In the field of engineering machinery, excavators are important equipment for heavy-duty operations. Their core technology and structural design directly determine the operating efficiency and safety. As an important support system for the whole machine, the excavator undercarriage not only bears the weight of the machine, but also directly affects the stability, durability and adaptability of the equipment in complex environments.
Overview of excavator undercarriage parts
The excavator undercarriage is the “cornerstone” of the whole machine, mainly composed of the following key parts:
- Tracks or wheels: provide equipment with walking and stable support in various terrains;
- Shock absorption system: effectively absorbs vibration and impact during work and protects the machine structure;
- Transmission device: transmits engine power to the undercarriage to achieve smooth walking;
- Hydraulic system: cooperates with the operating system to ensure the coordinated operation of various parts;
- Structural parts and connectors: constitute the overall skeleton of the undercarriage, disperse the load, and ensure stability during high-intensity operations.
Each component must meet the requirements of high load, high vibration, wear resistance, etc. when designing, so as to ensure that the equipment can operate efficiently and safely even in extreme working environments.
Mechanical analysis of excavator undercarriage parts
Force analysis
During operation, the excavator will be subjected to vertical loads, lateral forces and vibration shocks at the same time. Through reasonable mechanical design, these complex stresses can be evenly distributed on the various parts of the undercarriage, reducing local stress concentration, thereby effectively preventing metal fatigue and structural damage.
Material selection and structural optimization
The use of high-strength alloy steel or composite materials can greatly improve the undercarriage’s bending, torsion and impact resistance. In modern engineering design, finite element analysis (FEA) is used to simulate and test the undercarriage to further optimize the structural design and improve overall durability and stability.
Power transmission and energy absorption
High-quality undercarriage design requires that while transmitting engine power, it can also fully absorb the energy impact generated during operation. This not only protects other key parts, but also ensures a smooth and precise operation process, thereby extending the service life of the entire machine.
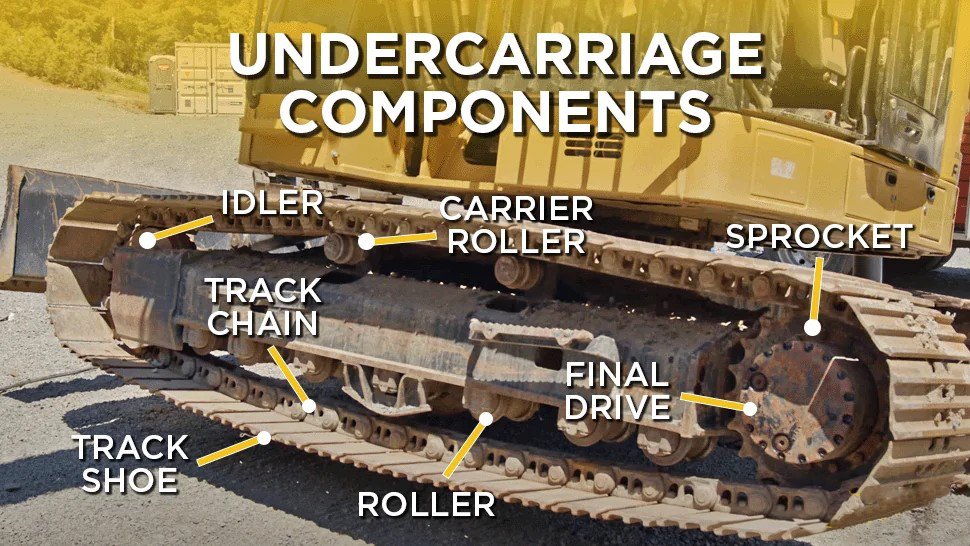
Different types of excavator undercarriage
According to different operating environments and usage requirements, excavator undercarriage are mainly divided into the following categories:
Track undercarriage
- Applicable scenarios: muddy, soft, and rugged construction site environments.
- Advantages: large ground contact area, good pressure dispersion effect, excellent passability and stability.
- Disadvantages: complex structure, high maintenance difficulty, and parts are more prone to wear.
Wheeled undercarriage
- Applicable scenarios: urban roads, flat ground and on-site operations.
- Advantages: flexible steering, fast speed, and relatively simple maintenance.
- Disadvantages: poor stability on uneven ground and relatively limited carrying capacity.
Hybrid undercarriage
- Features: Some equipment adopts a combination of crawler and wheel design, striving to achieve a balance between stability and maneuverability.
- Başvuru: Suitable for a variety of working environments, which can meet the requirements of urban operations and cope with some complex terrains.
Comparison between excavator undercarriage and mini crawler loader undercarriage
Although both excavators and small crawler loaders use crawler undercarriage, there are obvious differences between the two in design concepts and application scenarios:
- Structural design: Excavator undercarriage usually pays more attention to carrying capacity and durability, and is suitable for large and heavy-duty operations; while small loaders focus on maneuverability and flexibility.
- Working environment: Excavators often operate in complex and harsh working conditions, and have higher requirements for the undercarriage; small loaders are usually used in relatively mild environments.
Difference between Track undercarriage and wheeled undercarriage
Applicable terrain
- Track undercarriage: Designed to cope with complex terrain, such as muddy, gravel roads and uneven construction sites, with a large ground contact area, it can effectively reduce ground pressure and reduce the risk of getting stuck.
- Wheeled undercarriage: More suitable for paved roads or urban environments, providing higher driving speeds and handling flexibility, but not as good as crawler undercarriage on harsh terrain.
Stability and load capacity
- Track undercarriage: Due to its large ground contact area, it has higher stability and load capacity, and is suitable for heavy equipment.
- Wheeled undercarriage: Although it is more flexible to operate, it has relatively poor stability under high load and complex terrain conditions.
Maintenance and repair costs
- Tracked undercarriage: The structure is relatively complex, parts are easy to wear, and the repair and replacement costs are high.
- Wheeled undercarriage: The structure is relatively simple, the maintenance cycle is long and the cost is low, which is more suitable for daily maintenance and simple repairs.
The importance of regular maintenance
Extend the service life of equipment
Regular inspection and maintenance of the excavator undercarriage can timely detect potential faults and prevent small problems from turning into major faults, thereby greatly extending the overall service life of the equipment.
Ensure operational safety
Regular inspection of key parts such as tracks, shock absorbers, transmission systems, etc. ensures that the equipment can still maintain stable operation under high load and high vibration conditions, reducing the incidence of safety accidents.
Reduce maintenance costs
Preventive maintenance can deal with problems as soon as they occur, avoiding equipment downtime due to sudden failures. In the long run, it can effectively control maintenance costs and reduce unnecessary economic losses.
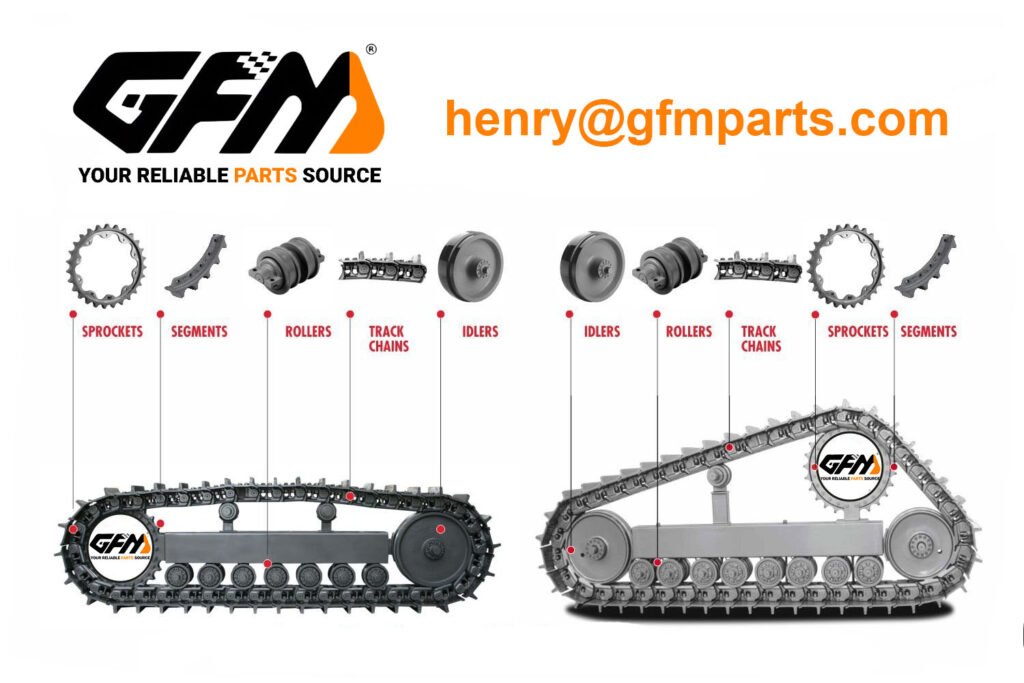
Undercarriage life and durability
Service life
High-quality undercarriage can reach tens of thousands of hours after scientific design and strict maintenance. The key lies in the selection of materials, the rationality of structural design and the implementation of daily maintenance work.
Measures to improve durability
- Material upgrade: Use high-strength wear-resistant materials and advanced anti-corrosion technology.
- Structural optimization: Through refined design and finite element analysis, reasonably distribute the stress points and reduce stress concentration.
- Regular inspection: Regularly inspect the hydraulic system, shock absorbers and other vulnerable parts to ensure timely replacement or repair.
The role of after-sales undercarriage parts
Replacement and upgrade
With the long-term operation of the equipment, some undercarriage parts will inevitably wear or age. High-quality after-sales parts can ensure that the replaced parts are consistent with the original factory standards and restore the best performance of the equipment.
Quality assurance
After-sales parts provided by regular manufacturers are strictly tested and meet international standards, which is crucial to ensure the overall safety and stability of the equipment.
Cost control
By replacing the worn parts in time, the chain reaction caused by local failures can be avoided, the overall maintenance costs and downtime can be reduced, and long-term cost control can be achieved.
How to choose the right undercarriage parts for your equipment
Choosing the right undercarriage parts can not only improve equipment performance, but also extend the service life of the whole machine. Here are a few key suggestions:
Understand the working environment and needs
- Analyze the main working scenarios of the equipment: indoor operations, harsh outdoor environments or variable working conditions.
- Choose the corresponding undercarriage type (such as crawler, wheeled or hybrid) according to the environment.
Focus on product quality and brand reputation
- Choose a brand that has been verified by the market and has good user reviews.
- Ensure that the product meets international or industry standards and guarantees long-term durability.
Regular inspection and professional consultation
- Inspect the undercarriage regularly to keep abreast of the status of the parts.
- Consult the manufacturer or professional technicians to develop maintenance and replacement plans based on the use of the equipment.
Perform a cost-effectiveness analysis
- Comprehensively consider the initial purchase cost, subsequent maintenance costs and service life.
- Choose products that meet both technical requirements and have economic benefits.
Hızlı ve ücretsiz bir teklif alın | E-posta: henry@gfmparts.com | Whatsapp: +86 17705953659 |
As the key basis for the operation of the whole machine, the mechanical design, structural optimization and regular maintenance strategy of the excavator undercarriage parts have a direct impact on the performance, safety and life of the equipment. In the process of selecting and maintaining construction machinery, paying attention to and investing in high-quality undercarriage parts, combined with a scientific maintenance plan, can not only improve operating efficiency, but also ensure the stable operation of the equipment under complex working conditions.
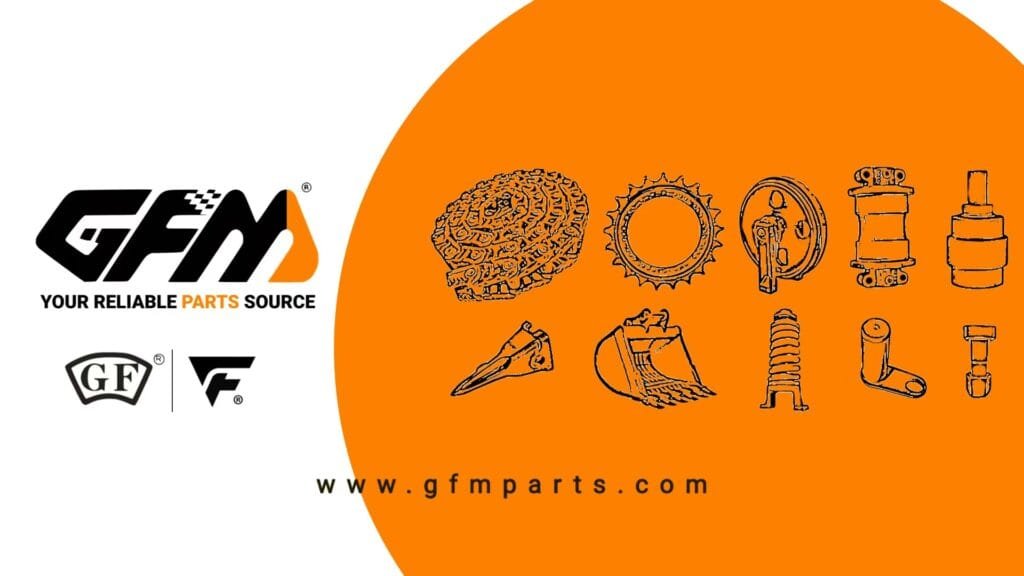