Excavators are indispensable heavy machinery equipment in modern construction and engineering, and track rollers, as an important part of the excavator undercarriage, bear important load-bearing and supporting functions. The normal operation of excavator track rollers directly affects the stability, service life and construction efficiency of the excavator. However, with long-term use or improper maintenance, various problems may also occur in the track rollers, affecting the overall performance of the equipment.
Main functions of excavator track rollers
As part of the track system, the main functions of excavator bottom rollers:
- Support track: The track rollers bear the weight of the excavator and ensure that the track remains in place to avoid deviation.
- Shock absorption: It can absorb a certain amount of impact during operation and reduce damage to other components.
- Provide stability: The track rollers help ensure that the excavator travels smoothly, especially on uneven ground.
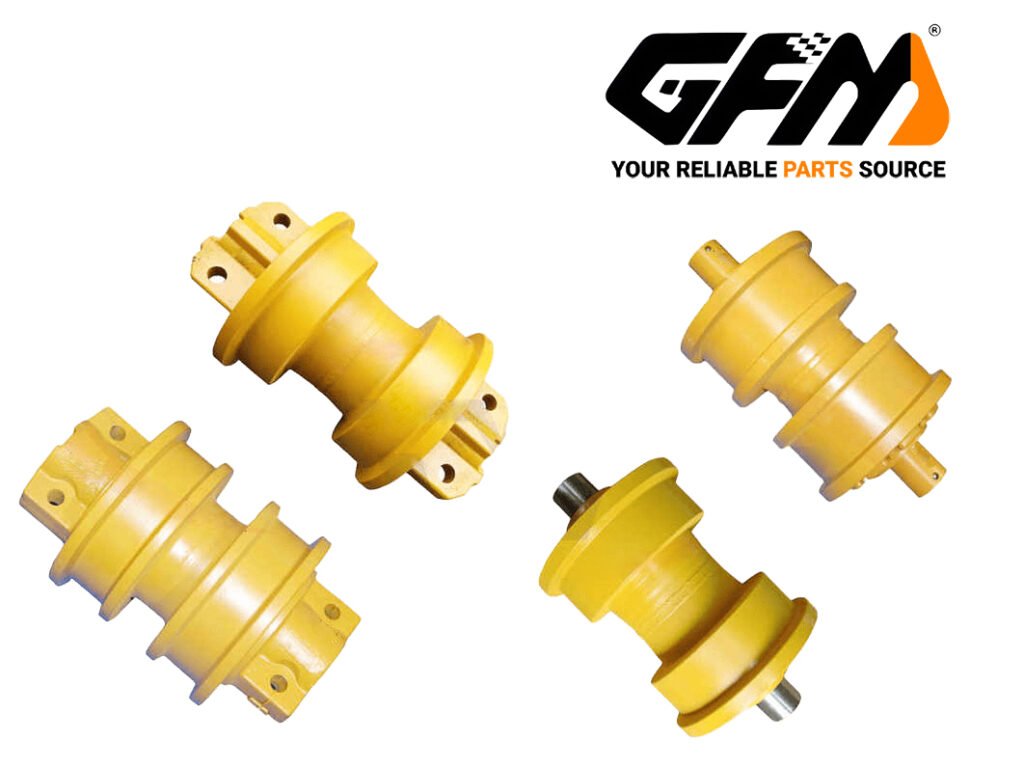
Common problems of excavator track rollers
Track rollers wear too fast
Reasons:
- Long-term overload work or frequent high-load operations.
- Uneven ground or hard working environment (such as stone yards, mining areas, etc.) causes excessive friction on the track rollers.
- Lack of regular lubrication and maintenance leads to increased wear.
Solution:
- Check the wear of the rollers regularly, especially after heavy load or high-frequency use, and replace the rollers with severe wear in time.
- When the working environment is harsh, the appropriate working mode should be selected to avoid excessive pressure on the rollers.
- Lubricate and maintain the rollers regularly to ensure that the roller components are in good lubrication condition.
Abnormal noise from rollers
Reason:
- Looseness or friction between the rollers and the tracks and crawlers causes abnormal sounds.
- Lack of lubrication causes friction between the rollers and the contact parts to produce noise.
- Aging, cracks or deformation of components affect the normal operation of the rollers.
Solution:
- Check the connection between the rollers and the crawlers and tracks to ensure that there is no looseness or excessive wear.
- Replace worn or aged parts to avoid long-term use of damaged rollers.
- Clean and add an appropriate amount of lubricating oil in time to reduce friction and prevent noise.
Roller stuck or stuck
Reason:
- Due to long-term lack of maintenance, impurities such as oil, sand, etc. appear inside the roller, causing the parts to get stuck.
- The bearing of the axle or roller is damaged or aged, making it difficult to rotate.
- Due to excessive load, the pressure on the roller exceeds the design allowable value.
Solution:
- Clean the roller regularly, especially in muddy or sandy construction sites.
- Check the lubrication of the bearings and axles, and replace aged or damaged parts when necessary.
- If the roller is stuck for a long time, consider reducing the workload or optimizing the operation method.
Roller oil leakage
Reason:
- The seal ring is aged, causing oil leakage.
- The seal between the axle and the roller is not tight, causing oil leakage.
Solution:
- Check the sealing parts of the roller regularly and replace the aged seal ring in time.
- Replace the damaged roller to ensure that the sealing performance returns to normal.
- Use high-quality lubricating oil to avoid premature aging of seals caused by low-quality oil.
Roller deformation or damage
Reason:
- Long-term high-intensity work causes deformation or severe wear of the rollers.
- The excavator encounters obstacles during work, and the rollers are hit or unevenly loaded.
- Improper installation or use of unsuitable roller models causes damage to the rollers.
Solution:
- When encountering obstacles, be careful to avoid severe impact on the rollers.
- Make sure the roller model is correct and meets the equipment specifications.
- Replace damaged rollers in time to avoid causing greater damage to other components.
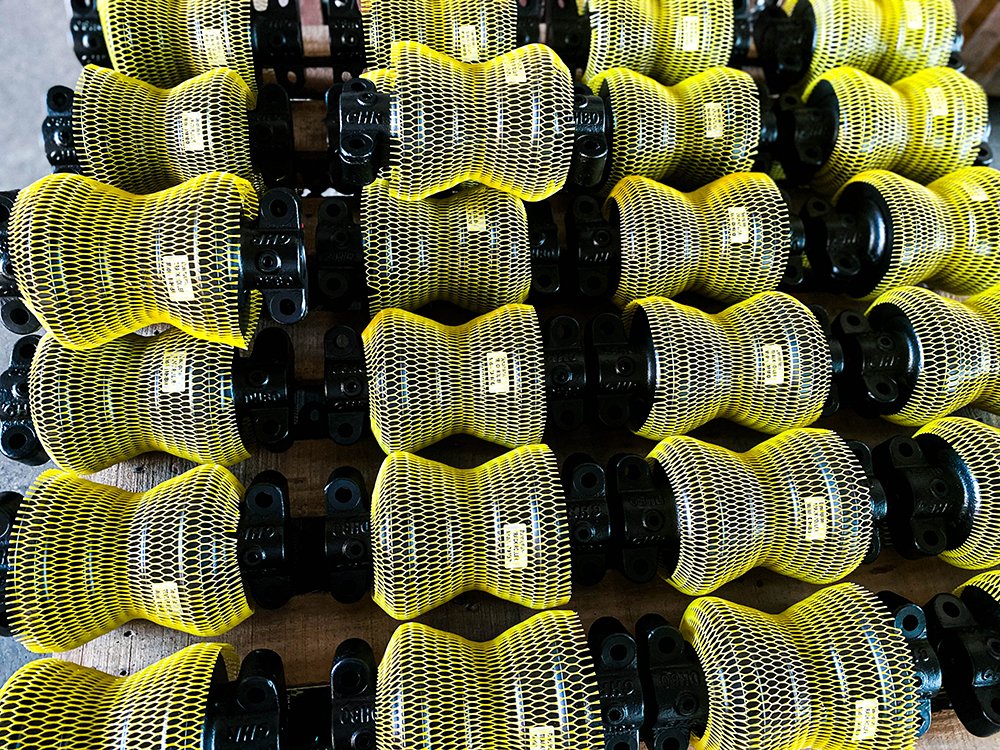
Analysis of common problems of rollers of excavators of different brands
Caterpillar excavator
The rollers of Caterpillar excavators perform well under high loads and harsh environments, but they are also prone to oil seal aging problems due to long-term use. Since Caterpillar excavators often face diverse geological environments during construction, the lubrication of rollers and the maintenance of seals are particularly important.
Solution:
- In the routine maintenance of Caterpillar excavators, be sure to check the lubricating oil and seals of the rollers.
- Clean and lubricate regularly, especially after high-load operations.
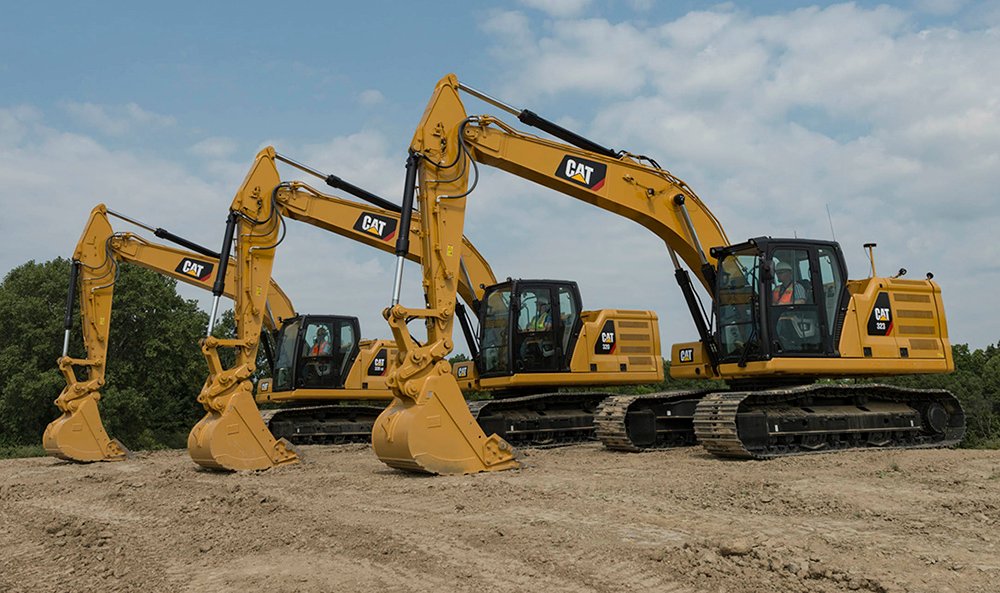
Komatsu excavator
Komatsu excavators are prone to track wheel jams in special environments such as mud and sand, especially in places with high humidity and a lot of mud and sand. Cleaning and lubricating the track wheels are the key to solving such problems.
Solution:
- In harsh working environments, increase the frequency of cleaning the track wheels to avoid accumulation of impurities.
- Use suitable lubricants to reduce jamming.
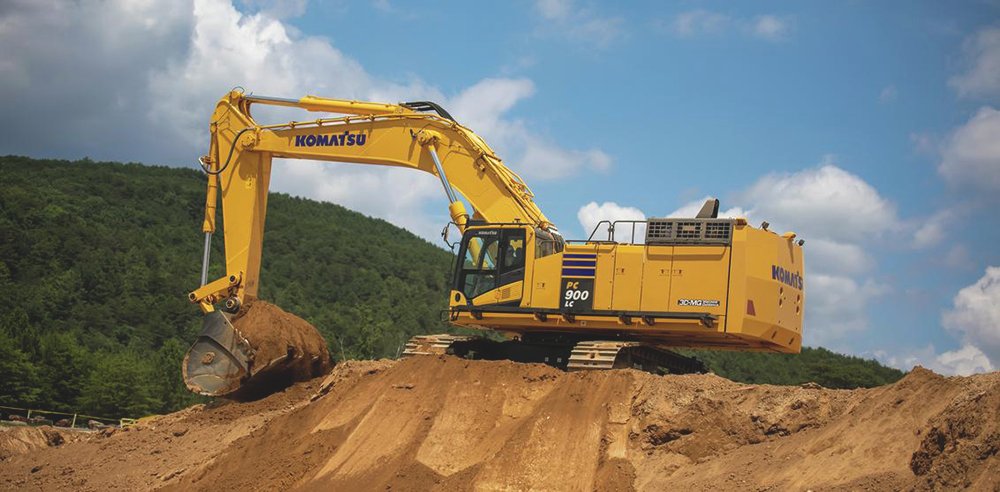
Hitachi excavator
The track wheels of Hitachi excavators often wear out too quickly after long-term high-intensity operations, especially in heavy-load operations. It should be noted that the material of Hitachi track wheels is relatively strong, but if not used and maintained properly, they are also prone to excessive wear.
Solution:
- For high-load operations, choose the appropriate operation method and avoid overload operations.
- Check the track wheels regularly, especially after heavy-load operations.
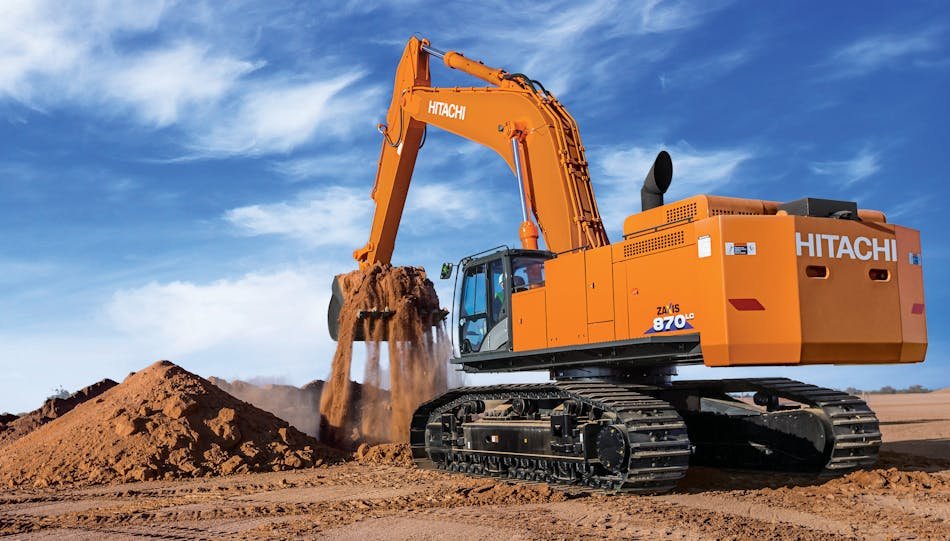
Hyundai excavator
Hyundai excavators are ideal for use on relatively flat ground, but deformation and damage of the track rollers are common in rugged or harsh terrain. Especially in uneven construction environments, the track rollers are under greater pressure.
Solution:
- When working in complex terrain, be more careful to avoid severe vibration or impact.
- Select track rollers with higher quality and more durable design for replacement.
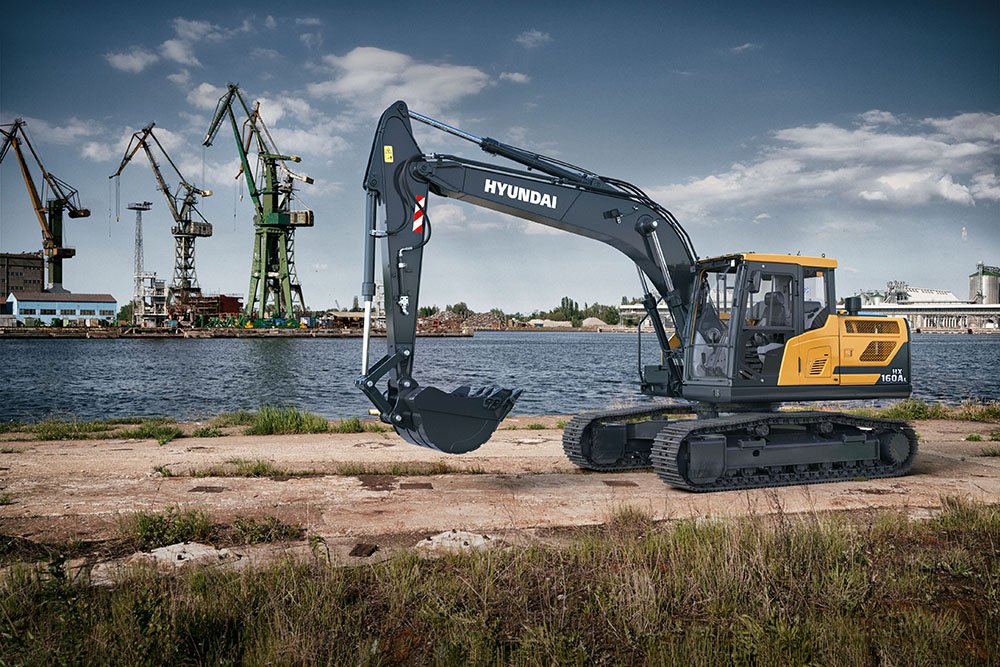
Preventive measures
- Regular inspection and maintenance: Check the track rollers regularly to find and solve problems in time to avoid small problems from turning into major failures.
- Maintain a good working environment: Try to avoid working in hard or obstacle-filled environments to reduce the risk of excessive impact on the track rollers.
- Reasonable operation: Avoid overload operation and ensure that the pressure on the track rollers is within the design range.
- Choose suitable accessories: Choose suitable track rollers for replacement according to the working environment and use requirements of the equipment.
Hızlı ve ücretsiz bir teklif alın | E-posta: henry@gfmparts.com | Whatsapp: +86 17705953659 |
Excavator track rollers are prone to various problems in long-term high-load operations, and reasonable maintenance and care can effectively extend their service life and ensure the normal operation of the excavator. I hope this article can help excavator users better understand the common problems, solutions and preventive measures of supporting wheels, and provide guidance to ensure the stability and efficiency of the equipment.
If you have more questions or need more in-depth equipment maintenance guidance, please contact us, professional technical support will help you!
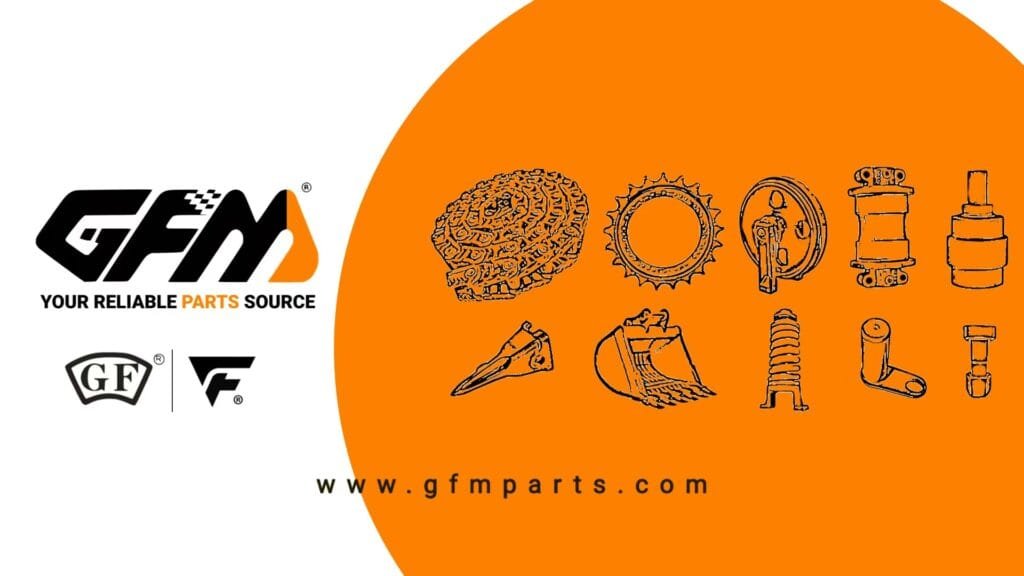