In the operating cost structure of construction machinery, fuel consumption accounts for as much as 40%-60%. Based on ten years of industry data accumulation, GFM excavator undercarriage part supplier deeply analyzes 15 proven effective fuel-saving strategies, covering three dimensions: operating specifications, equipment maintenance, and technical transformation, helping k customers achieve an average daily fuel saving of 20-35 liters per machine, saving more than 100,000 yuan in operating costs per year.
Optimization of operation behavior: Driver habits directly affect 20% fuel consumption performance
Golden rule for operation path planning
- Three-dimensional prediction method: Observe the terrain for 10 minutes before starting work, and use “elevation-obstacle-material” three-dimensional positioning to reduce invalid movement
- Fan-shaped operation method: Expand a 120° operation sector with the stop point as the center, which can reduce the rotation angle by 40% compared with the traditional straight line method
- Material stratification method: Divide the excavation depth into 3 layers of ladder operation, which can improve efficiency by 25% compared with disordered excavation
Precise control skills of hydraulic system
- Golden ratio of compound action: Maintain a 1:0.8 speed ratio between boom lifting and arm recovery
- Economic speed range: Control the engine speed in the green area, and the fuel efficiency will be improved by 12%
- Standby management specifications: The engine must be turned off if it stops for more than 15 minutes to avoid invalid idling and fuel consumption
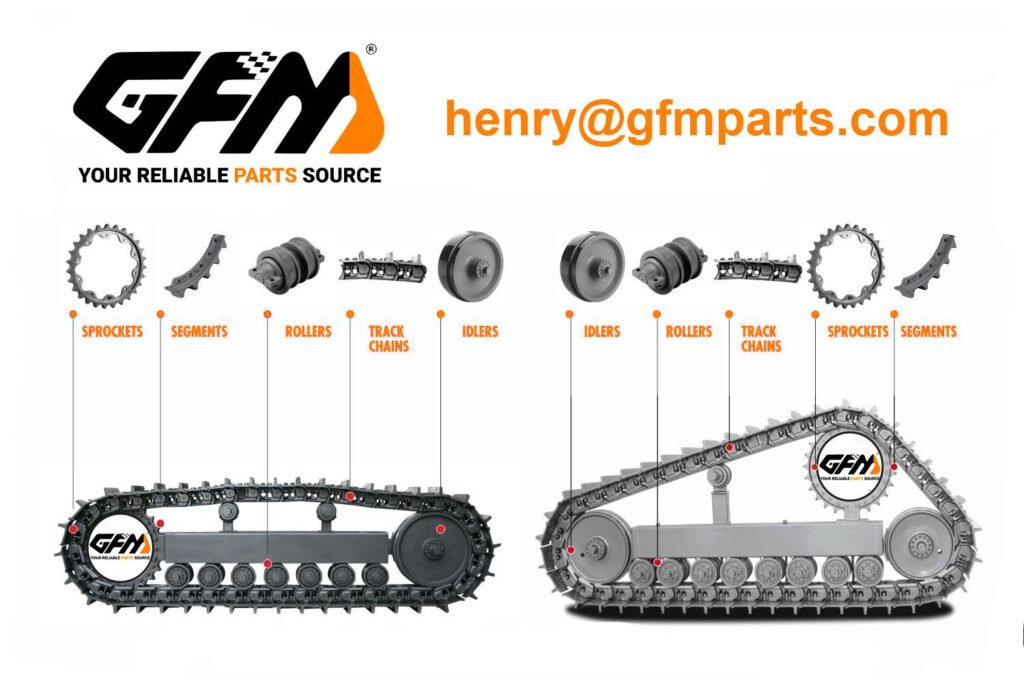
Equipment fine maintenance: The status of key components affects 30% fuel economy
Power system maintenance standards
Components | Detection cycle | Replacement standards | Fuel saving effect |
Air filter | 250 hours | Pressure difference > 25kPa needs to be replaced | 8-12% |
Diesel filter | 500 hours | Fuel flow < 90% needs to be replaced | 5-8% |
Injector | 2000 hours | Atomization uniformity < 85% | 10-15% |
Hydraulic system efficiency improvement plan
- Temperature control: Keep the hydraulic oil temperature at 50-70℃, and the viscosity will decrease by 30% and the pump loss will increase by 5% for every 10℃ increase
- Seal detection: Check the O-ring wear every 500 hours, and a 0.1mm gap will cause 5% pressure loss
- Pipeline optimization: Use GFM high-pressure hose, which reduces pressure loss by 18% compared with ordinary pipes
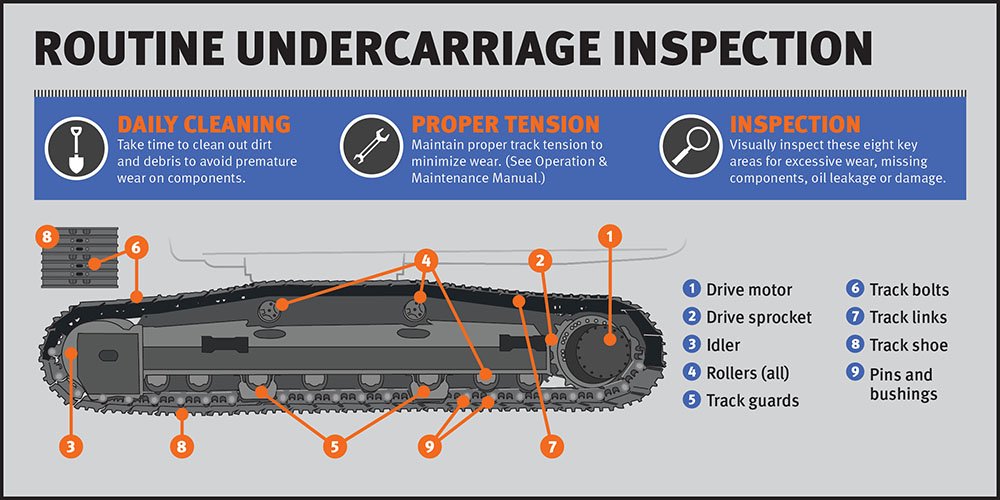
Technical innovation application: Intelligent transformation to achieve continuous energy saving
Engine intelligent control system
- ECO mode algorithm: Dynamically adjust the fuel supply curve through the GFM intelligent control module, saving 9-15% fuel in the non-full load stage
- Working condition adaptive technology: 5 working modes are configured, and fuel efficiency is improved by 22%
Energy recovery system (ERS)
- Swing brake energy recovery: converts braking kinetic energy into hydraulic energy storage, saving 3-5ml of fuel per swing
- Arm potential energy recovery: recovers gravity potential energy during descent, reducing engine load by 12%
By implementing the systematic solution in this guide, 85% of customers achieved a 18-35% reduction in fuel consumption within 3 months. Take action now to create greater value for every drop of fuel!
Hızlı ve ücretsiz bir teklif alın | E-posta: henry@gfmparts.com | Whatsapp: +86 17705953659 |
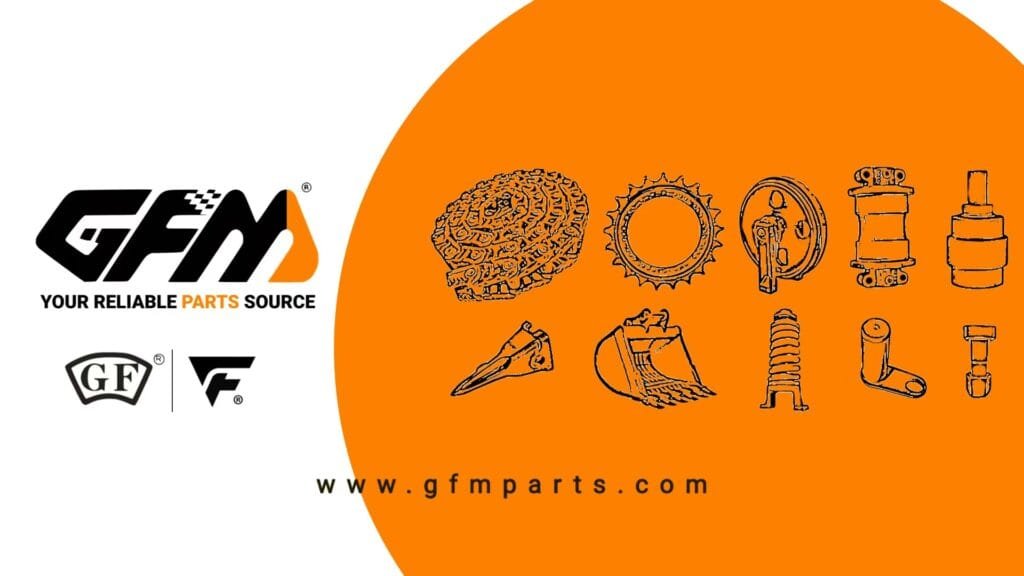