In the field of construction machinery, the efficient operation of excavators is directly related to project progress, cost control and environmental impact. As a GFM производитель деталей ходовой части экскаватора, we are not only committed to providing high-quality accessories, but also based on data and professional technology, we guide users to maximize efficiency through multi-dimensional measures such as optimized design, maintenance management and intelligent monitoring.
Technology upgrade and high-performance accessories application
Improvement of accessories materials and manufacturing processes
Application of high-strength materials
- Data case: By using high-strength alloy materials and advanced heat treatment processes, after laboratory and field tests, the wear resistance of GFM excavator main arm and dipper rod accessories can be improved by 20%-25%, while extending the service life of key components by 30%.
- Технические преимущества: The balanced design of material hardness and toughness reduces fatigue damage while ensuring impact resistance, effectively reducing downtime caused by accessory replacement.
Precision manufacturing and assembly process
- Precision requirements: CNC processing technology is used to control the size tolerance of parts within the range of ±0.02mm to ensure efficient transmission between connected parts and reduce energy loss.
- Case data: Field application data shows that after the accuracy of accessories is improved, the working efficiency of the whole machine is improved by 5%-8%, and the failure rate caused by assembly errors is reduced.
Hydraulic system and intelligent control technology
Hydraulic system optimization
- System improvement: By fine-tuning the hydraulic pump, valve and oil system, the matching of hydraulic flow and pressure is optimized. After actual measurement, under the same working conditions, the fuel consumption of the new hydraulic system is reduced by about 12%-15%, and the output power stability is improved by 10%.
- Test data: In the 1000-hour continuous operation test, the temperature rise of the improved hydraulic system is reduced by 8°C, and the equipment failure interval (MTBF) is extended by 15%.
Intelligent control and adaptive parameter adjustment
- Intelligent control: Using an embedded control system to collect data on the operating status (such as load, operating depth, and working environment temperature) in real time, and automatically adjust the hydraulic output and engine speed through AI algorithms to ensure that the equipment always operates under the best working conditions.
- Data feedback: Laboratory simulation data shows that the intelligent control system can improve excavation efficiency by about 10%, and in fuel-saving mode, fuel consumption can be reduced by about 8%-10%.
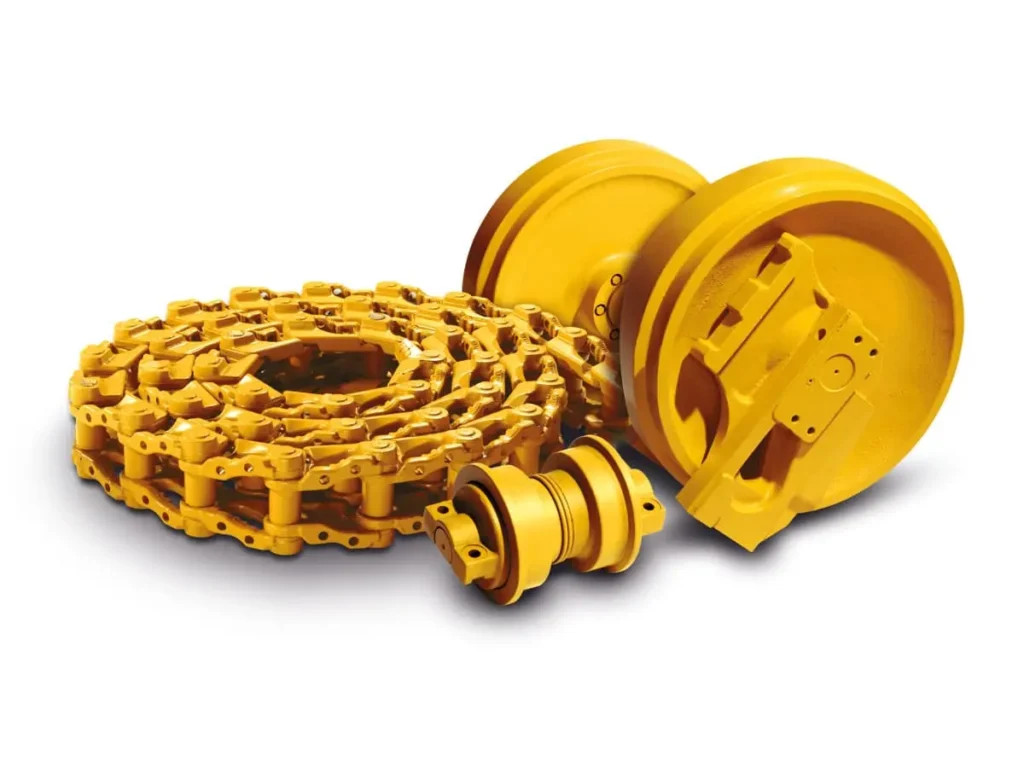
Maintenance management and preventive maintenance strategy
Regular inspection and data monitoring
Comprehensive inspection plan
- Inspection cycle: It is recommended to conduct a comprehensive inspection every 250 working hours and perform in-depth maintenance every quarter. Including hydraulic oil quality inspection, lubrication system oil renewal, component wear inspection, etc.
- Data monitoring: Through the online monitoring system, key indicators such as vibration, temperature, and pressure are collected, and historical data analysis is used to predict faults. Actual cases show that the fault warning system can reduce the probability of sudden downtime by about 20%.
Preventive maintenance effect
- Statistical data: After regular inspection and preventive maintenance, the overall equipment failure rate has dropped from an average of 8% to 5% per year. At the same time, due to early prevention, the maintenance cost has been reduced by about 15%-20%.
Fault prediction and big data analysis
Sensor network and big data platform
- System construction: IoT technology is used to install temperature, pressure, and vibration sensors on key components, and real-time data is transmitted to the big data platform for analysis and prediction.
- Data case: In a large engineering project, 5 potential failures were predicted in advance through data analysis, successfully avoiding about 120 hours of unplanned downtime and saving more than 500,000 yuan in economic losses.
Operator training and operation process optimization
Efficient operation and energy-saving operation
Optimize operation path planning
- Scientific planning: Reasonably plan the excavator operation route according to the terrain and operation requirements. Experimental data show that optimizing the operation path can reduce the no-load operation time by 15%-20% and improve the overall operation efficiency.
- Energy-saving mode: Enable automatic energy-saving mode under low load or no-load conditions, and record fuel consumption reduction of up to 10% in some projects.
Improvement of operating skills
- Professional training: Through regular theoretical and practical training, operators can improve their mastery of various machine systems. After training, the operating efficiency of qualified operators increased by about 12%, and the equipment wear and failure rate caused by operating errors can be effectively reduced.
Operating specifications and safety management
Safe operation specifications
- Standard process: Develop detailed operating specifications and emergency plans to ensure that operators can work efficiently while taking safety into account. Statistics show that following safe operating procedures can reduce the accident rate by about 30%.
- Continuous improvement: Combined with on-site feedback and data monitoring, the operating guide is revised regularly to form a virtuous circle and continuously promote the improvement of operating efficiency and safety management.
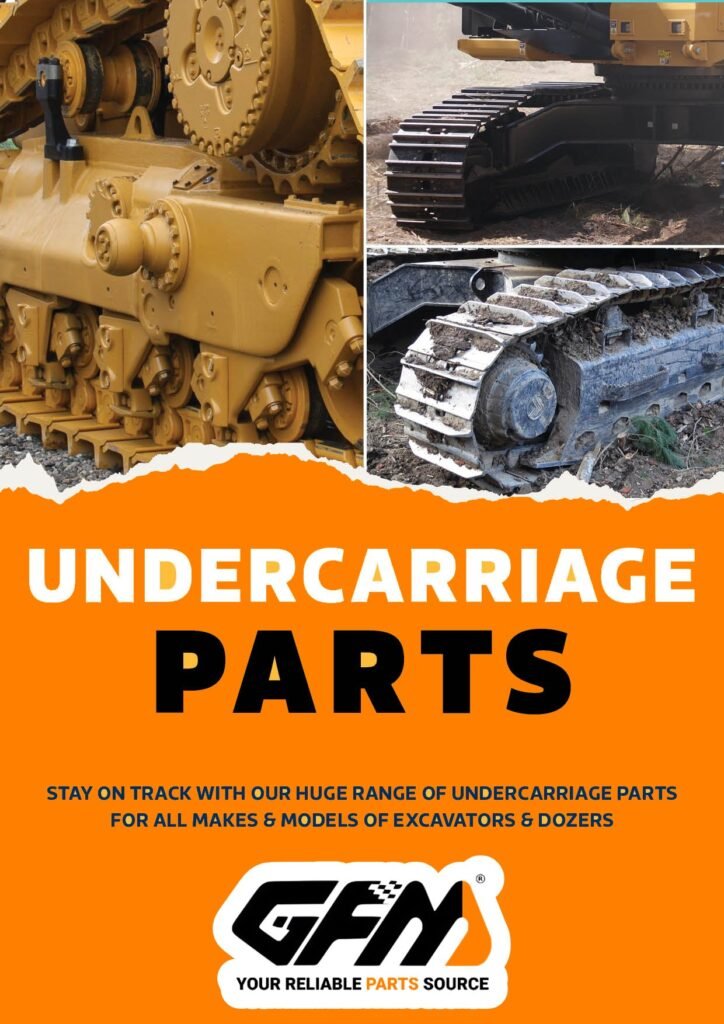
Intelligent monitoring system and remote control upgrade
Real-time remote monitoring platform
Intelligent monitoring system deployment
- System function: Using GPS, sensors and wireless communication technology, a remote monitoring platform is established to realize real-time monitoring of equipment location, working status, fuel consumption, vibration and other parameters. On-site data shows that after adopting the remote monitoring system, the equipment response speed is increased by nearly 20%, and the emergency fault handling time is shortened by 50%.
- Data integration: Connect with project management system and supply chain management system to achieve data sharing and rapid feedback, and improve overall collaborative efficiency.
Automatic scheduling system
- Case data: Through the automatic scheduling system, the equipment is deployed and the task is optimized in real time. In the collaborative operation of multiple excavators, the overall production efficiency is improved by about 15%-18%, and the waiting and scheduling time is reduced.
Overall system integration and data-driven decision-making
Full-chain data management
- Platform construction: Integrate equipment monitoring, maintenance records and operation data, and use data analysis to support decision-making. Statistics show that data-driven decision-making can increase equipment utilization by 8%-12% while reducing overall operational risks.
- System integration advantages: By connecting with the enterprise ERP and MES systems, the equipment status is seamlessly connected with the supply chain and project progress, ensuring that each link can respond and adjust quickly.
Environmental adaptability and sustainable development strategy
Equipment optimization for various working conditions
Environmental adaptability design
- Temperature and humidity control: Develop special protection kits and cooling and heat dissipation systems for high temperature, low temperature and humid environments. Experimental data show that after adaptive transformation, the operating stability of the equipment under extreme temperatures is improved by 25%, and the loss of key components is reduced by 18%.
- Vibration and dust protection: Use sealing technology and intelligent filtering systems to reduce failures caused by dust and vibration and extend the service life of the equipment.
Green manufacturing and circular economy
Green manufacturing concept
- Low-carbon technology: Actively adopt low-carbon environmentally friendly materials and energy-saving processes, and some products have achieved a 15% reduction in CO₂ emissions.
- Recycling: Promote the remanufacturing of accessories and the recycling of waste parts. In some cases, the utilization rate of raw materials has increased to 90%, realizing resource recycling.
Sustainable development data
- Long-term benefits: Sustainable manufacturing strategies not only reduce production costs, but also enhance the competitiveness of enterprises in the green market. Statistics show that after implementing green manufacturing solutions, the annual cost of enterprises is reduced by about 10%-12%, while improving customer satisfaction and brand recognition.
Получите быструю бесплатную расценку | Электронная почта: henry@gfmparts.com | Вотсап: +86 17705953659 |
Improving the efficiency of excavators is a systematic project involving design, technology, maintenance, operation and management. By introducing high-performance accessories, optimizing hydraulic and intelligent control systems, implementing regular inspections and big data monitoring, strengthening operator training, and deploying remote intelligent monitoring platforms, excavators can not only achieve a 10%-20% improvement in work efficiency, but also significantly reduce energy consumption and failure rates. At the same time, protection improvements and green manufacturing strategies for different operating environments also provide a solid guarantee for the long-term stable operation of equipment.
Как GFM производитель деталей для экскаваторов, we always rely on data to continuously promote technological innovation and system integration, help customers achieve efficient equipment operation, reduce operating costs, and seize opportunities in fierce market competition. In the future, we will continue to rely on professional technology and innovative thinking to provide more competitive solutions for the global construction machinery industry.
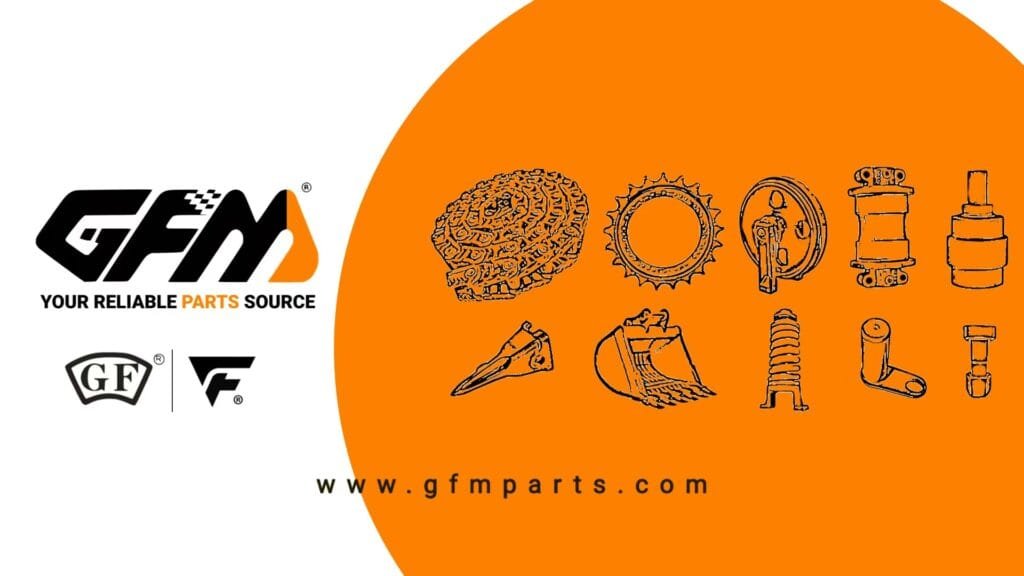