In the world of construction machinery, excavators are like the bones on the construction site, and track shoes are the foundation of the soles of the feet that support the movement and operation of this huge machine. They carry the weight of the whole machine, accept the impact from complex terrain, and face long-term friction and wear. Once there is a problem with the track shoe, it will not only affect the construction efficiency, but may even cause the whole machine to stop, resulting in high losses. Therefore, choosing a pair of high-performance track shoes is of great importance to improving the working efficiency of the excavator and extending the life of the whole machine.
With the increasing demand for high-intensity construction such as infrastructure expansion, mining development, and overseas projects, the market has put forward higher requirements for track shoe products-not only to be resistant to impact and wear, but also to be stable and not deformed, and to adapt to a variety of working conditions. This is exactly the area where GFM continues to stand out in the global construction machinery market.
Table of contents
- GFM: An industry leader with 14 years of deep cultivation in track shoe manufacturing
- The core role and key structure analysis of excavator track shoes
- Detailed explanation of the process advantages and product performance of GFM track shoes
- Customer case analysis: GFM track plates’ outstanding performance in global construction projects
- How to choose a suitable track shoe? GFM provides you with customized solutions
- Factory Strength: How GFM Achieves High-Quality Control from Raw Materials to Delivery
GFM: An industry leader with 14 years of deep cultivation in track shoe manufacturing
Since its establishment, GFM excavator track shoe manufacturers has always focused on the research and development and manufacturing of excavator undercarriage parts, especially in the field of track shoes, and has been deeply engaged in it for more than 10 years. At present, GFM has a modern production plant of more than 10,000 square meters, with an annual output of more than 500,000 track plates. Its products are widely used in more than 20 brands and more than 100 types of engineering machinery equipment.
The company adheres to the concept of “technological innovation and quality-oriented”, and independently controls the entire process from material procurement, mold design, heat treatment process, surface treatment to final assembly. GFM is a first-tier supporting supplier for many well-known excavator brands, including large domestic main engine manufacturers and key agents in Southeast Asia, the Middle East and Africa.
Not only that, GFM also has an independent technology research and development center, and regularly cooperates with colleges and universities and material research institutions to continuously optimize the wear resistance, impact resistance and service life of track plates. Many processes have applied for national utility model patents, and are the first in the industry to promote the industrial model of “customized track plate solutions”.
The core role and key structure analysis of excavator track shoes
The track plate is one of the core components of the track assembly, usually made of high-strength alloy steel stamped and welded. Its structural design directly affects the force distribution of the crawler, the ground adhesion and the stability of the whole machine operation. Generally speaking, a set of crawler chains contains several crawler plates, which are connected to the chain links by bolts and play multiple roles of pressure bearing, guiding and traction in the walking of the excavator.
At present, the mainstream crawler plates in the market can be divided into three categories according to their uses: standard type, widened type and swamp type:
- Standard type: suitable for most general working conditions, balanced design, widely used in foundation projects such as municipal and residential construction;
- Wide type: widened design based on the standard type, increasing the ground contact area, suitable for soft soil and slight swamp areas;
- Swamp type: adopts ultra-wide structure and special reinforcement ribs, suitable for extremely soft environments such as deep mud and paddy fields.
Common crawler plate specifications are: 500mm, 600mm, 700mm, 800mm, etc., corresponding to excavators of different tonnages, and the chain link hole spacing, pitch and chassis width must be considered together during installation.
In addition to standard models, GFM also supports non-standard customization, including details such as hole spacing, plate thickness, and rib style, to ensure that each track plate is perfectly matched with the customer’s equipment.
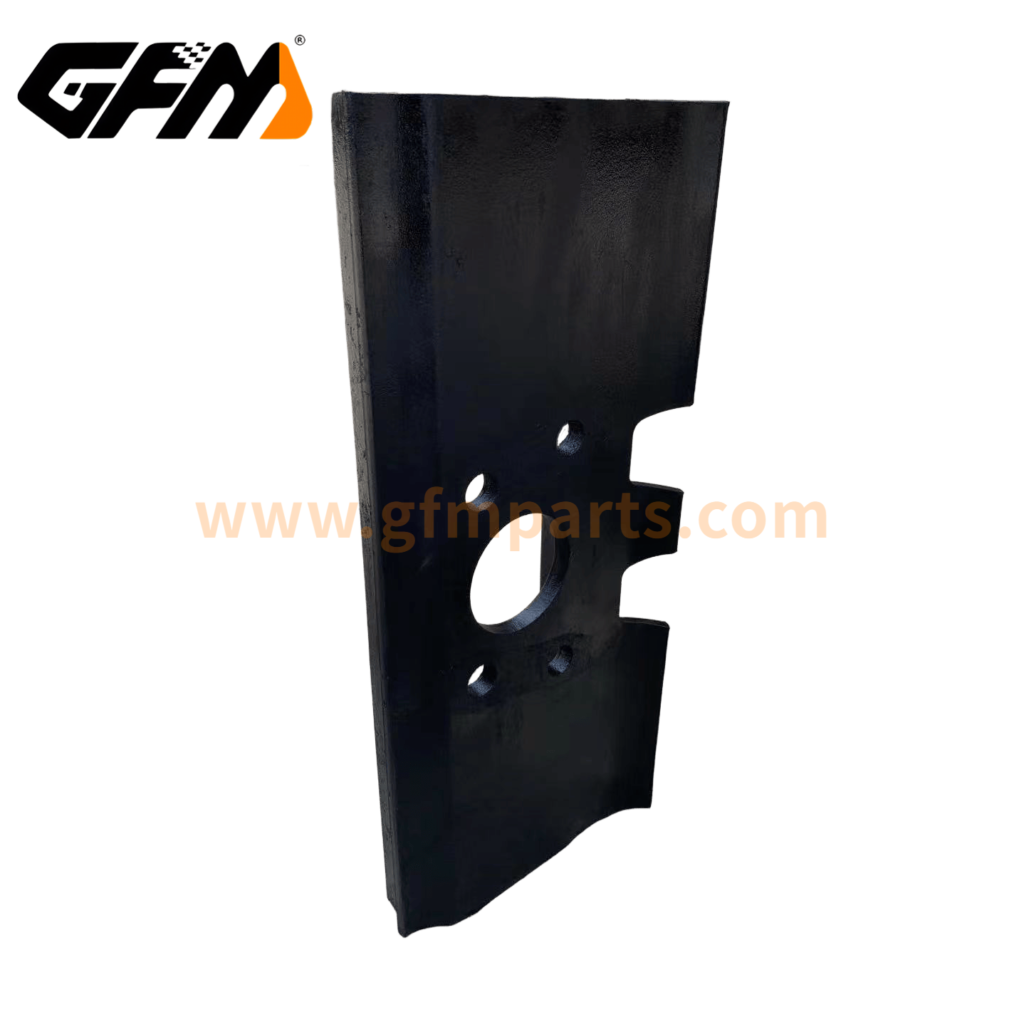
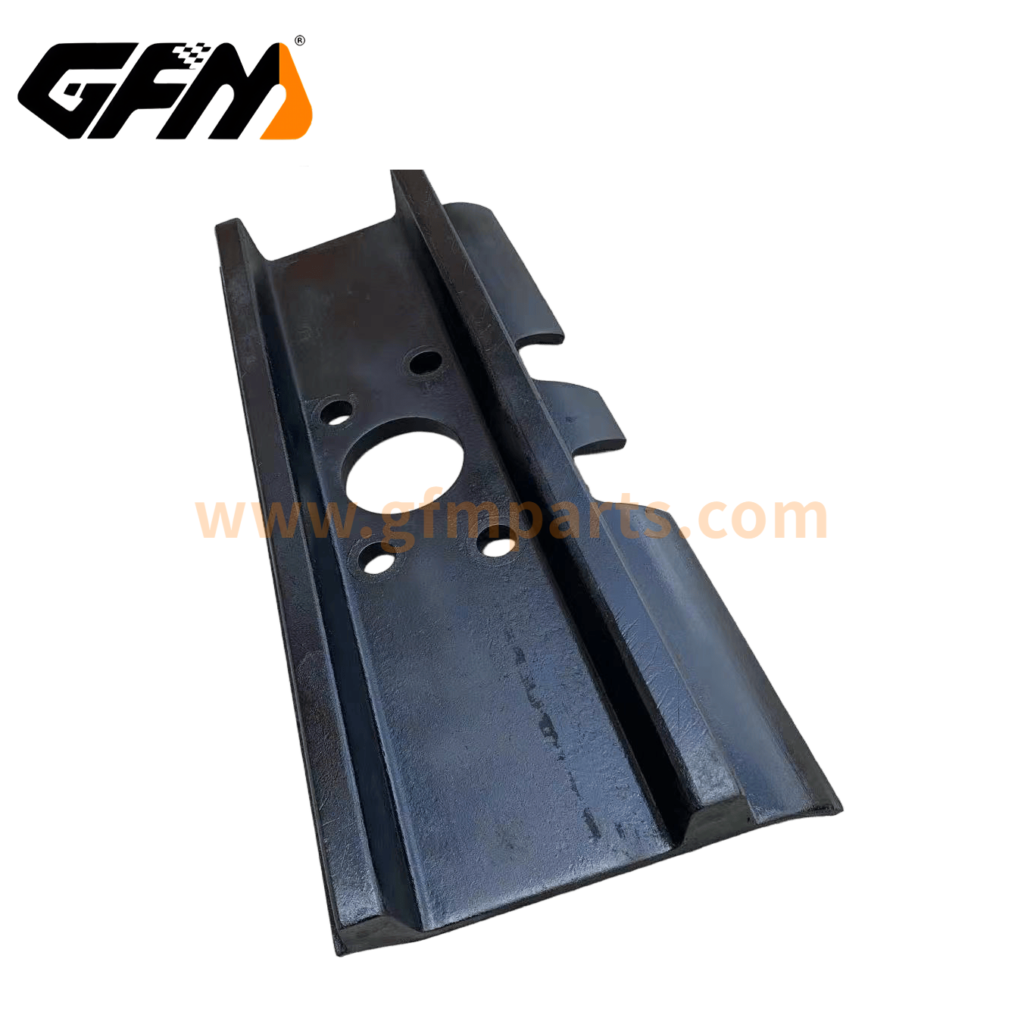
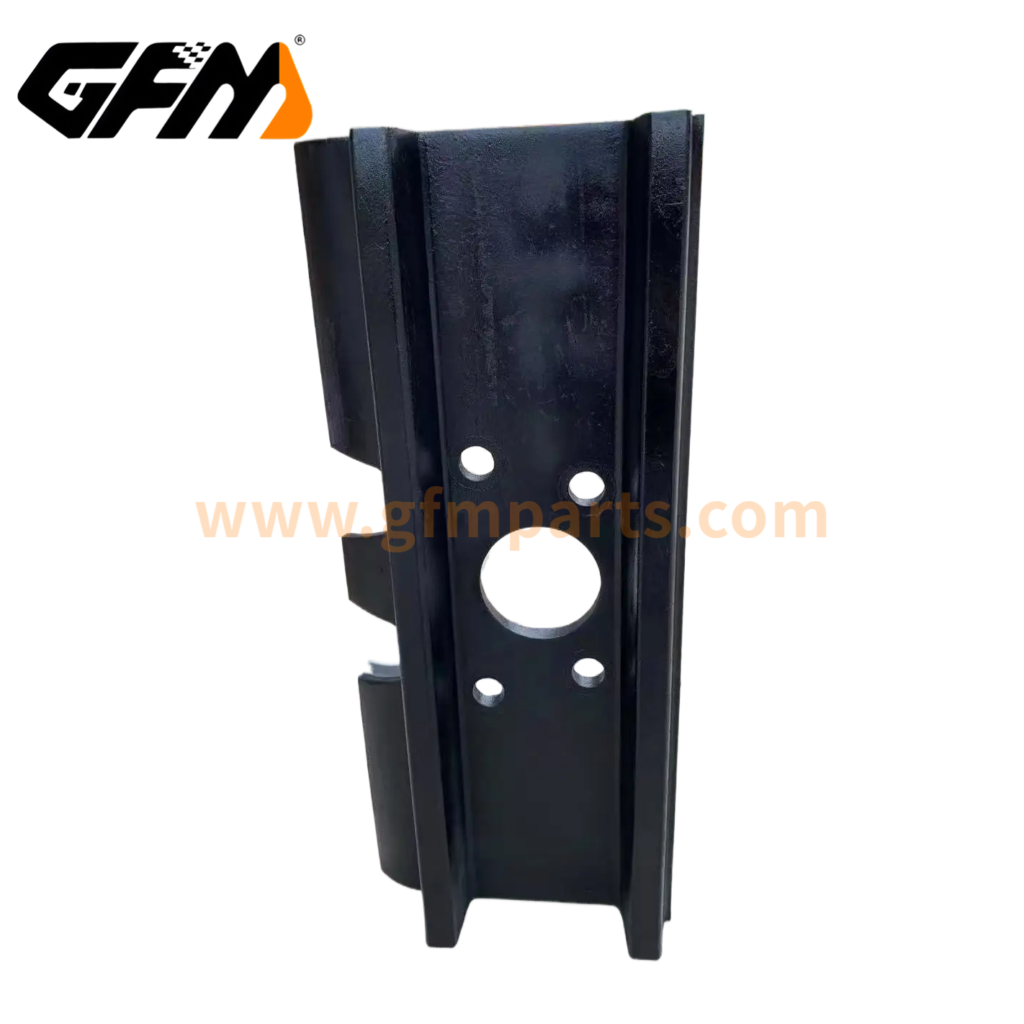
Detailed explanation of the process advantages and product performance of GFM track shoes
GFM’s track plate production process strictly follows ISO quality management standards and combines a number of independently developed processes to ensure that each product has excellent impact resistance and wear resistance. The following are several highlights of GFM in terms of technology:
Strict material selection: GFM prefers high-strength alloy steel and manganese steel materials, which have both strength and ductility to ensure that they are not easy to break and deform under frequent impact and lateral pressure.
Heat treatment optimization: All track plates need to undergo high-temperature quenching and low-temperature tempering after stamping. The surface hardness is controlled between HRC45~52, and the inner core maintains a certain toughness, taking into account wear resistance and crack resistance.
High-precision welding process: GFM uses a robot automatic welding system to effectively prevent quality risks such as false welding and biased welding. The welds are stable and consistent, and secondary stress annealing is performed to reduce the risk of cracks during use.
Surface treatment: All track plates are shot blasted and treated with environmentally friendly anti-rust coating before leaving the factory to improve corrosion resistance, especially suitable for coastal and high-humidity environments.
Strict testing: Each batch of track plates must undergo hardness testing, bending testing, metallographic analysis and other processes before leaving the factory to ensure that all indicators meet the standards.
According to GFM customers’ field test feedback in Central Asia, after using GFM track plates, the average replacement cycle is extended to more than 18 months, which is more than 30% higher than general market products, effectively reducing the maintenance cost of construction equipment.
Customer case analysis: GFM track plates’ outstanding performance in global construction projects
GFM track plates have been widely used in many large-scale engineering projects around the world. The following are several typical cases:
A large domestic coal mine project: The project uses a 50-ton mining excavator, which works more than 18 hours a day. The original track shoes frequently broke due to insufficient strength. After replacing them with GFM thickened track shoes, no damage occurred within half a year, and the equipment attendance rate increased by 12%.
Southeast Asian tropical forest mining project: The project is slippery and muddy all year round, and the track is very easy to slip or sink. The swamp-type ultra-wide track shoes customized by GFM not only improve the grip, but also effectively disperse the pressure of the fuselage, successfully solving the problem of frequent equipment sinking.
Road repair project in extremely cold areas of Russia: The local winter temperature can reach below minus 30 degrees Celsius, and most track shoes are brittle in low temperatures. GFM specially optimizes the material ratio to maintain low-temperature toughness and ensure that the customer’s construction cycle is not interrupted.
These cases not only reflect the strong adaptability of GFM products in different geographical environments, but also reflect its response speed and professional ability in the field of non-standard customization.
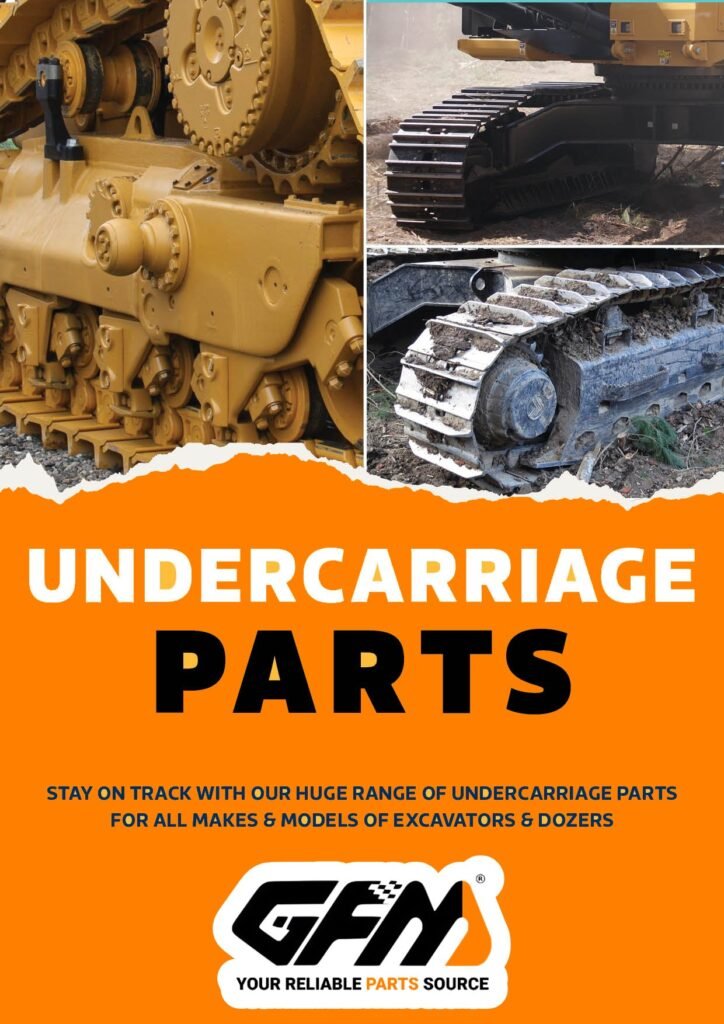
How to choose a suitable track shoe? GFM provides you with customized solutions
Faced with complex and changing construction environments and constantly upgraded equipment models, choosing a suitable track shoe is not an easy task. GFM provides customers with the following practical selection suggestions:
Selection by construction scenario: such as sand, stone yard, paddy field, etc., each environment has different requirements for the width, thickness and tooth shape of the track shoe.
Matching by equipment tonnage: From 3-ton small excavators to 80-ton mining equipment, the size and force requirements of the track shoe are significantly different.
Provide drawings or samples: GFM can develop corresponding products based on the CAD drawings or samples provided by customers, and support customization of various hole types, reinforcement ribs and bolt positions.
Expert team assistance: Customers can obtain technical support from GFM’s senior engineers to help confirm model matching and installation suggestions.
In addition, GFM also provides customers with free sample proofing services and technical data downloads to improve procurement decision-making efficiency.
Factory Strength: How GFM Achieves High-Quality Control from Raw Materials to Delivery
GFM track plates’ high quality comes not only from materials and processes, but also from a systematic production and quality control system:
Production equipment: Introducing multiple large-scale stamping machines, automatic welding robots, multi-station heat treatment furnaces and CNC drilling machines, the whole process is automated, accurate and efficient.
Quality Control Process: Establishing a professional quality inspection center, equipped with metallographic microscopes, three-coordinate measuring machines, tensile testing machines and other equipment, with a total of 8 quality control checkpoints from raw materials entering the factory to finished products leaving the warehouse.
Employee Management: Frontline workers must be certified to work, and skills assessment and technical training are conducted every quarter; key positions such as welding and heat treatment are handled by senior technicians.
Environmental Protection Measures: Strictly abide by environmental protection standards during the production process, use environmentally friendly rust removers and coating materials, and be rated as a “Green Factory Demonstration Unit”.
It is through the system guarantee of “equipment + people + process” that GFM can continuously and stably output high-quality products in the field of track plates.
Get a quick free quote | Email: henry@gfmparts.com | Whatsapp: +86 17705953659 |
In the context of increasingly efficient modern engineering construction and increasingly extreme environments, a pair of high-performance track shoes is no longer a cost, but an investment. It is related to the equipment’s attendance rate, construction stability, and overall project cycle control.
With more than 20 years of deep manufacturing experience, continuous technological innovation and strict quality control, GFM has become a trusted partner of many OEMs and construction companies. Whether you are facing high-intensity operations or special working conditions, GFM can provide you with the most suitable track shoe solutions.
In the future, GFM track shoe manufacturers will continue to uphold the concept of “making every excavator go further” and work with global customers to create a stronger and more efficient future for construction machinery.
If you want to obtain samples, drawings or more technical support, please feel free to contact the GFM team at any time. We look forward to working with you for a win-win situation.
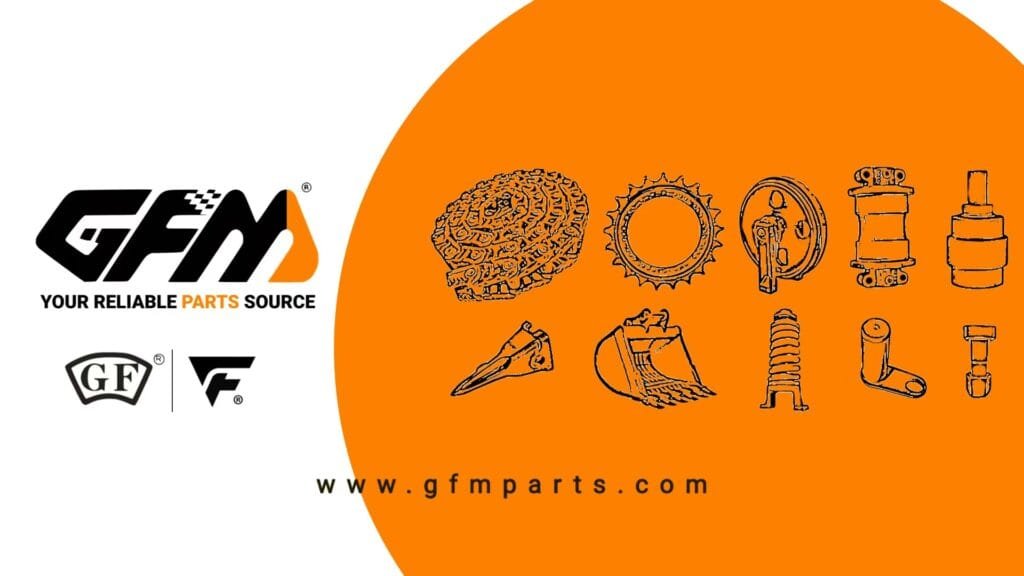