Table of contents
- Importance of excavator engine equipment maintenance
- Daily maintenance for excavator engines: routine inspection and cleaning and maintenance tips
- Professional tools and maintenance methods: accurate detection and systematic preventive measures
- Engine fault diagnosis and prevention strategy: from data monitoring to preventive maintenance plan
- Maintenance record management and intelligent data monitoring: Building a long-term guarantee system
Importance of excavator engine equipment maintenance
As an indispensable heavy equipment in engineering construction, the engine of the excavator undercarriage parts is the core of the operation of the entire mechanical system. Engine equipment maintenance is not just about regularly changing oil or cleaning filters, but a systematic project that covers all aspects of prevention, detection, adjustment and recording. The importance and basic principles of maintenance are explained in detail below:
- Ensure efficient operation of equipment:
- Excavators are generally in a state of long-term high-load operation at the construction site. Regular engine maintenance can ensure that all engine components are in the best condition, thereby ensuring the efficient and continuous operation of the whole machine, and effectively preventing the impact of sudden failures on the progress of the project.
- Extend engine service life:
- Every equipment manager hopes that the equipment investment can be fully returned. Through scientific maintenance, reducing internal wear of the engine, not only the daily maintenance rate is reduced, but also the deep damage caused by long-term neglect is avoided, thereby greatly extending the service life of the engine and the whole machine.
- Save maintenance costs and reduce the risk of failure:
- When the engine is not running properly, it is easy to cause a chain failure, resulting in downtime, increased maintenance costs and even accidents. Standardized maintenance procedures can detect abnormalities at an early stage and deal with them in time to prevent small problems from escalating into major failures. According to some authoritative studies, regular maintenance can reduce the risk of sudden failures by up to 30%.
- Improve engineering safety and environmental benefits:
- The operating status of the engine not only affects work efficiency, but also affects site safety and environmental protection. Problems such as engine overheating and incomplete combustion may cause fires or excessive emissions. Regular maintenance can effectively reduce such hidden dangers and meet modern environmental protection and safety standards.
Engine equipment maintenance is not only the key to extending equipment life, but also an important part of ensuring project progress and construction safety. Next, we will introduce more specific maintenance strategies and practical methods from a practical operation perspective.
Daily maintenance for excavator engines: routine inspection and cleaning and maintenance tips
Daily maintenance is a prerequisite for ensuring the smooth operation of excavator engines. Good daily maintenance can detect potential problems in time and prevent serious failures. The following are detailed daily maintenance steps and tips:
Check the engine oil and lubrication system
- Oil inspection and replacement:
- Before starting the machine every day, check the oil level and color to ensure that there are no impurities.
- It is recommended to change the engine oil every 200-300 hours according to the working environment and engine running time, and use high-quality engine oil that meets international standards.
- When changing the engine oil, it is recommended to change the oil filter at the same time to prevent impurities in the old oil from affecting the lubrication performance of the new oil again.
- Periodic lubrication of lubrication points:
- Regularly adding lubricating oil to all high-friction parts can reduce component wear.
- It is recommended to use a special lubrication gun and strictly follow the manufacturer’s instructions to prevent uneven lubrication or oil leakage.
Maintenance and inspection of the cooling system
- Coolant monitoring:
- Overheating of the engine is a common problem, so it is important to check the coolant level and concentration regularly.
- Check the radiator once a month to ensure that there is no blockage; the cycle of changing the coolant can be appropriately shortened in high temperature environment or heavy load conditions.
- Radiator and water pump:
- Check whether there is any foreign matter blocking the surface of the radiator, and clean it regularly to ensure heat dissipation efficiency.
- As a key part of the cooling system, it is recommended to check the water pump every six months to prevent water leakage or poor operation.
Air filter and fuel system maintenance
- Air filter cleaning and replacement:
- Excavators operate in dusty construction sites, and air filters are prone to clogging. They should be checked and cleaned or replaced every 100 hours of work.
- Filters using high-efficiency filter materials can not only improve air purity, but also help improve engine combustion efficiency.
- Fuel system maintenance:
- Check fuel quality regularly to prevent poor quality fuel or water from mixing into the injector and causing clogging.
- It is recommended to clean the injection system every 300 hours and replace the fuel filter simultaneously.
Electronic control system and sensor inspection
- Electronic control unit (ECU) detection:
- Use OBD or special detection instruments to regularly read the engine’s fault code and parameter data.
- After any abnormal indicators are found, they should be reviewed immediately or contact professional technicians for processing.
- Sensor calibration:
- Sensors such as temperature, pressure, and vibration are important monitoring elements for the health of the engine.
- Regularly calibrate and clean sensors to ensure accurate data and provide a basis for subsequent preventive maintenance.
Through the above daily and regular inspection measures, you can fundamentally ensure that the engine is in the best operating condition. Developing good daily maintenance habits can not only effectively reduce the occurrence rate of failures, but also quickly take countermeasures when abnormalities are found to avoid the expansion of problems.
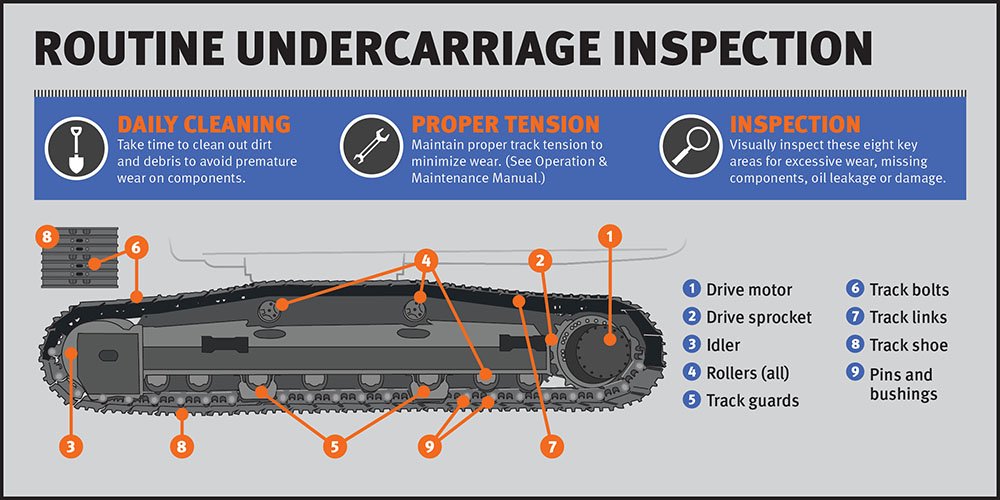
Professional tools and maintenance methods: accurate detection and systematic preventive measures
In order to further improve the refinement and systematization of engine maintenance work, the use of professional tools and equipment has become an industry standard. Here are some common professional tools and their applications, and detailed descriptions of several effective detection and prevention methods.
Professional diagnostic instruments
- Engine health tester:
Use digital instruments to read engine operating parameters such as oil pressure, temperature, speed, vibration frequency, etc., and form data reports.- Advantages: Real-time monitoring, early warning; by comparing historical data, the time period and components of the problem can be accurately located.
- Recommended brands: Well-known brands such as BOSCH and DELTA, whose equipment has been internationally certified, are guaranteed for accuracy and durability.
- Infrared thermometer:
Use non-contact infrared temperature measurement technology to quickly obtain temperature distribution maps of various parts of the engine.- Application scenarios: Especially suitable for checking whether there are hot spots in the radiator and cooling system to prevent damage caused by local overheating.
Data monitoring system and predictive maintenance platform
- Comprehensive monitoring platform:
Use IoT technology to monitor the engine operation status around the clock, and transmit data to the cloud platform in real time for remote diagnosis.
- Intelligent early warning system:
According to historical data and equipment use cycle, the system can automatically generate maintenance plans and early warning reminders to ensure the systematic and continuous maintenance work.
Standardized operating procedures and training system
- Standardized maintenance procedures:
Prepare detailed maintenance manuals and operating specifications, covering oil replacement, filter cleaning, cooling system maintenance, electronic testing and other aspects.- Execution points: Each operation step has clear standards and evaluation indicators to reduce human errors and ensure scientific and efficient maintenance work.
- Regular professional training:
Regular technical training is carried out for maintenance personnel, focusing on the use of new detection instruments and the latest maintenance technology.- Training content: Including equipment theoretical knowledge, fault case analysis, on-site emergency handling and the use of data monitoring systems to enhance the overall professional level of the maintenance team.
By introducing the above professional tools and systematic methods, you can not only accurately control the working status of the engine, but also prevent potential risks in advance to ensure the long-term stable operation of the equipment. These measures not only show a high level of professional technology, but also reflect the scientific attitude and sense of responsibility for equipment management, and have won high recognition from the market and users.
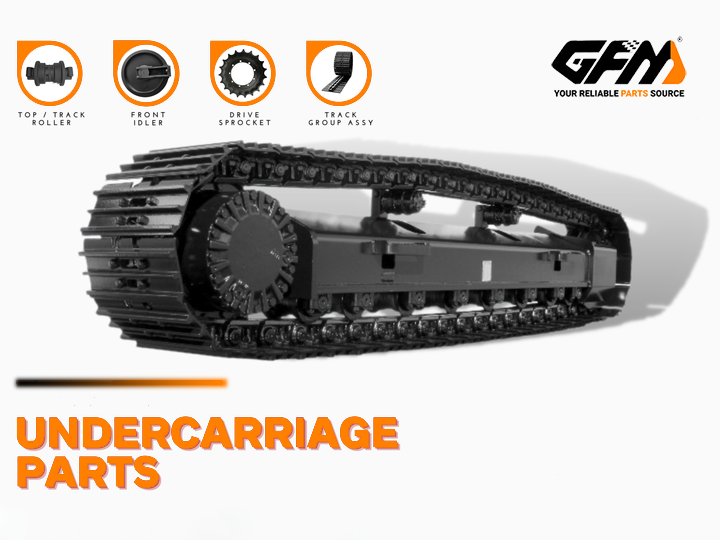
Engine fault diagnosis and prevention strategy: from data monitoring to preventive maintenance plan
When the excavator operates under high load conditions, engine problems often come quickly and hidden. The implementation of comprehensive fault diagnosis and prevention measures can significantly reduce the incidence of emergencies. The following steps introduce how to establish and implement a scientific preventive maintenance strategy.
Fault code and data comparison analysis
- Regular fault code detection:
Read and record fault codes regularly through the OBD interface and professional diagnostic equipment. Compare historical data to find abnormal changes.- Suggestion: Establish a fault code database to facilitate technicians to quickly locate problems and predict possible fault trends.
- Data comparison and trend analysis:
Use big data analysis tools to compare current data with historical records to capture minor anomalies.- Operation method: Set data thresholds. When the threshold is exceeded, the system automatically issues an early warning and arranges inspections and repairs in a timely manner.
Temperature, vibration and pressure monitoring
- Temperature monitoring:
Install thermistors and infrared monitoring instruments to monitor the temperature of key areas in the engine in real time.- Application suggestions: Combined with cooling system inspection, regularly check whether there is poor heat dissipation or local overheating.
- Points to note: Clean the radiator in time to ensure heat exchange efficiency and avoid aging of components due to high temperature.
- Vibration detection:
- Use acceleration sensors to monitor engine vibration and capture signals of loose bearings or unbalanced components.
- Practical effect: Abnormal vibration data usually indicates an early sign of mechanical failure. Once discovered, the machine should be stopped for inspection immediately.
- Oil pressure and fuel pressure monitoring:
Compare oil pressure and fuel pressure data under different working conditions to ensure that there are no abnormal fluctuations in the liquid system.- Common tools: Equipped with digital oil pressure gauge and pressure sensor, combined with intelligent data analysis system to ensure accurate judgment.
Develop preventive maintenance plan
- Periodic repair and maintenance plan:
According to the working conditions, formulate a detailed preventive maintenance plan, including monthly, quarterly and annual inspection items and operating standards.- Plan content: Each cycle should include oil replacement, filter cleaning, electronic testing, cooling system maintenance, fuel system maintenance, etc.
- Implementation details: Each operation has a clear person in charge and time node to ensure that no link is missed.
- Emergency plan and emergency mechanism:
For major parameter abnormalities detected, establish a rapid response plan.- Emergency measures: If the engine temperature exceeds the standard, the oil pressure drops, etc., immediately start the emergency maintenance process to ensure that the equipment is shut down for maintenance to avoid secondary damage.
- Information feedback: After each emergency maintenance, record the detailed cause and processing process to provide experience data for subsequent maintenance.
Through systematic fault diagnosis and preventive maintenance strategies, the incidence of emergency failures can be greatly reduced to ensure that the engine is always in the best operating state. Data-driven intelligent early warning systems and detailed maintenance plans not only help companies save costs, but also reflect the modern equipment management model that combines technology and management.
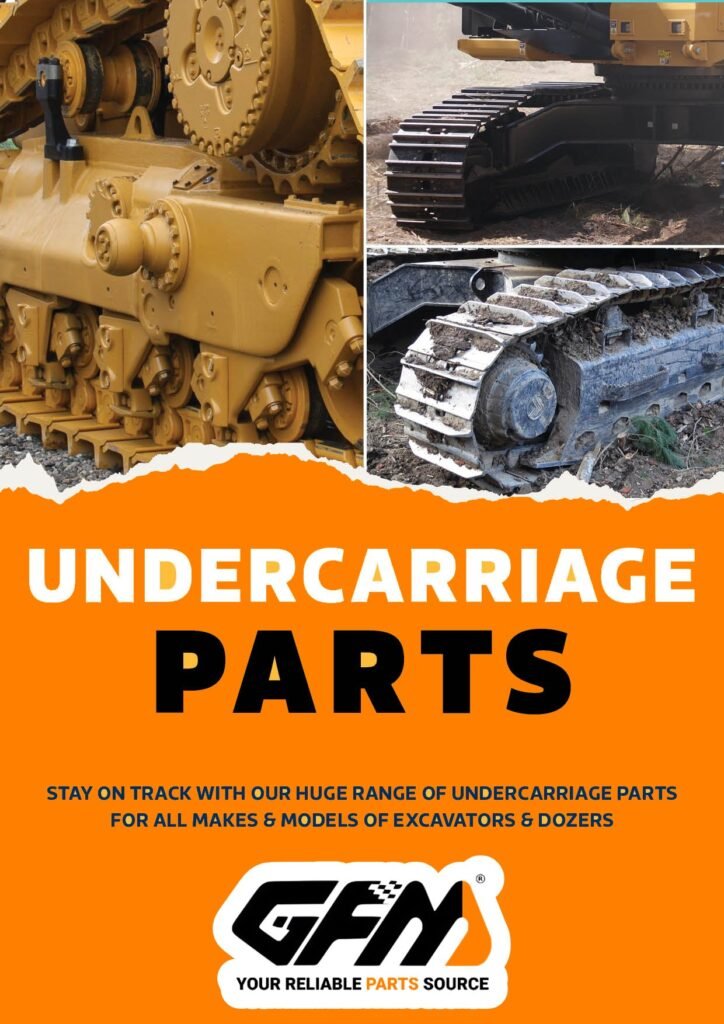
Maintenance record management and intelligent data monitoring: Building a long-term guarantee system
Efficient maintenance record management and intelligent data monitoring are important foundations for ensuring the long-term stable operation of the engine. Both daily inspection data and preventive maintenance records should be systematically archived and analyzed. The following are detailed steps and suggestions for building this system.
Detailed maintenance log records
- Maintenance record content:
After each inspection, maintenance or failure, record detailed data such as operation time, execution items, replacement parts, tools used and specific values.- Practical suggestions: The record form should cover the project name, operator, observation results, recommended measures and follow-up tracking feedback information to ensure that the data is true, comprehensive and traceable.
- Standardized recording process:
Make a record template in a unified format to ensure that all maintenance data is uniformly entered into the electronic database.- Long-term benefits: Records can not only serve as a basis for judging the health status of equipment in the future, but also assist in analyzing the frequency of failures and provide statistical data support for preventive maintenance.
Digital management and intelligent data analysis
- Equipment management system:
Introduce equipment management software to digitally manage all maintenance records and establish equipment archives.- Functional features: The system can automatically count key data, generate data charts, remind maintenance cycles and abnormal warnings, and facilitate managers to make timely decisions.
- Application of big data and cloud platform:
Use cloud platform data synchronization technology to achieve centralized management of multi-device data.- Operational advantages: Analyze and compare maintenance data under different equipment and different working conditions to provide support for the formulation of unified and scientific maintenance strategies for the entire fleet.
Team collaboration and information sharing mechanism
- Regular training and experience sharing:
Establish an experience exchange mechanism within the maintenance team, regularly organize technical discussions and case sharing sessions, and jointly solve maintenance problems.- Team building: Each technician participates in data entry and analysis training to improve the overall team skills and enhance collaborative combat capabilities.
- Manufacturer and third-party cooperation:
Regularly share data with engine manufacturers and professional testing agencies to obtain the latest technical support and improvement suggestions.- Cooperation form: Regularly feedback equipment operation data, participate in the manufacturer’s technical seminars, and jointly develop more rigorous preventive maintenance plans.
Through a complete maintenance record management and intelligent data monitoring system, enterprises can be data-driven, continuously optimize maintenance strategies, and improve the overall operation stability of equipment. This scientific management model not only reduces the equipment failure rate, but also enhances the company’s professionalism and authoritative image in the industry.
Get a quick free quote | Email: henry@gfmparts.com | Whatsapp: +86 17705953659 |
Excavator engine equipment maintenance is a systematic project, from basic daily inspections and regular cleaning to precise monitoring with professional equipment, and then to the establishment of a complete record and early warning mechanism, each step is crucial.
In the fierce competition of engineering projects, scientific maintenance can not only reduce the risk of failure and unnecessary maintenance costs, but also greatly extend the service life of equipment and ensure safe and efficient operation of the engineering site. Whether you are a novice or a senior technical expert, you can find maintenance strategies and tool suggestions suitable for you in this article. I hope that these professional and practical suggestions can help you deal with every inspection and every maintenance with a relaxed and friendly attitude, so that the excavator can always maintain the best condition and bring continuous and stable power to your engineering projects!
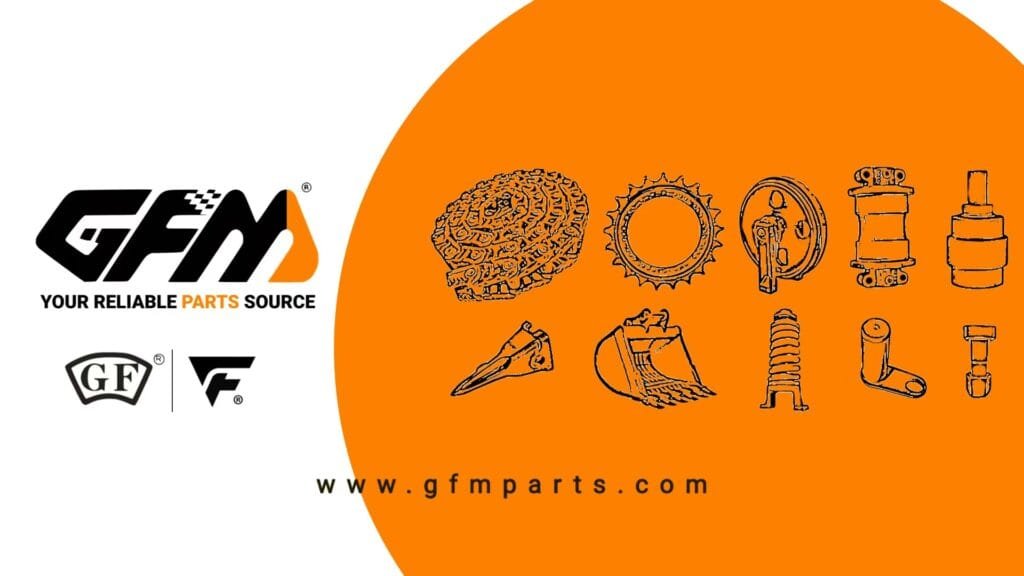