In the chassis system of excavators and bulldozers, track rollers, carrier rollers and idler wheels are indispensable and important components. They not only determine the operating efficiency of the equipment, but also directly affect the service life and overall performance.
What are track rollers, carrier rollers and idler wheels
Track rollers:
Track rollers are rollers installed under the track, mainly used to support the weight of the equipment and distribute it evenly to the track.
Carrier rollers:
The drag chain rollers are located above the track and are responsible for supporting the upper part of the track to prevent it from loosening and ensure that the track can run smoothly.
Idler wheels:
Idler wheels are usually located at both ends of the track. Their main function is to guide the running direction of the track and keep the track taut.
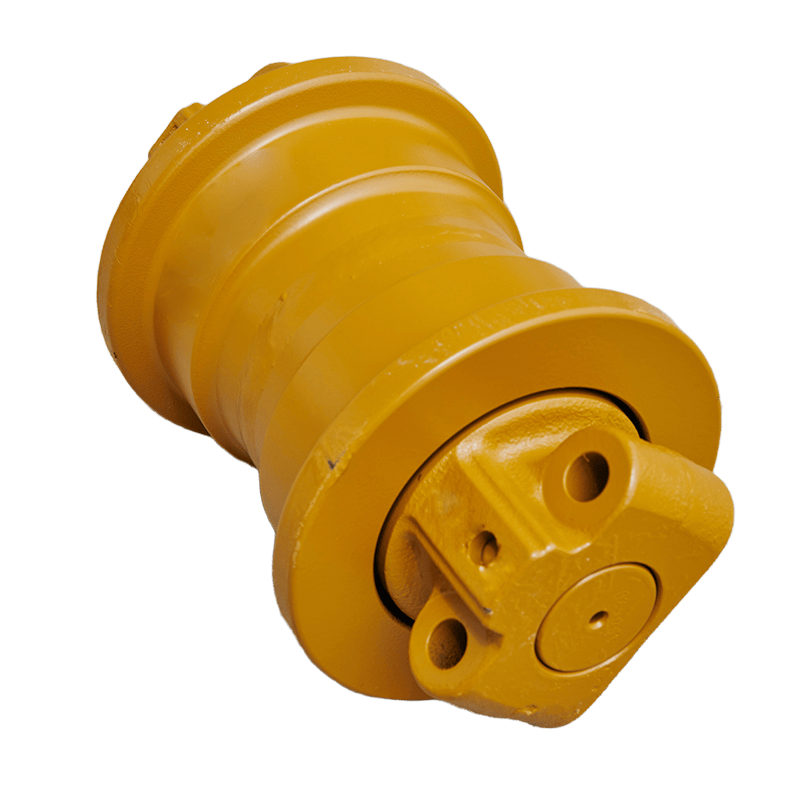
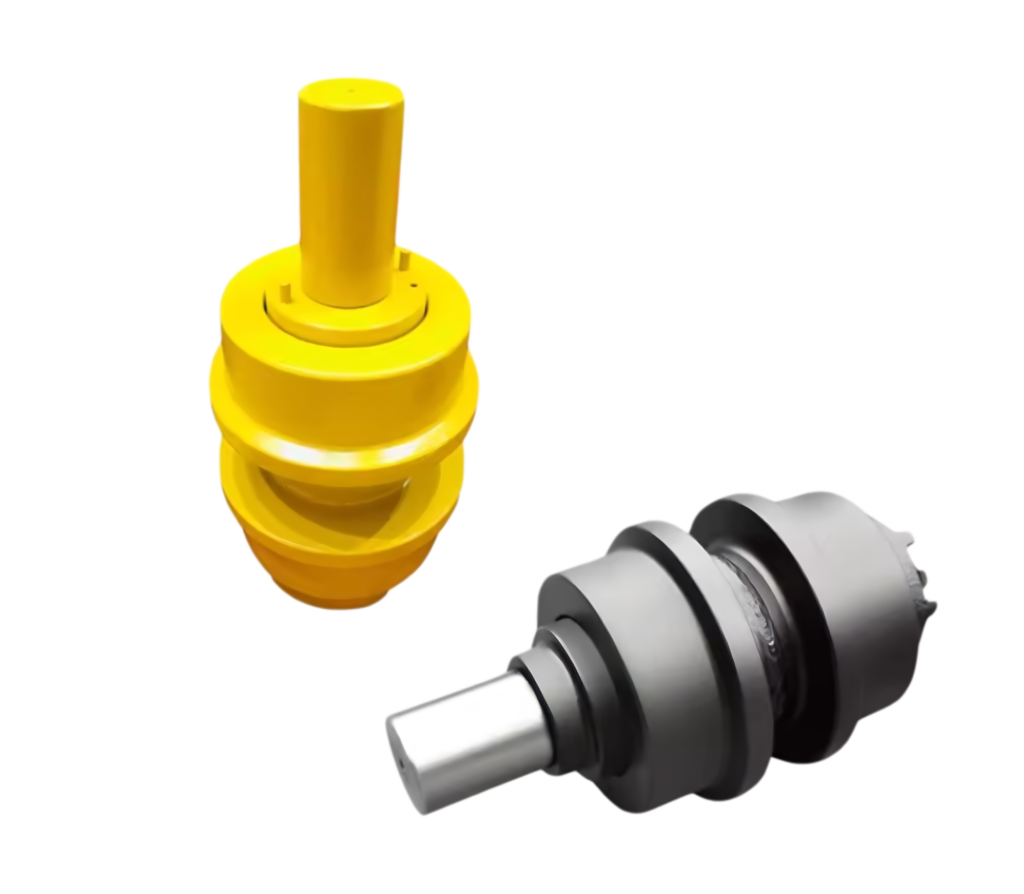
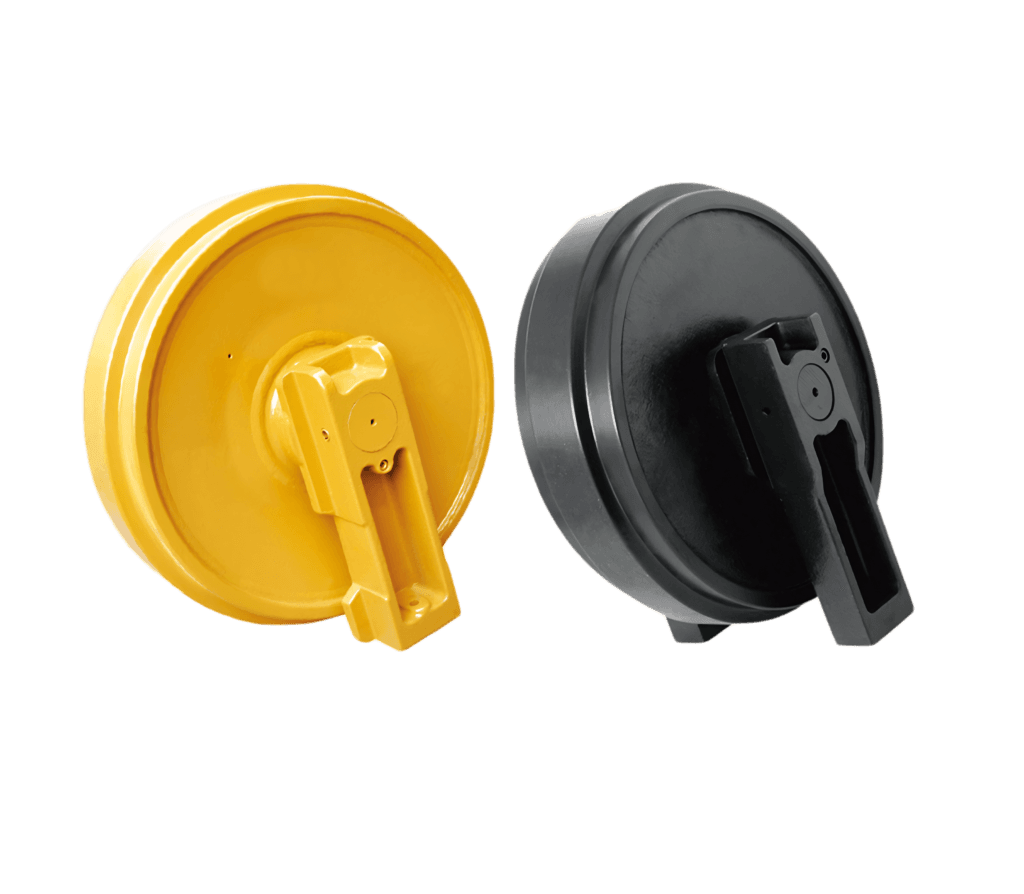
Function and working principle
Track rollers
The track rollers are in direct contact with the track to evenly distribute the weight of the equipment to the ground, ensuring that the equipment remains stable in complex terrain. In addition, the roller also acts as a shock absorber to reduce the impact force between the track and the ground.
Carrier rollers
The carrier roller helps the track maintain good tension and shape. It supports the upper part of the track and reduces the swing of the track, thereby improving the running stability and efficiency of the equipment.
Idler wheel
The idler wheel adjusts the track tension through a tensioning spring or hydraulic device to ensure that the track does not derail during operation. It meshes with the gear of the track to maintain the linearity of operation.
The connection and difference between rollers, carrier rollers and idler wheels
Rollers, carrier rollers and idler wheels are important components of the chassis system of crawler equipment. They are closely related in function, but each has different tasks.
The roller is mainly located under the track and in direct contact with the track. It is used to carry most of the weight of the equipment, evenly distribute the pressure to the ground, and play a shock absorbing role. This enables the equipment to maintain stability on rugged terrain and is a core component of the equipment’s load-bearing and stability performance.
The carrier roller is installed above the track, and its main responsibility is to support the upper part of the track to prevent the track from loosening. By maintaining the tension of the track, the drag sprocket ensures that the track can be in smooth contact with the ground and reduce the vibration and deviation of the equipment during operation. Although it does not directly bear weight like the supporting wheels, it is an important guarantee for the smooth operation of the track system.
The idler wheel is usually located at both ends of the track, and its function is mainly reflected in the guidance of the running direction of the track and the adjustment of the tension. The guide wheel engages with the track to maintain the linearity of the track during operation and prevent the track from derailing. At the same time, it can also adjust the tightness of the track through the tensioning device to extend the service life of the track and other components.
In general, the three have their own responsibilities in the track system. The supporting rollers are responsible for bearing weight, the drag sprocket ensures the stability of the track and the idler wheels adjust the running direction and tension of the track. They work together to ensure that the equipment can operate efficiently under various complex working conditions.
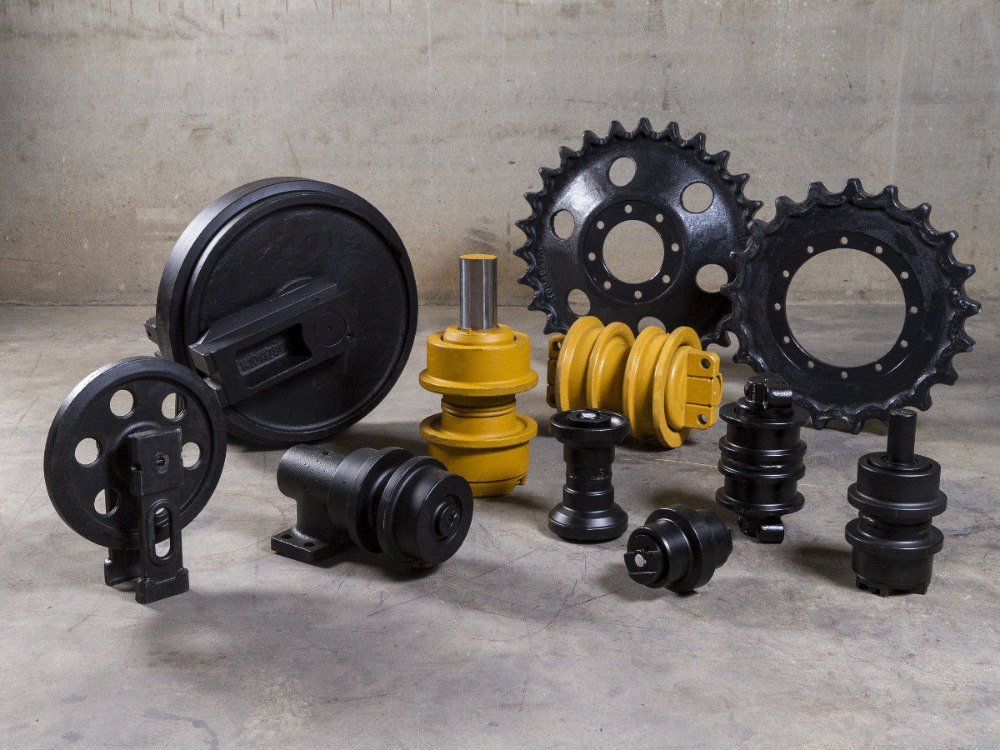
Production process
Material selection:
Use high-strength alloy steel to ensure wear resistance and impact resistance.
Forging and casting:
Forming through precision forging or casting process to ensure the structural strength of the parts.
Heat treatment:
Quenching and tempering treatment to improve the hardness and durability of the parts.
Precision machining:
Use CNC machine tools for machining to ensure the dimensional accuracy of the parts.
Yüzey işleme:
Apply anti-rust coating or high-frequency quenching process to improve corrosion resistance and wear resistance.
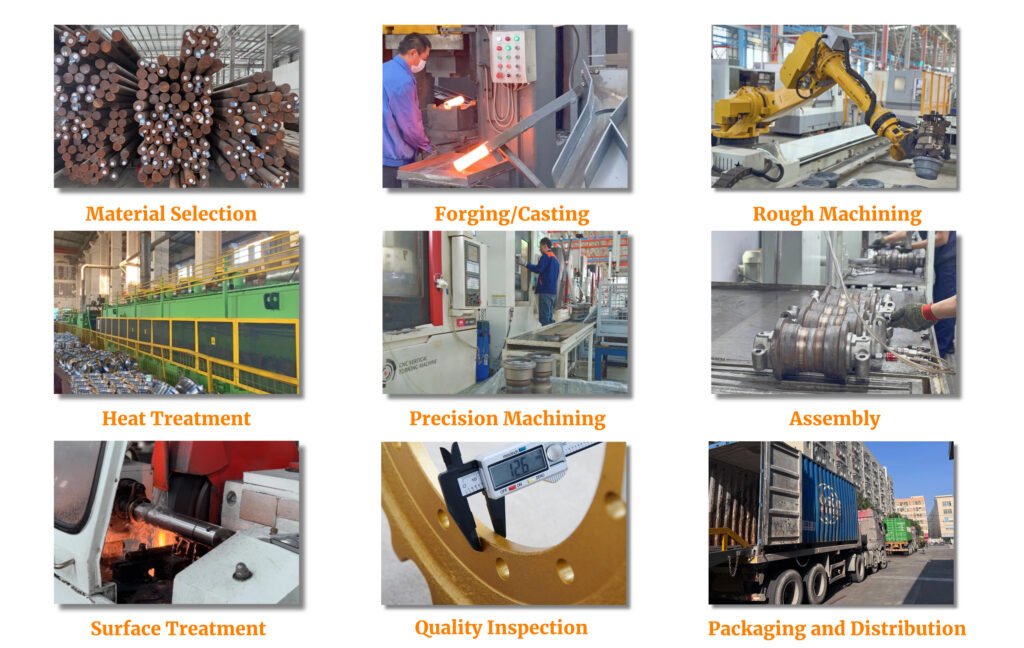
Daily maintenance and care
In order to extend the service life of the supporting track rollers, carrier rollers and idler wheels, users are advised to perform the following maintenance regularly:
Cleaning:
Regularly clean the dirt and debris on the wheel body and track surface to prevent wear.
Lubrication:
Add lubricating oil regularly according to the manufacturer’s recommendations to reduce friction and heat.
Check wear:
Check the wear of parts regularly and replace them in time if abnormalities are found.
Adjust the tension:
Ensure that the tension of the guide wheel is set within a reasonable range to avoid derailment or excessive stretching of the track.
Avoid overloading:
Avoid overloading of equipment during construction to reduce additional pressure on the chassis system.
Strengths and advantages of GFM Excavator Part Supllier
Bir profesyonel olarak ekskavatör alt takım parçaları üreticisi, GFM factory has the following unique advantages:
Advanced equipment:
Equipped with modern production lines, including CNC machining centers and fully automatic heat treatment equipment.
R&D capabilities:
With an experienced R&D team, we can provide customized solutions according to customer needs.
Sıkı kalite kontrolü:
Implement comprehensive quality management, from raw material procurement to finished product delivery, to ensure that each batch of products meets international standards.
Global service network:
GFM’s products have been exported to more than 50 countries and regions, providing fast response after-sales service.
E-posta: henry@gfmparts.com
Whatsapp: +86 17705953659
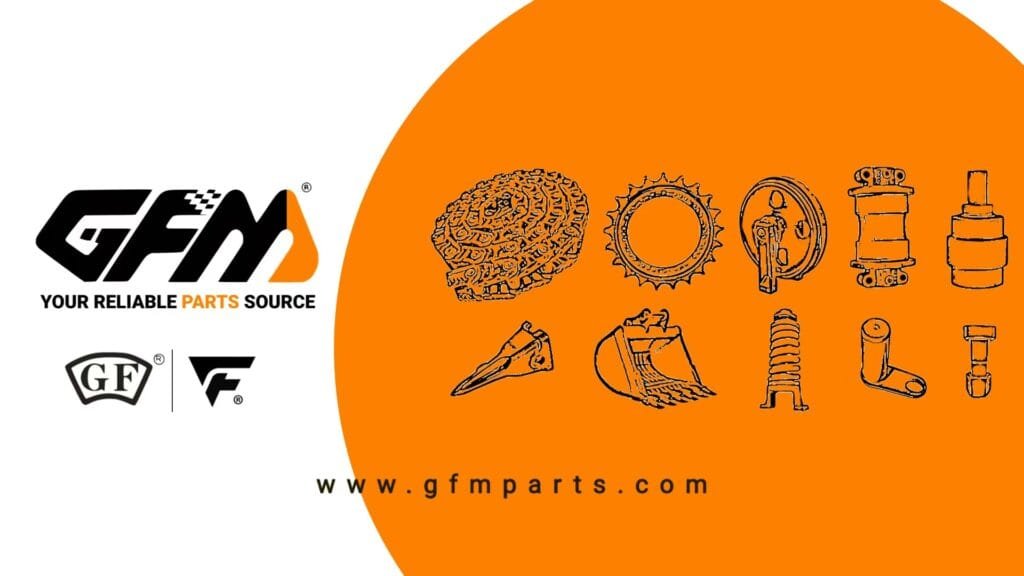