Table of contents
- When to replace the excavator bucket teeth? Identify 5 key signs of wear
- Preparation for replacing excavator bucket teeth: tools, environment and safety
- Detailed steps for replacing excavator teeth: complete step by step without pressure
- Common mistakes when replacing bucket teeth and how to avoid them
- How to extend the service life of the new bucket teeth? Practical maintenance tips sharing
- Why choose GFM excavator parts factory to replace your bucket teeth?
On any construction site, the efficiency of the excavator often directly affects the progress and cost control of the entire project. Among all the parts of the excavator, the bucket teeth, although seemingly insignificant, play a key role. The bucket teeth are the first contact point between the excavator and materials such as soil, rock, and gravel. It not only affects the digging force, but also determines the efficiency and accuracy of each digging.
During long-term use, the bucket teeth will wear or even break due to continuous friction. If they are not replaced in time, it will not only affect the digging efficiency, but may even damage the bucket tooth seat, destroy the entire bucket system, and increase maintenance costs. This article will give you a detailed introduction on how to judge whether the bucket teeth should be replaced, the specific steps for replacement, how to extend the life of the bucket teeth during use, and especially recommend why choosing the bucket teeth provided by the GFM excavator bucket teeth manufacturers will be a more reliable choice.
When to replace the excavator bucket teeth? Identify 5 key signs of wear
The digging efficiency is significantly reduced
The tip of the bucket tooth is the key part for breaking the ground. Once it becomes blunt, the digging resistance increases, the excavator moves slower, and the construction progress is hindered. If you find that the hourly output is reduced under the same working conditions, it is likely that the bucket teeth are no longer sharp.
Abnormal sound during excavation
The new bucket teeth make a relatively stable sound during excavation. Once a bucket tooth is loose or falls off, a “metal knocking” or abnormal vibration sound will be heard during the excavation process. These are warning signs of bucket teeth aging or improper installation.
Tooth tip is obviously blunted or even broken
Observe the bucket teeth with the naked eye. If the originally sharp tooth head has become flat, or even cracked or broken, it must be replaced immediately. Continued use will damage the bucket tooth seat or cause abnormal stress on other parts.
Tooth root is almost worn flat
Some users only pay attention to the tooth tip and ignore the root. In fact, the core of the strength of the bucket tooth is in the root. Once the root is severely worn, it is easy to break during high-intensity operations, causing the entire bucket device to fail to work.
Tooth seat deformation or lock pin loose
Every time you replace the bucket teeth, you should check the status of the tooth seat and lock pin. If you find that the tooth seat is no longer vertical or the lock pin cannot stably fix the bucket teeth, it is difficult to ensure safe use even if you replace the new bucket teeth.
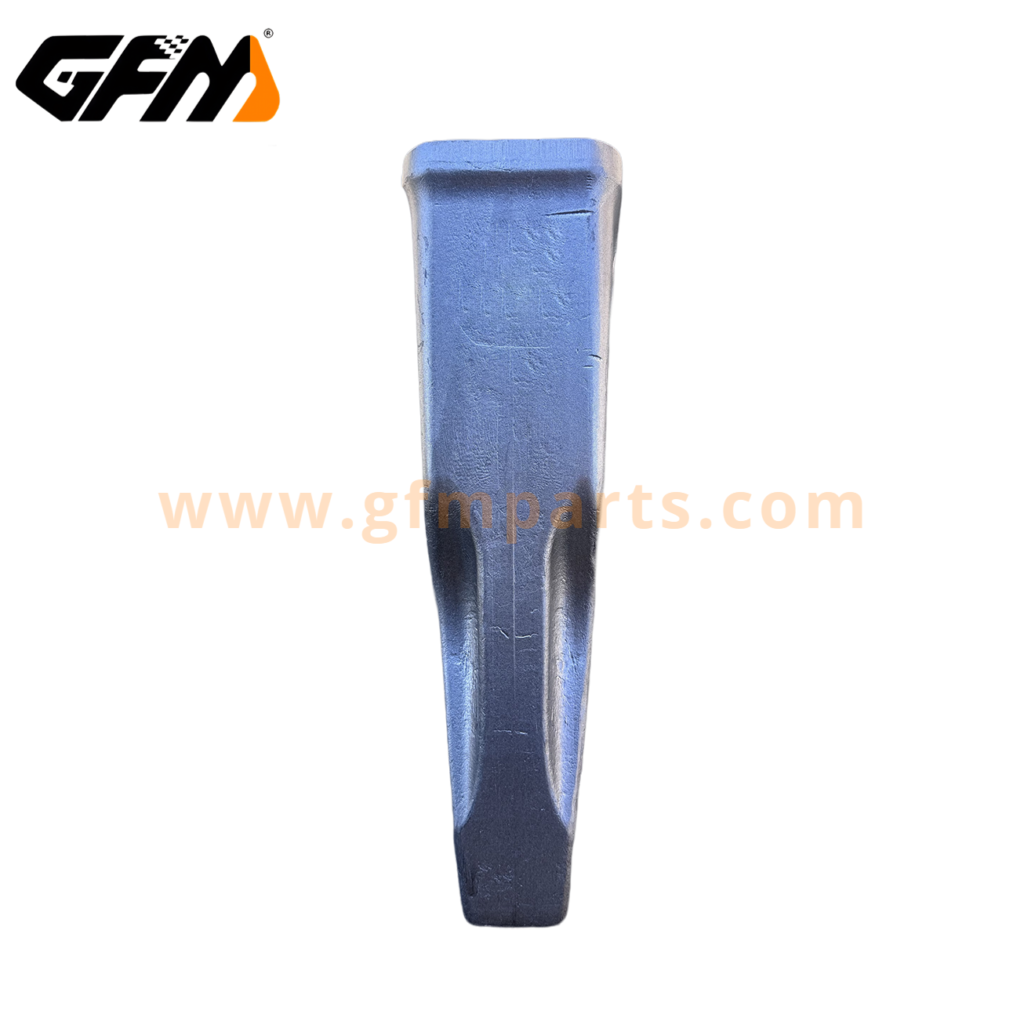
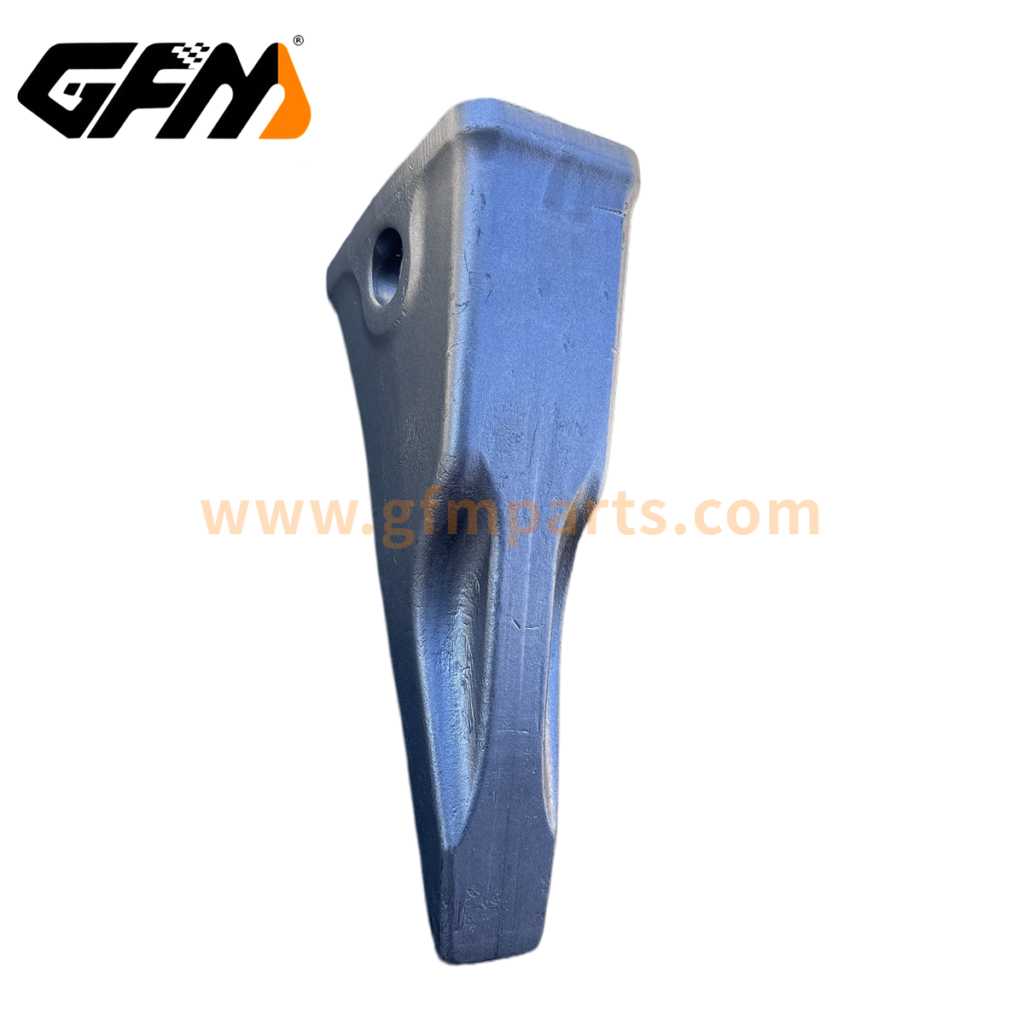
Preparation for replacing excavator bucket teeth: tools, environment and safety
Before starting to replace bucket teeth, preparation is crucial. A standardized replacement can not only avoid operating injuries, but also extend the service life of the new bucket teeth.
Required tools
- Sledgehammer and crowbar: used to remove old bucket teeth and install new bucket teeth.
- Chisel or steel chisel: used to knock out bucket tooth pins.
- Protective gloves and goggles: to ensure hand and eye safety during replacement.
- Lubricating oil or rust remover: used to help remove severely rusted pins.
Environmental requirements
Try to choose a dry and flat working environment to avoid slipping tools due to wet ground. To prevent accidents, it is recommended to fix the excavator in neutral and pull the handbrake. If necessary, put triangular wooden blocks on the tires or tracks.
Safety precautions
- Be sure to turn off the power and turn off the engine before operation to prevent misoperation of the bucket arm.
- Do not have multiple people operate on one side of the bucket tooth at the same time to prevent accidental injury to others.
- Stand firm when operating the sledgehammer to avoid falling due to the reaction force.
Detailed steps for replacing excavator teeth: complete step by step without pressure
Replacing the teeth is not complicated, but each step must be in place to ensure that the new teeth work firmly, safely and efficiently. The following is a more detailed step-by-step operation instruction, which is recommended to be carried out step by step in order:
Step 1: Confirm that the tooth model matches the accessories
Before replacement, you should carefully check the specific model of the existing teeth, including the shape, size, connection method (such as side plug-in, top plug-in), pin shaft size and tooth seat aperture. You can refer to the user manual, the model engraved on the old teeth, or consult GFM professionals for recommendations. Choosing the wrong model will make installation difficult and even affect safety.
Step 2: Clean the area around the old teeth
Use a wire brush, rag or high-pressure air gun to clean the sand, oil and rust at the joint between the teeth and the tooth seat, paying special attention to the inside of the lock pin hole. If there is severe rust, apply a small amount of rust remover and wait for a few minutes before cleaning to ensure smooth subsequent disassembly and assembly to avoid jamming or misoperation.
Step 3: Remove the old bucket teeth
Use a steel chisel or crowbar to knock the lock pin to loosen it and remove it. Some lock pin structures may have spring cards or nuts, which must be unlocked first. Then, hold both sides of the bucket teeth with both hands, shake them slightly or use a rubber hammer to gently knock the back to disengage them from the tooth seat. If they are stuck, you can increase the force appropriately or use a crowbar to pry them.
Step 4: Check whether the tooth seat and pin hole are damaged
After removing the old bucket teeth, the tooth seat should be fully inspected: observe whether there are deformations, cracks, excessive wear, etc., especially whether the inner wall of the lock pin hole is intact. If abnormalities are found, the tooth seat should be replaced or repaired in time to avoid affecting the fixing effect of the new bucket teeth.
Step 5: Install the new bucket teeth
Insert the new bucket teeth into the tooth seat hole in the original direction to ensure complete alignment. Then insert the new lock pin, which is usually pressed in or hammered. Use a hammer to properly strike the lock pin until it is fully inserted into the slot and confirm that it cannot slide out easily. If the bucket tooth is difficult to install, you can use a hammer to assist in pushing, but do not force it to avoid damaging the bucket tooth body or the tooth seat interface.
Step 6: Recheck the tightening status and angle
After installation, please stand in front of and to the side of the bucket tooth to observe whether it is in a vertical direction or tilted. Shake the bucket tooth and the pin shaft by hand to ensure that they are stable and not loose, and confirm again whether the lock pin is correctly in place.
Step 7: Test run inspection
Start the excavator and perform short-term no-load actions, such as light digging, rotating the bucket in place, swinging the arm, etc., to observe whether the bucket tooth shakes, falls off or makes abnormal sounds during actual actions. If any problems are found, stop the machine immediately for inspection and re-fix.
After completing the above steps, the bucket tooth replacement work is truly completed. Although the whole process is not complicated, details determine success or failure. Be sure to remain patient and strictly implement each link.
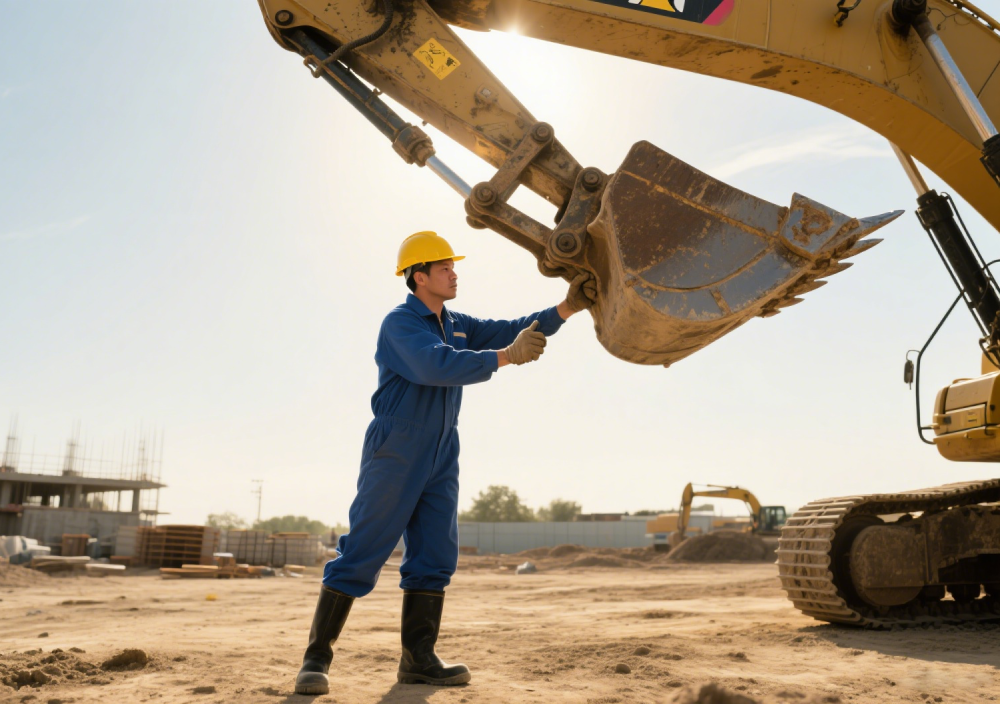
Common mistakes when replacing bucket teeth and how to avoid them
Even experienced operators may make some mistakes when replacing bucket teeth, which may affect the service life of the equipment.
Error 1: Ignoring model matching
Some users often use alternative models with the idea of ”similar size”, which will cause the tooth root and tooth seat to be loose and the risk of falling off during work.
Error 2: Continue to use the old pin shaft
The bucket tooth pin shaft is a key part for fixing the bucket teeth. The old pin shaft may have been deformed or worn after long-term use. Continuing to use it will reduce the overall structural stability.
Error 3: Incomplete installation
The bucket teeth are not completely knocked into the tooth seat. They may loosen under high-frequency vibration and fly out to injure people in serious cases.
Error 4: Not clean during installation
If the sand, rust or oil inside the tooth seat is not cleaned, it will make it difficult for the new bucket teeth to be in place or the lock pin cannot be inserted.
How to extend the service life of the new bucket teeth? Practical maintenance tips sharing
Replacing the bucket teeth is just the beginning. Scientific maintenance methods can truly maximize the efficiency of the bucket teeth and save long-term costs.
Reasonably control the excavation angle
When excavating, avoid vertical insertion and angled prying, and try to maintain a natural cutting angle of about 45°, which can not only improve efficiency but also reduce the wear frequency of bucket teeth.
Choose original quality bucket teeth
Although there are many imitation or low-priced bucket teeth on the market, these products usually have unstable steel composition and uneven heat treatment, which greatly shortens the service life. Choosing bucket teeth from regular manufacturers such as GFM is the basic guarantee for protecting equipment.
Regular inspection and tightening
It is recommended to check the tightening of bucket teeth and pins every 40 to 50 hours of work. If there is any looseness, deal with it in time to avoid losing the big picture because of the small.
Avoid working in abnormal environments
Avoid long-term work in acidic and alkaline mud, or long-term immersion in high-temperature asphalt. If it cannot be avoided, the bucket teeth should be cleaned and dried as soon as possible after work.
Lubrication and maintenance by season
Under low temperature conditions in winter, metal ductility is poor and bucket teeth are more likely to break. It is recommended to use special lubricants for maintenance at the joints; in summer, pay attention to surface heat dissipation and rust prevention.
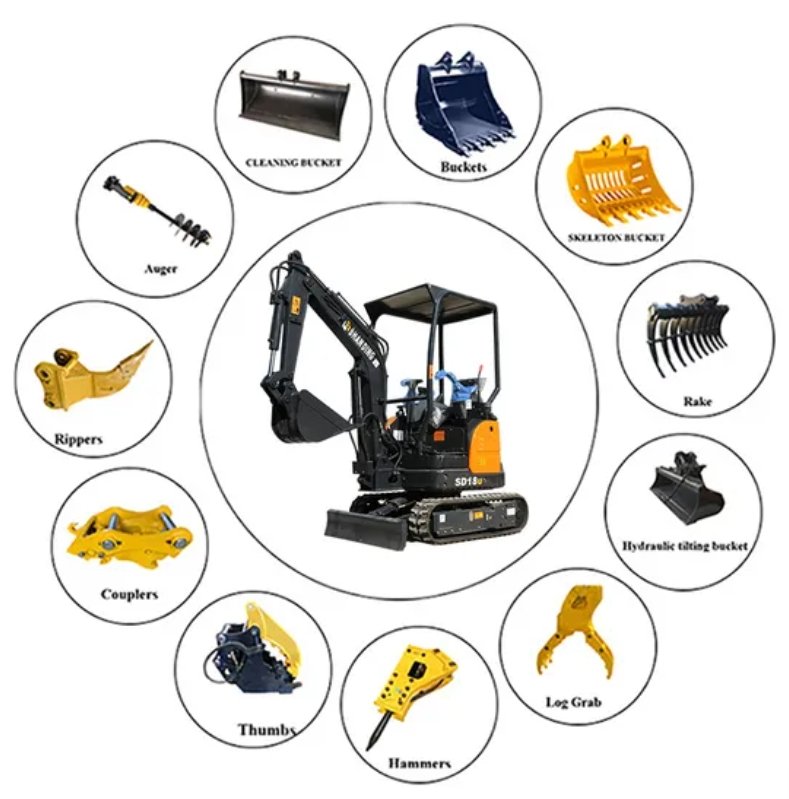
Why choose GFM excavator parts factory to replace your bucket teeth?
In the global excavator parts market, GFM has always won the trust of customers with high-quality and durable bucket teeth products. Choosing GFM is not just about choosing accessories, but also choosing a complete set of construction efficiency solutions.
Superior material and stable structure
GFM bucket teeth are forged with high-strength alloy steel and combined with high-frequency heat treatment technology to improve hardness and toughness while ensuring that they are not easy to break or fall off under harsh working conditions.
Precision manufacturing and high matching degree
GFM controls the size of each bucket tooth to 0.1mm to ensure perfect bite with the bucket tooth seat, easy installation, and safer use.
Support customization to meet special needs
Different soil types and construction environments have different requirements for bucket teeth. GFM can provide various types of bucket teeth such as rock type, mining type, general type, etc. according to the customer’s construction environment, and even supports customized drawing processing.
Years of service to global customers, rich experience
GFM has more than ten years of overseas export experience, and its products are exported to Southeast Asia, Africa, Europe and other regions, and are well received by customers. It can provide Chinese and English after-sales and technical guidance.
Strict quality control, quality traceability
Each batch of bucket teeth has an independent number and inspection report, and there are complete records from raw material procurement to factory inspection. Customers can rest assured to trace and review, which complies with the ISO standard system.
Hızlı ve ücretsiz bir teklif alın | E-posta: henry@gfmparts.com | Whatsapp: +86 17705953659 |
Although the bucket teeth are small, they are the direct output point of the excavator. Reasonable judgment of the wear state of the bucket teeth, use standard methods to replace the bucket teeth, and combine scientific maintenance habits can keep the excavation equipment in an efficient and stable working state.
If the replacement method is not standardized, it will reduce the operating efficiency at the least, and cause equipment damage at the worst, and even cause construction safety accidents. On the contrary, a standardized and meticulous replacement operation not only improves the construction efficiency, but also extends the overall life of the bucket teeth and tooth seats, and reduces maintenance costs.
In addition, choosing the right bucket tooth brand and supplier is also critical. As a trusted ekskavatör alt takım parçaları üreticisi in the industry, GFM not only provides high-quality, wear-resistant bucket tooth products, but also has a professional team to provide customers with technical guidance, after-sales support, and customized services to escort your every construction.
Whether you are an equipment operator, maintenance supervisor, or parts purchaser, you should pay attention to regular inspection and scientific replacement of bucket teeth. Only by paying attention to details and choosing the right products and methods can you truly achieve twice the result with half the effort and stable construction.
If you are looking for stable, durable, and professional excavator bucket tooth products, please contact our GFM team. We will wholeheartedly provide you with a one-stop solution to help you perform better on the construction site.
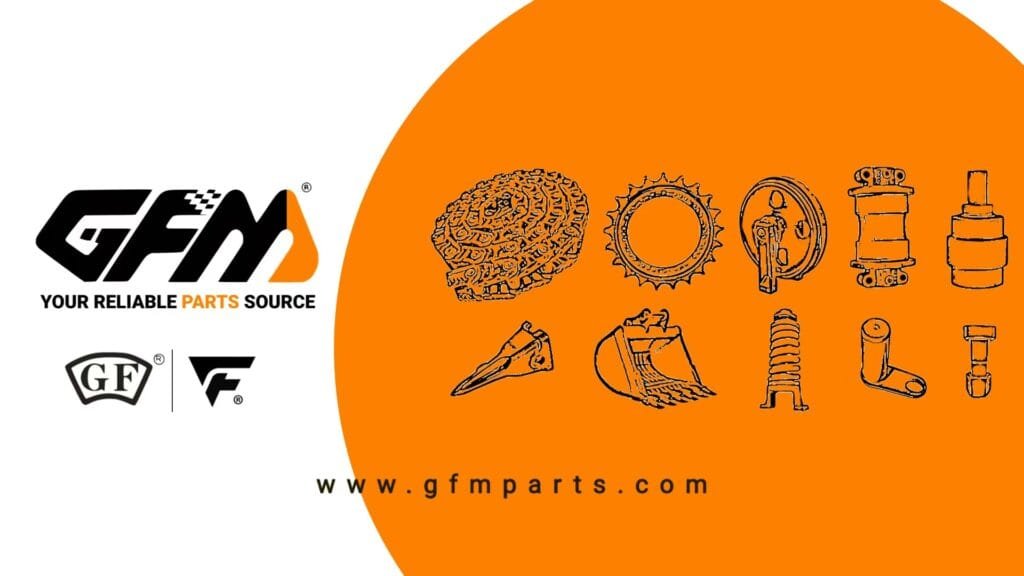