Excavator track roller is key component in the chassis system, playing an important role of support, guidance and stability, ensuring the smooth operation of the track system and the efficient operation of the machinery. Under different working environments, the performance requirements and design requirements of track rollers vary.
The key role of track rollers in the excavator undercarriage system
The track roller is an important part of the excavator track system, which directly affects the stability and operating efficiency of the machine. It is located on the inner side of the track and is usually composed of multiple track rollers, which play a role in supporting and guiding the operation of the track. The functions of the track roller are mainly reflected in the following aspects:
Supporting role
The track roller carries part of the weight of the track and is an important part of the load distribution of the excavator chassis. The track roller not only supports the track, but also helps share the total load of the machine. The size, material and structural design of the track roller are crucial to its supporting capacity:
- Size: The diameter and width of the track roller will directly affect its supporting capacity. Track rollers with larger diameters can share a larger load and adapt to heavy-duty operations.
- Material: The rollers are usually made of high-strength steel or cast iron, with a high wear-resistant coating to improve their durability. The use of alloy steel materials can effectively enhance the load-bearing capacity of the rollers and prevent deformation or breakage due to long-term high-load use.
- Bearing design: The bearings built into the rollers can help the rollers maintain good rotational stability during long-term operation, reduce friction and wear, and improve load-bearing capacity.
Guiding function
The rollers ensure that the tracks always maintain the correct path during operation through their contact with the tracks to prevent the tracks from deviating. The guiding function of the rollers directly affects the operating accuracy and safety of the excavator. The guiding effect of the rollers depends on the following parameters:
- Rim design: The design of the roller rim (the edge that contacts the track) will affect the guiding property of the track. A higher rim can effectively reduce the deviation of the track and improve the stability of the operation.
- Wheel surface structure: The wheel surface of the roller should be designed to be in close contact with the track surface to provide stable support and traction.
Protective function
Rollers also protect the chassis and other components. They disperse the load transmitted by the tracks, reduce the impact on the excavator chassis structure, and reduce the risk of damage to other parts of the chassis (such as chain rails, spindles, etc.). High-performance rollers can effectively extend the service life of the entire excavator.
The role and effect of important parameters
- Load capacity: The load capacity of the roller is a key parameter to measure its performance. When designing the roller, it is necessary to ensure that it can withstand the pressure generated by the tracks and loads to avoid failure under high loads.
- Resistencia al desgaste: The wear resistance of the roller directly affects its service life. Rollers with high hardness materials and wear-resistant coatings can be used for a long time in harsh working conditions such as mines and construction.
- Temperature stability: The working environment of the roller may be hot or extremely cold. Good temperature stability enables it to maintain its performance under various temperature conditions.
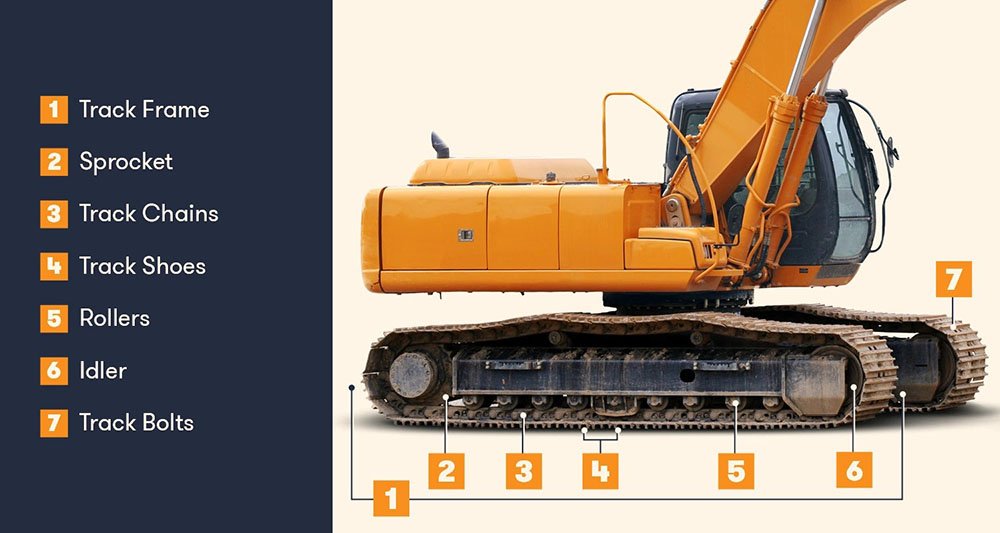
Different requirements for roller performance under different working conditions
Under different working conditions, the working conditions and pressures of the rollers are different. Therefore, the design requirements for track rollers vary for each working condition, which are manifested in differences in material, size, durability, etc.
Mining working conditions
Mining working conditions are usually harsh, and excavators need to work on soft, muddy or rocky ground. Track rollers need to have the following characteristics:
- High-strength steel: In mining operations, track rollers are often faced with large impact forces and wear, so high-strength alloy steel materials must be used, which can withstand high loads and impact forces.
- Corrosion resistance: There are many humid and corrosive substances in the mining environment, and track rollers need to have good corrosion resistance to prevent rusting during long-term operations.
- Large diameter design: A larger track roller diameter can help disperse the load and increase its impact resistance, especially when working on uneven mining ground, which can improve the stability of the equipment.
Construction working conditions
The working environment of construction sites is changeable, and excavators often need to work on uneven ground. Requirements for track rollers include:
- Strong deformation resistance: Since the ground of the construction site may be relatively uneven, the track rollers need to have strong deformation resistance. The design of the track rollers usually requires reinforcement of the wheel body to prevent deformation due to long-term load or impact.
- Guidance: The guidance of the track rollers must ensure the stable driving of the track on irregular ground and prevent the track from running off.
Agricultural working conditions
The environment of agricultural operations is usually relatively flat, but there may be more soil or sand on the ground, requiring the track rollers to have good adaptability:
- Good grip: Agricultural sites require the track rollers to adapt to soft soil, provide strong traction, and prevent the machine from sinking into the mud.
- Corrosion resistance: Since there may be a lot of water in the farmland, the track rollers should use corrosion-resistant materials to prevent rust.
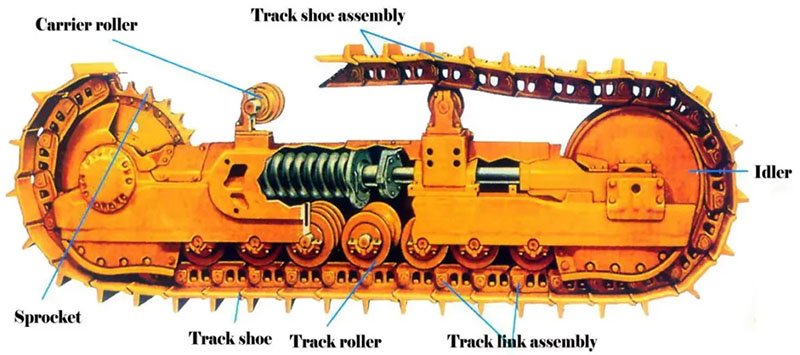
Industry standard interpretation: ISO and CE certification requirements for track roller manufacturing
The design and manufacturing of track rollers must comply with certain industry standards and certification requirements to ensure their quality and safety. Common industry standards include ISO 9001, CE certification, and ISO 9000 series standards.
ISO 9001
ISO 9001 is a quality management system standard developed by the International Organization for Standardization (ISO), which requires manufacturers to strictly control quality during design, production and after-sales service to ensure product reliability and consistency. For roller manufacturers, ISO 9001 certification means:
- Quality management system: A strict quality management system must be established and implemented, covering design, material procurement, production process, inspection and other aspects to ensure that each batch of rollers meets quality standards.
- Continuous improvement: Companies that meet ISO 9001 standards must regularly evaluate the quality of their products and make continuous improvements to ensure that their products can adapt to the ever-changing market.
CE certification
CE certification is a safety certification mark for the European market. If roller manufacturers want to enter the EU market, they must meet the requirements of CE certification. For rollers, CE certification requires:
- Safety requirements: Ensure that the design and manufacture of rollers comply with EU safety regulations and avoid the use of hazardous substances that may cause harm to operators or equipment.
- Environmental protection: CE certification also requires that the materials and production process of the rollers comply with the EU’s environmental protection standards to reduce negative impacts on the environment.
ISO 9000 series
The ISO 9000 series is an international standard for quality management. Roller manufacturers should ensure that their design, production and inspection processes meet this series of requirements. The implementation of the ISO 9000 series helps manufacturers improve production efficiency, reduce waste and ensure high-quality roller products.
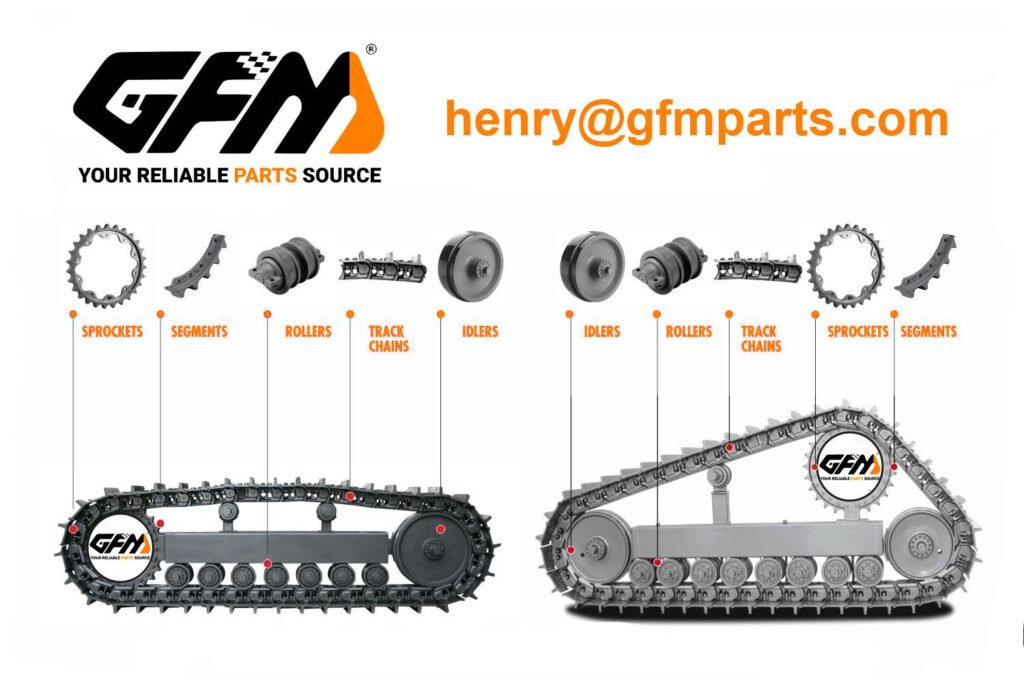
Roller failure case analysis: How to avoid equipment downtime losses?
Roller failure may cause excavator downtime, affecting construction progress and economic benefits. The following are several common roller failure cases and preventive measures:
Excessive wear
During long-term use, the roller surface may be severely worn due to hard ground or too many stones. Excessive wear may cause the roller to no longer effectively support the crawler.
Preventive measures: Choose materials with strong wear resistance, such as high-hardness steel, and regularly check the wear of the rollers, and replace the rollers with severe wear in time.
Insufficient lubrication
Insufficient lubrication will increase the friction between the roller and the bearing, increase wear, and eventually lead to the failure of the roller.
Preventive measures: Regularly check the amount of lubricating oil and lubrication status of the roller to ensure that the lubricating oil is sufficient and replaced in time.
Material fatigue and cracks
Long-term high-intensity workload may cause fatigue and even cracks in the material of the roller, which will lead to the fracture of the roller.
Preventive measures: Select high-strength alloy steel and conduct strict inspections through a meticulous quality control process to ensure that the material of the roller can withstand the workload.
Impact damage
The roller may be damaged when encountering a large impact force, especially in mining conditions.
Preventive measures: Strengthen the impact absorption design of the roller to ensure that it can effectively absorb the impact force and prevent cracking when encountering an impact.
Obtenga una cotización rápida y gratuita | Correo electrónico: henry@gfmparts.com | WhatsApp: +86 17705953659 |
Regular maintenance, timely inspection and selection of suitable materials can effectively avoid the failure of the roller and extend its service life.
The role of the excavator bottom roller in the chassis system is crucial. It not only undertakes key functions such as support, guidance and protection, but also exhibits different performance requirements under different working conditions. By having an in-depth understanding of industry standards and timely maintaining and servicing the track rollers, the service life and working efficiency of the equipment can be significantly improved.
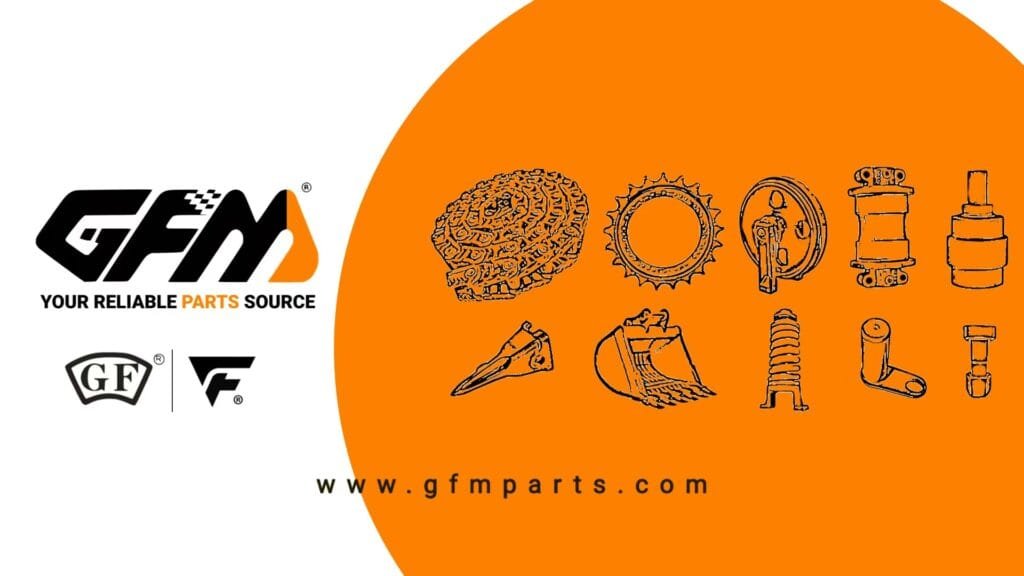