As the core load-bearing components of construction machinery, the maintenance of excavator undercarriage parts is directly related to the service life of the equipment and operational safety. As a professional produsen suku cadang undercarriage ekskavator, GFM, combined with 15 years of industry experience, will provide you with a detailed interpretation of the chassis system maintenance cycle and operating specifications to help users establish a scientific maintenance system.
Daily Maintenance and Inspection
Basic Inspection of Track System
- Tension Check: Use a ruler to measure the droop of the track. Too loose will cause derailment, and too tight will accelerate wear
- Foreign Matter Removal: Remove embedded objects such as stones and metal fragments to prevent abnormal stress on the chain links
- Visual Crack Screening: Focus on checking whether there are cracks or deformations at the chain links and track plate welds
Sprocket and Roller Status Monitoring
- Rotation Test: Manually rotate each wheel body to feel whether the resistance is uniform (abnormal jamming indicates bearing damage)
- Oil Leakage Diagnosis: Check whether there is grease seepage or pollution accumulation at the wheel body seal
- Wear Marking Method: Use chalk to mark the reference line on the wheel rim, and compare the offset the next day to determine the progress of wear
Main Points for Guide Wheel and Drive Gear Maintenance
- Tooth Block Engagement Check: Ensure that the drive tooth and the chain track pin sleeve are fully engaged. If the single tooth wear exceeds 5mm, it needs to be replaced immediately
- Grease Filling: Refill lithium-based grease through the grease nipple (select NLGI Grade 2 for temperature > -20℃)
Pre-Operation Checklist
- Track tension detection: Use a ruler to measure the track droop (recommended value 30-50mm), and adjust in time if the tightness is abnormal
- Sprocket/roller status: Visually check whether there is oil leakage, abnormal noise, and whether the temperature is abnormal (standard ≤65℃)
- Bolt tightening verification: Focus on checking the guide wheel and drive wheel mounting bolts (refer to the equipment manual for torque value, usually M24 bolts need to reach 450N·m)
- Foreign matter cleaning: Remove stones and metal fragments between the track plates to prevent stress concentration from damaging the pin sleeve
Operation Monitoring Points
- Check whether the track is deviated every 2 hours (allowable deviation ≤5%)
- Pay attention to abnormal vibration sources, especially abnormal chassis noise when turning
- Monitor the temperature of the hydraulic motor (normal range 40-80℃)
Post-operation care process
- Clean the chassis with a high-pressure water gun (pressure recommended 8-12MPa, angle 45°)
- Check the wear mark of the track shoe (GFM recommends replacing the track shoe if the wear exceeds 10mm)
- Grease replenishment: Add lithium-based grease to each lubrication point every 8 hours
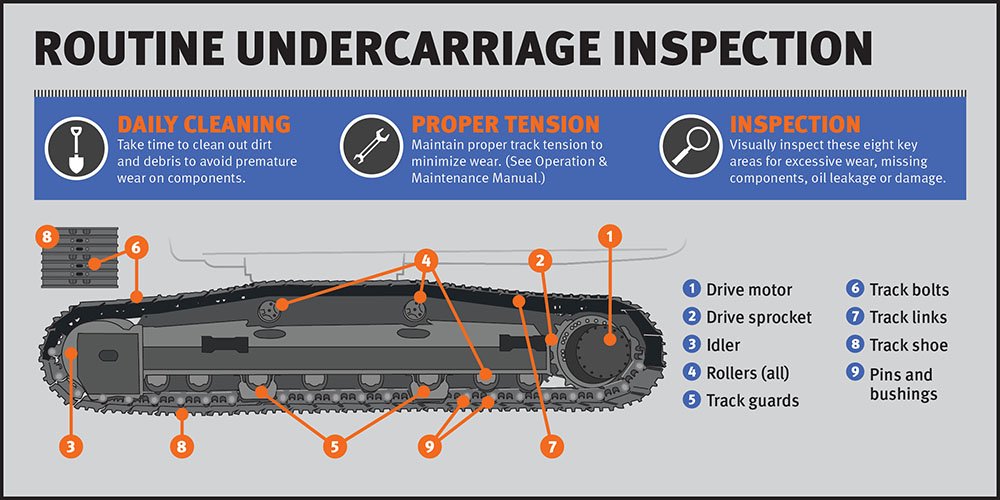
Periodic maintenance cycle
Weekly maintenance
- Track chain link inspection: Measure the chain link elongation (standard value <3%)
- Drive gear clearance: Use a feeler gauge to check the tooth side clearance (recommended 0.2-0.4mm)
- Buffer spring inspection: Measure the free length change (allowable tolerance ±5mm)
Monthly maintenance
- Track assembly flip: Implement 180° adjustment of the track to extend its life
- Track wheel seal test: Conduct a 3-minute immersion test, and the leakage volume is <5ml/min
- Bolt secondary tightening: Retighten all connectors according to the standard torque
Quarterly deep maintenance
- Measure the guide wheel sleeve clearance (limit value 1.5mm)
- Check the rotation flexibility of the track pin sleeve (rotation resistance ≤15N·m)
- Check the tooth shape of the drive wheel (replacement is required if the wear exceeds 20% of the tooth height)
Annual Overhaul
- Metal flaw detection: Magnetic particle detection of key load-bearing parts
- Sealing system update: Replace all O-rings and oil seals
- Lubrication system modification: Upgrade to automatic oil filling device
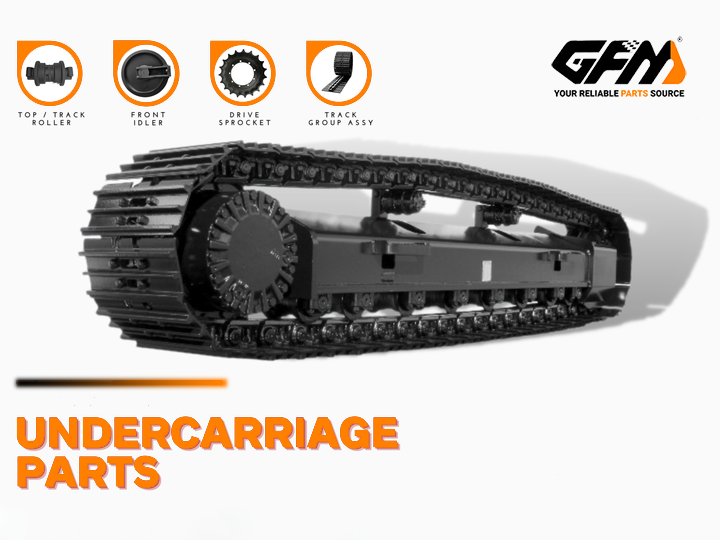
Reference for key component replacement cycle
▶ 50-hour basic maintenance
Guide wheel bearing grease injection amount: 20-30ml/time
Sprocket wheel grease injection frequency: replenish once every 3 hours of operation
Track chain link pin lubrication: spray penetrating anti-rust lubricant (WD-40 products are prohibited)
▶ 250-hour core component inspection
Chain track pitch measurement: use special caliper to detect (wear limit: standard pitch + 3%)
Drive tooth chamfer evaluation: tooth tip thickness < 60% of the original size needs to be replaced in groups
Support wheel axial clearance: feeler gauge detection (allowable value < 2mm)
▶ 500-hour system in-depth maintenance
Track assembly flip: Symmetrically swap the left and right tracks to extend service life
Guide wheel bushing inspection: Measure the inner diameter expansion after disassembly (limit value: original size + 0.8mm)
Tension spring preload test: Compression difference > 10% requires adjustment
▶ 1000-hour key component replacement
Chain track pin sleeve replacement standard: When the pin sleeve outer diameter wear > 8mm or rotation jam occurs
Buffer spring detection: Must be replaced if the free length is shortened by more than 10%
Full vehicle bolt re-tightening: Tighten in stages according to the torque value specified by the manufacturer
▶ 2000-hour overhaul maintenance
Road wheel assembly disassembly: Check the wheel tread wear groove (depth > 5mm requires replacement)
Track frame deformation detection: Use a laser alignment instrument to measure the parallelism error (> 3mm/m requires correction)
Travel motor seal pack replacement: Prevent hydraulic oil from contaminating the bearing
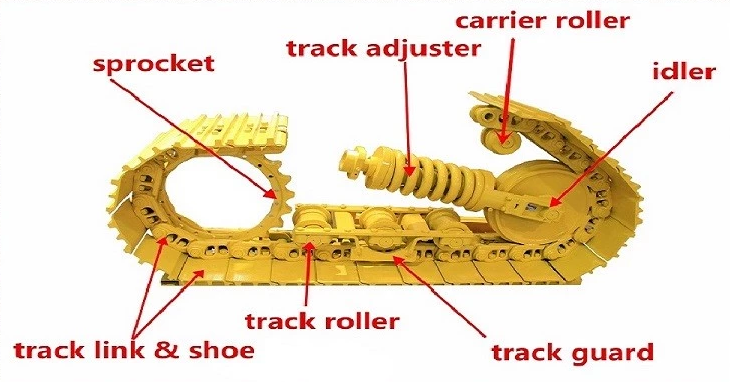
Maintenance quality verification standard
- Travel test: Straight line travel 50 meters deviation < 2 meters
- Load test: Parking on a 20° slope for 15 minutes without slipping
- Temperature rise test: Bearing temperature rise ≤35℃ after 2 hours of continuous operation
Tanya Jawab Umum
Q: How to adjust the maintenance frequency in rainy season?
A: Increase the seal inspection of the supporting roller to once a week and use GFM waterproof grease (code WP-220)
Q: Three major causes of abnormal track wear?
A: ① Improper tension (42%) ② Foreign matter on the ground (35%) ③ Centering deviation (23%)
Q: How to determine whether professional maintenance is needed?
A: When there is a deviation phenomenon that fails to be adjusted for 3 consecutive times, or the temperature difference of the supporting roller on one side is greater than 15℃
Dapatkan penawaran cepat dan gratis | Surel: henry@gfmparts.com | WhatsApp: +86 17705953659 |
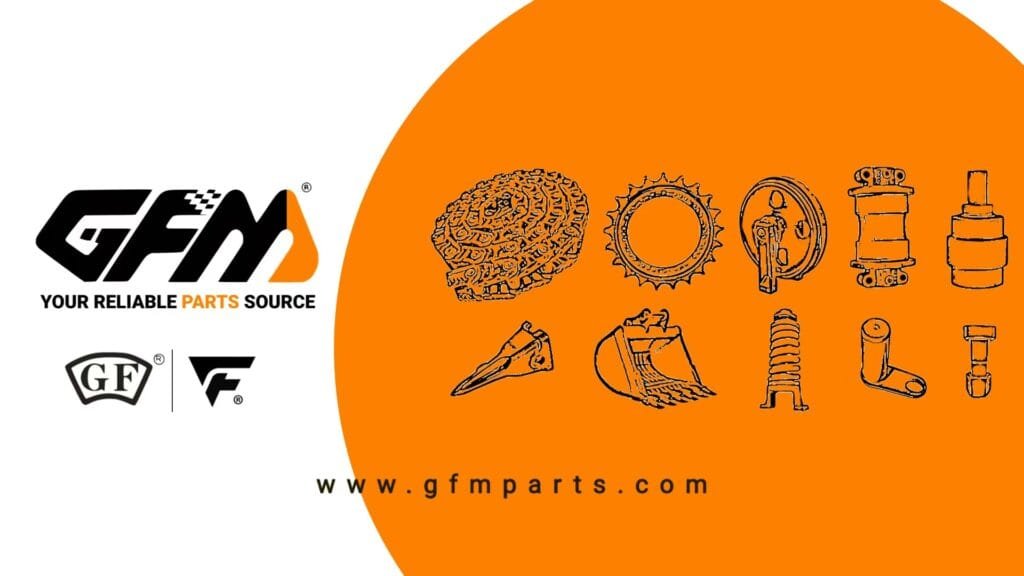