Table of contents
- Compact Excavator Selection Guide: Learn about Features and Benefits
- Key points for purchasing heavy equipment excavators: performance and applicable scenarios
- How to evaluate the key performance parameters of excavators
- Expert advice: Choose an excavator suitable for your project
- Practical tips: Excavator maintenance and accessories purchase strategy
GFM excavator parts manufacturer has always been committed to providing customers with high-quality, stable and reliable parts products. With years of industry experience and professional technology, we not only continue to innovate in product research and development, but also strive for excellence in customer service. This article aims to provide a detailed selection guide for engineering project managers and equipment maintenance teams to help you make a wise choice between compact excavators and heavy equipment excavators. We hope to provide a practical reference for your engineering decisions, so that every investment is worth the money.
Compact Excavator Selection Guide: Learn about Features and Benefits
Compact excavators are widely used in urban projects, park construction, and projects with limited working space. These devices are small, flexible, and can work efficiently in complex environments, making them a great helper for urban construction.
When choosing a compact excavator, in addition to focusing on basic performance, engineers also focus on the following professional points:
Advanced hydraulic system
- Many compact devices use the latest hydraulic technology to improve working accuracy and response speed.
- Flow and pressure control systems are fine-tuned to help achieve stable working performance.
Energy-saving and environmentally friendly design
- Efficient fuel injection system and intelligent energy recovery device can effectively reduce fuel consumption and meet modern environmental protection requirements.
- Energy-saving design not only reduces long-term operating costs, but also reduces environmental impact.
Digital control platform
- Some devices are equipped with digital dashboards and remote monitoring systems to achieve real-time data collection.
- Using Internet of Things technology, working status, fault warnings and maintenance plans can be managed intelligently.
Technology upgrade and customization
- Compact excavators can be customized according to different working conditions, such as equipped with precise control systems or additional modules.
- Manufacturers continue to provide users with more competitive products through software upgrades and hardware improvements.
Using compact excavators can significantly improve work efficiency and reduce engineering cycles. Engineering data shows that in urban construction, such equipment can save 30% to 50% of working time and reduce fuel consumption by 30%.
Engineers usually use professional simulation software and virtual reality (VR) test platforms to preview the performance of equipment in specific environments in advance to ensure that the equipment selection is accurately matched with engineering requirements.
In addition, most manufacturers also provide equipment operation data and historical performance analysis reports to help engineering decision makers better conduct cost-benefit analysis. By comparing data on work efficiency, energy consumption, failure rate, etc. of different models of equipment, companies can make scientific and reasonable purchasing decisions.
Key points for purchasing heavy equipment excavators: performance and applicable scenarios
Heavy equipment excavators are mainly used in mines, heavy-duty earthwork projects and large-scale infrastructure construction. Their high-load and high-efficiency operating capabilities provide strong support for large-scale projects.
When purchasing a heavy equipment excavator, you should not only pay attention to conventional parameters, but also comprehensively evaluate the following professional contents:
Powerful power system
- Heavy equipment uses high-power engines and efficient hydraulic transmission systems to ensure stable performance under high load conditions.
- Professional testing equipment can accurately measure the engine output and the response speed of the hydraulic system, providing strong data support for performance evaluation.
Ultra-large operating radius and arm span design
- Equipment design usually focuses on the balance between arm span length and operating radius, and improves the operating coverage area by optimizing the structure.
- In actual tests, engineers use laser ranging and 3D modeling tools to determine the optimal operating angle and range.
Durability and anti-harsh environment design
- Using high-strength steel and anti-corrosion technology, heavy equipment can adapt to harsh environments such as mines, dust and high temperatures.
- Equipment life and failure rate are verified through rigorous laboratory and field tests to ensure long-term stable operation.
Data monitoring and remote diagnosis
- Modern heavy excavators are equipped with sensor networks to monitor engine status, hydraulic pressure and temperature changes in real time.
- Using big data and cloud platforms, maintenance teams can perform fault diagnosis and preventive maintenance remotely.
Professionals suggest that when purchasing, you should also pay attention to the manufacturer’s service network and after-sales guarantee. Regular participation in technical training and maintenance seminars can help project managers better master equipment operation and maintenance skills. Actual data shows that under suitable working conditions, the production efficiency of heavy equipment can be about 40% higher than that of compact equipment, but at the same time, the professional requirements for operation and maintenance are also higher.
Before purchasing, it is advisable to conduct on-site demonstrations and comparisons of multiple brands, and obtain the operating data of each equipment under real working conditions through data acquisition instruments to ensure that the best product is finally selected.
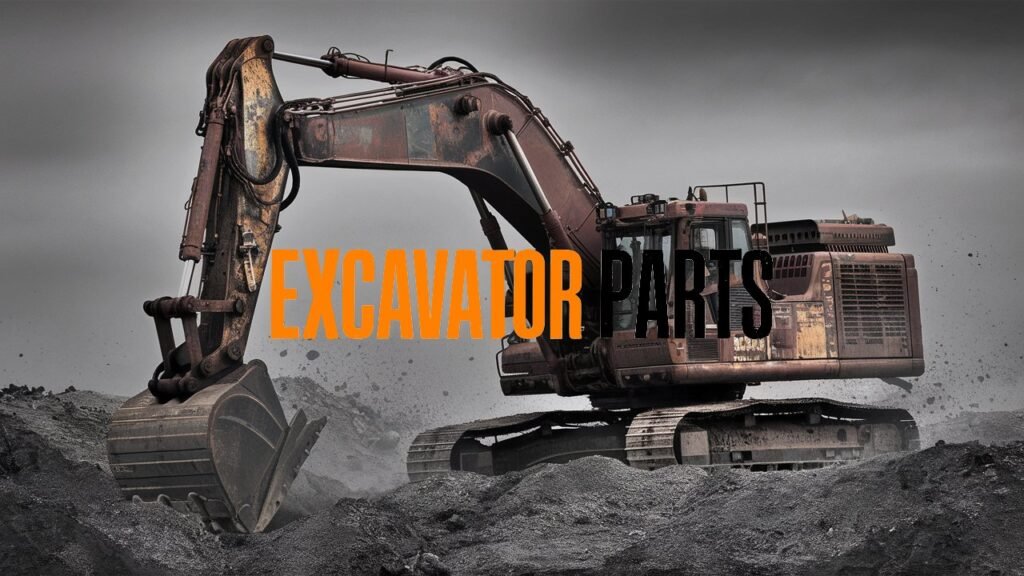
How to evaluate the key performance parameters of excavators
When choosing an excavator, it is difficult to fully reflect the performance of the equipment simply by relying on appearance and nominal parameters. Professional evaluation requires the use of scientific tools and system analysis methods to quantify the key performance of the equipment.
The following are some practical and professional evaluation methods:
Work efficiency evaluation
- Operation simulation: Use virtual simulation software to simulate the operating efficiency of the equipment under different working conditions.
- On-site testing: measure the excavation volume, handling volume and cycle time in the actual working environment, and record the changes in various indicators.
- Data comparison: use the big data platform to compare the working efficiency of different models of equipment, and form intuitive charts and reports.
Fuel consumption and economic analysis
- Sensor monitoring: install fuel flow meters to monitor fuel consumption in real time.
- Load testing: test fuel consumption data under different loads to form a standard operating fuel consumption curve.
- Economic model: calculate the operating cost of the equipment throughout its life cycle through a cost analysis model to provide a quantitative basis for investment decisions.
Operation comfort and ergonomic design
- Cab evaluation: ergonomically evaluate the cab layout, seat comfort and operation panel design to ensure comfort in long-term operations.
- Field of view detection: use a high-resolution camera system to record the driver’s perspective, analyze blind spots and operational convenience.
- Feedback collection: collect actual operator feedback through questionnaires and on-site interviews to improve equipment design and functions.
Equipment durability and maintenance indicators
- Material testing: use laboratory tensile, fatigue and impact test data to evaluate the durability of key components.
- Failure rate statistics: Analyze common equipment failures through long-term operation data and formulate preventive maintenance plans.
- Sensing technology: Use infrared thermal imaging and vibration monitoring technology to detect potential hidden dangers in advance and reduce the occurrence rate of failures.
After combining the above multiple evaluation indicators, you can use professional software to summarize the data to form a comprehensive performance report. This report not only helps with equipment selection, but also provides data support for subsequent maintenance and repairs. Engineers recommend the use of unified standards and third-party test reports to ensure the authority and reliability of the evaluation results.
Expert advice: Choose an excavator suitable for your project
In actual projects, the specific requirements and environmental conditions of each project are different, so professional advice is particularly important when choosing an excavator. The following are professional suggestions summarized by many engineering experts to help you make wise decisions:
Clarify project requirements
- Site analysis: Detailed evaluation of the space limitations, terrain characteristics and environmental conditions of the construction site.
- Task definition: Determine the main work content based on the project task, whether it is earthwork, ore excavation or fine construction.
- Risk assessment: Analyze the potential safety hazards and equipment failure risks that may be encountered during construction, and formulate response strategies in advance.
Budget and investment return analysis
- Initial investment and long-term costs: Not only pay attention to the equipment purchase price, but also evaluate the hidden costs such as daily maintenance, spare parts procurement and energy consumption.
- Payback period: Calculate the equipment input-output ratio through financial models to ensure that the investment can be recovered within a reasonable period.
- Financing plan: Explore flexible financing methods such as leasing and installment payments to reduce financial pressure.
Test machine and technical exchange
- On-site test machine: Before the equipment is officially purchased, it is recommended to organize multiple test machines to experience the response speed and stability of the equipment through actual operation.
- Expert exchange: Participate in professional forums, technical seminars and manufacturer training courses to gain an in-depth understanding of the technical characteristics of the equipment and the latest upgrade solutions.
- Case sharing: Refer to successful cases in the same industry and learn from the experience of equipment selection and application in other engineering projects.
Quality assurance and after-sales service
- Testing and certification: Pay attention to whether the equipment has passed international quality certifications such as ISO and CE.
- After-sales network: Find out whether the manufacturer has a complete national or regional after-sales service network to ensure that the equipment can be repaired in time when problems occur.
- Data transparency: Choose brands that can provide detailed historical operating data and technical documents to increase the reliability of decision-making.
Experts suggest that using professional comparison tools and data analysis platforms for multi-dimensional comparisons will help improve the scientific nature of equipment selection. Engineering decision makers can combine the actual situation of the project to form a complete set of procurement, maintenance and upgrade plans to ensure long-term stable and efficient operation of the equipment.
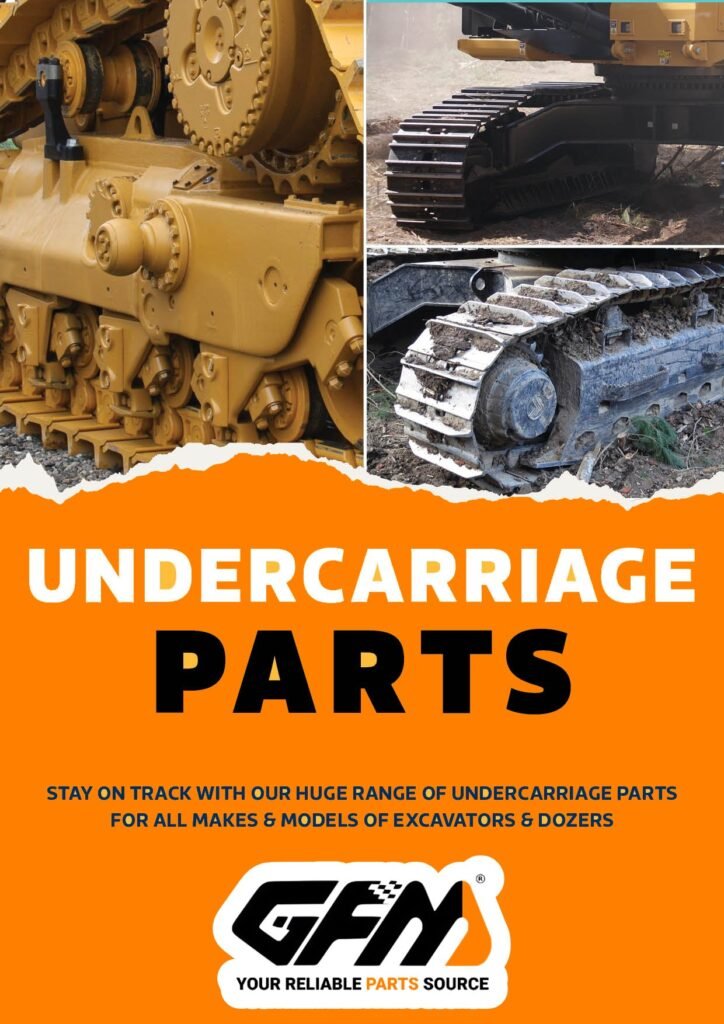
Practical tips: Excavator maintenance and accessories purchase strategy
Whether you choose a compact or heavy excavator, daily maintenance and the use of high-quality accessories are the key to ensuring equipment stability and extending service life. Here are some professional and practical maintenance and accessories purchase tips:
Regular inspection and preventive maintenance
- Maintenance plan formulation: According to the equipment manual and operating data, formulate detailed monthly, quarterly and annual inspection plans.
- Key component detection: Use professional detection tools to detect key components such as hydraulic systems, engines, and transmission systems.
- Data recording and analysis: Establish equipment maintenance files, record each inspection, replacement of parts and repair details, and predict failure risks through data analysis.
Original and certified parts are preferred
- Quality assurance: Original parts are usually strictly tested, meet equipment design standards, and can effectively extend the life of the machine.
- Supply chain management: Prefer brands with perfect after-sales service and parts supply channels to ensure that parts can be quickly replaced in the event of sudden failures.
- Performance comparison: Use professional tools to compare the performance of different brands of parts in terms of durability, matching and cost-effectiveness, and make scientific choices.
Use intelligent monitoring system
- Real-time data monitoring: Modern excavators are equipped with sensor networks, which monitor the status of equipment in real time through cloud platforms to achieve fault warning.
- Remote diagnosis and debugging: Combine the Internet of Things and big data technologies to remotely obtain equipment operation data and assist technicians to quickly locate problems.
- Customized maintenance plan: According to monitoring data and equipment operation status, timely adjust the maintenance plan to achieve precise maintenance.
Professional training and team building
- Regular training: Organize operators and maintenance personnel to participate in professional training to master the latest equipment operation and maintenance technology.
- Technical exchange: Establish effective communication channels between the maintenance team and the manufacturer’s technical support to promptly resolve difficult problems in the use of equipment.
- Experience sharing: Exchange equipment maintenance experience and optimize maintenance processes through internal sharing sessions and industry forums.
These measures are not only applicable to daily maintenance, but also help companies build a long-term equipment management system. Through scientific and systematic management, the equipment downtime rate can be reduced, the overall operating efficiency can be improved, and a win-win situation of economic benefits and safety can be achieved.
See also: How to effectively maintain and repair excavators
Get a quick free quote | Email: henry@gfmparts.com | Whatsapp: +86 17705953659 |
Selecting the right excavator is both a science and an art. Whether it is the flexible performance of compact excavators in small spaces or the strong power of heavy equipment in large-scale projects, engineering decision makers need to make a delicate balance between actual needs, budgets and environmental conditions.
Engineers can use advanced tools such as virtual simulation, IoT monitoring and big data analysis to conduct multi-dimensional evaluations of equipment performance to ensure that procurement decisions are scientific and reasonable. At the same time, through regular professional training and experience sharing, ensure that the equipment is always in the best condition in actual use.
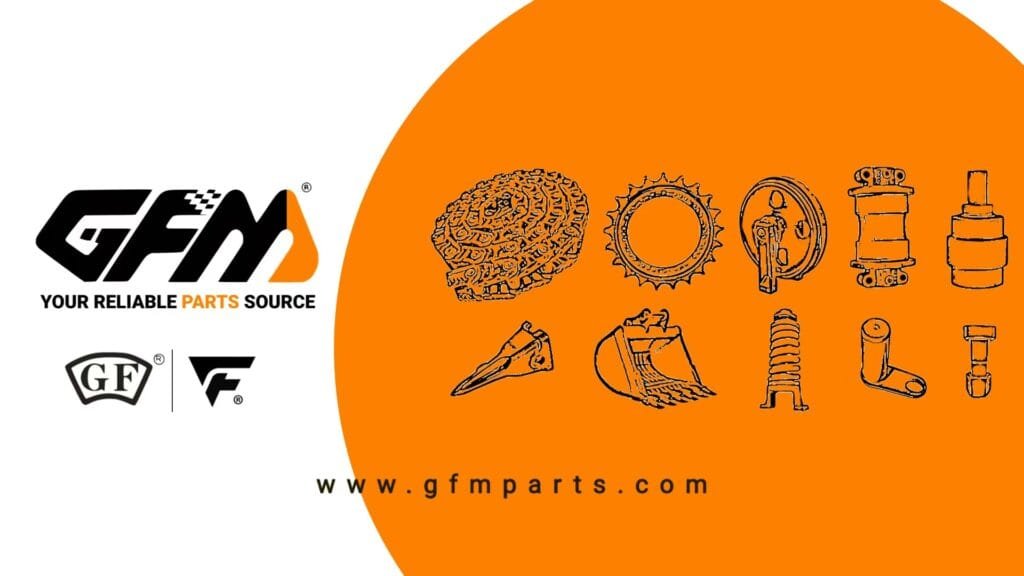