In the undercarriage system of an excavator, alt silindirler and carrier rollers are two important components. They work together on the crawler system of the excavator to ensure the stability, durability and efficiency of the equipment during operation. Although the two components have similarities in function, they have significant differences in design and function. Understanding these differences is crucial for excavator users and can help choose the right parts to improve the performance and life of the equipment.
What are bottom rollers?
The roller is one of the important components in the undercarriage system of the excavator that contacts the crawler chain. Its main function is to support the weight of the crawler and help maintain the tension of the crawler. The roller is usually located at the front end (or rear end, depending on the excavator design) of the crawler and works together with the sprocket and tensioner to ensure the smooth operation of the crawler system during operation.
The main functions of the roller:
- Support the weight of the crawler: The roller bears the weight of the front and rear parts of the crawler to ensure that the equipment does not sink or tilt during driving.
- Tension track system: The rollers work with the tensioning device to maintain the tension of the track and prevent the track from being loose or too tight, which affects the performance of the equipment.
- Prevent track deflection: The structure of the rollers helps the track stay on the correct track and prevents the track from running off track.
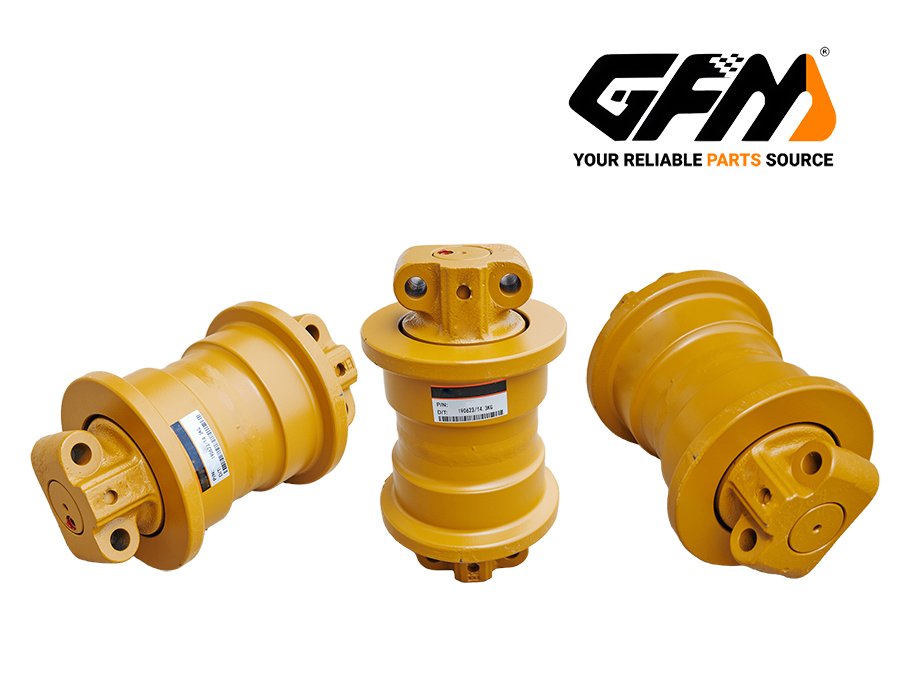
What is a carrier roller?
The carrier roller is mainly located in the middle of the excavator chassis, usually below or on the side of the track. Its main function is to support the lower part of the track chain and reduce the friction burden between the track chain and the ground. Unlike rollers, the carrier roller does not directly affect the tension of the track, but is more used to improve the stability of the track.
The main functions of the carrier roller:
- Reduce the burden on the track: The carrier roller helps share the pressure between the track and the ground, reduces ground friction, and extends the service life of the track.
- Improve track stability: The carrier roller supports the bottom of the track to ensure that the track remains stable when driving in complex terrain and prevents track imbalance due to excessive wear.
- Improve equipment maneuverability: The supporting role of the supporting roller under different terrain conditions enables the excavator to work more smoothly and improves the maneuverability of the machine.
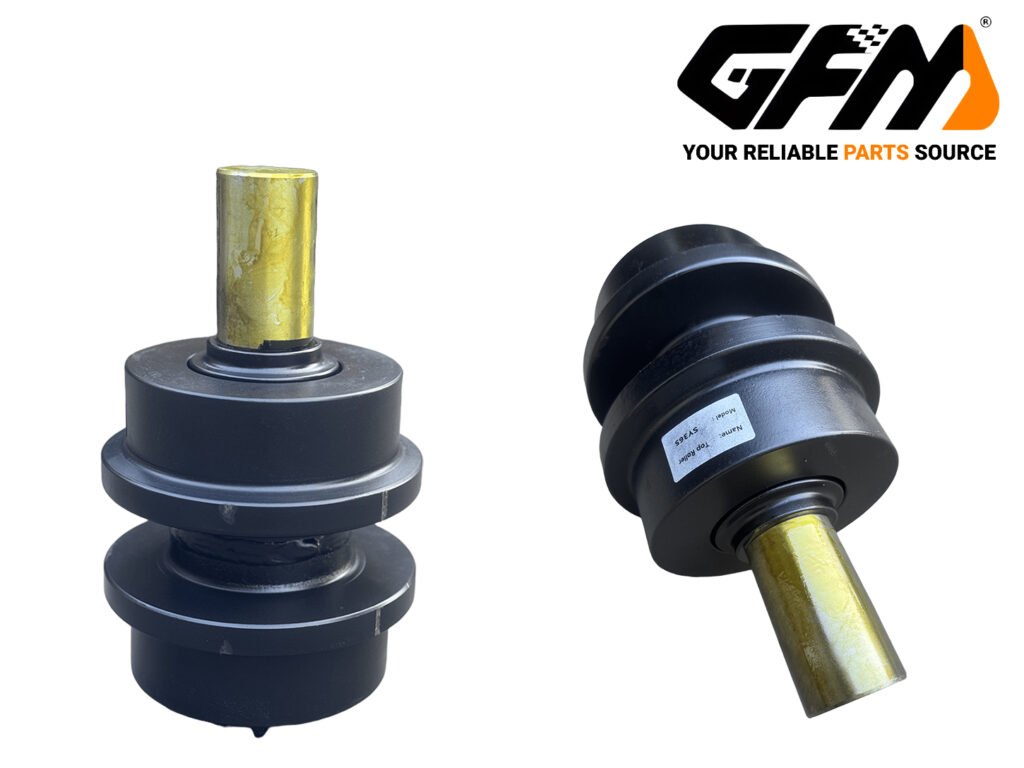
The main difference between bottom rollers and carrier rollers
Although the functions of supporting rollers and supporting rollers are closely related to the support and stability of the track, they have some significant differences in structure, function and usage scenarios:
Position and structure:
- The bottom roller is usually located at the front or rear end of the excavator track, directly supporting the track and adjusting the tension.
- The carrier roller is located in the middle of the track and mainly improves stability by supporting the lower part of the track.
Functional differences:
- The bottom roller is mainly responsible for supporting the weight of the track, maintaining the tension of the track, and preventing the track from loosening.
- The function of the carrier roller focuses on reducing the burden on the track, improving stability and reducing friction with the ground.
Durability requirements:
- The bottom roller needs to withstand greater pressure, so its material and design are usually more durable.
- Although the carrier roller also needs to be wear-resistant, due to its lighter workload, the material requirements are relatively low.
Maintenance:
- The maintenance of the bottom rollers is mainly focused on ensuring the adjustment of the track tension and regularly checking the wear of the supporting rollers.
- The maintenance of the carrier roller is more focused on reducing wear and improving the fit between them and the track, ensuring the flexible rotation of the supporting rollers.
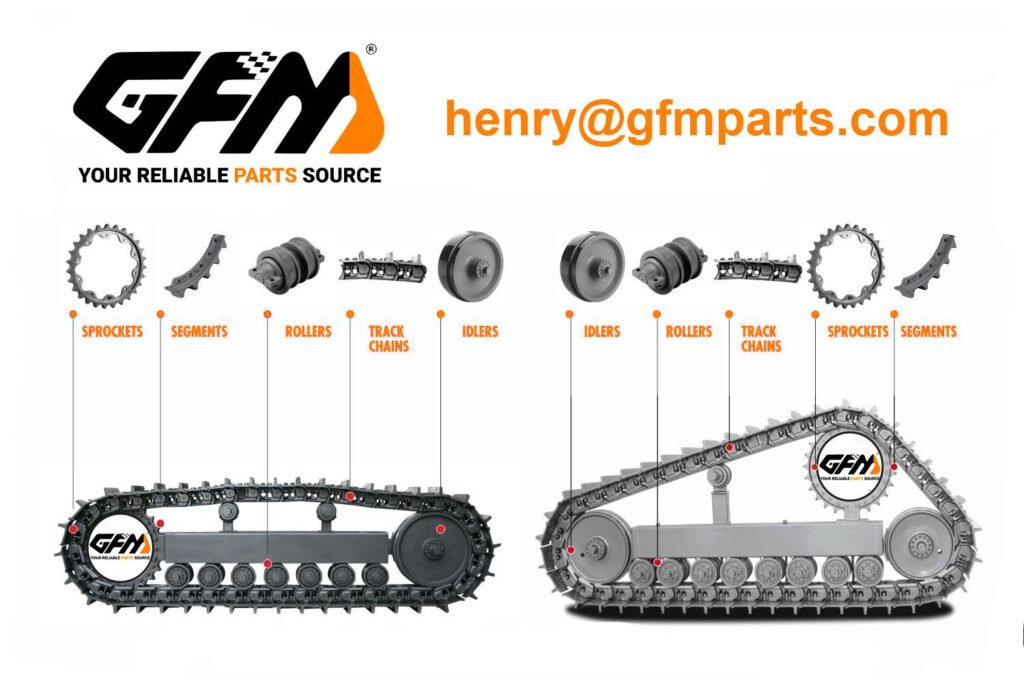
How to choose the right bottom rollers and carrier rollers?
Choosing the right track rollers and carrier rollers is crucial to the overall performance of the excavator. Here are a few factors to consider when choosing these two components:
- Equipment type and use environment: Different types of excavators have different requirements for supporting rollers and supporting rollers. If you are working on soft or unstable terrain, it is particularly important to choose more wear-resistant components.
- Quality and brand: Choosing well-known brands and high-quality components can ensure the service life of the supporting rollers and supporting rollers and the stability of the equipment. High-quality components can effectively reduce maintenance costs and improve the working efficiency of the equipment.
- Workload: Choose appropriate supporting rollers and supporting rollers according to the workload of the excavator. If heavy-duty operations are often carried out, choosing high-strength components can reduce the failure rate and ensure the continuous operation of the equipment.
Hızlı ve ücretsiz bir teklif alın | E-posta: henry@gfmparts.com | Whatsapp: +86 17705953659 |
Bottom rollers and carrier rollers are key components that cannot be ignored in the undercarriage system of the excavator. They ensure the normal operation of the crawler system through their unique functions. When selecting and using these parts, understanding their differences and their respective functions can help users better maintain the excavator and improve work efficiency. Whether it is a bottom roller or a carrier roller, choosing high-quality and suitable accessories is the basis for ensuring the long-term and stable operation of the excavator.
GFM ekskavatör alt takım parçaları provide high-quality bottom rollers and carrier rollers suitable for various working environments. Our products are known for their durability and stability, ensuring that your excavator remains in optimal operating condition. For more information or customized solutions, please contact our professional team!
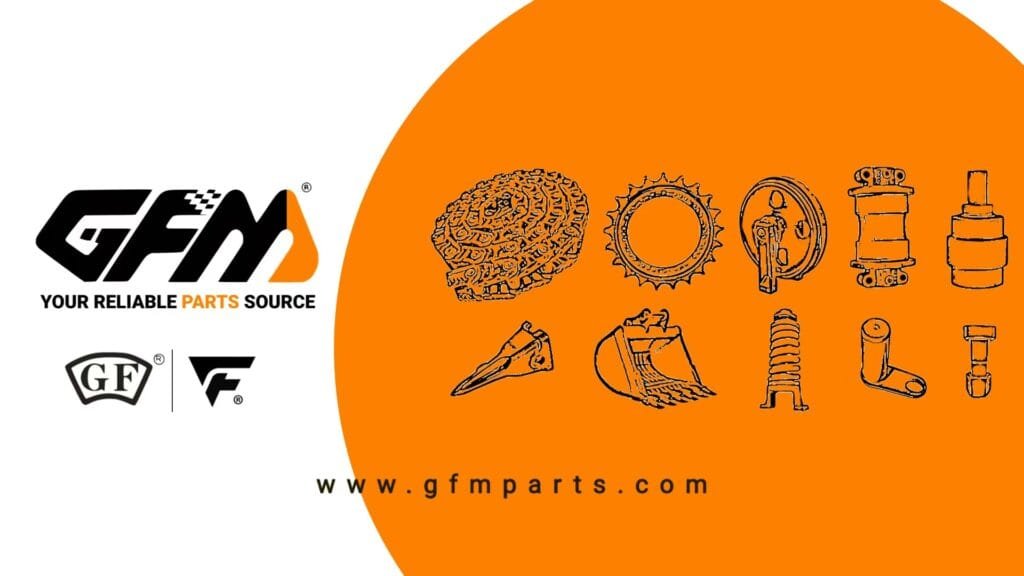