Как производитель деталей для экскаваторов, we know that in heavy-duty operating environments, the efficient operation of equipment depends on the normal operation of every key component.
Оглавление
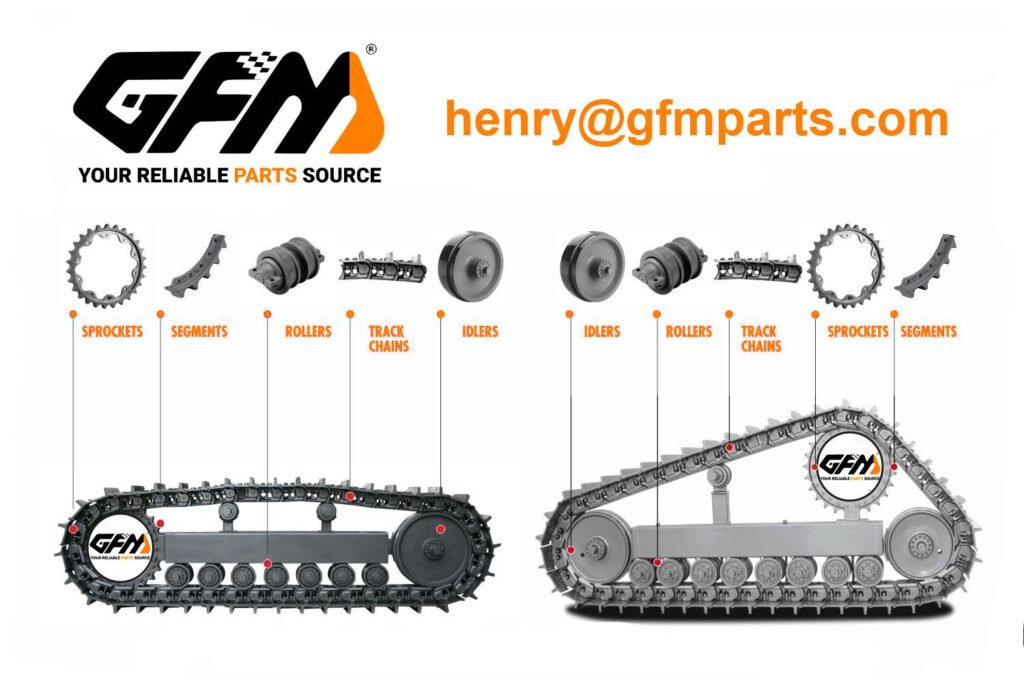
Key Points
In excavator maintenance, there are several core principles that cannot be ignored:
- Overall maintenance strategy: The various systems of the excavator – engine, hydraulic system, chassis, accessories, electrical system and cab – constitute the nerve center of the equipment operation. According to market research data, 80% of excavator failures can be attributed to the imbalance of the hydraulic system and engine system. Therefore, developing a maintenance plan covering the entire system is the key to extending the life of the equipment.
- Preventive maintenance: Regular inspections and preventive maintenance can reduce the failure rate. According to statistics, preventive maintenance can reduce equipment downtime by 30% and reduce maintenance costs by about 20%.
- Replace parts in time: During the operation of the equipment, by monitoring equipment indicators (such as oil pressure, hydraulic oil temperature and vibration data), early signs of component degradation can be captured in time to prevent small problems from turning into major failures.
- Standardized process: Develop and implement standardized parts procurement and replacement processes to ensure that each operation meets the equipment’s technical parameters and safety standards, thereby improving overall operating efficiency and safety.
Excavator parts list and their functions
For the key systems of the excavator, the components of each subsystem carry important functions. The following is a detailed analysis of each major system:
Engine system
- Main function: The engine, as the “heart” of the excavator, is responsible for converting fuel into mechanical energy and providing stable power for the entire equipment. Modern excavator engines usually have an output power of between 100 and 400 horsepower and must meet ISO or EPA emission standards.
- Core parts: Piston, cylinder, crankshaft, valve system and fuel supply system. High-precision machining and heat treatment technology can improve engine efficiency by 5%-10%. Regular monitoring of oil pressure (generally maintained at 3-4 bar) and temperature (maintained at 80-90°C) is the key to ensuring its efficient operation.
Hydraulic system
- Main function: The hydraulic system determines the precise operation of the excavator arm, bucket and other accessories. The hydraulic system pressure of high-end equipment can usually reach 300 to 350 bar.
- Core parts: hydraulic pump, hydraulic cylinder, oil tank, valve and filter. The quality of hydraulic oil directly affects the efficiency of the system. Industry data shows that high-efficiency hydraulic oil can reduce energy consumption by about 5%. Regular replacement of hydraulic oil (usually every 2000-3000 working hours) and filters can prevent system contamination and ensure response speed and control accuracy.
Chassis components
- Main function: The chassis system supports and transmits the load of the whole machine to ensure the stability of the equipment in complex terrain. The chassis design of modern excavators focuses on wear resistance and shock absorption performance, and the track wear rate usually needs to be tested every 1000 working hours.
- Core parts: walking device, track, shock absorption system and suspension system. Data show that the tension of the track has a direct impact on the stability of the equipment, and proper adjustment can reduce the chassis failure rate by about 15%.
Accessories
- Main function: Accessories determine the application range of the excavator under different working conditions, such as crushing, drilling, loading, etc. Depending on the intensity of work and the environment, the wear rate of accessories may be accelerated by 20%-30%.
- Core parts: Arm, bucket, breaker and grab. Material strength and wear resistance need to be considered during design. The use of high-strength alloy materials can extend the service life of accessories by more than 20%.
Electrical system
- Main functions: The electrical system integrates control, monitoring and feedback functions, and monitors the status of equipment in real time through high-precision sensors and control modules. Data shows that precision instrument calibration can increase the overall system response speed by 5%-8%.
- Core parts: Electric control box, sensor, instrument panel and line system. Regularly checking the aging of the electric control box and lines to ensure accurate data collection is the key to ensuring the stable operation of the system.
Cab
- Main functions: The cab not only provides a safe and comfortable working environment for the operator, but also undertakes the task of real-time monitoring and control of equipment. According to ergonomic design, a comfortable cab can reduce operator fatigue by 15%-20%.
- Core parts: Seats, instruments, air conditioning system and seat belts. High-standard cab configuration can significantly improve operating efficiency and safety, especially in high or low temperature environments, the stable operation of the air conditioning system is particularly important.
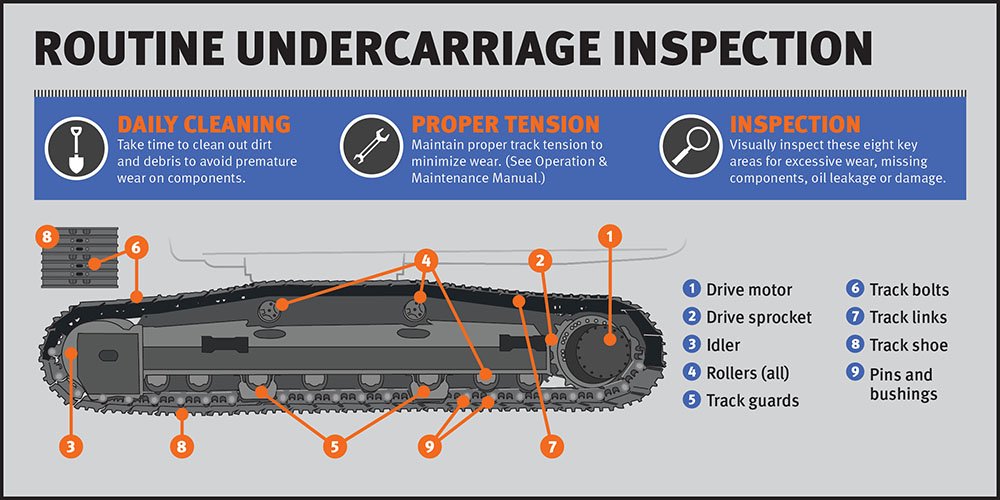
Maintenance tips for excavator parts
Engine system maintenance
Regular maintenance is the key to ensure long-term operation of the engine:
- Oil change: It is recommended to change the oil every 250-500 hours of operation, and use high-quality oil that meets API or ACEA standards.
- Cooling system: Check the radiator and fan every month to keep the coolant ratio at the recommended value (generally 50/50 mixture).
- Fuel system: Clean the fuel nozzle and filter regularly to ensure that the combustion efficiency remains above 95%.
Hydraulic system maintenance
Ensure efficient response and precise control of the hydraulic system:
- Hydraulic oil maintenance: Replace the hydraulic oil every 2000-3000 hours. The quality of the oil directly affects the efficiency of the system.
- Filter cleaning: According to the working environment, check and clean or replace the filter every 1000 hours to prevent clogging by impurities.
- Seal inspection: Check the hydraulic pump and valve seals regularly to prevent leakage and pressure drop.
Chassis maintenance
Chassis stability is the basis of machine safety:
- Проверка пути: Check the wear of the track every 500 hours, adjust the tension or replace the seriously worn parts if necessary.
- Lubrication maintenance: Lubricate the walking parts before and after daily operation to reduce friction and heat damage.
- Shock absorption system: Regularly check whether the shock absorption system has oil leakage or performance degradation to ensure that the suspension performance is always in the best condition.
Accessory maintenance
Accessories directly affect work efficiency and operation accuracy:
- Connection inspection: Check whether the connection between the bucket arm and the bucket is firm before and after each operation, and tighten it in time if it is loose.
- Wear monitoring: According to the intensity of the operation, the accessory wear inspection is carried out every 500 hours to ensure that the parts are free of cracks or fatigue.
Electrical system maintenance
As the “nerve center” of the equipment, the electrical system requires high reliability:
- Line detection: Regularly check the electric control box and line system to prevent short circuits caused by aging or moisture.
- Калибровка датчика: Calibrate sensors and instruments every 1000 hours to ensure accurate data.
- Spare parts reserve: It is recommended to establish a spare parts library for key electrical parts to cope with emergencies.
Cab maintenance
The good condition of the cab is related to operator safety and operating efficiency:
- Environmental cleaning: Clean the inside and outside of the cab regularly to keep the line of sight clear and avoid instrument reflection affecting operation.
- Safety equipment inspection: Check the seat belts, seats and dashboard regularly to ensure that the safety equipment is not aging or faulty.
- Air conditioning system: In extreme climates, the maintenance of the air conditioning system is particularly important. Check it once a quarter to ensure the efficient operation of the system.
Signs that excavator parts need to be replaced
By regularly testing the equipment operation data, you can effectively identify the early warning signs of the imminent failure of parts:
Engine system
- Common signs: Abnormal noise, increased vibration, and decreased power output.
- Data reference: Oil contamination or a 5%-10% drop in pressure may indicate that the internal parts are severely worn, and core components such as piston rings and crankshafts need to be replaced in time.
Hydraulic system
- Common signs: Delayed operation response, hydraulic oil leakage, and reduced hydraulic pump efficiency.
- Data reference: When the hydraulic system working pressure drops by more than 10%, or the hydraulic oil temperature rises abnormally (exceeding the recommended value by more than 10°C), the hydraulic cylinder, pump and valve seals need to be checked.
Chassis components
- Common signs: Severe track wear, cracks or breaks, unstable walking.
- Data reference: The test data shows that the track wear rate exceeds 30%, or the shock absorption system response drops by more than 15%, and the relevant parts should be replaced or repaired in time.
Accessories
- Common signs: The bucket or breaker has obvious cracks and the wear rate exceeds 20% of the design life.
- Data reference: If the attachment connection is loose or abnormal vibration occurs, it may affect the overall operating efficiency and needs to be repaired or replaced in time.
Electrical system
- Common signs: Abnormal instrument data, frequent alarms, and sensor failure.
- Data reference: When the temperature or voltage fluctuation in the electric control box exceeds the standard range of ±10%, it is recommended to detect the circuit board and sensor to prevent large-scale failures.
Cab
- Common signs: Slow response of instruments and consoles, aging of safety equipment.
- Data reference: If the service life of components such as seats and dashboards is significantly lower than expected (usually after 5-7 years), you should consider updating related equipment to ensure safe operation.
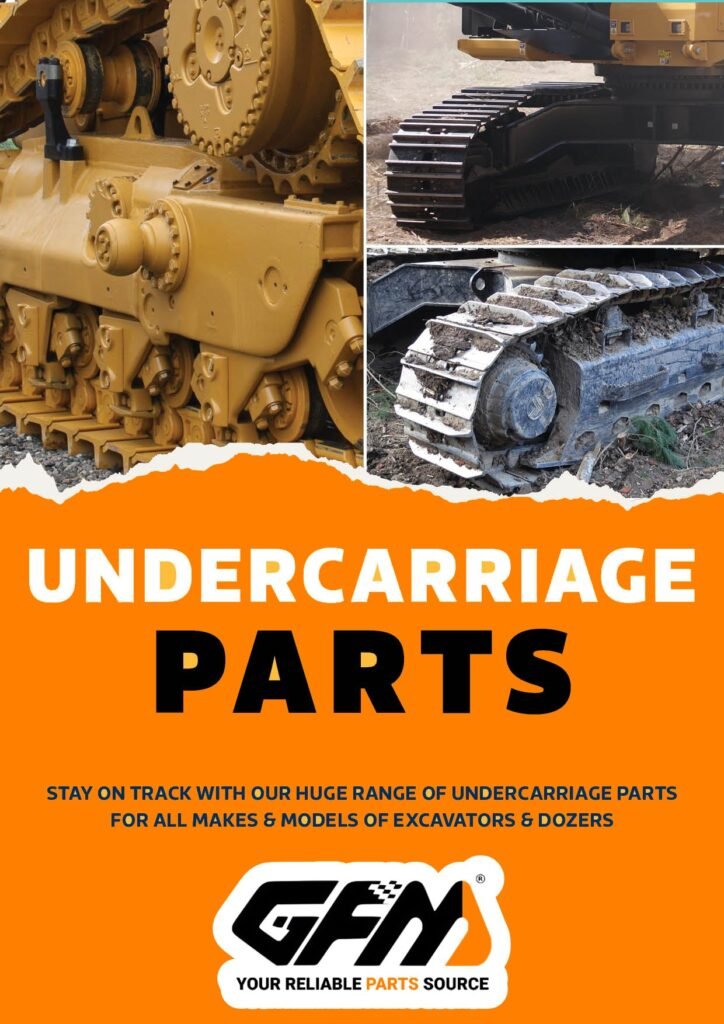
How to purchase and replace excavator parts
Purchase and replacement play a vital role in equipment maintenance. Its standardized process and rigorous operating procedures can ensure the long-term stable operation of the equipment.
Purchase parts
- Channel selection: It is recommended to choose the original manufacturer or certified dealers first to ensure that the quality of parts meets ISO, CE or domestic certification standards. Data shows that the use of original parts can reduce the failure rate caused by parts mismatch by about 20%.
- Price and service: While comparing prices through multiple channels, it is necessary to pay attention to warranty policies and after-sales services. It is recommended to check the historical performance data and user feedback of parts before purchasing to ensure the high reliability and durability of parts.
Replacement of parts
- Professional operation: Parts replacement should be carried out by trained professional technicians to ensure safe operation and system compatibility. Standardized operating procedures (such as detailed operating manuals and video tutorials) can reduce the operating error rate to less than 5%.
- Record management: It is recommended to use an electronic file system to record each replacement and maintenance data in detail to provide data support for future fault prediction and prevention.
Ensure compatibility
- Technical matching: Be sure to check the part model, production batch and equipment parameters before purchasing. It is recommended to refer to the equipment maintenance manual and the parts list recommended by the manufacturer to ensure that the replacement parts are consistent with the original configuration.
- Certification standards: Parts procurement should meet relevant certification standards to ensure the stable operation of the equipment under high-load conditions, and at the same time, the data report of a third-party testing agency is used as evidence.
Troubleshooting common problems of excavator parts
It is crucial to develop a scientific troubleshooting process for common faults in different systems:
Hydraulic system problems
- Common problems: Hydraulic oil contamination, oil circuit blockage, and seal aging.
- Troubleshooting strategy: According to data analysis, when the impurity concentration in the hydraulic oil exceeds 5%, the oil needs to be replaced; regular cleaning of the hydraulic system and testing of the oil circuit pressure (maintained within the standard range of 300-350 bar) can effectively prevent faults.
Electrical system problems
- Common problems: Line aging, short circuit, sensor calibration misalignment.
- Troubleshooting strategy: Use professional testing instruments to regularly test the electric control box to ensure that the voltage and temperature fluctuations are within a reasonable range of ±10%, and periodically calibrate and test key sensors.
Chassis problems
- Common problems: Loose tracks, shock absorption system failure, insufficient lubrication.
- Troubleshooting strategy: Regularly tighten the chassis connection parts, monitor the track tension and wear, and adjust or replace the wear parts in time when the data is abnormal.
Engine problems
- Common problems: Oil contamination, cooling system blockage, and poor fuel supply.
- Troubleshooting strategy: Regularly monitor the oil pressure and temperature, ensure that the coolant ratio is within the recommended range, and clean the fuel nozzle to ensure that the combustion efficiency is maintained above 95%.
Часто задаваемые вопросы
Q1: What is the most important part of the excavator for regular maintenance?
A1: The engine system and hydraulic system are the core of the excavator. Data shows that the failure rate of these two parts accounts for nearly 80% of the total failures. Regular maintenance of these two parts can effectively prevent most failures and ensure the long-term operation of the equipment.
Q2: How often should the air filter of the excavator be replaced?
A2: It is recommended to check it every 500 to 1000 hours or every quarter depending on the working environment and the intensity of use. Data shows that in dusty environments, the replacement frequency should be higher to prevent the engine efficiency from decreasing due to poor air filtration.
Q3: Can aftermarket parts be used to repair the excavator?
A3: Yes, but you must choose high-quality aftermarket parts that have been certified and tested. Statistics show that the use of certified aftermarket parts can reduce the equipment failure rate by about 15% while ensuring the stability of the equipment under high load conditions.
Q4: How to identify the correct replacement parts for the excavator?
A4: It is recommended to check the part model, parameters and production batch, and refer to the equipment maintenance manual and manufacturer’s recommendations. Using professional testing tools to compare new and old parts can effectively avoid system failures caused by mismatched parts.
Q5: What tools are necessary for replacing excavator parts?
A5: Common tools include wrenches, screwdrivers, hydraulic lifting equipment, lubrication tools and testing instruments. The specific tools depend on the replacement project, and a set of standard toolboxes can reduce the operating error rate to less than 5%.
Получите быструю бесплатную расценку | Электронная почта: henry@gfmparts.com | Вотсап: +86 17705953659 |
Whether it is regular preventive maintenance or sudden fault handling, scientific and systematic operating procedures can significantly improve equipment operating efficiency and extend service life. For GFM and its customers, building a complete equipment maintenance system is the fundamental guarantee for engineering efficiency and safety. Continuously paying attention to equipment status, timely updating maintenance data and using high-quality parts are the only way to ensure that excavators always maintain optimal performance in the highly competitive market.
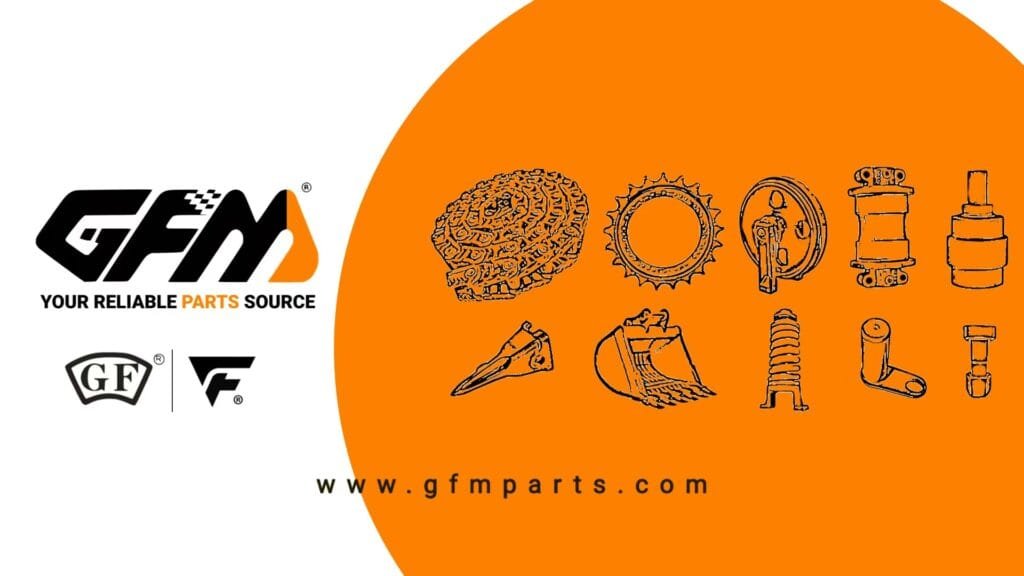