Table of contents
As a “versatile” equipment in the field of construction machinery, loaders are widely used in many scenarios such as construction, roads, agriculture, and mines due to their efficient material handling, excavation, and loading capabilities. As the requirements for construction efficiency, safety, and sustainability of engineering projects continue to increase, various types of loaders are also continuously upgraded in terms of technology and configuration. As an authority in the field of bulldozer undercarriage parts manufacturing, GFM has been deeply involved in chassis parts production for many years, providing reliable chassis support for various types of loaders with precise manufacturing processes and strict quality control.
Backhoe Loader
Introduction to Structure and Working Principles
Backhoe loaders integrate loaders and excavators, with a loading bucket at the front and a swing backhoe arm at the rear. The typical displacement is between 50–100 HP. Taking the Caterpillar 415 IL as an example, its net power is 69 HP (52 kW) and the maximum operating weight can reach 17,637 lb (8,000 kg). Through the center pivot or side shift design, the backhoe arm can rotate more than 180° to achieve flexible excavation.
Construction flexibility brought by the multi-functional arm design
Center-pivot and side-shift: The center pivot design is more compact and suitable for operation in small spaces. The side-shift arm can achieve horizontal movement without moving the whole machine, improving accuracy and efficiency.
Compatible with multiple attachments: In addition to the common bucket, it can also be equipped with rock hammers, compactors, hydraulic shears and other accessories to expand to multiple operation scenarios such as crushing, compaction, and demolition.
Typical operation scenarios and data comparison
Municipal pipeline construction: The backhoe loader can dig up to 14 ft (4.27 m) deep, which is suitable for trench excavation and backfilling.
Road repair and landscaping: With the ability to quickly switch between front and rear arms, the machine scheduling time is reduced, saving about 15-20% of working hours compared to a single excavator and loader combination.
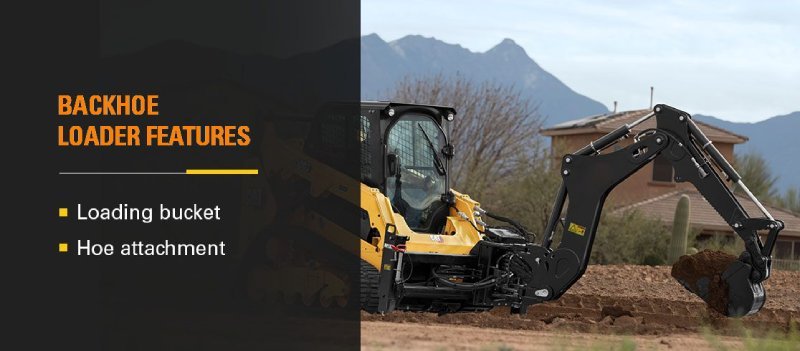
Skid Steer Loader
Compact body and high maneuverability
The skid steer loader rotates in place through the opposite movement of the left and right wheels, with a turning radius of zero. The body width is usually between 1.5–2.0 m, which is suitable for narrow working conditions. Standard models such as the Bobcat S650 have a rated operating capacity of 2,721 lb (1,235 kg) and a hydraulic output of up to 31.4 gpm (119 L/min).
Multi-way valve control system and hydraulic accessories
High flow option: Optional high flow kit, hydraulic output increased to 45 gpm (170 L/min), to meet the needs of high flow accessories such as drilling, sweeping, snow removal, etc.
Quick connector system: With universal quick connectors, buckets, wood grabs, sweeping brushes, breaker hammers, etc. can be replaced within 30 seconds to improve equipment utilization.
Cases of urban construction, small earthwork and gardening operations
Indoor demolition: Skid steer loaders can be equipped with a variety of crushing heads to efficiently demolish walls and Φ200 mm concrete layers on the ground in a limited space.
Landscaping: Equipped with a tree planting machine and a pit digging drill, it can achieve integrated tree planting and hole digging operations.
Potholes and countermeasures: The weight of the skid steer chassis is concentrated, and long-term hard ground operations can easily aggravate tire wear. It is recommended to cooperate with regular tire inflation inspections and tire protection chain installation.
Compact Track/Multi-Terrain Loader
Impact of crawler walking system on ground pressure
Compared with skid steers, compact crawlers distribute weight over the length and width of the crawler tracks. The typical ground contact pressure is only 4-6 psi (27.6-41.4 kPa), while the skid steer loader is 35-45 psi. Crawler machines can “float” and walk in soft and wet environments to reduce damage to the ground.
Stability in construction on soft ground and slopes
Tipping angle: The crawler chassis provides a lower center of gravity, and the safe working slope can reach 30°, far exceeding the 20° of wheeled or skid steers.
Gradability: With high-traction crawlers, the maximum climbing gradient can reach 70%, which is suitable for complex terrain such as field leveling, agricultural and forestry operations.
Comparison data with skid steers
Item | Skid steers | Compact track loaders |
Ground pressure (psi) | 35–45 psi | 4–6 psi |
Rated operating capacity | 1,200–2,200 lb | 1,000–2,000 lb |
Top speed | 7–12 mph | 6–8 mph |
Cost | Low tire replacement cost | Slightly higher track maintenance cost |
Applicable scenarios and best matching accessories
Wetland construction: can be equipped with swamp tracks to further reduce ground pressure.
Municipal green construction: equipped with sanitation brushes and vacuum cleaner accessories, one machine can do multiple things.
Maintenance suggestions: regularly remove dirt and rocks under the tracks, apply chain track grease, and extend the life of chassis parts.
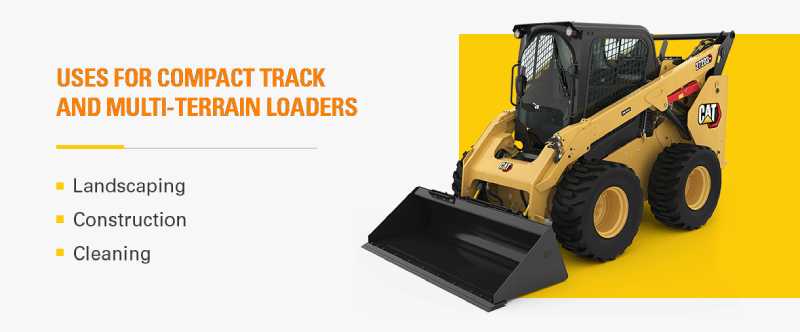
Wheel Loader
Power system and transmission mode
Taking the Caterpillar 950 medium wheel loader as an example, its engine net power is 249 hp (186 kW), maximum net torque is 908 ft·lb (1,231 N·m), and operating weight is 42,461 lb (19,260 kg). It adopts an all-purpose transmission axle and a multi-stage oil bath brake system to ensure efficient power transmission and braking safety.
Contribution of large displacement power to loading efficiency
Bucket capacity: standard bucket volume is 3.75–5.75 yd³ (2.9–4.4 m³), and high load can load 7–9 t of materials at a time.
Cycle efficiency: With the automatic bucket rotation control system, the bucket loading cycle can be shortened by 12%, and the daily output can be increased by about 8%.
Common use cases in engineering projects
Mine loading: With high bucket impact force (breakout force 36,203 lb, 161 kN), ore and slag can be quickly stacked and matched with a wide mining crawler chassis, which is anti-skid and wear-resistant.
Port terminal: High stability and high working height (maximum bucket unloading height 11 ft) make it easy to load bulk cargo into vans and ocean-going ships.
Fuel-saving driving skills and data support
Economic mode (Eco Mode): After activation, the engine speed automatically drops to about 1,800 rpm, reducing fuel consumption by 10–15%.
Multi-condition transmission coordination: Real-time adjustment of shifting strategy according to load, linkage with intelligent electronic hydraulic system, and improvement of fuel efficiency by 5%.
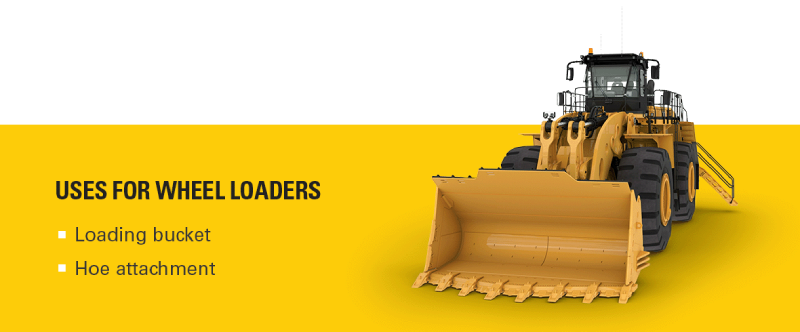
Track Loader
Advantages of full crawler travel system
Track loaders evenly distribute the weight of the entire machine, providing excellent traction and stability on mud, ice and snow and loose soil. Take the Takeuchi TL8 compact crawler loader as an example. The ground pressure under the 12.6″ crawler track is only 5.4 psi (37.2 kPa), which greatly reduces the damage to the ground.
Evaluation of steering and maneuverability
Steering method: A combination of torsion bars or hydraulic steering valves is used to achieve smooth driving and precise turning.
Speed regulation characteristics: Low gear 4.6 mph, suitable for heavy-load operations; high gear 6.8 mph, to meet the needs of rapid maneuvering within the construction site.
Comparison of advantages and disadvantages with wheel loaders
Ground adaptability: Crawler machines are better than wheeled machines on soft ground, and wheeled machines have advantages in driving speed and maintenance costs on hard ground.
Traction capacity: The maximum traction of crawler machines is increased by about 20%, and they can operate stably in low-adhesion environments.
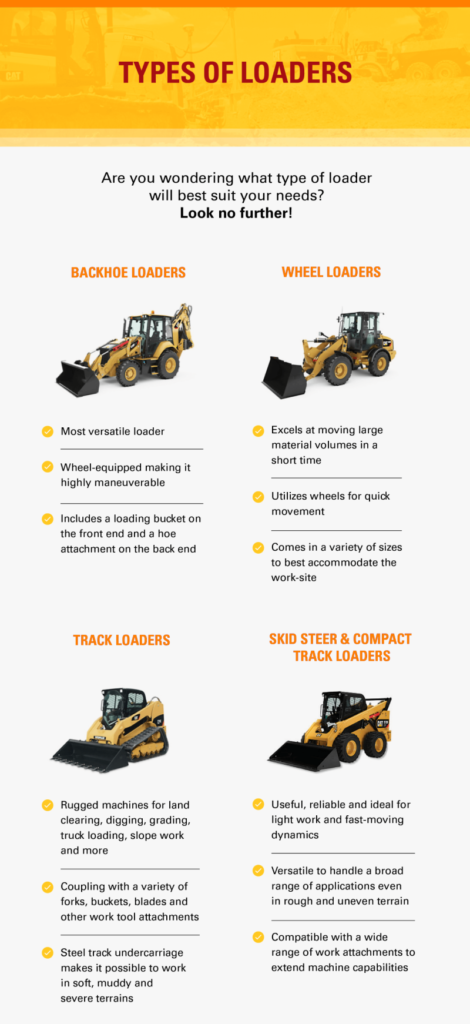
How to choose a suitable loader according to working conditions
Key parameters: working environment, load requirements, terrain conditions
- Working environment: indoor factory buildings, urban roads, mines or agriculture.
- Load requirements: light dump buckets, heavy-load bulk or concrete, etc.
- Terrain conditions: hardened surface, loose soil, swamp or inclined slope.
Selection process and professional evaluation tools
- Demand research: interview with site managers and equipment operators to collect real working conditions.
- Simulation: Use BIM or construction simulation software to test the equipment’s walking trajectory and loading efficiency in advance.
- Field test: organize prototypes to enter the site and evaluate fuel consumption, operating rate and maintenance convenience through a 1-week test.
GFM’s technical support advantages in chassis parts manufacturing
- Deep hole quenching and precision grinding process: ensure accurate matching of chain rails and support chains, and reduce wear rate by 15%.
- Multi-alloy material formula: optimize alloy composition for different geological environments (stone, sand, clay), and extend the service life of chassis parts by 20%.
Practical guide for daily maintenance and care of loaders
Daily/periodic inspection points
- Engine compartment: Check engine oil, coolant, fuel filter, and perform routine inspections before refueling every day.
- Hydraulic system: Check oil level, hose interface oil leakage, 50 h Replace the hydraulic oil filter.
- Chassis parts: Clean the chain rails and support chains every day, and check the track tension and wear periodically.
Maintenance tools and recommended lubricant models
- Hydraulic oil: It is recommended to use high-grade anti-wear hydraulic oil that meets the ISO VG 46 standard.
- Gear oil: The chassis reducer uses SAE 80W-90 GL-5 grade gear oil.
- Lubricating gun and grease: Equipped with a high-pressure grease gun, regularly oil the support chain, aligning wheel and slewing bearing.
Common troubleshooting and quick repair tips
- Slow walking: Clean the coupling box filter and check the hydraulic control valve.
- Hydraulic shaking: Expel air and check the blockage of the return oil filter.
- Abnormal chassis noise: Adjust the track tension and tighten the loose bolts.
Professional advice to extend the life of chassis parts
- Evenly distribute the load: Avoid long-term heavy-load single-sided operation to reduce chain track fatigue.
- Regularly rotate the track: Interchange the left and right tracks to delay excessive wear on one side.
- Environmental adaptation material selection: High wear-resistant or heat-resistant alloy chassis parts are selected according to the working environment.
Hızlı ve ücretsiz bir teklif alın | E-posta: henry@gfmparts.com | Whatsapp: +86 17705953659 |
Through an in-depth analysis of the five major types of loaders, we can see that:
- Backhoe loaders are flexible and suitable for small and medium-sized earthwork and comprehensive operations.
- Skid steer loaders are extremely maneuverable and are the first choice for narrow spaces and multi-condition attachment applications.
- Compact crawler machines conquer soft and sloping land with low ground pressure and superior stability.
- Wheel loaders dominate large-tonnage handling with large displacement power and high discharge efficiency.
- Crawler loaders are as stable as a rock in extreme terrain and heavy-load traction.
GFM As a dozer parts manufacturing expert, we provide solid and reliable chassis support for various types of loaders through precise material formulation and precision processing technology. Looking to the future, with the integration of intelligence, electronics and new energy technologies, loaders will make breakthroughs in automated driving, energy efficiency management and remote diagnosis.
Whether you are in the stage of equipment selection, project implementation, or maintenance management, the professional insights and practical suggestions provided in this article can bring practical help to your decision-making and daily work. Welcome to communicate with the GFM chassis parts team at any time to jointly create more efficient, safe and sustainable engineering machinery solutions!
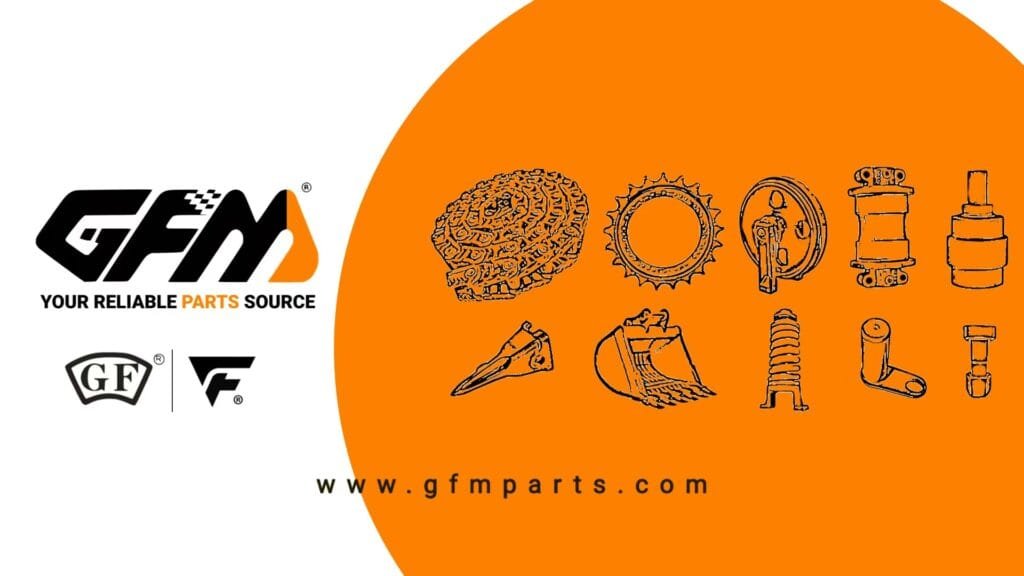