In the field of construction machinery, excavators are undoubtedly indispensable and important equipment. As a key component of the excavator, the performance and quality of the excavator bucket teeth directly affect the operating efficiency and service life of the excavator.
Definition and classification of excavator bucket teeth
As the name suggests, the excavator bucket teeth are the parts at the front end of the excavator bucket that are used to directly contact, crush and excavate materials. It usually consists of two parts: the tooth seat and the tooth tip, which are connected by a precise pin shaft to ensure stability and efficiency in complex and changing working environments. Depending on the application scenario, bucket teeth can be divided into many types:
- Rock teeth: designed for hard rock operations, using high-strength alloy materials, with excellent wear resistance and impact resistance.
- Earthwork teeth: suitable for excavating softer materials such as soil, sand and stone, and the design focuses more on durability and efficiency.
- Conical teeth: mostly used in coal mining, its unique conical design helps reduce material adhesion and improve excavation efficiency.
The role and working principle of bucket teeth
Excavator bucket teeth are not only vulnerable parts on excavators, but also a “shield” that protects the bucket as a whole from excessive wear. During the excavation process, the bucket teeth effectively crush the materials through their sharp edges and solid structure, and use the lever principle of the bucket to load the materials to the designated location. The conical design of the bucket teeth and the reasonable layout between the teeth make the excavation force more concentrated and improve the working efficiency.
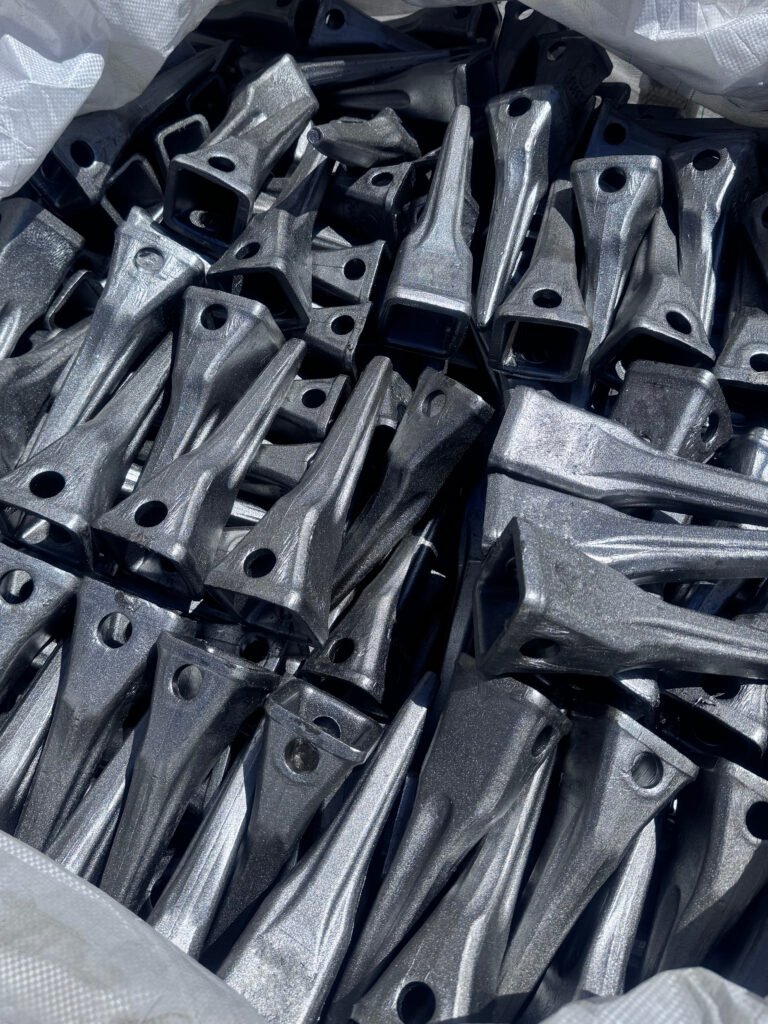
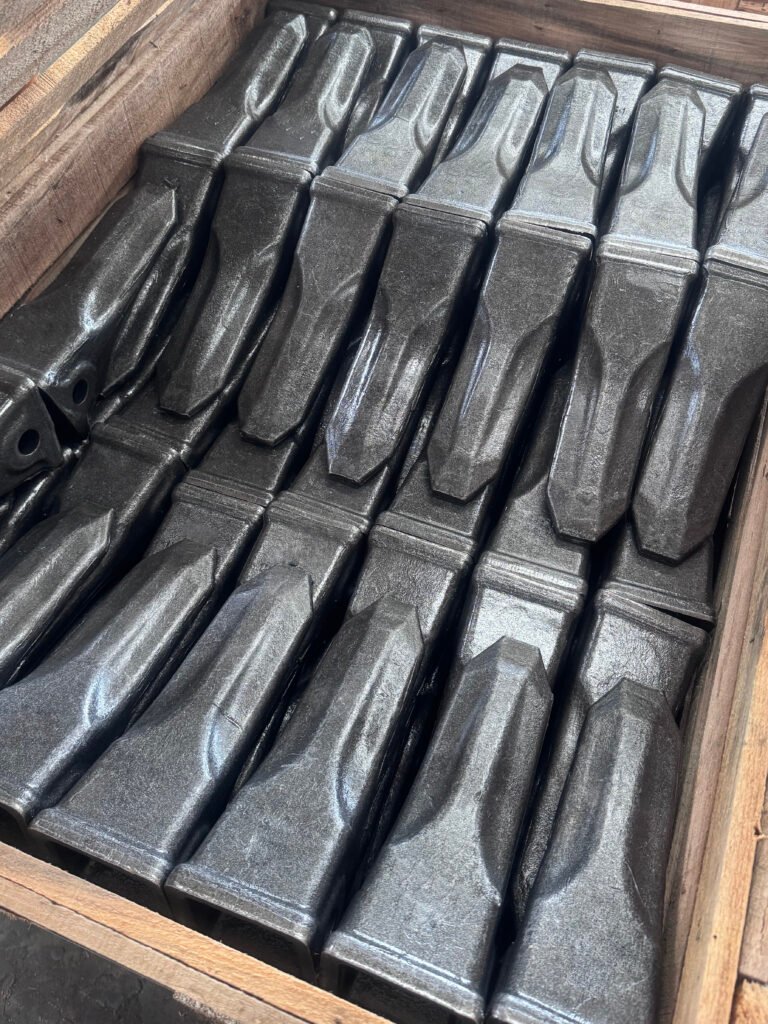
Production process
GFM excavator bucket teeth production process combines modern technology and craftsmanship to ensure that each product meets the highest standards:
- Material selection: Select low-alloy wear-resistant steel as raw material to ensure the high strength and wear resistance of the bucket teeth.
- Heating and forging: Heat the raw materials to a suitable temperature and perform rough forging through an air hammer or press to form a basic T-shaped structure.
- Forming and trimming: Use the forming die for stamping to ensure the accurate shape of the bucket teeth, and then perform processes such as trimming and trimming.
- Punching and marking: Punch the pin shaft hole on the bucket teeth and mark the brand mark for easy identification and installation.
- Heat treatment: Improve the hardness and wear resistance of the bucket teeth through heat treatment processes such as quenching.
- Surface treatment: Shot blasting to remove the surface oxide layer, then apply anti-rust paint to enhance the anti-corrosion performance.
- Inspection and packaging: Strict quality inspection, including appearance inspection, dimension measurement, hardness test, etc., to ensure that the product is qualified before packaging and storage.
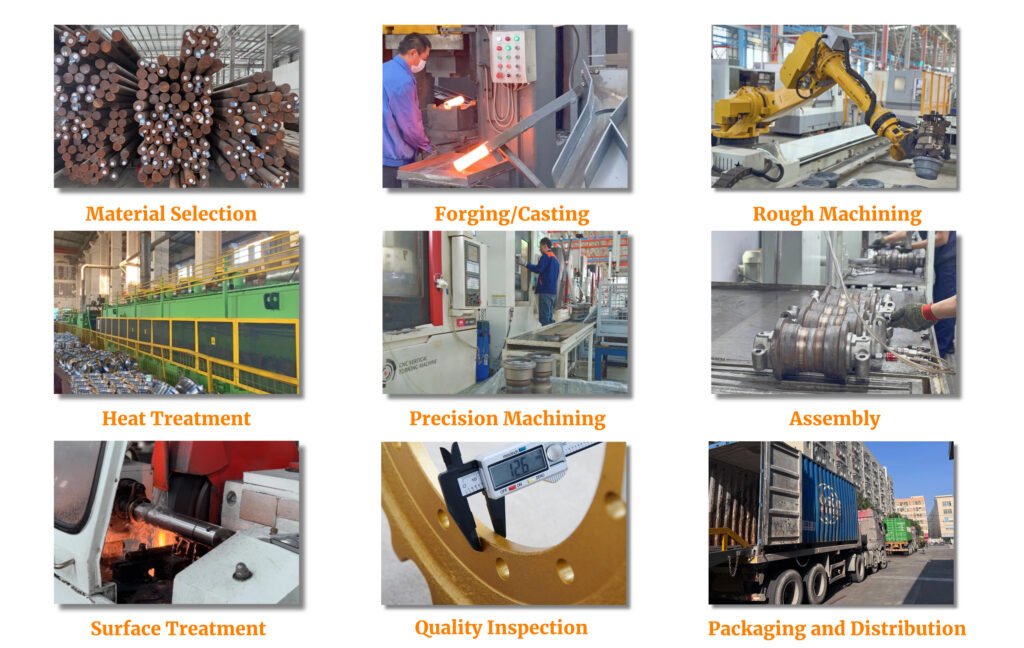
How to judge the quality of bucket teeth
- Appearance inspection: Observe whether there are cracks, bubbles, rust and other defects.
- Material and thickness: Make sure to use high-strength alloy materials and the thickness meets the design requirements.
- Abrasion and Impact Resistance: Evaluate its abrasion and impact resistance through laboratory testing.
For bucket teeth, in addition to the quality control in the above production process, the quality can also be judged by the following methods:
- Hardness test: Use a hardness tester to test the hardness of the bucket teeth to ensure that they meet the design requirements.
- Wear resistance test: simulate actual working conditions and test the wear resistance of bucket teeth.
- User feedback: Collect and analyze user feedback to understand the performance of bucket teeth in actual applications.
Significant advantages of GFM excavator bucket teeth
- High strength and wear resistance: Using high-quality alloy materials, precision forging and heat treatment ensure that the bucket teeth have excellent strength and wear resistance.
- Precise design and manufacturing: Advanced CAD/CAM technology is used for design and manufacturing to ensure accurate bucket tooth shape and improve operating efficiency.
- Easy to replace and maintain: The bucket teeth and gear seat adopt standardized design, which facilitates quick replacement and maintenance and reduces the cost of use.
- Customized services: Provide customized services based on customer needs to meet the needs of different application scenarios.
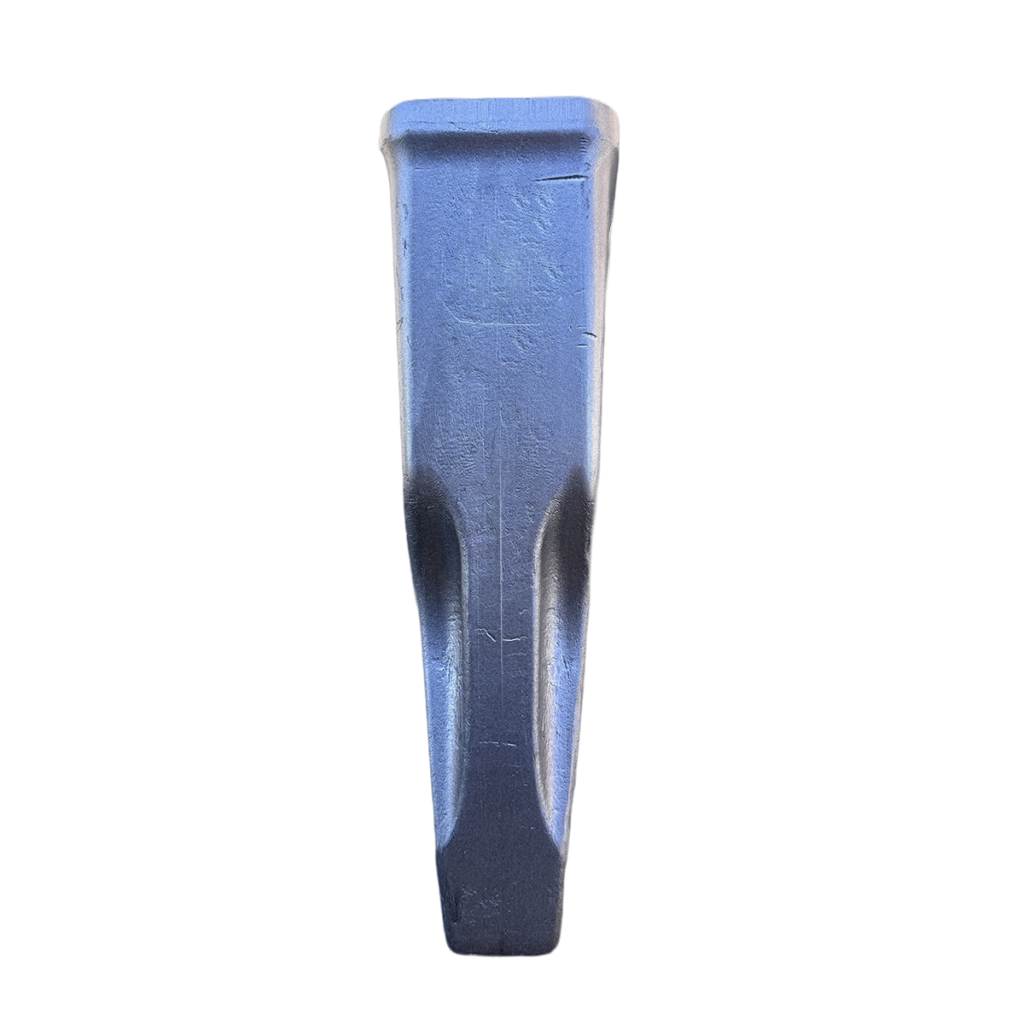
Practical suggestions for daily maintenance of excavator bucket teeth
In order to extend the service life of the excavator bucket teeth and improve operating efficiency, the following are some practical maintenance suggestions:
- Regular inspection and replacement: Regularly check the wear of bucket teeth and replace seriously worn bucket teeth in time to avoid affecting the overall performance.
- Correct operation and operation: During the excavation process, keep the bucket teeth perpendicular to the working surface to avoid excessive inclination causing bucket teeth to break. At the same time, avoid staying on hard materials for a long time or digging forcefully.
- Keep it clean and lubricated: Clean the dirt and impurities on the bucket teeth regularly to keep their surface clean. At the same time, check and lubricate the pin shaft and other connecting parts to ensure the tight fit between the bucket teeth and the gear seat.
- Proper storage and preservation: When the excavator is not in use, the bucket teeth should be stored in a dry and ventilated place to avoid moisture and corrosion.
GFM factory strength advantage
As a leader in the industry, GFM excavator bucket teeth manufacturer has its factory strength and advantages mainly reflected in the following aspects:
- Advanced production equipment: The introduction of advanced production equipment and technology at home and abroad ensures high-quality production of bucket teeth.
- Professional R&D team: We have a R&D team composed of senior engineers and technicians, dedicated to the technological innovation and upgrading of bucket tooth products.
- Perfect quality management system: A perfect quality management system has been established. From raw material procurement to finished product delivery, strict quality control is carried out in every link.
- High-quality after-sales service: Provide comprehensive after-sales service and technical support to ensure that customers receive timely and effective help during use.
Email: henry@gfmparts.com
Whatsapp: +86 17705953659
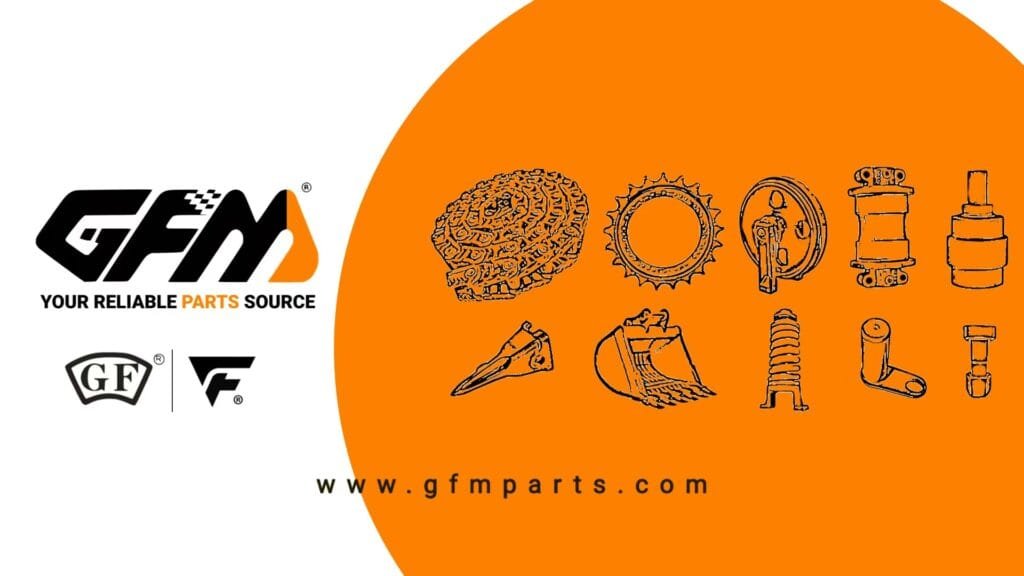