Due to its compact size, flexibility and economic efficiency, mini excavators have become an indispensable and important equipment in municipal engineering, landscaping, residential construction and other scenarios.
Detailed analysis of mini excavator parts
Engine system
- Power source and combustion technology
- The engine adopts high-efficiency internal combustion engine technology and achieves high power output and low emissions through advanced fuel injection and combustion management systems. Before operation, the engine oil, air filter and coolant should be checked to ensure that the engine is in the best working state.
- Startup and temperature control
- In low temperature environments, it is recommended to preheat the engine and use a special starting device; after the engine is running, the temperature instrument needs to be monitored to prevent overheating due to long-term overload.
Hydraulic system
- Hydraulic pump and hydraulic cylinder
- The hydraulic pump converts the mechanical energy output by the engine into high-pressure hydraulic energy, and the hydraulic cylinder drives the bucket, dipper rod and other working parts. Regularly check the hydraulic oil quality, oil level and oil temperature, and visually inspect the pipelines and seals to prevent oil leakage.
- Control valve and electronic regulation
- Modern equipment is equipped with an electronically controlled hydraulic system, and the operator uses the hydraulic control lever to achieve precise positioning. Be sure to regularly check the control valve response speed and hydraulic pressure to ensure system stability.
Travel system and steering mechanism
- Excavator tracks shoe and drive wheels
- The design of the track system directly affects the traction and stability of the equipment in uneven terrain. In daily operation, pay attention to checking the tension and wear of the track and the wear of the drive wheel to prevent slipping or loss of control due to looseness or damage.
- Suspension and steering control
- An efficient steering system requires not only mechanical transmission accuracy, but also hydraulic assistance to ensure smooth control. Check the steering fluid status and the wear of related transmission components before and after operation.
Operator’s room and human-machine interface
- Control panel and instrument display
- The humanized operator’s room is equipped with a multi-function display, control lever and emergency stop button. The operator should be familiar with each function key, instrument warning light and fault prompt to ensure rapid response in emergency situations.
- Safety seat and field of view design
- Safety seat, adjustable field of view and shockproof design can effectively reduce the risk of fatigue caused by long-term operation and improve operation accuracy and safety.
Operation accessories
- Arm and bucket
- The arm structure determines the excavation radius and operating depth, and the bucket shape and edge design affect the excavation efficiency. After each operation cycle, it is recommended to check and replace the arm welding parts, bucket connection points and wear parts as necessary.
- Auxiliary devices
- Such as hammers, crushers, etc., are designed for specific working conditions. Please confirm whether the device is firmly installed before use, and perform special maintenance according to the manufacturer’s recommendations.
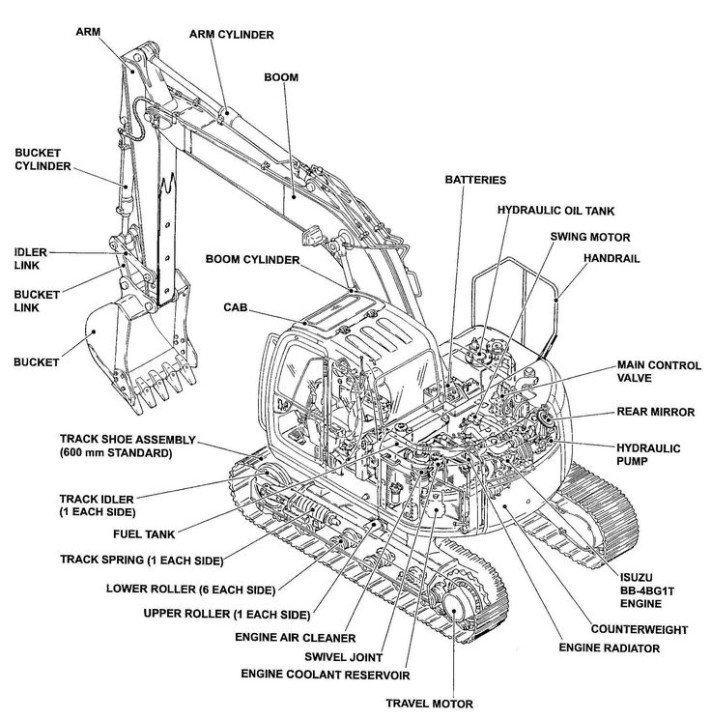
Working principle and energy conversion process
Power transmission process
- Fuel combustion and mechanical energy generation
- After the fuel in the internal combustion engine is fully burned, the mechanical energy generated is transmitted to the hydraulic pump through the crankshaft.
- Hydraulic energy conversion
- The hydraulic pump converts mechanical energy into high-pressure hydraulic energy, and the oil passes through a high-precision control valve to drive the hydraulic cylinder and other actuators to complete the action.
- Multi-task collaborative work
- At the same time, part of the mechanical energy is transmitted to the walking mechanism through the gear or chain drive system to achieve smooth movement and steering operation of the equipment.
Digital monitoring and feedback
- Sensor and fault self-detection
- The built-in multi-point sensor monitors the oil temperature, pressure, vibration and liquid level changes in real time; the data is fed back to the display screen through the control module to ensure that the equipment operates within the safety parameters.
- Automatic fault alarm system
- When the system detects an abnormality, it will automatically trigger the alarm program to remind the operator to check the key components immediately to avoid accidents.
Comparison between mini excavators and medium and large models
- Operation scenarios and adaptability
- Mini machines are compact and suitable for operations in mini spaces and complex terrains; medium and large models focus on large-scale earthwork projects and high-load operating environments.
- Power and operating radius
- Medium and large models have greater power and digging radius, while mini excavators have more advantages in precise operation and low-noise environments.
- Economy and maintenance cost
- Mini excavators have low fuel consumption, transportation and maintenance costs, and are suitable for mini and medium-sized projects; although medium and large models are more powerful, their operating costs are relatively high.
Operation method and practical guide
Pre-operation inspection process
- Environment and safety area confirmation
- Ensure that there are no obstacles and pedestrians in the operating area, and conduct a preliminary assessment of the surrounding environment.
- Check the flatness and slope of the ground to ensure that the equipment operates smoothly.
- Equipment external inspection
- Check whether the hydraulic oil, engine oil, and coolant levels meet the standards.
- Check whether the crawler and steering mechanisms are intact and properly tensioned.
- Check whether all operating accessories are firmly installed without looseness or abnormal wear.
- Instrument and warning system self-test
- Before starting, observe whether the indicator lights on the dashboard (oil pressure, temperature, power, etc.) are normal.
- Confirm that the emergency stop button and alarm device are working properly.
Startup and low-speed test run
- Startup steps
- Sit tight and fasten your seat belt;
- Perform a “warm-up” operation before pressing the start button (especially in cold environments) to gradually increase the engine temperature;
- After starting, observe the engine and hydraulic system pressure gauges to ensure that the indicators are within the normal range.
- Low-speed test run
- Test the hydraulic system response by slightly moving the joystick before operation;
- Try to move forward, backward and turn on the spot at low speed to ensure that the equipment responds sensitively to the operation instructions;
- Check whether the operation attachment moves smoothly and adjust the control lever sensitivity (if necessary).
Normal operation skills
- Precise control of the operating lever
- Use the left and right hands to coordinate the operation, the left hand controls the walking, and the right hand is responsible for the operation arm and bucket movement.
- When adjusting the operation depth and angle, keep the movement stable and avoid sudden acceleration and severe vibration.
- Reasonable distribution of work load
- Adjust the excavation force according to different soil types and operation requirements, avoid long-term high-load operation, and reduce the risk of overheating of the hydraulic system and engine.
- When performing continuous operations, reduce the operation speed in time to prevent the equipment from overloading for a long time.
Shutdown and follow-up inspection
- Normal shutdown steps
- After completing the operation, reset the bucket and working arm to a safe position.
- Press the stop button to turn off the engine and hydraulic system in turn.
- After shutting down, check whether the instrument panel has returned to zero, and pay attention to whether there are any residual fault alarms.
- Cleaning and recording
- Clean the mud and impurities on the surface of the equipment and key parts, especially the hydraulic oil circuit and track clearance.
- Record the working hours, abnormal operations and maintenance conditions of the day to provide a basis for future maintenance.
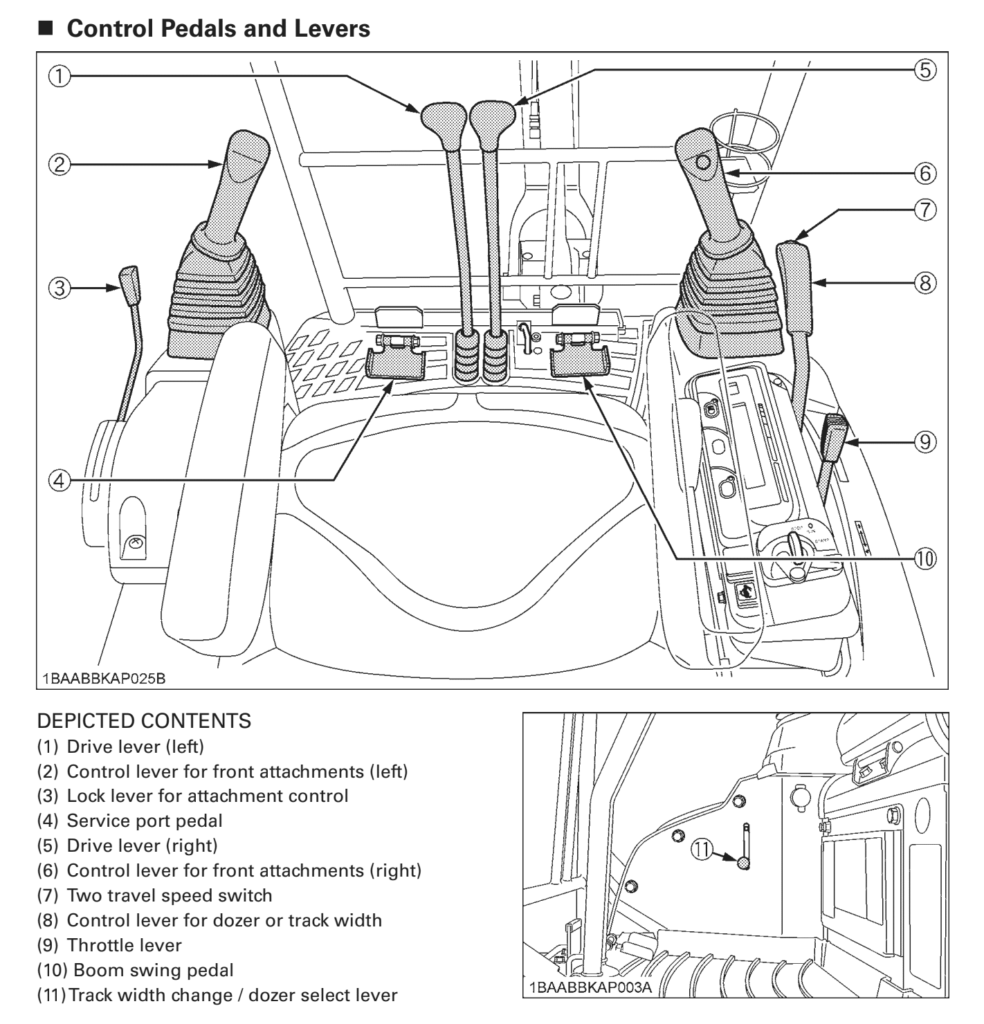
Systematic maintenance manual and maintenance cycle
Ежедневное обслуживание
- Lubrication and cleaning
- After each shift, clean the surface of the equipment, especially the mechanical moving parts.
- Lubricate all rotating parts and hinges appropriately to ensure that the friction coefficient is in a normal state.
- Hydraulic system inspection
- Check the hydraulic oil level, oil quality and oil temperature daily, and add or replace contaminated oil in time.
- Regularly check the hydraulic pipelines, joints and seals to ensure that there are no leaks.
Periodic inspection and maintenance
- Engine maintenance
- Replace the engine oil, air filter and fuel filter at the recommended working intervals (e.g. every 200 hours or every month).
- Check whether the cooling system is blocked or leaking, and clean and cool the radiator.
- Hydraulic system maintenance
- Analyze and test the hydraulic oil every 300 to 500 hours, and adjust the replacement cycle according to the test results.
- Clean the deposits inside the hydraulic valve body and oil circuit to ensure the system is responsive.
- Track and steering system
- Regularly check the track wear and adjust the tension every 200 hours.
- Check the wear of bearings, gears and hydraulic power-assisting components in the steering mechanism, and replace wearing parts in advance if necessary.
Troubleshooting and preventive maintenance
- Data monitoring
- Use the on-board diagnostic system to monitor engine speed, hydraulic pressure, temperature, vibration and other data in real time.
- Record abnormal data and establish equipment files to formulate preventive maintenance plans.
- Emergency handling of faults
- Develop detailed troubleshooting procedures for common faults (such as overheating of the hydraulic system, abnormal vibration of the engine, etc.).
- Train operators to master preliminary fault judgment and simple maintenance skills to ensure that problems are handled at an early stage.
Precautions and fault prevention during operation
Safe operation
- Strictly abide by the operating procedures
- The equipment must not be started when it is in an abnormal state, and all safety protection devices must be in place.
- When operating on a large slope or unstable terrain, pay attention to the adjustment of the center of gravity of the equipment to prevent rollover.
- Environmental monitoring
- Pay attention to weather changes in a timely manner, and take protective measures in advance in high temperature, low temperature, dusty, and humid environments.
- In extreme environments, it is recommended to shorten the continuous operation time and give the equipment enough rest.
Fault prevention and emergency measures
- Abnormal vibration and noise monitoring
- When the equipment has abnormal vibration, noise or operation delay, immediately reduce the workload and stop the machine for inspection.
- Perform fault self-inspection according to the equipment manual, and contact professional maintenance personnel if necessary.
- Data feedback and remote monitoring
- Use modern monitoring systems to track equipment status in real time, and automatically trigger alarms once signs of failure are found.
- It is recommended to establish a regular data evaluation mechanism to predict the risk of future equipment failure.
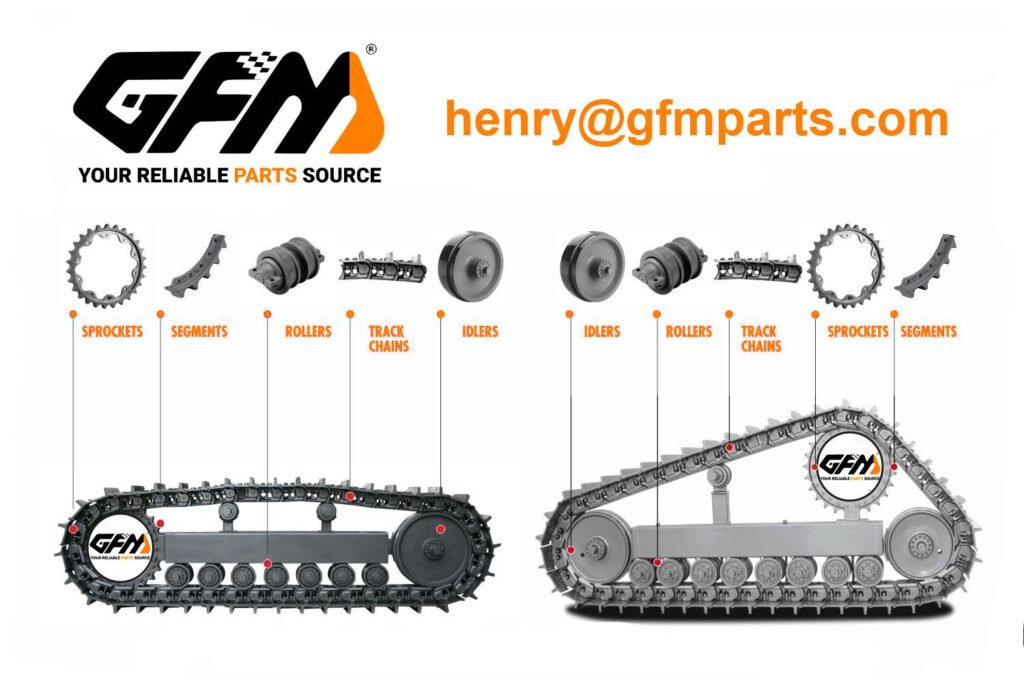
Service life of each component and influencing factors
Engine
- Service life reference
- Under good maintenance and reasonable working conditions, the cumulative engine usage hours can reach 2500 to 5000 hours or even higher.
- Influencing factors include fuel quality, lubricant replacement cycle, operating load and ambient temperature.
- Life extension suggestions
- Regularly replace engine oil and filters to keep the engine clean;
- Arrange short shutdowns for heat dissipation during continuous high-load operations to reduce temperature damage to mechanical components.
Hydraulic system
- Durability of core components
- The design life of hydraulic pumps and hydraulic cylinders is generally 3000 to 5000 hours, which is greatly affected by hydraulic oil contamination, temperature changes and operating frequency.
- Regularly inspect seals, oil pipes and filters to prevent system failures due to oil quality degradation.
Travel and steering system
- Track and transmission system
- Tracks and drive wheels are worn more due to harsh working environment (such as hard rock and gravel road surface). It is recommended to conduct a comprehensive inspection every 200 to 300 hours.
- Correctly adjust the track tension and replace the severely worn rubber pads or steel plates when necessary.
Working accessories
- Dipper stick and bucket
- Excavation accessories are greatly affected by the hardness of the working medium (such as rock and soil). Regularly measure the wear of the bucket edge. It is recommended to calibrate and replace them as necessary after each working season.
- Visually inspect the welding parts to prevent crack expansion and cause work accidents.
Technical and management suggestions
Intelligence and remote monitoring
- Internet of Things data collection
- Use sensors and remote data platforms to collect equipment operation data in real time to provide a basis for maintenance decisions.
- Remote diagnosis and early warning systems can detect hidden dangers in advance and reduce failure rates and maintenance costs.
Energy-saving and environmental protection technology upgrade
- Low-emission engine and intelligent hydraulic system
- Promote the use of the latest generation of low-emission engines, optimize the fuel injection system, and improve energy efficiency.
- Combine intelligent control algorithms to adjust the working parameters of the hydraulic system in real time to reduce energy waste.
Digital maintenance management
- Equipment health records and predictive maintenance
- Establish equipment operation data archives and use big data analysis to predict the life of key components.
- Develop periodic maintenance plans and use mobile APP or enterprise management systems to track equipment status in real time.
Получите быструю бесплатную расценку | Электронная почта: henry@gfmparts.com | Вотсап: +86 17705953659 |
Through detailed analysis of the core systems of mini excavators, refinement of specific operating methods, and formulation of periodic maintenance and preventive measures, we not only master the operating principles of the equipment, but also provide clear technical guidance for on-site operation and management. The key lies in:
- Strictly implement pre-operation inspections and safety regulations
- Develop detailed maintenance plans in accordance with manufacturer and engineering requirements
- Use modern monitoring methods to achieve real-time data feedback and fault prevention
Continuous technical training and equipment upgrades will further improve the operating efficiency and safety of mini excavators, and bring long-term benefits to engineering construction and equipment management.
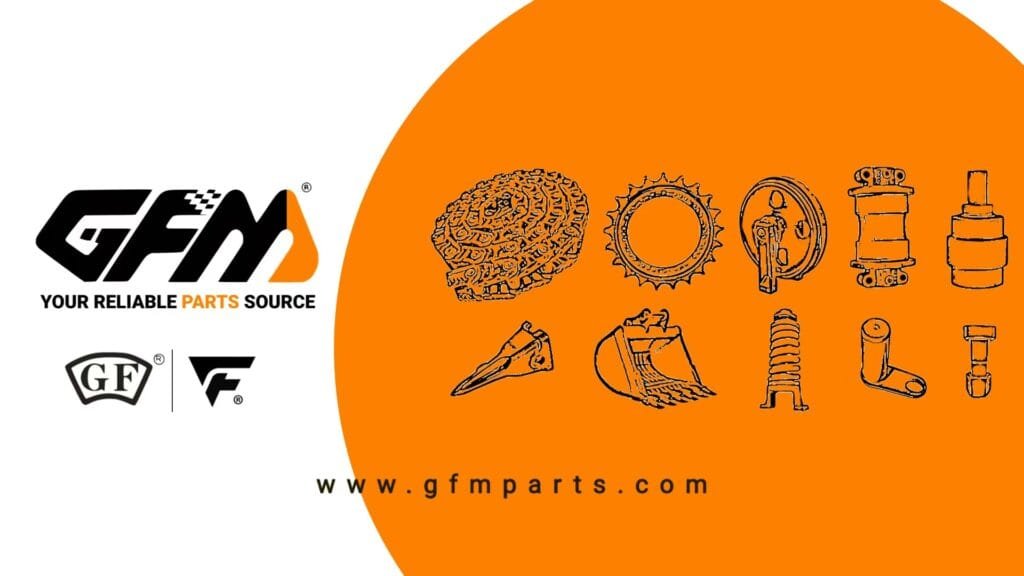