Track shoes are an important part of the excavator track system, which directly affects the stability and operating efficiency of the equipment in complex terrain. In the field of construction machinery, track shoes are not only a key component for transmitting power, but also the basis for ensuring the stable driving of the excavator.
What are track shoes?
Track shoes are the main components of the excavator track chain and are usually made of high-strength steel. They are designed to provide strong grounding capabilities to ensure the normal operation of the equipment on various complex terrains. The track shoes are connected by bolts fixed to the track chain to form a closed track system.
Classification of track shoes:
- Single-tooth track shoes: suitable for soft terrain, such as sand or snow.
- Double-tooth track shoes: used in general earthworks.
- Three-tooth track shoes: suitable for hard terrain such as rocks.
Choosing the right type of track shoes according to the construction scenario can effectively improve operating efficiency and reduce equipment wear.
Function and working principle of track shoes
Increase ground contact area
Track shoes evenly distribute the weight of the excavator over a larger area of the ground, effectively reducing the unit ground pressure and preventing the equipment from sinking into soft ground.
Provide grip
The track shoe pattern design provides additional grip to ensure the stability of the equipment on slippery, rugged or steep terrain.
Power transmission
The track shoe transmits the power of the engine to the ground through the cooperation of the chain and the drive wheel, pushing the excavator forward or turning.
Protect the ground and equipment
High-quality track shoes not only protect the track chain and drive device, but also reduce damage to the ground, especially when working in sensitive areas.
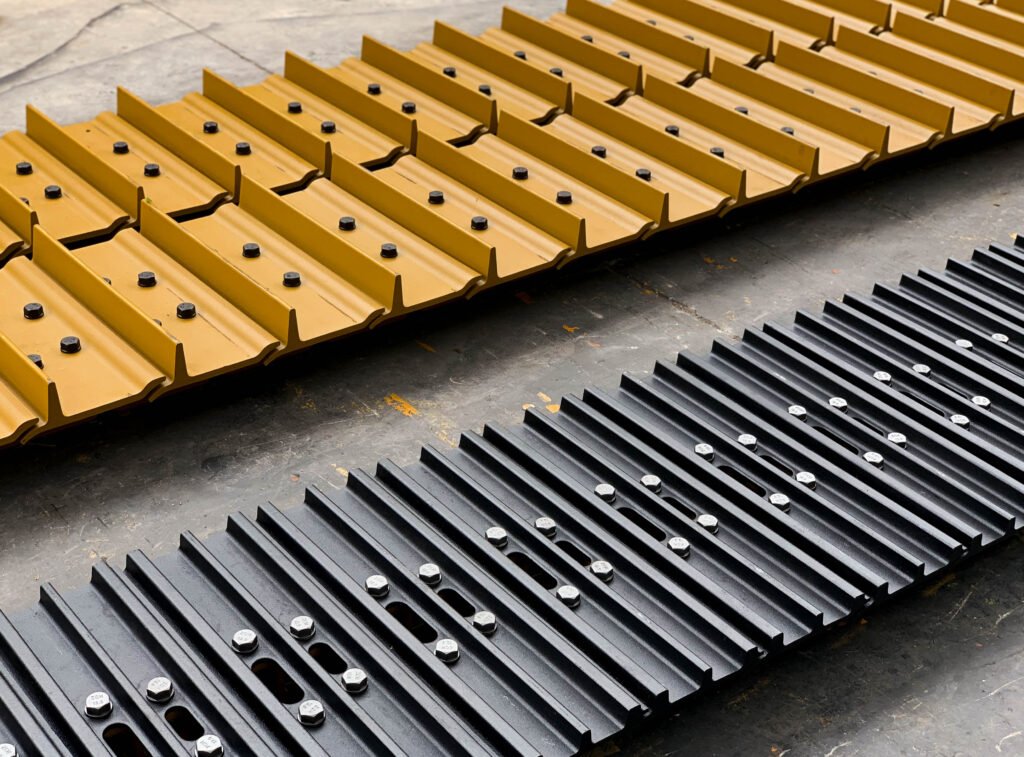
How to judge the quality of track shoes?
Material and process
High-quality track shoes are usually made of high-strength alloy steel, and the wear resistance and impact resistance are improved through heat treatment processes such as quenching and tempering.
Dimensional accuracy
The size and hole spacing of the track shoe must strictly meet the standards to ensure a perfect match with the track chain and other components.
Surface treatment
Anti-corrosion coating can extend the service life of track shoes, especially when working in wet or chemically corrosive environments.
Durability test
High-quality track shoes need to pass a number of rigorous tests, including wear resistance, crack resistance and bending resistance tests to verify their reliability in high-intensity working environments.
Core advantages of GFM track shoes
As an industry-leading excavator parts manufacturer, GFM has accumulated rich experience in the research and development and production of track shoes. The following are the unique advantages of GFM track shoes:
High-quality materials and high-precision technology
GFM track shoes are made of world-class high-strength alloy steel and undergo a unique heat treatment process to give them excellent wear resistance and impact resistance.
Diversified specification design
GFM provides track shoes of various specifications to meet the needs of different types of excavators and various working environments. In addition, the company also supports customized services to ensure that the products fully meet the personalized requirements of customers.
Strict quality control
Each track shoe must pass multiple quality inspection processes from raw material testing to finished product testing, including wear resistance testing, tensile strength testing and actual working condition simulation testing.
Wide range of uses
Suitable for all terrains – rock, mud or soft ground.
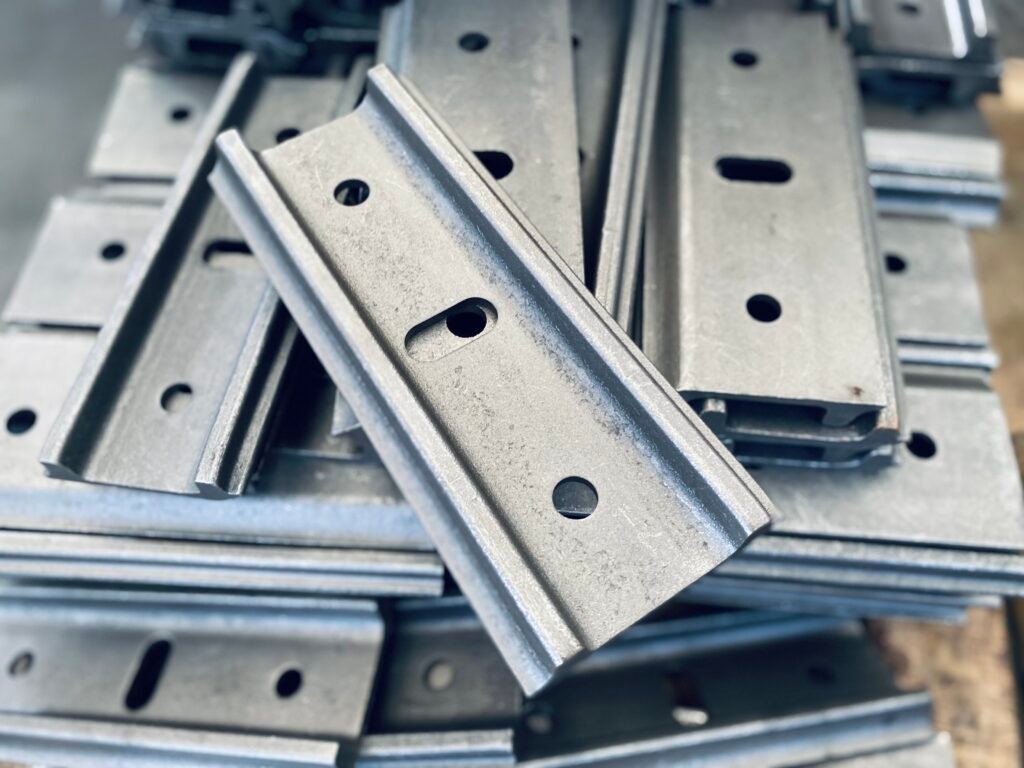
How to maintain track shoes?
As a vulnerable part in high-intensity operations, the service life of track shoes is closely related to daily maintenance. The following are key measures to effectively extend the service life of track shoes:
Regular cleaning
After the operation, remove the mud and stones on the track shoes in time to avoid abnormal wear due to accumulation.
Check the tightness of bolts
Regularly check whether the bolts connecting the track shoes to the chain are loose, and tighten them if necessary to prevent them from falling off due to vibration.
Lubricate the chain
Regularly add lubricating oil to the track system to reduce the friction between the track shoes and the chain.
Monitor wear
When the thickness of the track shoes is reduced to 50% of the original thickness or obvious cracks appear, they should be replaced in time to avoid further damage to other parts.
Regularly check the track tension
Maintaining proper track tension can prevent derailment and reduce additional wear on the track shoes.
GFM track shoe factory strength display
Automated production equipment
GFM has introduced the world’s leading fully automated production line to ensure the efficiency and accuracy of products from manufacturing to delivery.
Strong R&D team
GFM has a professional R&D team dedicated to the development of new materials and innovative designs for track shoes, and continuously optimizes product performance.
Perfect supply chain system
GFM has established long-term cooperative relationships with many international suppliers to ensure the high quality and stable supply of raw materials.
Environmentally friendly production process
Adhering to the concept of green manufacturing, GFM vigorously reduces carbon emissions during the production process and meets global environmental standards.
As an important component of the excavator, the performance of the track shoe has a profound impact on the operating efficiency and service life of the equipment. GFM track shoes are a trustworthy choice for customers with their excellent quality, professional services and industry-leading technical advantages. If you have any needs or questions, please feel free to contact us!
Email: henry@gfmparts.com
Whatsapp: +86 17705953659
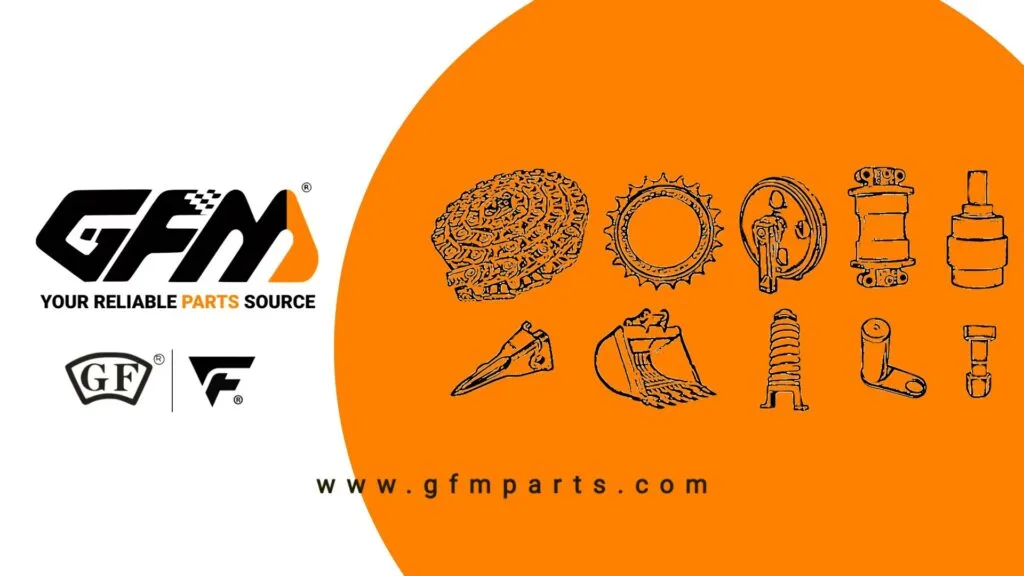