In the construction machinery industry, the operating performance of the excavator depends largely on the stability and durability of the chassis system. In the chassis, the chain is the core component that connects the drive wheel, the sprocket wheel and the track plate, and determines the stable walking, traction and load-bearing capacity of the whole machine. If the chain quality is not up to standard, it will not only directly affect the construction efficiency, but also easily cause early damage to the whole machine and increase the maintenance cost.
As the industry’s top excavator track chain manufacturers, GFM has formed a complete R&D, production, inspection and service system in excavator chain manufacturing with 14 years of manufacturing experience, and has become a long-term partner of many international construction machinery brands
Table of contents
- GFM: 14 years of focus on excavator chain manufacturing industry benchmark
- What is an excavator chain?
- Key factors that determine the quality of excavator chains: from materials to heat treatment
- Five major technical advantages of GFM chains, how to define “top manufacturing in the industry”
- Chain customization service guide: How to choose the right chain according to equipment and working conditions
- Application case: GFM chain’s outstanding performance in complex engineering environments
GFM: 14 years of focus on excavator chain manufacturing industry benchmark
GFM is a small and medium-sized processing plant focusing on crawler assemblies and chain track segments. With the continuous upgrading of technology and the unremitting pursuit of quality, GFM has gradually transformed from spare parts processing to the manufacturing of a complete set of chassis systems. It has now become a modern enterprise integrating casting, forging, heat treatment, CNC precision processing and whole chain assembly.
At present, GFM’s factory covers an area of more than 30,000 square meters, equipped with 12 automatic chain rail processing production lines and 3 heat treatment centers. The annual output of excavator chains exceeds 100,000, covering various chain rail models for small 5-ton to large 120-ton excavators, including international brand matching models such as Hitachi, Komatsu, Caterpillar, Volvo, SANY, Doosan, etc.
The company has passed the ISO9001 quality management system certification and obtained a number of national technical patents. GFM adheres to the concept of “technology-based enterprise, quality-oriented” and is committed to becoming a chain solution provider trusted by global customers.
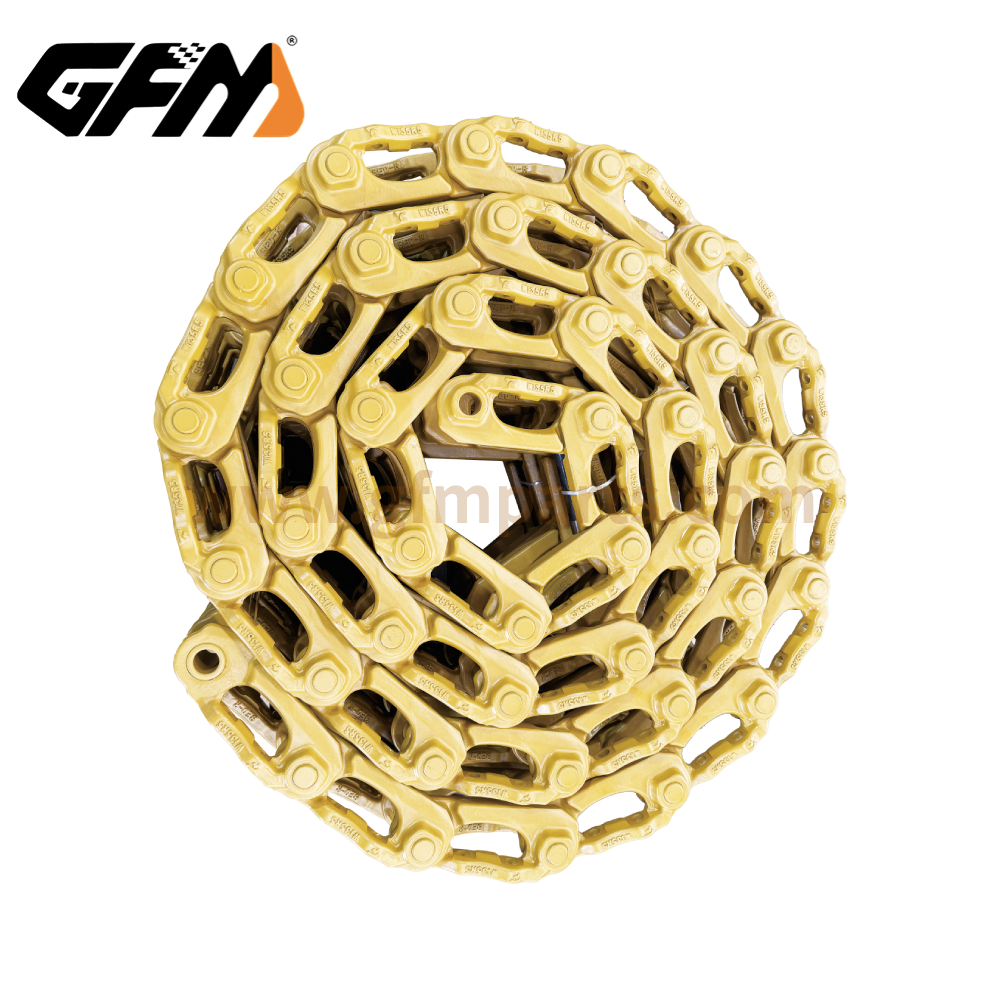
Are you looking for quality track link assy at the best price? You have come to the right place. We are committed to providing excellent products and offering the best value to our customers. Your satisfaction is our motivation. Send an email to henry@gfmparts.com now and our excavator undercarriage parts experts will be happy to serve you.
What is an excavator chain?
The excavator chain is one of the core transmission components of the crawler chassis system. It consists of multiple track links, pins, bushings and oil seals. The chain mainly plays the following roles:
- Load-bearing and transmission: Through cooperation with the track plate, drive wheel and guide wheel, the engine power is converted into traction, so that the whole machine can move forward, backward or turn.
- Impact buffering: Under uneven working conditions, the cooperation between the chain and the sprocket can effectively alleviate vibration and impact force and protect the chassis structure.
- Maintain track tension: A properly installed chain can always maintain a tensioned state to prevent the chain from slipping or derailing.
Chains are generally classified by pitch, and different tonnage models use different chain pitches. For example, small machines generally use chains with a pitch of 135mm, while medium and large models can reach 190mm or more. At the same time, different working conditions such as rock sites, wetlands, mining, etc., also have different requirements for the wear resistance and structural strength of the chain.
Key factors that determine the quality of excavator chains: from materials to heat treatment
In the chain manufacturing process, there are several key processes that directly affect the service life and performance of the product:
Selection of high-strength alloy steel raw materials
GFM uses high-strength alloy structural steels such as 20Mn, 40MnB and 35CrMo for the chain track segments. Through multiple steel heat treatments and composition control, the chain track segments are guaranteed to have good toughness and fatigue resistance.
Heat treatment process control
The pins and bushings of the chain need to have extremely high wear resistance and impact resistance. GFM uses multi-frequency induction quenching + tempering process to form a uniform martensitic structure, and the depth of the hardened layer is tested piece by piece to ensure that each chain can withstand high load conditions.
High-precision CNC machining and assembly
All mating surfaces are precision machined by CNC lathes, and the assembly tolerance is controlled within ±0.02mm to ensure that the spacing between chain segments is consistent and the meshing is smooth. In the assembly process, GFM uses an automatic press-fit and locking system to improve the stability and reliability of the entire chain.
Sealing and lubrication technology
In order to reduce chain wear and extend the service life, GFM chains widely use lubricated sealed chains (Sealed & Lubricated Track), which effectively reduce the metal friction between the pin and the bushing and extend the life by more than 30%.
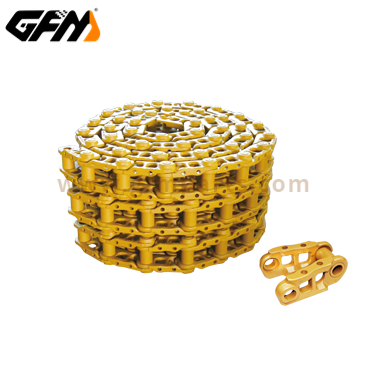
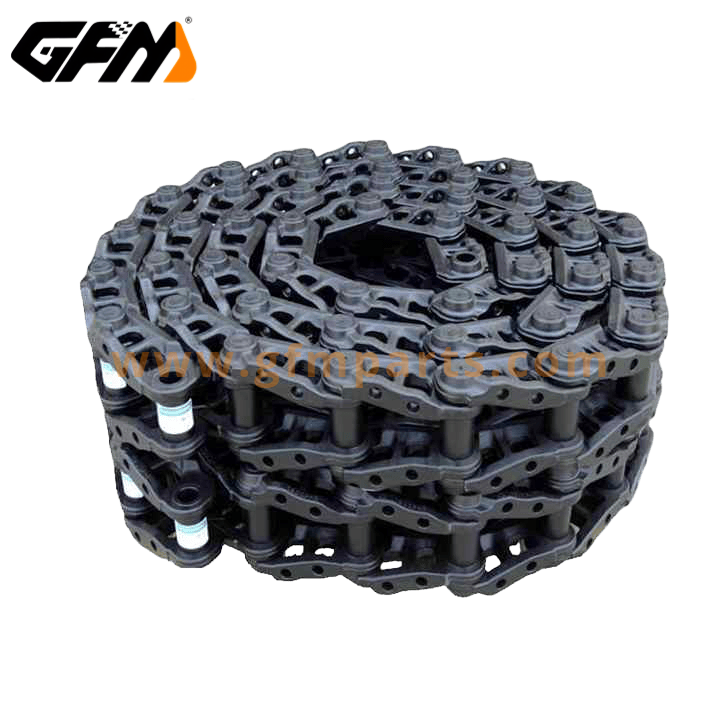
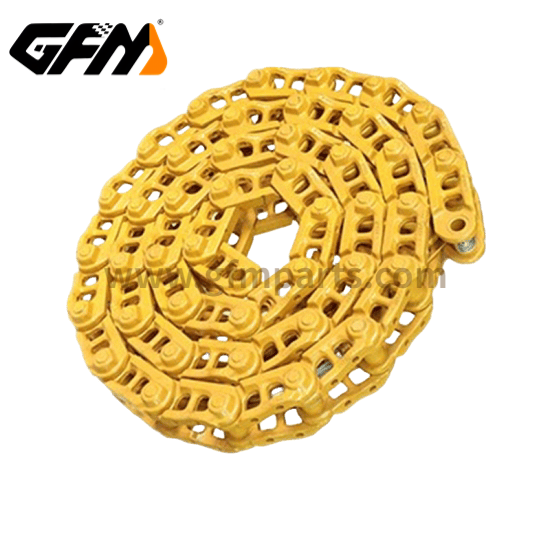
Five major technical advantages of GFM chains, how to define “top manufacturing in the industry”
Full specification coverage: From PC35 small excavators to PC1250 large mining equipment, GFM provides more than 60 specifications and models, suitable for mainstream brand hosts.
Ultra-long wear life: GFM high-end series chains have been tested by a third party, and the wear rate is less than 0.2mm after running for 3000 hours in simulated rock conditions.
Customized adaptation service: Support processing according to drawings and samples, and can be customized according to the special pitch, number of sections, chain track width, etc. provided by customers, with short delivery time and high adaptability.
Multiple testing guarantees: Including magnetic particle flaw detection, hardness test, tensile test, etc., to ensure that the factory chain is 100% qualified.
International customer cooperation certification: OEM support has been provided to more than 60 agents and complete machine factories in the Middle East, Southeast Asia, Europe and other regions, with excellent reputation.
Chain customization service guide: How to choose the right chain according to equipment and working conditions
When choosing a chain, you cannot blindly pursue “universal matching”, but must customize it in combination with equipment parameters and usage environment. The following are several key points that GFM often considers when providing customization for customers:
Equipment tonnage and brand model: For example, Komatsu PC200 vs CAT 320, the chain pitch and number of sections are different.
Working environment: Rocks, sand, wetlands, quarries, etc. have different requirements for the wear resistance of chain rail sections and pin sleeves.
Construction cycle and strength: High-frequency quenching, sealed and lubricated chains are required for high-intensity continuous operations.
Customer budget and life cycle expectations: GFM provides three product lines: economical, standard and enhanced, for customers with different budgets to choose from.
GFM engineers will also provide three-view drawings and assembly suggestions before customization to ensure seamless chain assembly and risk-free on-site replacement.
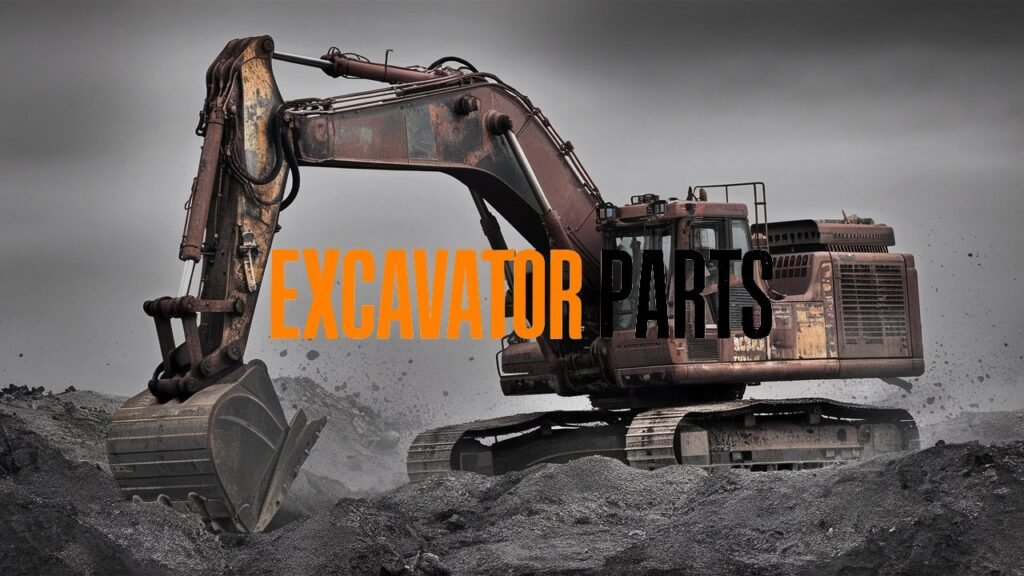
Application case: GFM chain’s outstanding performance in complex engineering environments
Case 1: Sichuan mining project
- Customer equipment: multiple PC360 excavators
- Problem: The original chain was severely worn in less than half a year in gravel mountain operations.
- Solution: GFM recommends the use of reinforced chain track + high carbon bushing + sealed lubricated pin combination chain.
- Effect: The entire chain has maintained good meshing after running for more than 2,400 hours, and the customer continues to purchase it.
Case 2: Indonesian wetland civil engineering project
- Customer equipment: CAT 320D
- Problem: The construction site is soft and slippery, and ordinary chains are prone to derailment.
- Solution: Customized wide chain track + anti-mud structure design
- Effect: Significantly improve track stability, and the probability of derailment is reduced by more than 80%.
Hızlı ve ücretsiz bir teklif alın | E-posta: henry@gfmparts.com | Whatsapp: +86 17705953659 |
In the fiercely competitive construction machinery parts market, what can really win the trust of customers is solid manufacturing skills, innovative technical capabilities and consistent service attitude. GFM has become a stable supplier of many global host brands and construction units with these advantages. In the future, GFM will continue to promote chain manufacturing towards higher durability, stronger adaptability and lower maintenance costs, empowering every construction builder to create more efficient and reliable construction chassis solutions.
If you are looking for a stable, cost-effective and customizable excavator chain supporting solution, you may consider GFM and let the professional chain manufacturing experience escort your equipment.
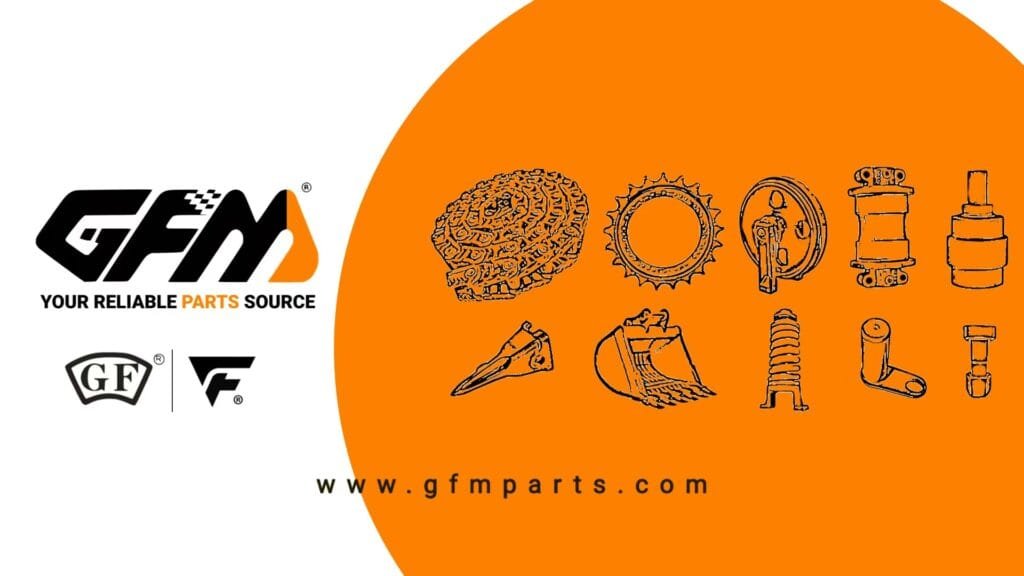