In the excavator transmission system, the sprocket is a key component that converts engine power into chain movement. Its stability and durability directly determine the equipment’s operating efficiency and safety.
Sprocket structure and manufacturing process
Material selection and heat treatment process
High-strength alloy steel and heat treatment technology
Sprockets are often made of high-strength alloy steel or special quenched and tempered steel. After quenching and tempering, the surface hardness and wear resistance can be significantly improved. The precise control of the heat treatment process (such as temperature, holding time and cooling rate) is directly related to the fatigue resistance and crack resistance of the tooth surface.
Surface strengthening technology
Carburizing, nitriding or laser heat treatment methods can be used to form a high-hardness strengthening layer on the tooth surface while maintaining the toughness of the matrix, thereby improving wear resistance and impact resistance.
Precision casting and machining
Precision casting technology
Through precision casting and forging technology, the compactness of the overall structure of the sprocket and the uniform distribution of internal stress are ensured, which helps to extend the service life.
CNC machining and tooth shape correction
Modern CNC machining technology (CNC) can achieve extremely high tooth shape accuracy, and with online measurement and automatic correction technology, it ensures that each tooth surface meets the design standards and reduces the risk of early wear caused by manufacturing errors.
Structural design and stress distribution optimization
Tooth shape design
Optimizing the tooth shape can not only improve the meshing efficiency, but also make the transmitted torque evenly distributed and reduce local stress concentration. Advanced CAD/CAM systems can simulate actual working conditions and perform finite element analysis (FEA) to provide accurate stress data for gear design.
Overall structural optimization
For the meshing state of the sprocket and the chain, the design takes into account parameters such as tooth pitch, tooth width, and tooth root fillet to ensure that the sprocket is not easily deformed under high load and impact load, while ensuring good power transmission and heat dissipation performance.
Impact of sprocket on excavator performance
Power transmission and mechanical energy conversion
Power transmission mechanism
The sprocket converts the torque output by the engine into the linear motion of the chain through precise meshing with the chain, realizing various working states such as equipment walking and rotation. The ideal transmission state requires that the meshing error between the sprocket and the chain is extremely low to ensure that the loss during energy transmission is minimized.
Energy conversion efficiency
The tooth profile accuracy and the lubrication state of the material surface directly affect the energy conversion efficiency. High-quality sprockets not only improve power output, but also maintain stable operation under low-speed and high-torque conditions.
Impact on excavator operating efficiency and safety
Improved operating efficiency
The design and maintenance of the sprocket directly determine the response speed and working stability of the whole machine. Precision manufacturing and good maintenance can keep the equipment responsive during startup, acceleration and load changes, thereby significantly improving engineering operation efficiency.
Safety Assurance
Problems such as sprocket wear, cracks or deformation can cause the chain to loosen, fall off or vibrate abnormally, which not only reduces work efficiency, but is also likely to cause equipment failure or safety accidents. Therefore, monitoring the sprocket status has become a key link in ensuring the safe operation of the excavator.
Synergistic influence on other components of the transmission system
Chain life
The meshing state of the sprocket and the chain determines the wear rate of the chain. High-precision sprockets can evenly distribute stress, reduce local wear of the chain, and thus extend the overall service life of the chain.
Vibration and noise control
Optimized tooth design and regular lubrication can significantly reduce the vibration and noise generated by the sprocket during operation, improve the operating environment, and reduce fatigue damage caused by resonance to other transmission components.
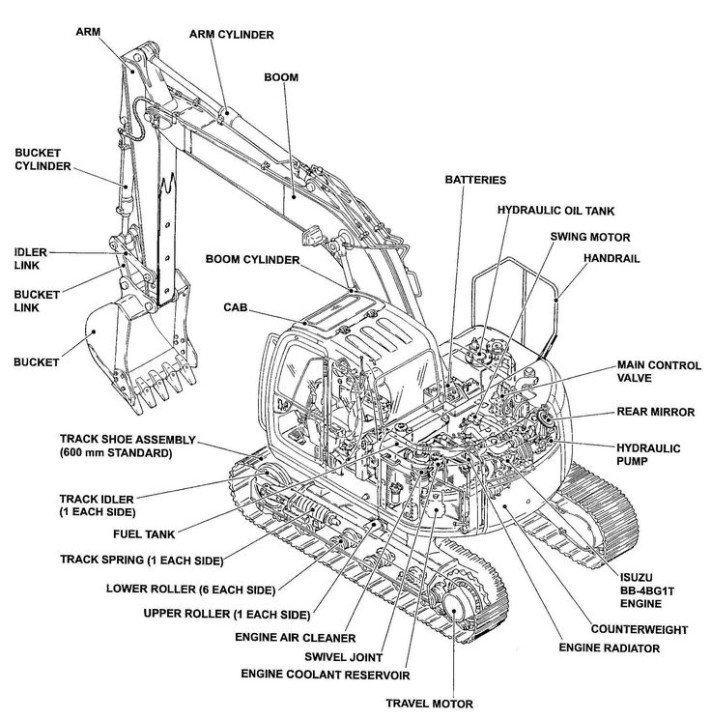
Advanced lubrication management and intelligent monitoring technology
Selection and optimization of lubrication system
Lubricant performance and selection
For different working conditions, it is recommended to use high-performance lubricants or greases that meet international standards. Lubricants must have good antioxidant, high temperature and corrosion resistance.
Diversification of lubrication methods
The use of automatic filling system, circulating lubrication system and local high-pressure lubrication technology can ensure that the sprocket and chain are always in the best lubrication state during continuous high-load operation, reducing wear and temperature rise.
Intelligent monitoring and online detection
Temperature and vibration sensors
Install temperature, vibration and noise sensors at key parts of the sprocket and transmission system to predict potential failure risks through real-time data collection and monitoring.
Non-contact measurement technology
Use laser scanning and infrared detection technology to regularly inspect the sprocket surface, analyze tooth surface wear, crack extension and micro defects, and provide data support for maintenance decisions.
Big data and early warning system
Combined with the data acquisition platform, establish a sprocket health file and early warning model to achieve predictive maintenance, early warning and formulate targeted maintenance plans, and reduce the risk of downtime caused by sudden failures.
In-depth analysis of fault diagnosis and repair process
Common faults and diagnostic methods
Wear failure
After long-term operation, the sprocket tooth surface will be locally flattened and unevenly worn. The degree of wear can be evaluated by quantitative detection using a surface roughness meter and a coordinate measuring machine (CMM).
Fatigue cracks and microcracks
During continuous high-load operation, fatigue cracks may occur in the sprocket. Non-destructive testing methods such as ultrasonic testing and magnetic particle testing can be used to detect microcracks in time and evaluate their expansion trend.
Thermal deformation and structural failure
Under high-temperature working conditions, the sprocket may be locally deformed due to thermal stress. The temperature distribution of the sprocket is monitored by an infrared thermal imager, and the possible thermal deformation areas are monitored in combination with finite element simulation.
Professional repair technology and process
Surface repair and reprocessing
For sprockets with slight wear or local cracks, grinding, polishing and laser repair technology can be used to restore the tooth surface profile. Tolerances must be strictly controlled during reprocessing to ensure the accuracy of the repaired sprocket.
Heat treatment remanufacturing technology
When the sprocket is severely worn or thermally fatigued, re-heat treatment, annealing and quenching processes can be used to partially restore the material properties, but this process must be carried out under strict process parameter control.
Modular replacement design
Some new sprocket designs adopt modular structures. When local damage is serious, only the damaged module is replaced instead of the entire wheel, which reduces maintenance costs and shortens downtime.
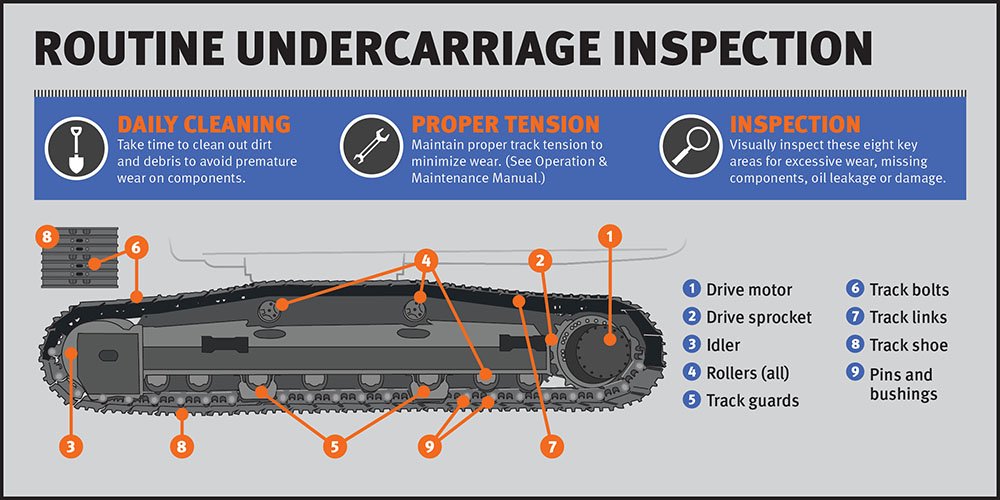
Excavator sprocket comprehensive maintenance and maintenance manual
Customized maintenance cycle and inspection plan
Ежедневный осмотр
The operator should visually inspect the sprocket and chain before starting the equipment, focusing on whether there is oil pollution, abnormal noise and abnormal wear.
Periodic maintenance plan
According to the use environment and operation intensity, formulate weekly, monthly or even quarterly maintenance plans, and regularly detect the tooth surface status, temperature and vibration in combination with sensor data.
Technical file management
Establish detailed sprocket use and maintenance files, record each overhaul, lubrication replacement and inspection data, and provide data support for subsequent preventive maintenance and technical improvements.
Lubrication and cleaning operation specifications
Lubrication plan formulation
According to the sprocket workload and temperature changes, select lubricants with appropriate viscosity and additive formulas. It is recommended to use an automated lubrication system to ensure uniform distribution of lubricants during long-term high-load operation.
Cleaning and decontamination steps
- After the equipment is shut down, thoroughly clean the sprocket and chain with industrial cleaning agents or special solvents;
- Use high-pressure airflow or ultrasonic cleaning equipment to remove deep oil and impurities;
- Dry in time after cleaning to avoid residual moisture;
- Apply new lubricants in accordance with regulations to ensure uniform coverage of each tooth surface.
Safe operation and training system
Operation safety guide
Develop strict safety operation procedures and emergency plans for the risks of high temperature, sharp edges and heavy object movement during sprocket maintenance.
Regular technical training
Periodic training for technicians and equipment operators, covering the latest detection technology, fault diagnosis methods and maintenance processes to ensure that every link meets safety and quality standards.
Impact of environment and working conditions on maintenance strategy
Special measures in harsh environments
In dusty, humid or chemically corrosive environments, it is recommended to add anti-corrosion coatings and sealing protection measures; at the same time, shorten the maintenance cycle, and frequently clean and inspect.
Dynamic adjustment of temperature and load
Adopt a real-time data monitoring system to dynamically adjust the lubricant replacement cycle and lubrication amount to ensure that the sprocket remains in the best operating state under extreme working conditions.
Cutting-edge technology and future development
Digital maintenance and Internet of Things (IoT) integration
Intelligent maintenance platform
Upload sprocket status monitoring data to the cloud platform, use big data analysis and artificial intelligence algorithms to achieve fault prediction and maintenance decisions, and improve the intelligent level of maintenance.
Remote diagnosis and real-time feedback
Through the remote monitoring system, technical experts can obtain key data in real time during equipment operation, adjust maintenance plans in time, and reduce errors and delays caused by manual inspection.
New materials and coating technologies
Superhard ceramic coating
Research on the application of ceramic coatings to sprocket tooth surfaces to improve wear resistance and corrosion resistance while reducing lubricant consumption.
Composite materials and self-healing materials
Explore the combination of composite materials and self-healing coating technology to automatically repair the sprocket when it is slightly damaged, extend the service life of parts and reduce the frequency of maintenance.
Получите быструю бесплатную расценку | Электронная почта: henry@gfmparts.com | Вотсап: +86 17705953659 |
As the core component of the excavator transmission system, the design, manufacturing, inspection, maintenance and repair of the sprocket involve many advanced technologies and scientific principles. By selecting high-strength materials, precision manufacturing, reasonable tooth design and intelligent monitoring methods, it can not only significantly improve the power transmission efficiency, but also reduce energy consumption, reduce vibration and ensure the long-term safe operation of the equipment. Combined with periodic preventive maintenance and cutting-edge fault diagnosis technology, enterprises can not only reduce maintenance costs, but also improve overall engineering benefits by optimizing production efficiency.
Как GFM производитель деталей для экскаваторов, we are committed to providing world-leading technical support and high-quality products. Through systematic technical analysis and comprehensive maintenance manuals, we hope to provide customers with scientific and rigorous sprocket maintenance solutions to ensure that every excavator can still maintain efficient, stable and safe operation under extreme conditions, and achieve dual guarantees of economic benefits and equipment reliability.
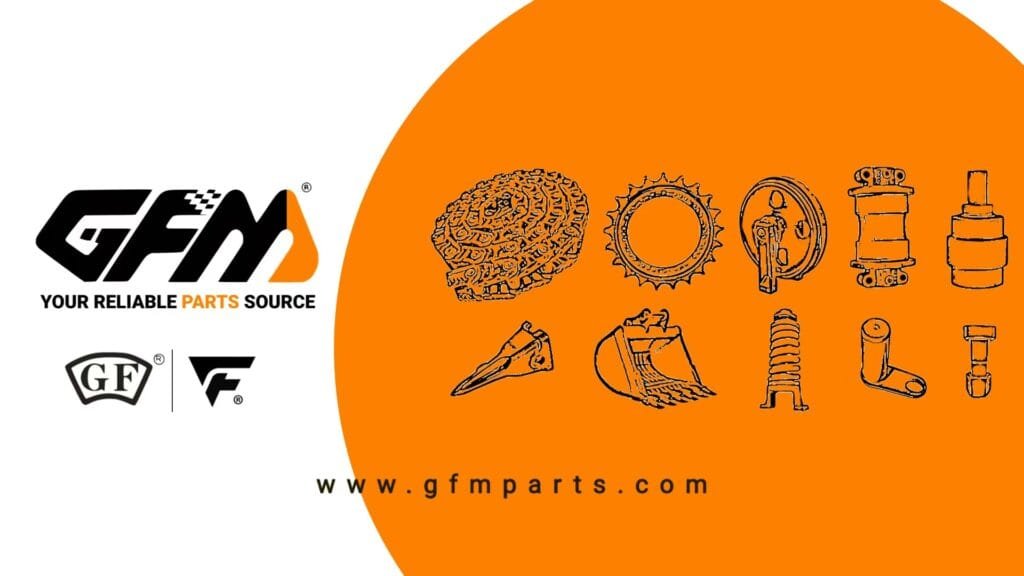