In the current fields of construction, gardening, mining and municipal engineering, mini excavators have become the preferred equipment in many engineering projects due to their flexible maneuverability and efficient operation capabilities. As a key component to ensure the stability of the whole machine and the safety of operation, track rollers play a vital role in the entire system.
Technical parameters and performance analysis
Digging force and operating range
- Digging depth and operating radius:
- Different models of mini excavators have different maximum digging depths and operating radiuses. In actual projects, it is crucial to understand the working limits of the equipment under full load conditions. For example, municipal renovation projects may require the machine to achieve deeper excavation capabilities in limited spaces, while earthwork projects are more concerned with the flexibility of operating radius and sidewall excavation.
- Digging force and hydraulic system:
- Digging force directly determines the ability of the equipment to cope with hard ground and complex working conditions. An efficient hydraulic system can not only provide sufficient digging force, but also achieve precise control. When comparing different products, customers can pay attention to the pressure parameters, flow rate and response speed of the hydraulic system to ensure that the equipment remains stable during high-load operations.
Mobility and operating system
- Steering and travel system:
- The flexibility of mini excavators in narrow sites depends on their steering system and crawler design. Customers should pay attention to the walking stability, steering radius and shock absorption effect of the equipment under various ground conditions to improve overall operating efficiency and safety.
- Control system and human-machine interface:
- Whether the layout of the operating handle, console and display interface conforms to ergonomic design directly affects the driver’s operating experience. Advanced intelligent control systems can automatically adjust working parameters and reduce the risk of human operating errors.
Environmental adaptability
- Extreme temperature and humidity resistance:
- For different engineering areas, the equipment needs to maintain stable operation in high temperature, low temperature, high humidity or dusty environment. Customers can pay attention to the manufacturer’s dustproof and waterproof design and environmental adaptability test report to ensure that the equipment can perform at its best under various climate conditions.
Fuel consumption, energy saving and environmental protection performance
Fuel economy analysis
- Working condition fuel consumption data:
- There are significant differences in fuel consumption indicators under different working conditions (such as light load, full load, and intermittent operation). By comparing the standard working condition fuel consumption provided by the manufacturer with the actual site data, customers can more accurately estimate the long-term operating cost of the equipment.
- Advanced engine technology:
- The new engine adopts high-efficiency combustion technology, exhaust gas recirculation (EGR) and intelligent control system, which enables the equipment to significantly reduce fuel consumption and exhaust emissions while meeting high power output, meeting increasingly stringent environmental standards.
Energy-saving design and intelligent control
- Energy-saving mode and automatic adjustment:
- Some models have introduced automatic energy-saving mode, which can automatically adjust the engine speed and hydraulic system parameters according to the operating load to optimize the energy consumption structure to the greatest extent.
- Emission standards and environmental certification:
- When purchasing equipment, customers should pay attention to whether the product meets national and international environmental standards, such as Euro IV and Euro V emission standards, and understand the relevant certification status to ensure that the use of the equipment is both efficient and environmentally friendly.
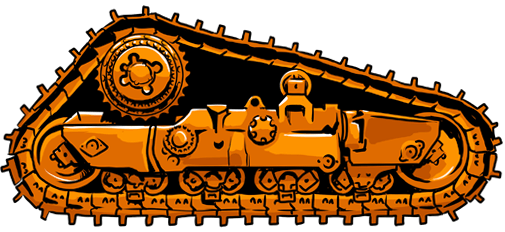
Applicable working conditions and engineering cases
Engineering types and scene applications
- Urban construction and municipal engineering:
- Due to its compact size and excellent flexibility, mini excavators are suitable for road maintenance, underground pipe network laying and urban square landscape transformation. In actual cases, many urban renewal projects use this equipment for precise operations.
- Garden landscape and agricultural construction:
- In garden landscape design and agricultural irrigation system construction, mini excavators can complete earthwork, trenching, planting pits and other operations in a limited space, ensuring a balance between construction efficiency and landscape beauty.
- Mining and earthwork engineering:
- For some mini and medium-sized mines and earthwork engineering, the high load-bearing capacity and stability of the equipment become the key. By choosing the right model, the construction period and operating costs can be greatly reduced.
Maintenance and repair management
Regular maintenance strategy
- Daily inspection:
- Before daily operation, check the key media such as hydraulic oil, fuel, and lubricating oil; at the same time, check whether the tracks, supporting wheels, and various connecting parts are loose or abnormally worn.
- Periodic maintenance:
- It is recommended to conduct weekly, monthly, quarterly, and annual comprehensive inspections according to the manufacturer’s manual, covering the hydraulic system, engine, transmission system, and electronic control module, etc., to ensure long-term stable operation of the equipment.
Troubleshooting and preventive measures
- Common fault identification:
- Hydraulic system leakage, excessive wear of supporting wheels, electronic component failure, etc. are more common problems during use. By establishing troubleshooting records and regular inspection plans, hidden dangers can be discovered in time.
- Preventive maintenance:
- Use a monitoring system to monitor key parameters (such as hydraulic pressure, oil temperature, vibration, etc.) in real time. Once abnormal data is found, take immediate measures to prevent mini problems from turning into major failures, thereby reducing maintenance costs and downtime.
Price, cost-effectiveness and total cost of ownership analysis
Initial investment and purchase cost
- Brand and model selection:
- There are large differences in prices among mini excavators of different brands and models on the market. Although high-end models have higher initial investment, they usually have more advanced technology, longer service life and lower maintenance frequency.
- Customized configuration and additional functions:
- Some equipment provides customized services, such as high-precision control systems, intelligent monitoring modules or special material support wheels. These additional configurations will increase the price of the equipment to a certain extent, but at the same time they can also improve overall work efficiency and safety.
Long-term use cost and total cost of ownership (TCO)
- Fuel and maintenance costs:
- In addition to the initial investment, fuel consumption, daily maintenance and spare parts replacement costs constitute the main operating costs of the equipment. By comparing the fuel consumption and maintenance cycles of various models under different working conditions, customers can more scientifically evaluate the total cost of ownership of the equipment.
- Residual value and depreciation rate:
- Cost-effective equipment usually maintains a high market residual value after a certain period of use, thereby reducing the depreciation rate. When choosing, customers can refer to the second-hand transaction data in the market to judge the value retention rate of the equipment and the possible recycling value in the future.
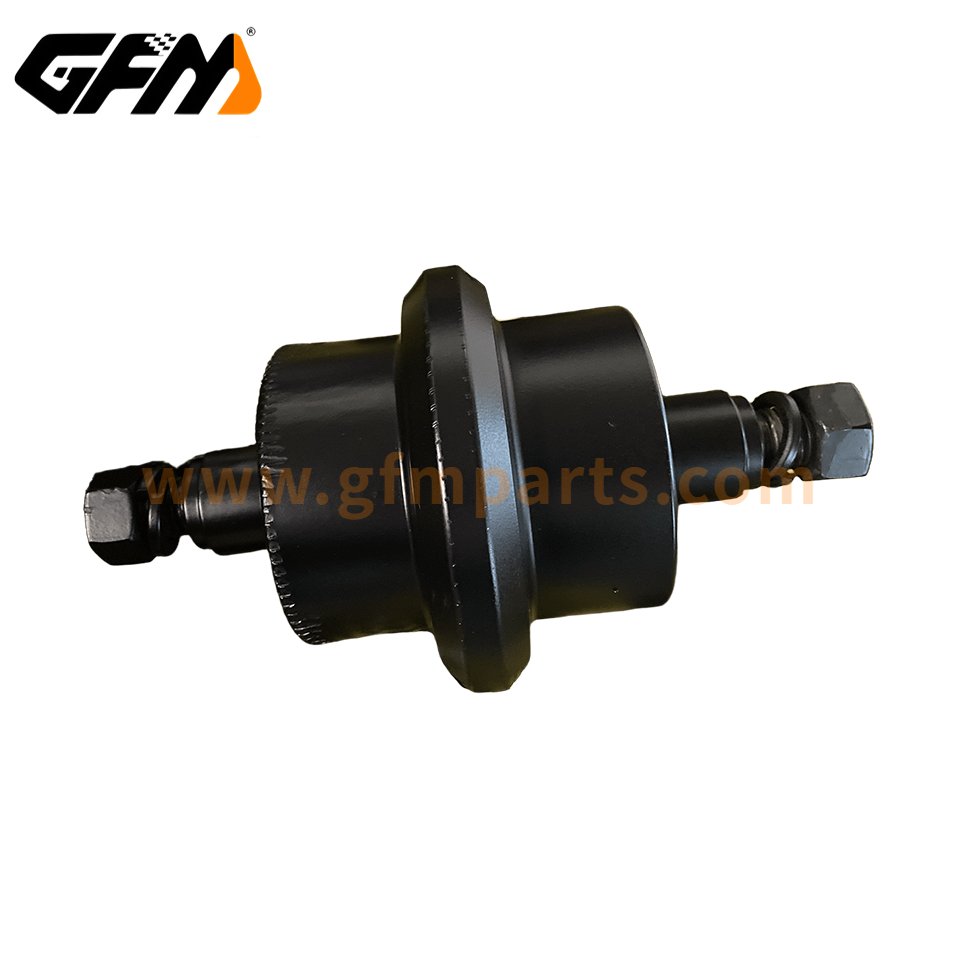
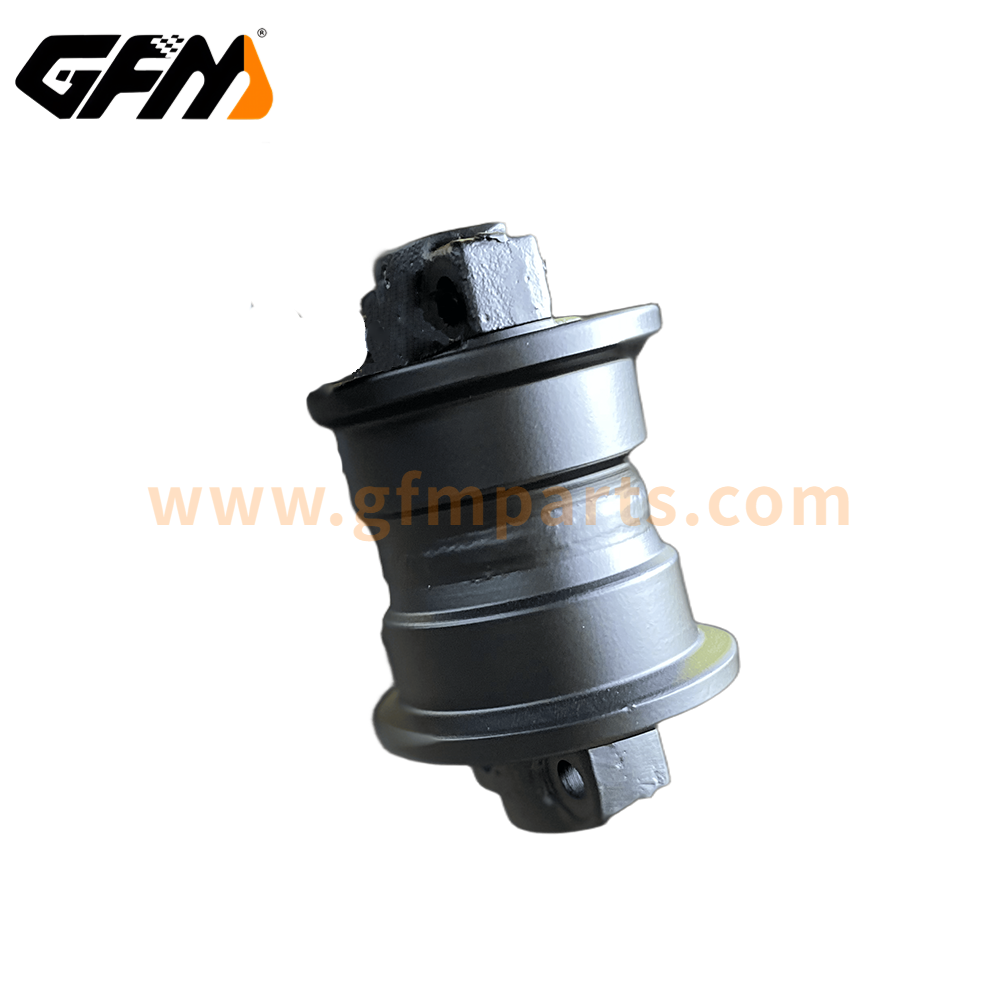
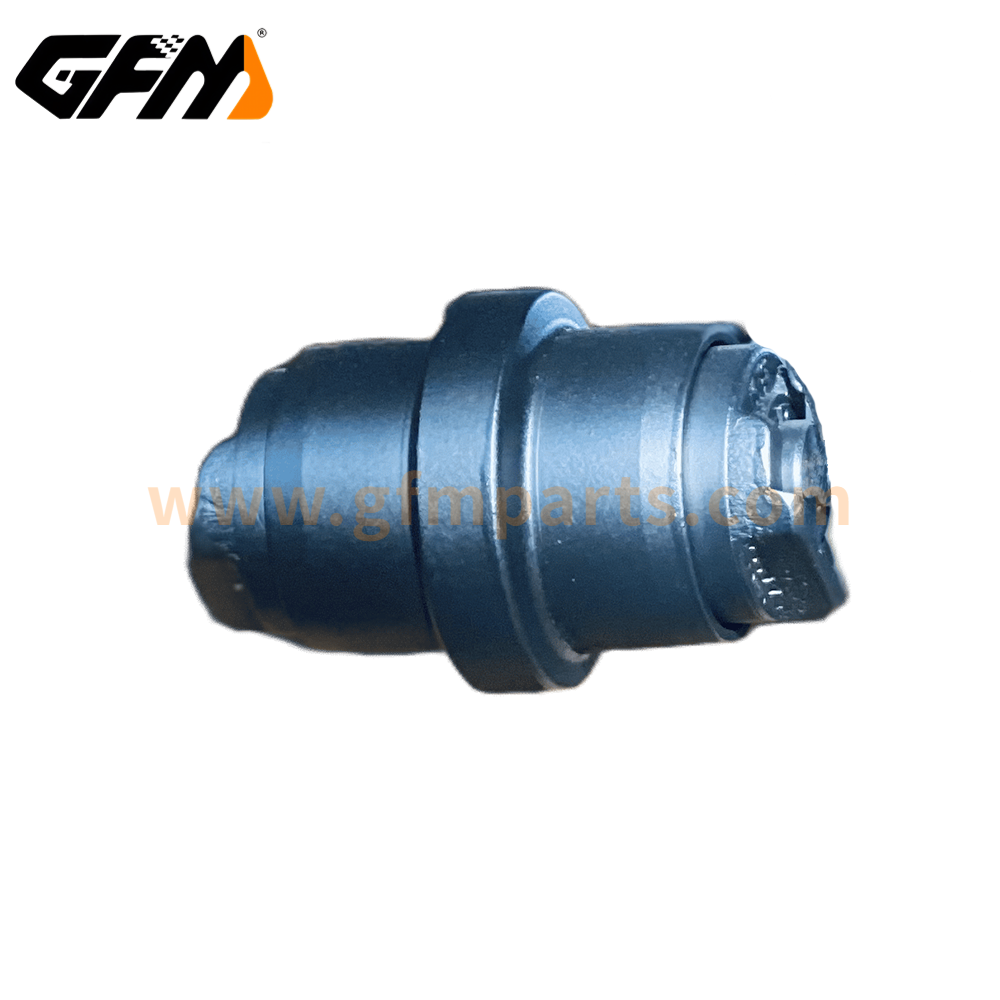
Key role and technical principle of the supporting roller
Stability and load distribution
- Load-bearing function:
- The main function of the supporting roller is to disperse the weight of the whole machine and ensure the stability of the equipment on high load and uneven ground. Scientific and reasonable load distribution design can effectively reduce the risk of damage to the machine due to partial load or vibration.
- Anti-overturning design:
- During the design process, by calculating the center of gravity and the force area, the supporting roller can provide additional anti-overturning support to ensure that it is still safe and reliable during sharp turns and slope operations.
Collaboration with other systems
- Collaboration with hydraulic system:
- The supporting roller works with the hydraulic system and the crawler system to ensure that the equipment can be evenly stressed under various operating conditions.
- Electronic monitoring and data feedback:
- In modern equipment, some high-end models are even equipped with supporting roller status monitoring modules, which remind operators to maintain or replace the supporting rollers in time through real-time data feedback to prevent safety hazards caused by neglecting details.
Design and material of track rollers for mini excavators
Design structure and process
- Structural form:
- Common track rollers designs include integral tire type, semi-tire type and combined type design. Different structures have different focuses on load-bearing, shock absorption and wear resistance. During the design process, it is necessary to balance the hardness, elasticity and wear resistance of the tire to ensure the normal operation of the equipment under complex working conditions.
- Process technology:
- Modern manufacturing technology (such as molding process, automated vulcanization, etc.) has greatly improved the consistency and durability of supporting wheels, while also making production costs and maintenance cycles more competitive.
Material selection and performance comparison
- Rubber and polyurethane materials:
- Rubber materials have good cushioning and shock resistance, while polyurethane performs better in wear resistance, corrosion resistance and service life. Some high-end products even use composite materials, combining the advantages of both and improving overall performance.
- Material innovation:
- With the continuous emergence of new materials, such as nano-enhanced rubber and polymer composite materials, supporting wheels have been significantly improved in durability, environmental protection performance and energy consumption control. Customers can refer to the material test reports and use cases provided by the manufacturer to determine which material is more in line with actual use requirements.
Installation, replacement and detection methods of bottom roller
Standard installation process
- Detailed explanation of installation steps:
- Pre-inspection and cleaning: Before installation, the installation area, fixing bracket and interface of the supporting roller need to be thoroughly inspected and cleaned to prevent impurities from affecting the fixing effect.
- Fixed installation: According to the installation manual provided by the manufacturer, use professional tools to tighten the bolts and position the correction to ensure that the supporting rollers are perfectly connected with the whole machine system.
- Verification test: After the installation is completed, conduct a test run to observe the operating status of the supporting rollers and confirm that there is no abnormal vibration or deviation.
Replacement and regular inspection
- Wear assessment and detection method:
- Regularly check whether there are cracks, depressions or abnormal wear on the surface of the supporting rollers; use measuring instruments to detect the thickness and uniformity of the tires to ensure that they meet safety standards.
- Judgment of replacement timing:
- When the supporting rollers are obviously worn, aged or have multiple fault prompts, they should be replaced in time according to the equipment manual or the advice of the technicians. Preventive replacement can reduce the risk of sudden accidents and extend the life of the whole machine.
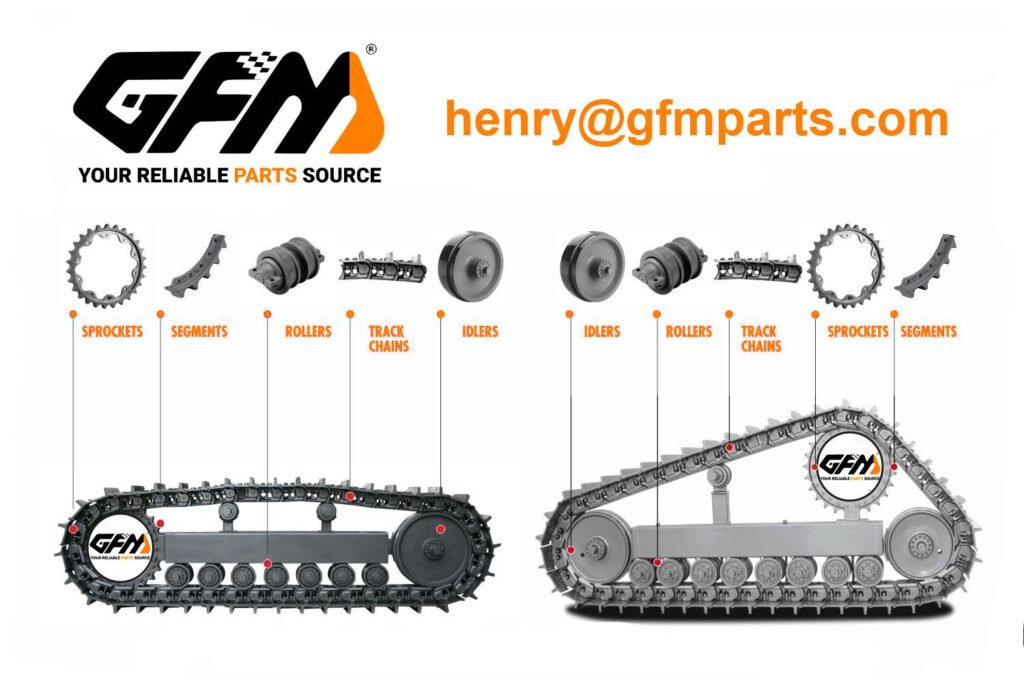
After-sales service system and spare parts support
Brand after-sales service guarantee
- Technical support and response:
- High-quality manufacturers are usually equipped with professional after-sales service teams, which can provide 24-hour online technical consultation and rapid response services. Customers should understand the service network coverage, response time and fault handling process in detail before purchasing.
- Warranty and training services:
- Some manufacturers provide long-term warranty services and regular technical training to help customers better master equipment operation, daily maintenance and troubleshooting skills to ensure the stability and safety of equipment during use.
Spare parts supply and inventory management
- Accessories sufficiency:
- The supply of key parts such as supporting wheels, hydraulic parts, and transmission devices directly affects the continuous operation ability of the equipment. High-quality suppliers usually have a complete inventory management system and logistics distribution system to ensure that customers can quickly obtain spare parts when needed.
- User feedback and market reputation:
- When purchasing equipment, customers can refer to the feedback of other users and independent third-party evaluations to have a more comprehensive understanding of the durability and service quality of equipment and accessories.
Safety operating procedures and professional training
Safety operating standards
- Operating procedure formulation:
- Establish detailed operating manuals and safety specifications, and put forward clear requirements for each link such as equipment startup, operation, shutdown, maintenance, etc., to ensure that each operation step meets safety standards.
- Risk prevention measures:
- Develop emergency response plans and safety reminders for different operating environments, such as how to prevent equipment from overturning when operating on slopes, how to deal with sudden hydraulic failures, etc.
Professional training and technical certification
- Driver training:
- Regularly organize professional training to help drivers become familiar with equipment operation, daily maintenance and troubleshooting skills. Training courses can cover theoretical knowledge, practical exercises and case analysis to improve the overall operation level.
- Safety certification and assessment:
- To ensure safe operation, it is recommended that enterprises or users conduct safety certification and assessment regularly, based on the latest industry standards and regulations, to ensure that all personnel have the necessary safety knowledge and emergency response capabilities.
Obtenga una cotización rápida y gratuita | Correo electrónico: henry@gfmparts.com | WhatsApp: +86 17705953659 |
With its excellent flexibility and efficient operation ability, mini excavators have become indispensable core equipment in various projects; and the design, material, installation and daily inspection of the supporting wheels as key components to ensure the stability and safety of the equipment are also crucial. From a comprehensive analysis of the equipment’s technical parameters, fuel economy and environmental adaptability to an in-depth discussion of maintenance management, price performance, after-sales service and safe operation, this article provides customers and users with a systematic and detailed reference framework.
Through a comprehensive analysis of various factors, customers can not only clearly understand the actual performance of the equipment under different working conditions, but also reasonably plan long-term operating costs and maintenance strategies, thereby achieving the best balance between equipment performance and safety. In the fierce market competition, a comprehensive grasp of this information will help customers make more informed purchasing decisions and use arrangements, ensuring that every construction project can be successfully completed under the premise of efficiency and safety.
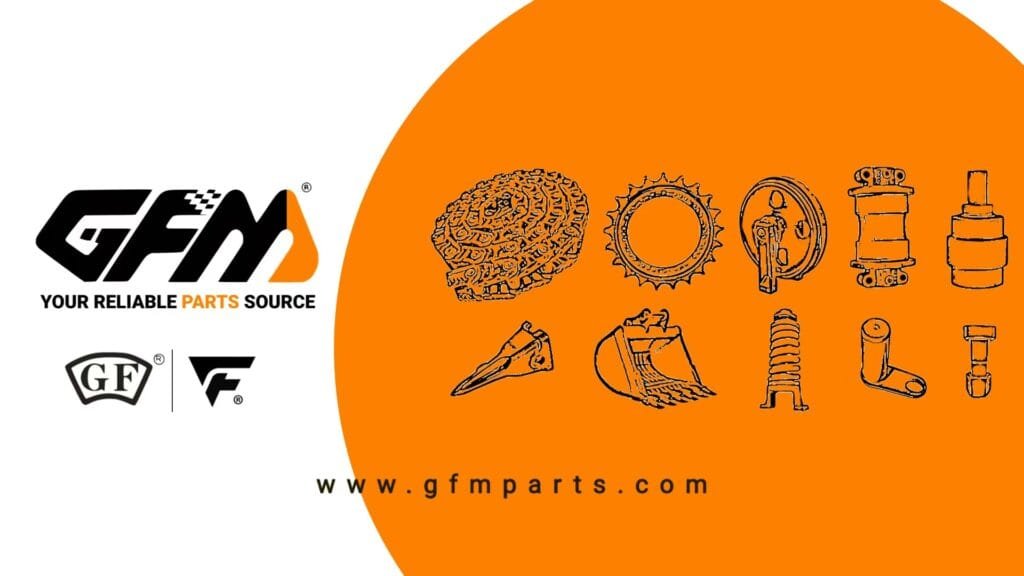