Как GFM производитель деталей для экскаваторов, we are constantly committed to providing customers with high-quality and high-performance products. Mini excavators are widely used in municipal engineering, garden construction, mining and other fields. Their compact structure and flexible operating performance make them important equipment under various complex working conditions. With the advancement of hydraulic control, electronic control system and Internet of Things technology, how to scientifically optimize equipment structure and operation process has become the key to improving overall production efficiency
Technical analysis of mini excavator track system
Structure and working principle of track system
Core structure: The track system of a mini excavator is mainly composed of track shoes, drive wheels, guide wheels and tensioning devices. The track shoes are generally designed with high-strength rubber and steel plates, which not only ensures sufficient wear resistance, but also effectively alleviates vibration. The design of the drive wheel and guide wheel needs to consider the load distribution and friction matching to ensure the smoothness of power transmission.
Принцип работы: The hydraulic system drives the track to move continuously through the drive wheel. The precise tension adjustment device ensures that the track maintains the optimal tension when the load changes, avoiding the risk of early wear or falling off due to too loose or too tight.
Technical parameters and design optimization
Materials and wear resistance: The use of multi-layer composite materials and nanotechnology to improve the rubber formula can significantly improve the wear resistance and anti-aging performance, while maintaining elasticity and impact resistance in extremely cold or high temperature environments.
Friction coefficient and shock absorption technology: Through the design of surface microstructures and the application of elastic shock-absorbing layers, the friction between the track and the ground is effectively reduced, and the off-road performance and energy consumption control of the equipment are improved.
Structural simulation analysis: With the help of finite element analysis (FEA), the force distribution and dynamic response characteristics of the track are optimized, thereby improving the reliability and service life of the overall system.
Daily inspection and fault warning
Inspection points: Regularly check the cracks, wear, tension and wheel system connection of the track plate. Use infrared imaging and vibration analysis to identify local stress concentration areas in advance.
Maintenance recommendations: When the track is found to be loose or the local wear exceeds the standard, the tensioning device should be adjusted or the wear parts should be replaced in time. It is recommended to use a real-time monitoring system based on the Internet of Things to achieve remote early warning and maintenance data analysis.
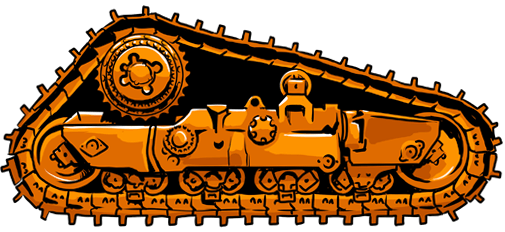
Technical analysis of mini excavator undercarriage system
Undercarriage structure and mechanical analysis
Structural design: As the load-bearing platform of the equipment, the undercarriage is usually constructed with high-strength steel plates, and long-term stability is guaranteed by advanced welding technology and anti-corrosion coating technology. In view of the impact and vibration during operation, the load distribution and stress concentration problems must be fully considered in the undercarriage design.
Mechanical simulation: The finite element method is used to analyze the stress, fatigue and vibration of the undercarriage structure to ensure that safety standards can be met under different working conditions. Dynamic load testing and vibration monitoring instruments can be used to calibrate the simulation model to ensure the accuracy of the design data.
Technical indicators and optimization directions
Carrying capacity and stability: The undercarriage design must meet the high load requirements under different models and working scenarios. By optimizing the support structure and adding anti-vibration devices, the risk of micro-cracks caused by fatigue during long-term operation is reduced.
Anti-corrosion and environmental adaptation: For wet and highly corrosive working environments, high-performance anti-corrosion coatings and cathodic protection technology are used to extend the service life of the undercarriage and reduce the cost of subsequent maintenance.
Modular design concept: The modular structure design is adopted to facilitate the rapid replacement of wear parts and overhaul to ensure that downtime is minimized.
Operation technology and system control of mini excavators
Hydraulic system and electronic control
Hydraulic system analysis: The efficient hydraulic system is the core of power transmission of mini excavators. Key components include hydraulic pumps, control valves and actuators. Precision hydraulic sensors and pressure monitoring modules can provide real-time feedback on system status to ensure stable working pressure under different workloads.
Electronic operation panel: Modern equipment is equipped with a multi-function touch operation interface that supports real-time data monitoring, fault diagnosis and remote upgrades. Operators can instantly adjust the working mode and walking speed through the system interface to optimize the operation process.
Operation process and intelligent assistance technology
Standard operation process:
- Pre-start inspection: Check the status of fuel, hydraulic oil, electronic control system and sensors to ensure that all parameters are within the normal range.
- Preheating procedure: After the engine and hydraulic system are started, the preheating is completed through the built-in self-check module to ensure that the temperature of each system meets the standard before entering the operation state.
- Operation execution: Select the appropriate operation mode according to the task requirements, reasonably allocate the handle action, and use the system feedback data to achieve precise control.
- Shutdown procedure: Shut down each module in the prescribed order, and use the data recording system to back up the operation log for subsequent analysis and maintenance.
Intelligent assistance technology: With the help of GPS, gyroscope and Internet of Things data acquisition system, operation path planning, precise positioning and dynamic load monitoring are realized, thereby reducing human operation errors and equipment losses.
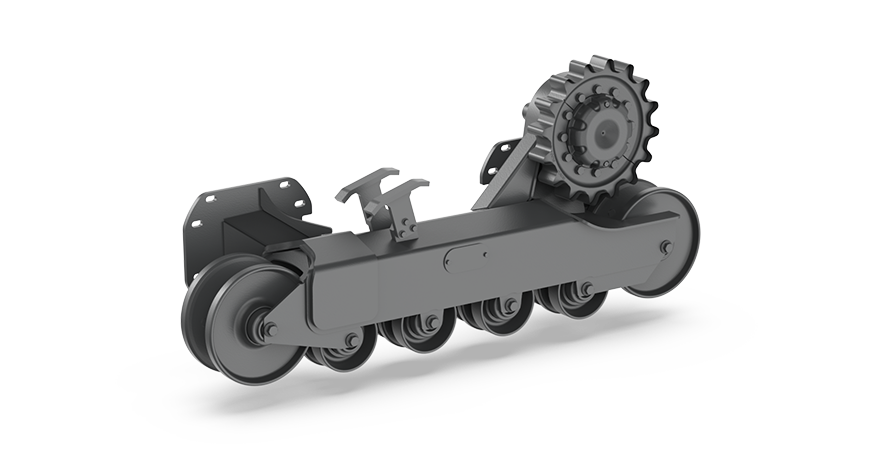
Safety and precautions for mini excavator operation
Safety operation procedures and protective measures
- Operator requirements: All operators must undergo professional training, have internationally or regionally recognized operation qualification certificates, and regularly participate in safety skills assessments.
- Safety protection equipment: In addition to basic protective equipment (safety helmets, goggles, reflective vests), it is recommended to install an on-board emergency power-off device and an automatic fault alarm system to ensure that countermeasures can be taken quickly in case of abnormalities.
- Operating environment monitoring: In severe weather and high-risk operating environments, real-time monitoring of obstacles, personnel and surrounding equipment in the operating area ensures all-round safety protection.
Common misunderstandings and risk prevention
- Sudden acceleration and sudden braking: Sudden acceleration or braking will cause a sharp change in the pressure of the hydraulic system, which may cause fatigue damage to key components. It is recommended to adopt progressive operation and use the system warning function.
- Insufficient equipment preheating: Ignoring the preheating procedure may increase friction in the engine and hydraulic system, thereby accelerating component wear. Equipment preheating and parameter calibration must be strictly carried out in accordance with the manufacturer’s requirements.
- Overload operation risk: Long-term overload operation not only reduces the life of the equipment, but may also cause serious failures in the hydraulic system and transmission system. It is recommended to develop an operation load assessment mechanism and adjust work tasks based on real-time monitoring data.
Technical analysis of the service life and influencing factors of mini excavators
Service life assessment method
- Vibration and fatigue testing: Use accelerometers and vibration sensors to monitor the dynamic response of the equipment during operation, and determine the fatigue life and potential failure points through data analysis.
- Data-driven life prediction: Combine historical maintenance data and real-time monitoring data, use big data analysis and machine learning algorithms to predict the remaining service life of key components, and then formulate preventive maintenance plans.
- Standardized testing: Relying on international standards (such as ISO, ANSI) and industry testing methods, regular inspection and calibration of key systems such as hydraulics, transmission, and undercarriage are carried out to ensure that each technical indicator meets the standard requirements.
The impact of environment and operating load on life
- Working environment: High temperature, low temperature, humidity and corrosive environment will accelerate material aging and wear. It is recommended to adopt corresponding protective measures and optimize the lubrication system according to the operating scenario.
- Operation load: Overload and long-term continuous operation will cause premature failure of the hydraulic system, undercarriage and key transmission parts. Through real-time monitoring and intelligent control, the load is reasonably distributed to reduce equipment loss.
Suggestions for extending equipment life
- Preventive maintenance: Establish equipment operation files, formulate detailed maintenance and maintenance cycles, and prevent failures in advance through regular replacement of wearing parts, lubricant analysis and component inspection.
- Technology upgrade: Use advanced monitoring systems and self-diagnosis modules to achieve real-time feedback and automatic alarm of equipment status, and adjust working parameters and load distribution in time.
- Operation standardization: Reduce equipment damage caused by human factors through standardized operation training and strict operating procedures.
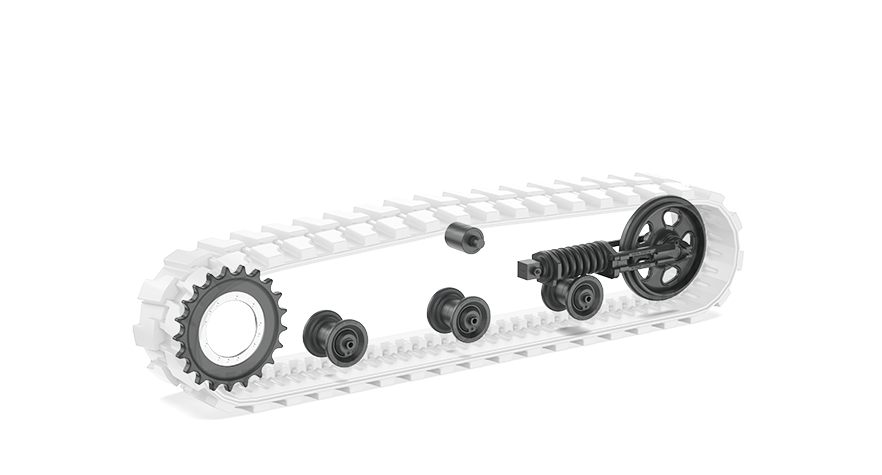
Maintenance and maintenance manual for mini excavators
Daily inspection and maintenance process
Hydraulic system maintenance:
- Check the hydraulic oil level, oil quality and filter status every day, and use online monitoring instruments to record parameters such as oil temperature and oil pressure;
- Regularly analyze hydraulic oil samples, evaluate the internal wear metal content, and replace hydraulic oil and filters in time.
Engine and transmission system:
- Regularly replace engine oil, air filter and fuel filter;
- Check the lubrication and wear status of the transmission system to ensure that the transmission gears and bearings are in good working condition.
Track and undercarriage maintenance:
- After each operation, clean the sand and debris from the tracks, rollers and undercarriage to avoid intrusion into key connecting parts;
- Regularly check the welding points and anti-corrosion coatings. If local damage is found, repair them in time.
Regular maintenance and overhaul plan
- Comprehensive inspection: Conduct a comprehensive inspection every quarter, including an overall inspection of the hydraulic system, electronic control system and structural components, and use data records to analyze fault trends;
- Overhaul cycle: According to the operating intensity of the equipment, it is recommended to perform an overhaul after every 2000 to 3000 hours of operation, and replace and adjust key components;
- Maintenance record management: Establish an electronic maintenance file system to record each maintenance, inspection data and maintenance reasons, so as to facilitate long-term data analysis and technical improvement.
Intelligent monitoring and remote diagnosis
- Internet of Things monitoring: Deploy intelligent sensors and remote monitoring platforms to collect equipment operation data in real time and realize automatic warning of abnormal data;
- Remote diagnosis system: Use big data and cloud analysis technology to timely determine the cause of equipment failure, optimize maintenance plans, and reduce downtime and maintenance costs.
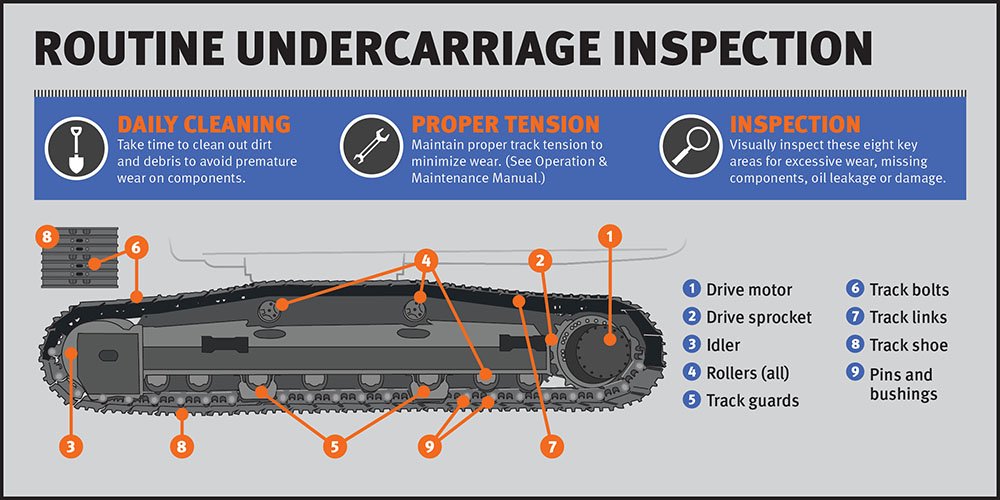
Advanced technology dimensions and cutting-edge applications
Energy saving, environmental protection and intelligent operation
- Energy consumption management: By optimizing the operation path and load distribution, frequency conversion control technology is adopted to achieve optimal energy consumption;
- Environmentally friendly materials: Environmentally friendly and non-toxic materials are used in consumables such as lubricants and cleaning agents to meet green environmental protection standards and reduce environmental pollution.
Digital transformation and smart construction sites
- Data-driven decision-making: Combined with real-time monitoring data of the operation site, the data analysis platform is used to optimize scheduling, maintenance plans and equipment update cycles;
- Smart construction site applications: Using advanced technologies such as GPS positioning and drone monitoring, the digital management of equipment scheduling and on-site safety is realized to improve overall operation efficiency and safety.
Operator training and skill improvement
- Professional training system: Formulate standardized training plans covering modules such as hydraulic systems, electronic control systems, maintenance and emergency handling, and organize assessments regularly;
- Skill certification system: Promote professional certification to ensure that each operator has the latest technical knowledge and operating skills and improve the overall team quality.
Получите быструю бесплатную расценку | Электронная почта: henry@gfmparts.com | Вотсап: +86 17705953659 |
Through a comprehensive technical analysis of the track system, undercarriage structure, operation control, safety precautions, service life and maintenance of mini excavators, this article provides customers with a systematic and in-depth technical guidance. We recommend that customers use intelligent monitoring and data analysis technology in combination with the actual working environment and equipment status, implement preventive maintenance and regular overhauls, so as to effectively extend the life of the equipment, improve operating efficiency and reduce operating costs.
Как GFM производитель деталей ходовой части экскаватора, we continue to promote product technology upgrades and service optimization, and are committed to providing customers with comprehensive and technologically advanced solutions.
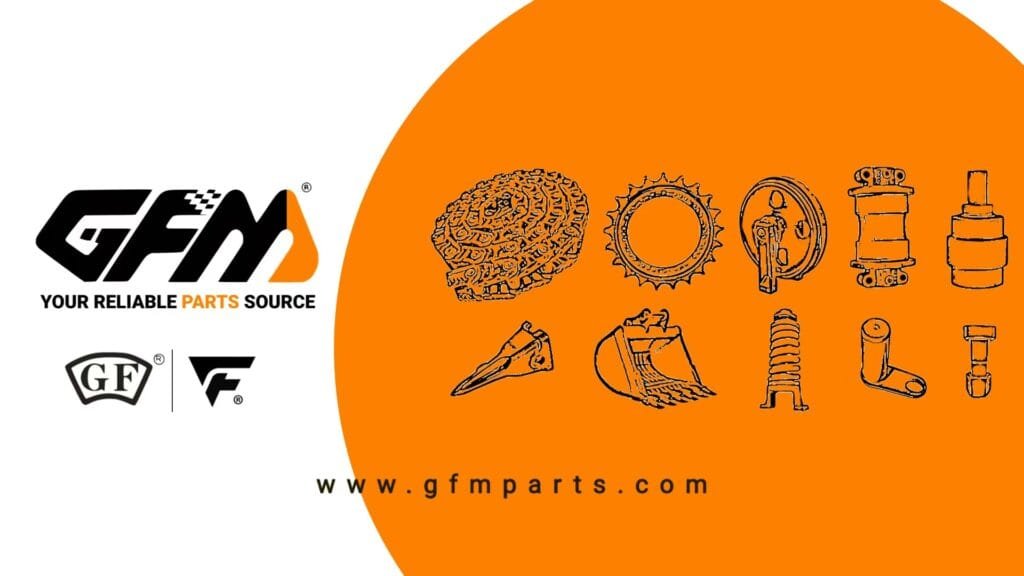