As an important part of heavy engineering machinery, the performance of bulldozers depends not only on the engine and hydraulic system, but also on the sturdy and durable undercarriage system. Undercarriage parts, including crawler tracks, track links, rollers, guide wheels, drive wheels and track shoes, bear the weight of the whole machine and the load support tasks under complex working conditions, which is the guarantee of stability and efficiency of bulldozers during high-intensity operations.
With the continuous advancement of global infrastructure construction, especially the rapid growth of large-scale earthwork projects, mining and water conservancy projects in countries along the “Belt and Road” and emerging market countries, the bulldozer market continues to expand, and the quality and supply capacity of undercarriage parts have also become key factors that whole machine manufacturers and terminal purchasers pay close attention to. Understanding the world’s top bulldozer parts manufacturers can not only help companies make wise decisions in the procurement process, but also effectively avoid equipment damage, construction interruptions and even safety accidents caused by low-quality and shoddy accessories.
We will select five manufacturers with deep accumulation and market recognition in the field of undercarriage parts from around the world, deeply analyze their advantages in technology, process, product structure and market service, and compare GFM’s positioning and rise path in the global market as a representative of Chinese manufacturing, to help you fully understand the pattern and selection criteria of this industry.
Table of contents
- Caterpillar: The undercarriage power of a century-old brand and heavy industry giant
- Komatsu: Model of Japanese manufacturing rigor and undercarriage parts reliability
- Liebherr: High-performance undercarriage parts made with German technology
- GFM: Representative of Made in China, a rising force with both customization and cost-effectiveness
- Volvo CE: R&D of undercarriage parts under the Nordic green concept
- How to choose a suitable bulldozer undercarriage parts manufacturer
Caterpillar: The undercarriage power of a century-old brand and heavy industry giant
Company background and global influence
Founded in 1925, Caterpillar (CAT for short) is one of the most influential construction machinery manufacturers in the world, headquartered in Peoria, Illinois, USA. As one of the world’s top 500 companies, Caterpillar has an unparalleled market position in the field of bulldozers, and its undercarriage parts are widely used in mines, quarries, heavy earthwork and road construction.
Undercarriage parts technical advantages
CAT undercarriage parts manufacturing relies on its self-developed high-strength forging materials and heat treatment processes to make its track sections, supporting wheels and other components have super wear resistance and impact resistance. Taking its D11 series bulldozer as an example, its undercarriage system adopts oil bath sealed rollers, thickened track joints and central lubrication technology, which greatly extends the maintenance cycle and service life.
Process highlights and quality control
Caterpillar’s undercarriage parts production process covers a number of high-precision technologies such as automated welding, laser cutting and plasma heat treatment, with a global unified quality standard and service network to ensure that every component meets the highest standards of engineering applications.
Market data
According to Statista statistics, Caterpillar’s share of the global bulldozer market in 2023 is about 30%, of which the annual output value of original undercarriage parts for the D6 to D11 series exceeds US$900 million.
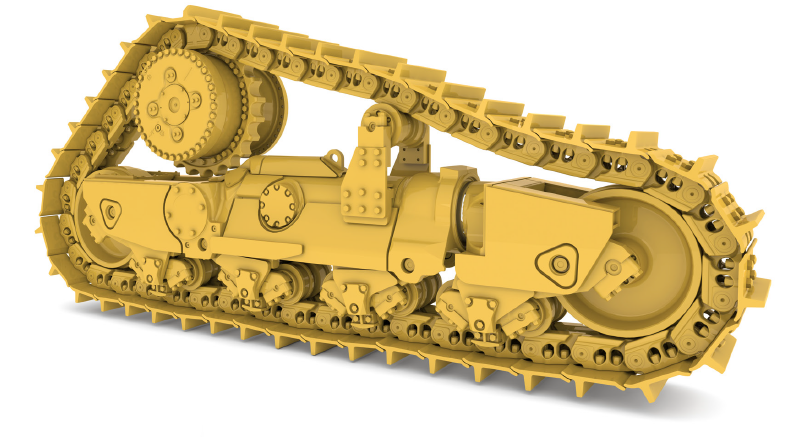
Are you looking for quality bulldozer parts at the best price? You have come to the right place. We are committed to providing excellent products and offering the best value to our customers. Your satisfaction is our motivation. Send an email to henry@gfmparts.com now and our bulldozer undercarriage experts will be happy to serve you.
Komatsu: Model of Japanese manufacturing rigor and undercarriage parts reliability
Brand profile and manufacturing system
Founded in 1921, Komatsu is Japan’s largest and the world’s second largest construction machinery manufacturer. Its bulldozer product line includes D65, D155, D275, D475 and other series, which are mainly used in mining stripping, port preparation and large-scale civil engineering projects.
Performance characteristics of undercarriage parts
Based on high-strength alloy steel casting, combined with multi-stage heat treatment, the tensile strength and crack resistance of the track link are significantly better than the industry average. At the same time, the track roller adopts multi-layer oil seals and labyrinth structure to effectively prevent sand and mud erosion.
Technical rigor
Komatsu’s unique production management model (for example: JIT just-in-time production system) ensures that the entire process from design to manufacturing of parts is in a high-efficiency and high-precision state. Its parts bases in Tokyo and Osaka have exclusive undercarriage parts test centers, which regularly conduct load fatigue tests and corrosion resistance analysis.
International certification and market feedback
All Komatsu undercarriage parts comply with ISO 9001 and ISO/TS 16949 quality management system standards, and are widely exported to North America, Australia, Southeast Asia and the Middle East. According to its 2023 annual report, the undercarriage parts division’s revenue accounts for approximately 28% of the overall bulldozer parts business.
Liebherr: High-performance undercarriage parts made with German technology
Company introduction
Founded in 1949 and headquartered in Germany, Liebherr is a family-controlled heavy equipment manufacturer. Although its bulldozer market share is relatively small, Liebherr’s technological leadership in the manufacture of high-end undercarriage parts is widely recognized, especially for special working conditions.
Undercarriage parts design features
Liebherr adopts a modular undercarriage design for quick disassembly and maintenance. The track section is forged with high-carbon chromium steel, combined with nano heat treatment technology, which effectively improves durability and corrosion resistance. At the same time, its guide wheel system has added intelligent dynamic tensioning technology to make the bulldozer run more smoothly on uneven terrain.
Advanced manufacturing technology
Liebherr has introduced Siemens-controlled five-axis CNC numerical control equipment in its Austrian factory to achieve high-precision processing of key undercarriage parts. Each batch of products shipped is accompanied by a detailed test report, and the raw material batches can be traced.
Authoritative Recognition
Liebherr undercarriage products have passed CE certification, REACH standards and German internal mechanical durability test standards, and are widely used in wind power construction, plateau railways and polar scientific research equipment.
GFM: Representative of Made in China, a rising force with both customization and cost-effectiveness
Company Background and Development Path
GFM, as a local Chinese engineering machinery parts manufacturer, has been deeply involved in the undercarriage parts industry for more than 20 years, focusing on the production and export of bulldozer and excavator undercarriage systems. The company has a complete independent production line and R&D center, which can realize the whole process control from raw material selection, mold development to finished product testing.
Product Coverage and Technical Strength
GFM’s bulldozer undercarriage parts products include:
- Track shoes (standard, swamp, reinforced)
- Track links (bolted, pin-pressed)
- Rollers and guide wheels (single-side/double-side support)
- Drive wheel body (precision control of heat treatment of gear ring)
Adopting multiple advanced technologies such as isothermal forging, CNC machining, induction hardening and shot peening, the comprehensive life of the product can reach more than 4,000 hours.
Customization and service capabilities
Supports drawing customization and fast proofing, and is compatible with multiple brands such as Komatsu, CAT, Shantui, Zoomlion, etc. At the same time, it provides customers with global logistics support and after-sales parts tracking system to reduce spare parts management costs.
Customers and certifications
GFM products are exported to more than 30 countries including South America, Southeast Asia, Africa, and the Middle East, and have obtained CE, ISO 9001 and BV classification society certifications. Some products have entered the European and American aftermarket and have been evaluated by customers as “the best choice for cost performance.”
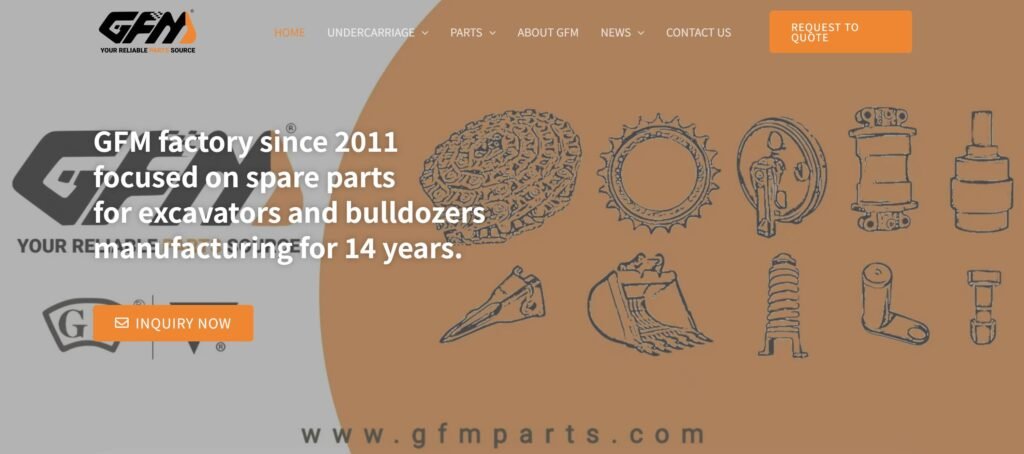
Volvo CE: R&D of undercarriage parts under the Nordic green concept
Brand positioning and development concept
As a well-known Swedish brand, Volvo Construction Equipment (Volvo CE) has always adhered to the concept of environmental protection and sustainable development in the manufacturing of heavy equipment. Although the investment in bulldozers is relatively small, the quality of its undercarriage parts is highly recognized for its high performance and green manufacturing.
Undercarriage materials and processes
Volvo CE uses recyclable high-manganese wear-resistant steel and uses low-energy laser cutting technology to effectively reduce the carbon footprint of production. The undercarriage structure adopts a modular design for easy maintenance and upgrading.
Supporting technology and system support
Volvo Assist intelligent system can monitor undercarriage wear and usage intensity in real time, and combined with remote diagnosis functions to help users achieve preventive maintenance and reduce the risk of sudden downtime.
International certification and reputation
Volvo CE undercarriage parts comply with ISO 14001 environmental standards and are widely used in environmental protection projects and urban infrastructure projects, especially favored by users in the high-end market in Europe and the United States.
How to choose a suitable bulldozer undercarriage parts manufacturer
To choose a undercarriage manufacturer that suits your engineering needs, you need to conduct a comprehensive assessment based on the following points:
Clear the working environment and load requirements
Regular earthwork vs. highly corrosive mining areas vs. swamp terrain, products with different strengths and coatings should be selected.
Evaluate the manufacturer’s strength and supporting capabilities
Does it have a complete manufacturing and testing process? Does it have international certification? Does it provide after-sales technical support?
Pay attention to delivery and customization services
Can standard parts be delivered quickly? Can special models be customized? Can proofing verification be provided?
Recommended tools and methods
Use the “Parts Life Management System” for periodic assessment (e.g. Komtrax, Cat VisionLink)
It is recommended to provide material reports, heat treatment process instructions and on-site installation guidance documents when purchasing
Avoid common purchasing misunderstandings
Mistakenly trusting counterfeit products or second-hand refurbished parts can easily lead to track shedding and breakage accidents
Ignoring the compatibility issues with the whole machine, resulting in abnormal assembly clearance or failure to operate normally
Hızlı ve ücretsiz bir teklif alın | E-posta: henry@gfmparts.com | Whatsapp: +86 17705953659 |
Through a comparative analysis of the world’s top five bulldozer undercarriage parts manufacturers, it is not difficult to see that each major brand has its own advantages: CAT and Komatsu represent technical stability and global influence, while Liebherr and Volvo CE focus on special working conditions and green manufacturing. As a representative of Made in China, GFM is continuously expanding its influence in the global market with its flexible customization capabilities, high cost-effectiveness and reliable product quality.
GFM has not only accumulated rich experience in traditional manufacturing, but also continued to make efforts in intelligent production, rapid delivery and international cooperation, and gradually built an efficient, professional and sustainable construction machinery parts supply ecosystem. As the world pays more attention to environmental protection and equipment operation efficiency, GFM is also developing degradable packaging materials, low-carbon manufacturing processes and intelligent sensing undercarriage parts to respond to the industry’s expectations for future technologies.
For global buyers, reasonable comparison and accurate selection will be the key to ensuring smooth project construction and maximizing equipment life. Whether you are a large contractor, mining company or complete machine manufacturer, choosing a trustworthy undercarriage parts manufacturer will provide a more solid “foundation” for your equipment.
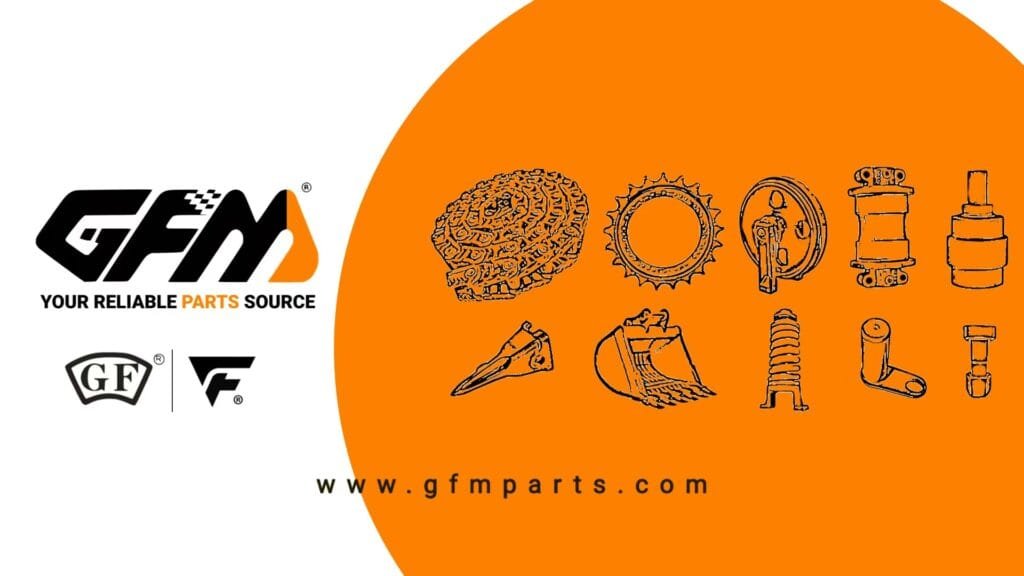