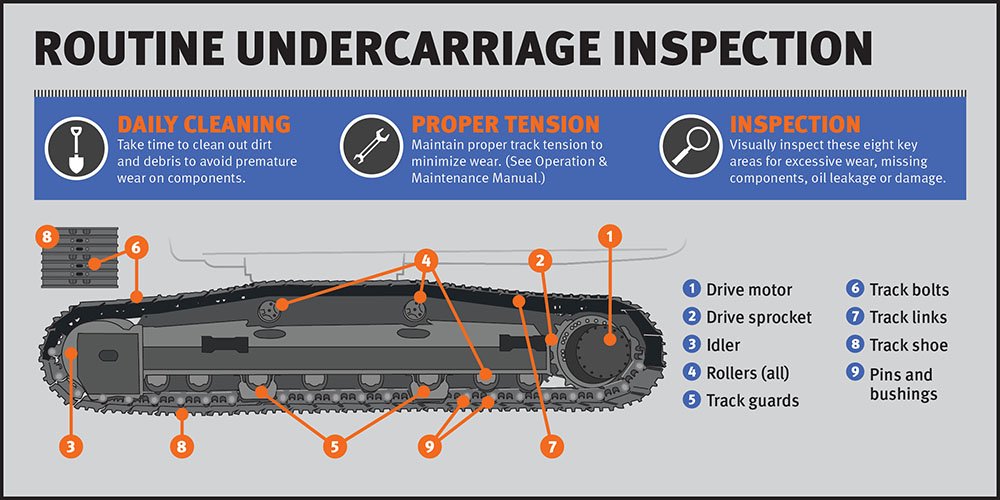
Five typical causes of failure and repair solutions
Abnormal wear
Root cause:
- Lubrication failure (aging of the seal ring leads to impurities intrusion)
- The hardness of the chain link material does not meet the standard (HV < 450)
- Frequent sharp turns on the walking route (lateral friction exceeds the limit)
Repair solution:
- Replace the sealing component and use high-temperature lithium-based grease
- Use laser cladding technology to repair the worn surface
Chain link fracture
Fracture mode analysis:
- Brittle fracture (material toughness decreases under low temperature environment)
- Fatigue fracture (crack extension under alternating load)
Emergency treatment:
- Use high-strength bolts to temporarily fix the fractured part
- Symmetrical chain links need to be replaced in pairs to maintain balance when replacing
Track derailment
Cause diagnosis:
- Guide wheel bearing damage (radial clearance > 0.5mm)
- Train roller wear (coaxiality error ≥ 2mm)
Reset operation specification:
- Use hydraulic jack to adjust the track tension to the manufacturer’s recommended value
- Check whether the wear of the drive wheel tooth profile exceeds 15% of the tooth height
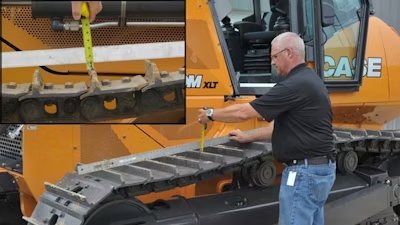
Common faults and causes
The track chain will have various faults in long-term work. Common causes include:
Material fatigue and wear
Long-term repeated high-intensity loads and continuous impacts will cause fatigue cracks in the chain plate and connecting pins. This is like a metal part that has been used for a long time gradually losing its initial toughness, and small cracks will gradually expand after they appear, which may eventually lead to breakage.
Insufficient lubrication or oil quality problems
Lubricating oil plays a role in reducing metal friction and dissipating heat. If the lubricating oil is insufficient or poor quality oil is used, the chain parts will directly rub against each other, generate a lot of heat, and accelerate wear and aging.
Improper installation and adjustment
If the chain tension is not appropriate (too tight or too loose) and the sprocket is not accurately aligned during installation, local stress concentration will occur in the crawler chain. This unbalanced stress state can easily cause a part to wear out prematurely or even damage.
Environmental factors
Excavators often work in dusty, muddy and wet environments. External impurities and corrosive substances can easily penetrate into the chain, accelerate oxidation and corrosion of the metal surface, and reduce the overall life.
Overload operation
When the excavator is overloaded or encounters a very hard working object, the pressure on the crawler chain will far exceed the design standard, which can easily cause deformation, breakage and other failures of the chain plate.
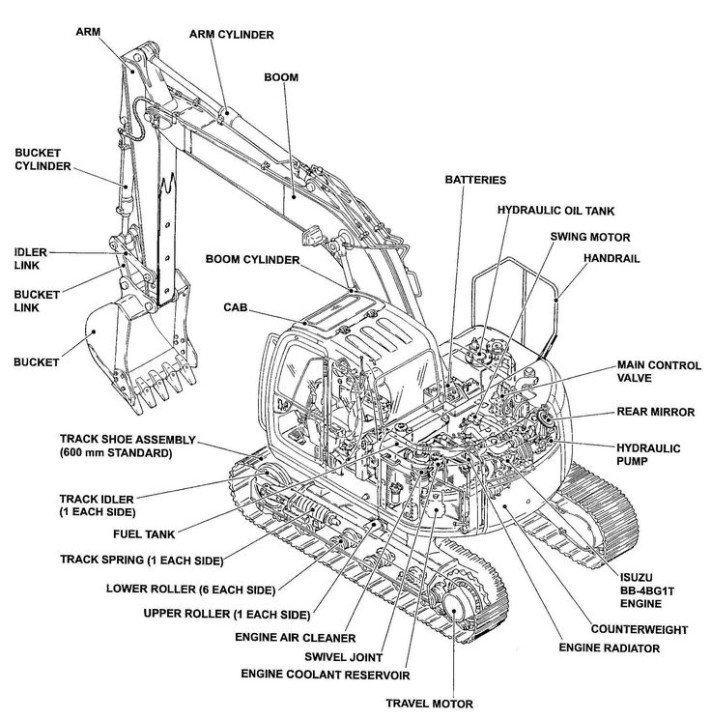
Common fault repair methods
When there is a problem with the crawler chain, timely measures should be taken to repair it to ensure the safety and efficient operation of the equipment:
Replace damaged parts
If the chain plate, connecting pin or wheel system is found to be obviously worn, cracked or broken, the first method is to replace these damaged parts. Timely replacement can avoid the problem from expanding and ensure the transmission performance of the entire chain.
Adjust the chain tension and alignment
Check whether the chain is moderately tight and correct the position of the sprocket and guide wheel. Proper tension can not only prevent the chain from skipping teeth or falling off, but also evenly distribute the load and reduce local stress.
Lubrication system inspection and maintenance
Regularly check the amount of lubricating oil and the quality of oil to ensure the normal operation of the lubrication system. If the oil is found to be deteriorating or insufficient, the lubricating oil should be replaced in time, the lubrication channel should be cleaned, and sufficient lubrication protection should be ensured between the metal parts.
Surface repair and anti-corrosion treatment
For parts that are affected by corrosion or slight wear, they can be repaired by sandblasting, heat treatment or anti-rust coating. This can not only restore the original performance, but also extend the subsequent service life.
Use professional testing tools
Use non-destructive testing technologies such as ultrasonic and magnetic powder to regularly detect whether there are invisible cracks and fatigue damage inside the chain. Through dynamic monitoring and data analysis, hidden dangers can be discovered in advance, and early prevention and early repair can be achieved.
Preventive maintenance system
Daily inspection checklist
- Lubrication management: Add special extreme pressure grease (NLGI grade 2) every 50 hours
- Tension detection: Use a ruler to measure the sag (standard value: 30-50mm between two sprockets)
- Bolt preload: Use a hydraulic wrench to tighten according to the torque specification table (such as M24 bolts need 1100N·m)
Seasonal maintenance focus
- Winter: Switch to low-temperature antifreeze lubricant (pour point <-35℃)
- Dusty environment: Increase the frequency of seal inspection and install magnetic filters
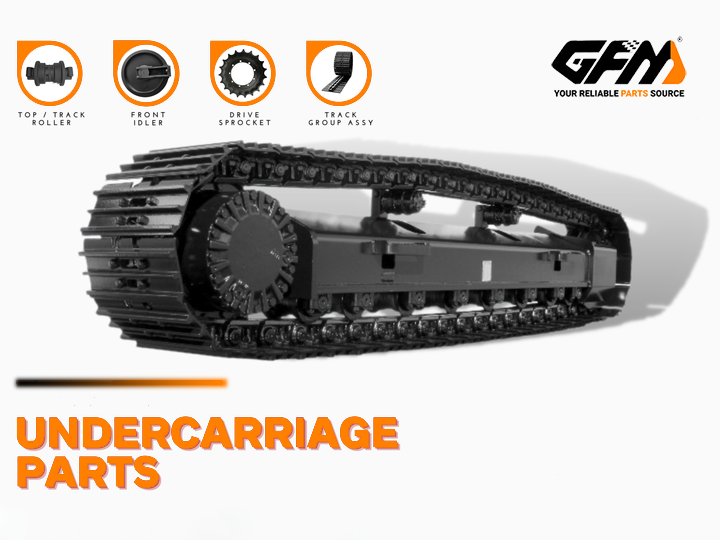
Daily maintenance strategy
Preventing problems is more economical and safer than repairing them afterwards. Here are some practical daily maintenance suggestions:
Inspección regular
Make a detailed inspection plan. It is recommended to check each key component of the chain after a certain number of working hours. The inspection content includes the wear of the chain plate, the tightening state of the connecting pin, and whether the sprocket is offset.
Cleaning and lubrication
After the operation is completed, remove impurities such as sand and dust on the surface of the chain in time to ensure that the lubricating oil can be evenly distributed on each component. Use professional cleaning agents to clean regularly to avoid residual dirt affecting the lubrication effect.
Monitor temperature and vibration
In a high-load operating environment, installing temperature and vibration monitoring devices can detect abnormal conditions in time. When an abnormal increase in local temperature or excessive vibration amplitude is detected, the vehicle should be stopped and checked immediately to prevent small problems from causing major failures.
Operator training
Provide professional training for operators to let them understand the basic structure and maintenance requirements of the crawler chain. Correct operating habits, such as avoiding sudden acceleration, sharp turns, and overload operation, can greatly reduce damage caused by human factors.
Record maintenance history
Establish detailed maintenance records and usage files, and record relevant data for each inspection and maintenance. Long-term accumulated data helps analyze wear trends and provide a basis for subsequent preventive maintenance and product improvements.
How to confirm and customize the right track chain
Choosing the right crawler chain is an important prerequisite for ensuring the efficient operation of the excavator. The following are the specific steps to confirm and customize the crawler chain:
Confirm technical parameters
According to the model, working environment and working intensity of the excavator, determine the load, speed and fatigue resistance that the crawler chain needs to bear. Provide detailed technical drawings and parameter requirements to help suppliers understand the needs.
Reference quality certification
Give priority to suppliers with international certifications such as ISO and CE to ensure that the product quality meets international standards. Check product test reports and user feedback to help evaluate the durability and safety of the product.
Servicio personalizado
If the standard product cannot meet the needs of special working conditions, you can communicate in depth with the supplier to discuss customized solutions. Including material selection, surface treatment process, special lubrication solutions, etc., to ensure that the product performs best under actual working conditions.
Sample test verification
Before purchasing in large quantities, order samples for on-site testing. Verify the matching and durability of the crawler chain through actual use, adjust the customization plan based on feedback, and ensure that the final product fully meets expectations.
Perfect after-sales support
Choose suppliers who not only have excellent product quality, but also have perfect after-sales service and technical support. Once a problem occurs, timely response, on-site guidance and rapid maintenance services will greatly reduce equipment downtime and operating costs.
Obtenga una cotización rápida y gratuita | Correo electrónico: henry@gfmparts.com | WhatsApp: +86 17705953659 |
As an important “lifeline” for equipment movement and transmission, the conjunto de enlace de pista of the excavator has strict technical requirements in the design, cause of failure, repair method and daily maintenance. Only under the premise of all-round prevention, timely maintenance and continuous optimization of product design can the safety and efficient operation of the equipment be truly guaranteed. Enterprises and users should pay attention to these details together to remain invincible in the increasingly severe market competition.
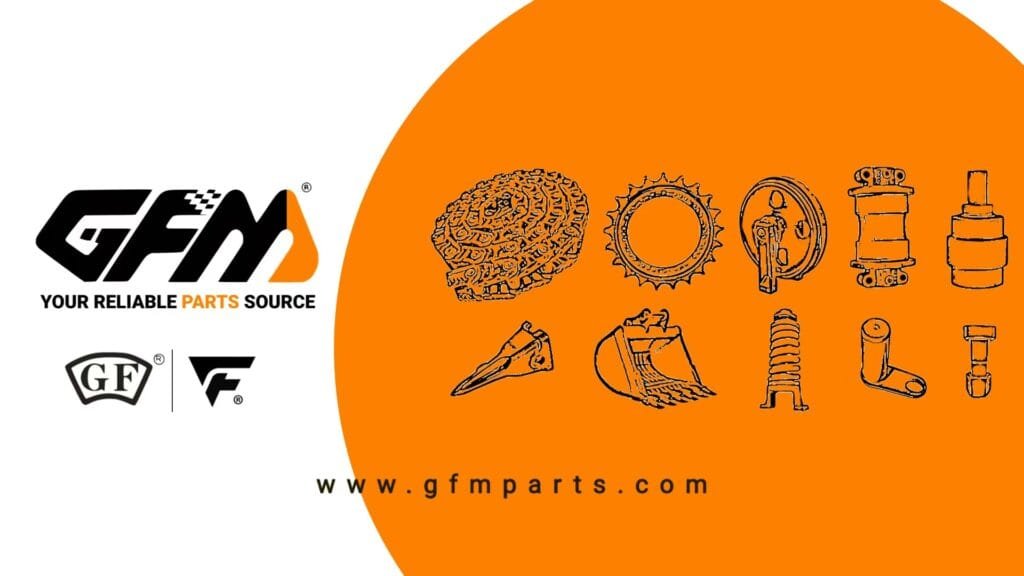