Excavators are indispensable heavy machinery equipment in modern construction and mining projects, and track shoe are one of the key components of the crawler system. It not only bears the load-bearing and driving functions of the excavator, but also plays a vital role in various working environments. In order to ensure the efficient operation of the excavator, it is important to understand different types of track shoe, their design principles, how to choose the right track shoe, and how to maintain and replace them.
Composition and design principle of zapata de oruga de excavadora
Excavator track shoe are an important part of the crawler system, mainly used to support the crawler and help transmit driving force. Track shoe are generally made of steel, with high tensile strength and wear resistance, ensuring that they can be durable in complex working environments. Each Track shoe consists of multiple parts, usually including the following main components:
- Track shoe body: usually cast from steel, is the main part of the Track shoe, and carries the load of the excavator.
- Internal and external ribs: The internal and external ribs are the supporting frame structure of the Track shoe, which increases the strength and stability of the Track shoe and ensures that the Track shoe can still maintain good working performance under high loads.
- Roller Path: Made of quenched high-carbon alloy steel (hardness HRC58-62), responsible for dispersing equipment weight and ground impact
- Bushings and pins: Bushings and pins are used to connect the Track shoe and other parts of the track, providing flexible rotation and wear resistance.
- Bolt assembly: 12.9 grade high-strength bolts with self-locking nuts, preload must reach 850N·m±5%
Engineering mechanics design principles
- Three-point support theory: Reduce the ground pressure by 30-50% through double/triple rib structure (mathematical model: P=W/(n×L×B))
- Dynamic load compensation: The arc bottom design increases the impact load attenuation rate by 40%
- Anti-derailment mechanism: The lateral guide rail inclination is controlled at 15°±1°, and the contact area is increased by 25%
- Impact resistance: The Track shoe needs to have sufficient impact resistance to cope with rough working environments.
Types of excavator track shoe
There are many types of excavator track shoe. According to different designs and structures, they can be divided into double grouse track shoe, triple grouse track shoe, and special track shoe. Each type of Track shoe has different application scenarios and performance characteristics.
Double grouse track shoe
Double grouse track shoe are usually composed of two inner and outer ribs, and have high strength and stability. Due to its simple structure and low manufacturing cost, double grouse track shoe are widely used in excavators with light loads, such as small or medium-sized excavators. The advantages of double grouse track shoe are:
- Low cost, suitable for projects with tight budgets.
- Strong load-bearing capacity, suitable for flatter working environments.
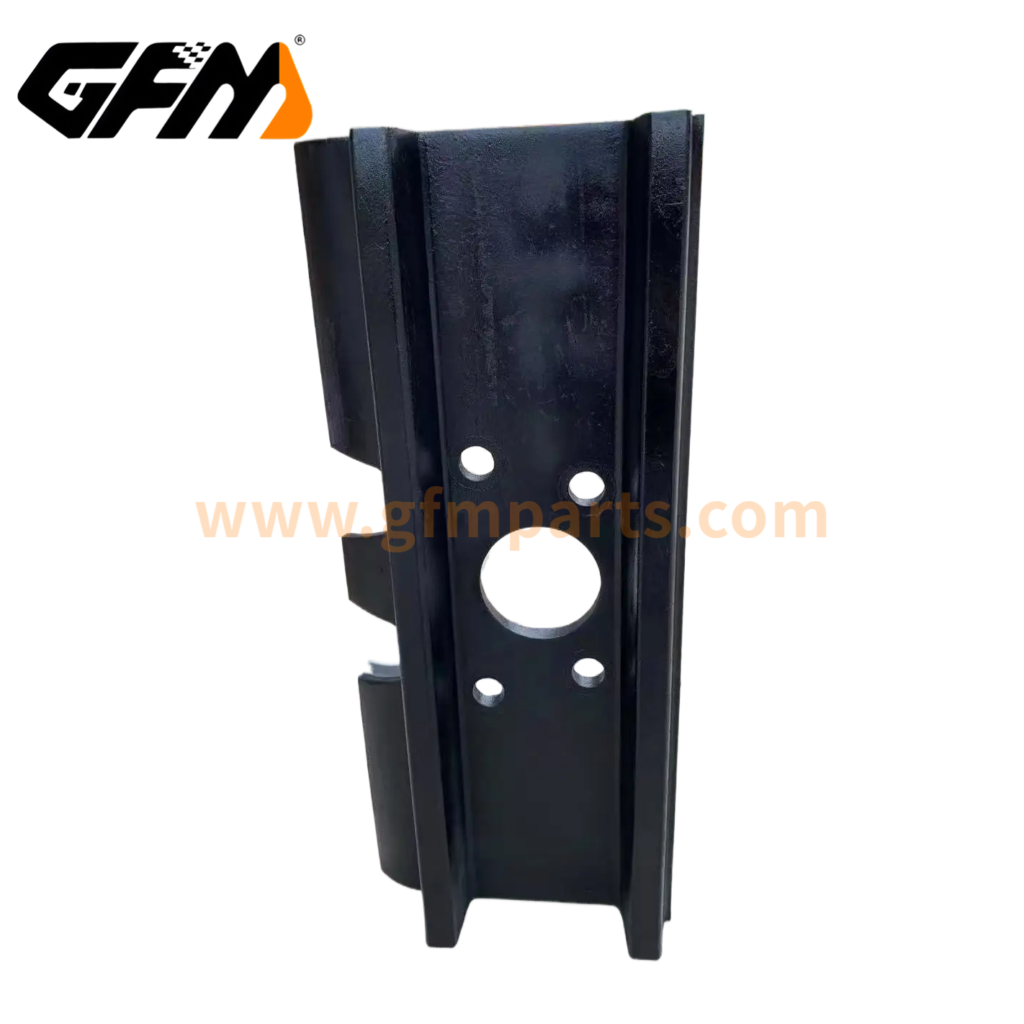
Triple grouse track shoe
Triple grouse track shoe add one rib to the double grouse Track shoe, further improving the strength and durability of the Track shoe. Triple grouse track shoe are suitable for excavators that carry heavier loads, especially in more complex working environments. Its advantages include:
- High-strength load-bearing, able to cope with heavier workloads.
- Enhanced wear resistance, suitable for long-term high-intensity working environments.
- Good impact resistance, able to work efficiently on rough and uneven ground.
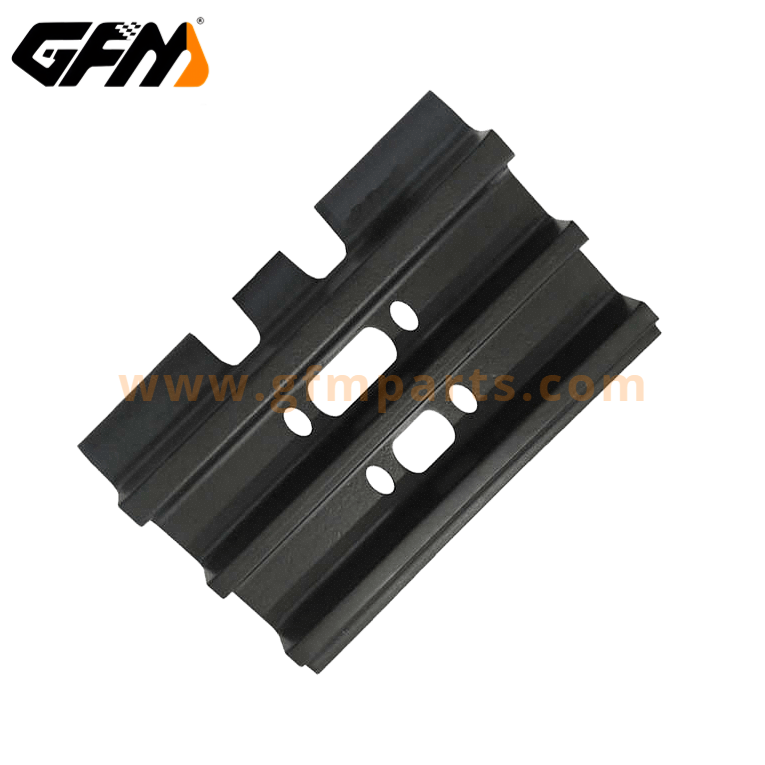
Flat-bottomed track shoe
Flat-bottomed track shoe is a special design of crawler chain. The bottom of the chain is smooth and widely used on soft or loose ground, such as sand, mud, etc. The advantages of flat bottom plates include:
- Increase the ground contact area, effectively disperse the pressure, and reduce the intrusion into soft ground.
- Improve traction, especially suitable for soft ground, such as swamps or slippery environments.
Swamp track shoe
Swamp track shoe is a type of chain designed for operation in extreme environments such as swamps and wetlands. The bottom is wide and equipped with special thread or groove design, which can effectively prevent the crawler from slipping on wet and soft ground. Its characteristics are:
- The bottom is wide, increasing the ground contact area to prevent the chain from sinking into the soft ground.
- Special texture design provides better traction and stability to prevent the crawler from slipping.
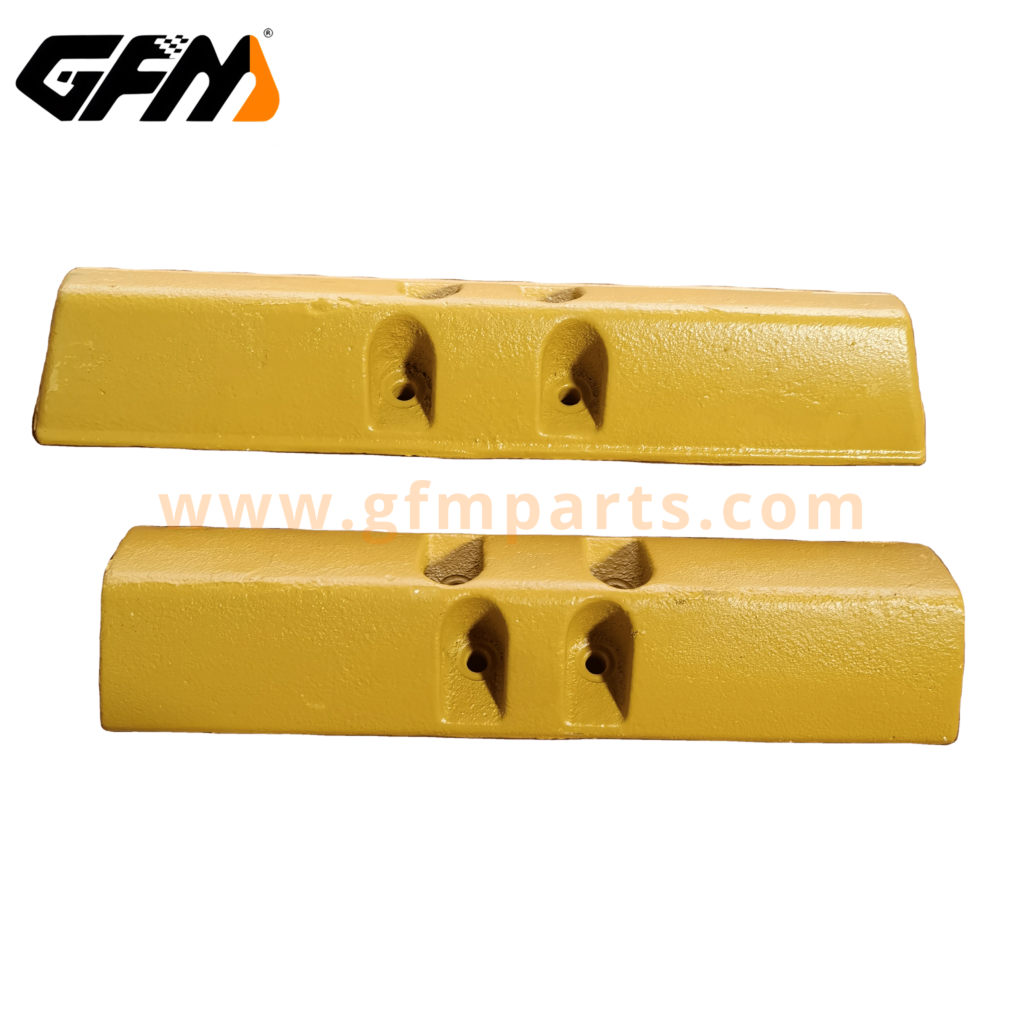
Special track shoe
Special track shoe is a type of Track shoe customized for special working environments or needs. For example, chains suitable for high temperature environments, low temperature environments or humid environments. Common special chains include:
- Anti-corrosion track shoe: specially designed for wet or corrosive environments to extend the service life of the track shoe.
- High temperature track shoe: suitable for high temperature working environments, and can resist the damage of high temperature to the Track shoe material.
How to choose the right excavator Track shoe
Choosing the right excavator Track shoe is the key to ensuring the efficient operation of the equipment. The choice of Track shoe depends not only on the load and working environment of the excavator, but also on the design and material of the Track shoe. The following are technical factors to consider when choosing a suitable Track shoe:
Impact of the working environment
Different working environments have very different requirements for track shoe, and these factors need to be fully considered when choosing a Track shoe:
- Soft soil or sand: If the excavator will be working on soft ground, such as sand, mud or slippery ground, it is best to choose a flat plate Track shoe or a swamp plate Track shoe. These chains help improve traction and reduce the risk of the Track shoe sinking into soft ground by increasing the contact area and special texture design.
- Rocks and hard ground: When working on hard ground, especially in rocks or hard soil, it is recommended to choose a three-rib Track shoe. This Track shoe can withstand greater loads and impacts and provide better wear resistance.
- Complex terrain or high-load operation: If the excavator needs to be used in a complex construction environment or under high-load work, a three-rib Track shoe should be selected. It can provide stronger support and is suitable for occasions that require high-intensity operations.
Excavator load and type
When choosing a Track shoe, you also need to consider the model, size and operating load of the excavator:
- Light excavator: It is suitable to use a double-rib Track shoe with lower cost and moderate load capacity.
- Heavy excavator: Heavy excavators should choose a three-rib Track shoe with higher load capacity and impact resistance.
- Ultra-large excavators: For ultra-large excavators working in extreme environments, it may be necessary to customize swamp track shoes or other special chains to meet the challenges of ultra-high loads and extreme environments.
Operation cycle and maintenance requirements
For equipment that operates for a long time and at a high frequency, it is more appropriate to choose a three grouse Track shoe or a special Track shoe with better wear resistance and impact resistance. Although these chains are more expensive, in the long run, they can reduce the frequency of maintenance and replacement and improve the overall efficiency of the equipment.
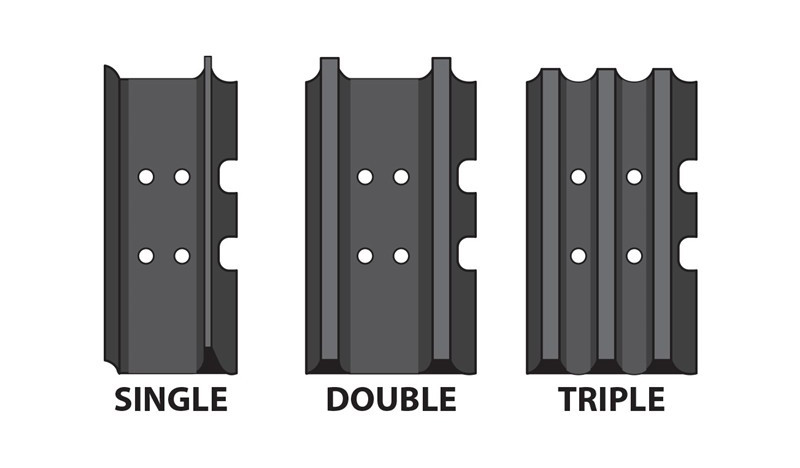
How to replace the excavator Track shoe
The replacement of the excavator Track shoe is the core content of the crawler system maintenance. Improper operation may cause chain damage or crawler system failure.
Special tool preparation list
- Hydraulic tensioner (pressure range 0-35MPa)
- Pin punch (material SKD61, hardness HRC60)
- Laser centering instrument (accuracy ±0.1mm/m)
Eight-step replacement method
- Equipment lifting: Use a 200T jack, and the support point must be at the chassis reinforcement position
- Old Track shoe removal: Loosen the bolts in diagonal order, and oxygen cutting is strictly prohibited
- New Track shoe pre-installation: Use hot installation method (heating temperature 120±10℃)
- Torque calibration: Tighten to the standard torque in three times (300N·m→600N·m→850N·m)
Standardized operating procedures
Preparation work
- Equipment shutdown: Before replacing the Track shoe, make sure that the excavator is completely shut down and disconnected from the power supply.
- Lifting equipment preparation: Use a hydraulic jack or lifting equipment to lift the excavator stably and ensure that there is enough space for operation.
Removing the old chain
- Removing the pins and bushings: Use special tools to remove the pins and bushings that connect the chain to the track wheel, ensuring that other components are not damaged during operation.
- Checking the chain wear: During the removal process, check the wear of the chain and record the parts that need to be replaced so that the new chain can be installed.
- Removing the chain: Gently pull out the old chain. If the chain is rusted or severely damaged, use special tools to remove it.
Installing the new chain
- Checking the new chain: Before installation, check the size, hole position and material of the new chain to ensure that it matches the excavator model.
- Aligning the installation position: Align the connection between the new chain and the track wheel to ensure that it is in the correct position.
- Installing the pins and bushings: Use new pins and bushings to fix the chain in place to ensure a firm connection.
- Tightening and adjustment: Use tools such as wrenches to tighten the connecting parts to ensure that there is no looseness.
Complete the test
- Test run: After installing the new Track shoe, conduct a short low-speed test to ensure that the Track shoe is firmly installed and there is no abnormal sound.
- Check each part: After the test is completed, check the connection points of the Track shoe to ensure that there is no looseness or damage, and confirm that it is in normal working condition.
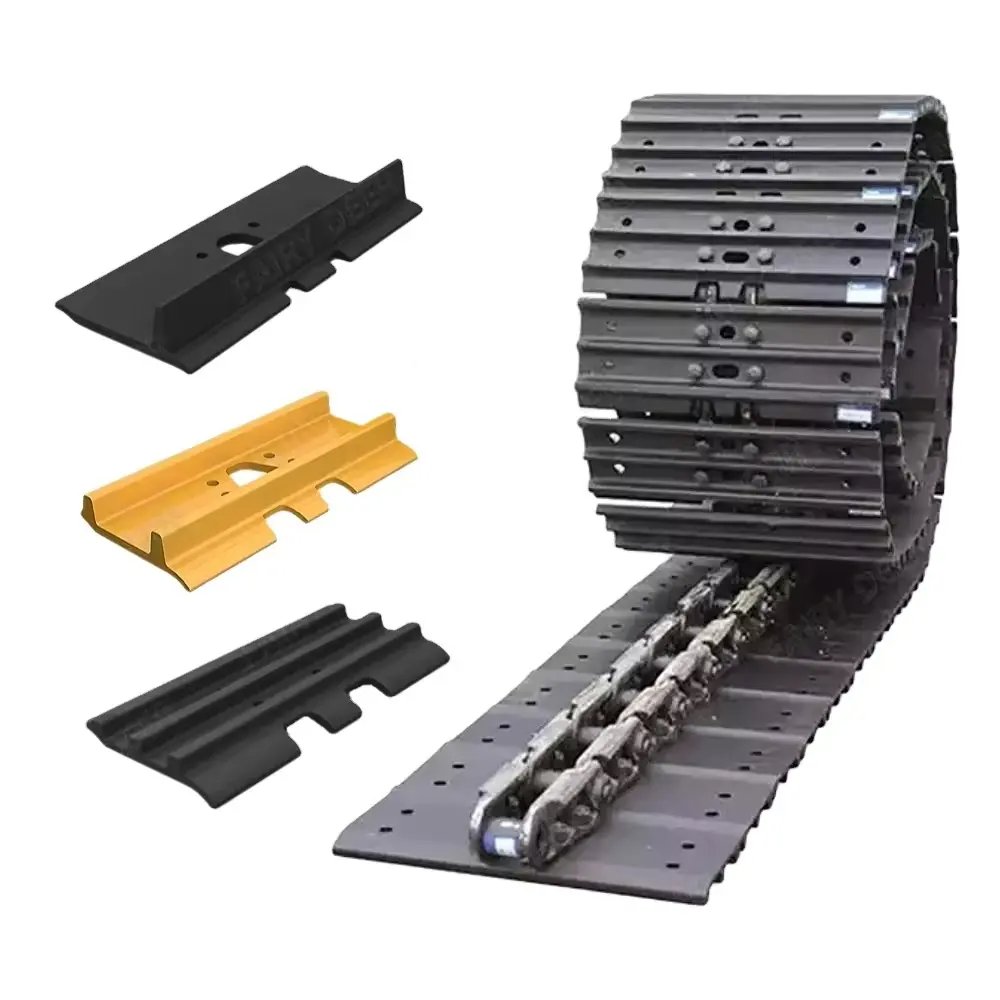
Maintenance and care of excavator track shoe
In order to extend the service life of the Track shoe and ensure the efficient operation of the excavator, daily maintenance is essential. Here are a few key suggestions for Track shoe maintenance:
- Regular cleaning: Remove dirt, sand and other debris on the Track shoe to avoid scratches on the surface of the Track shoe.
- Lubrication and maintenance: Regularly add lubricating oil to the pins and bushings of the Track shoe to reduce wear and improve flexibility.
- Check wear: Regularly check the wear of the Track shoe, especially the pins and bushings. If there is obvious wear, it should be replaced in time.
- Avoid overload operation: Avoid overload operation, especially when working on uneven ground and slippery environments, to reduce the burden on the Track shoe.
Obtenga una cotización rápida y gratuita | Correo electrónico: henry@gfmparts.com | WhatsApp: +86 17705953659 |
Understanding different types of excavator chains and their applicable environments, and choosing the right track shoe according to the excavator’s load, operating environment, and budget requirements, is the key to ensuring efficient operation of the equipment and extending the service life of the chain. Regular inspection, maintenance, and timely replacement of damaged chains will help the excavator always maintain its best working condition. Through this technical analysis, you can more professionally select, install, and maintain your excavator chain, thereby improving work efficiency and reducing maintenance costs.
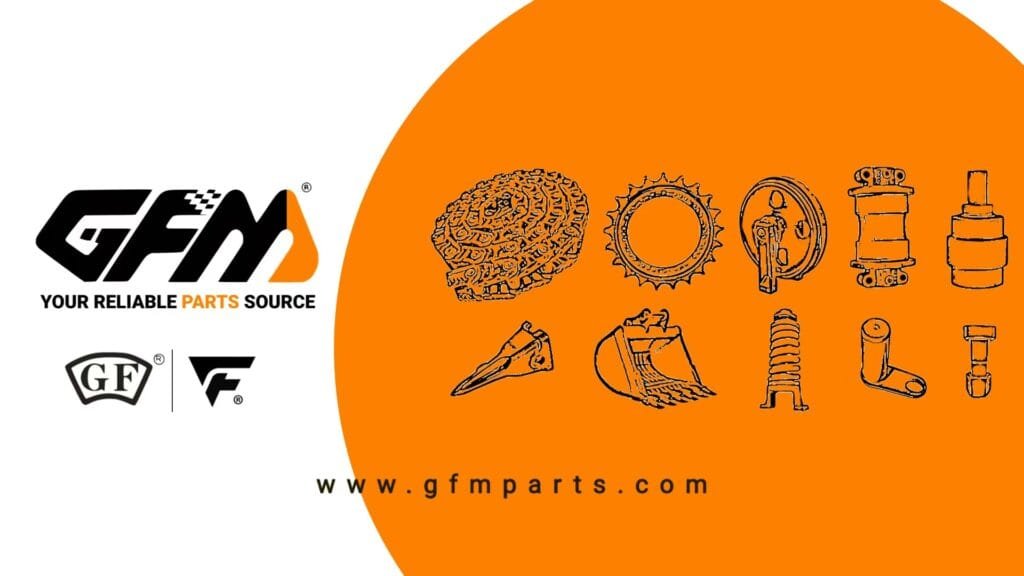