In the heavy machinery industry, the bulldozer track roller is an indispensable and important part. Whether in earthwork, mining or construction, the quality and performance of the track roller directly affect the operating efficiency and service life of the bulldozer.
Definition
The bulldozer track roller is a heavy engineering machinery accessory used to support the weight of engineering machinery such as bulldozers and roll on the track rail or track plate surface. It not only provides support and stability, but also prevents the track from slipping laterally and ensures that the machine moves in the direction of the track.
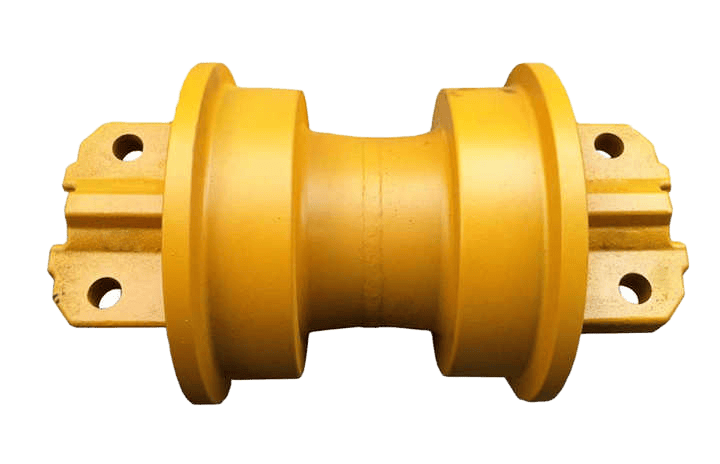
Working principle
The track roller is fixed under the wheel frame by screws to distribute the weight of the machine on the track plate. Its roller flange clamps the chain rail to prevent the track from derailing and ensure the stable operation of the machine on various terrains. The design of the track roller makes it have less rolling resistance and has a longer service life when operating in mud and water.
Design features and advantages
The track roller can be divided into single-sided track roller and double-sided track roller according to its structure. The single-sided track roller design gives the bulldozer strong climbing ability and passing performance, which is particularly suitable for operations on hard ground. The double-sided track roller contacts the ground through two wheels, which improves the stability of the bulldozer and is suitable for large operating areas, flat ground or soft soil environments.
- High-strength material: GFM track rollers are made of high-quality alloy steel, and have excellent impact resistance and wear resistance through high-temperature forging and heat treatment processes.
- Excellent sealing performance: Equipped with high-performance sealing rings to prevent mud and water from intruding and extend service life.
- Strong load-bearing capacity: High-precision processing technology is used to ensure the perfect match between the bearing and the track, and it can withstand high-load operation.
- Multi-environment adaptability: Designed for extreme environments such as high temperature, high cold, and muddy, it meets a variety of construction needs.
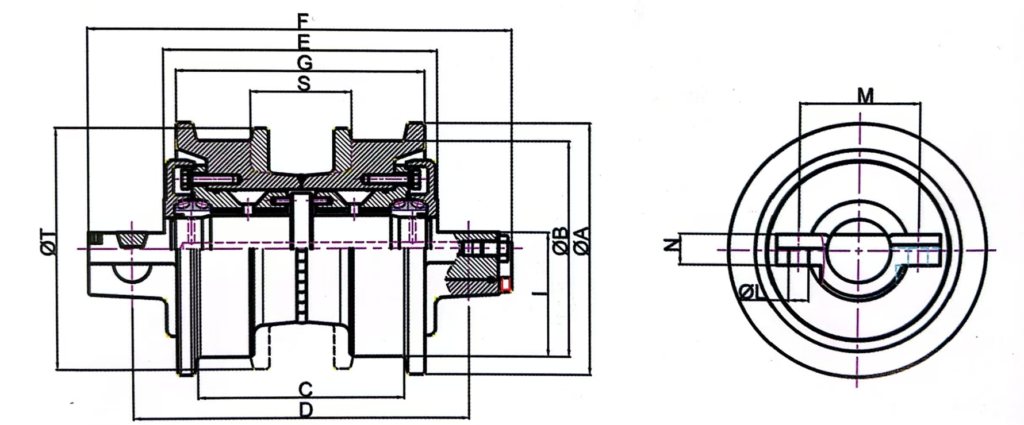
Differences from excavator track rollers
Bulldozer track rollers and excavator track rollers are different in working conditions and structures. Bulldozer track rollers need to move continuously, and the operating ratio is much higher than that of excavator track rollers, so the quality requirements are higher. In addition, bulldozer rollers usually have stronger load-bearing capacity and higher wear resistance to adapt to harsh working environments.
- Differences in use: Bulldozer rollers mainly carry the weight of the machine and guide the crawler to run, while excavator rollers need to adapt to frequent rotation and multi-angle operations.
- Structural design: Bulldozer rollers focus more on wear resistance and impact resistance, while excavator rollers emphasize flexibility and lightness.
- Load capacity: Bulldozer rollers usually need to withstand higher static loads, while excavator rollers need to adapt to dynamic loads.
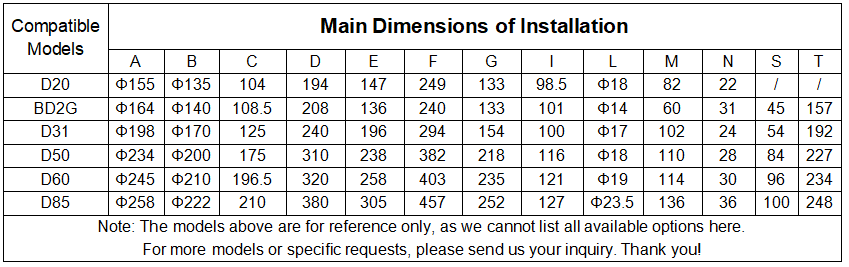
Accessory models and compatibility
GFM bulldozer accessories manufacturers provide a variety of models of rollers that are compatible with bulldozers of different brands and models. We support OEM/ODM customization services and can design exclusive specifications according to customer needs to ensure perfect compatibility.
Production process
GFM bulldozer bottom roller factory use advanced production processes to ensure the high quality of rollers. Casting processes are used to manufacture rollers with complex shapes, while forging processes are used to produce rollers with high strength and toughness. After the roller is formed, it is precision-machined, including turning, milling and drilling, to ensure its dimensional accuracy and surface finish. In addition, heat treatment processes are used to improve the hardness and wear resistance of the roller.
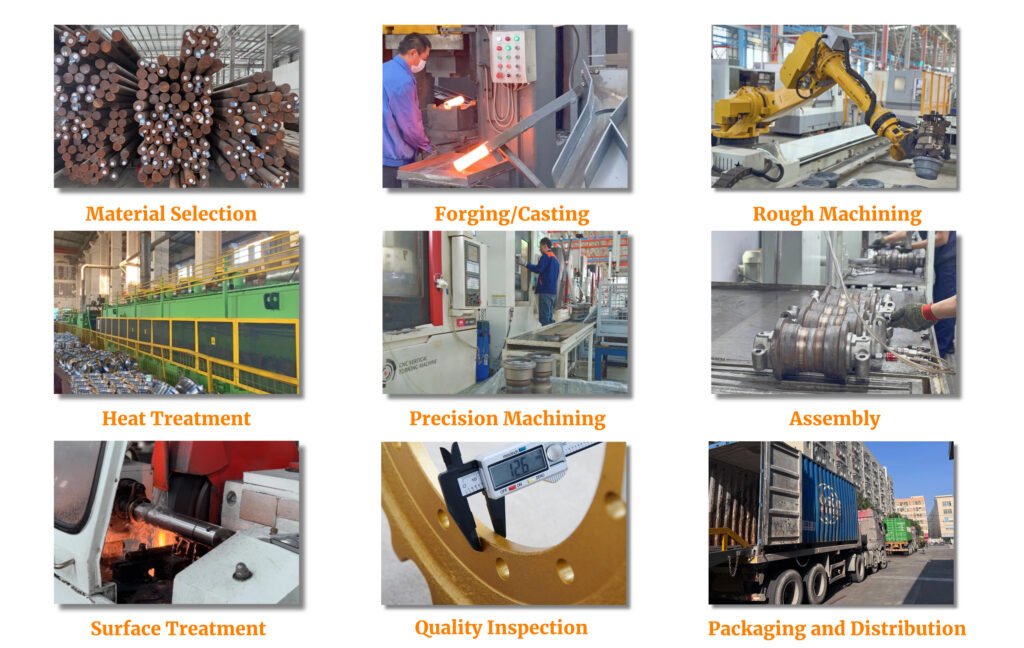
Daily maintenance
In order to extend the service life of the roller, regular maintenance is required. This includes:
- Maintaining proper tension of the track to avoid wear caused by over-tightening or over-loosening
- Maintaining the centering of the guide wheel position to reduce wear on other parts of the walking mechanism
- Flipping the track pin and the pin sleeve at the appropriate time to restore the correct track pitch
- Tightening the bolts and nuts in time to prevent loosening and breaking
- Lubricating the walking mechanism regularly to avoid “burning” of the bearings
- Checking cracks in time and welding and strengthening them.
Factory advantages
GFM excavator and bulldozer parts manufacturer has significant advantages in the production of rollers. We have advanced production equipment and a technical team that can provide customized solutions according to the different needs of customers. Our products enjoy a good reputation in the market and are known for their high quality, high performance and long life. In addition, we also provide high-quality after-sales service to ensure that customers receive timely technical support and maintenance services during use.
Reasons to choose GFM bottom rollers
- Advanced technology: GFM has industry-leading R&D capabilities and its products are ISO 9001 quality certified.
- Comprehensive service: Provide full-process services from selection, design to after-sales to meet customers’ all-round needs.
- Global supply chain: Relying on a strong production and logistics system, we respond quickly to customer orders and ensure on-time delivery.
- Industry reputation: GFM rollers have been highly recognized by many customers around the world for their stable performance and ultra-long service life.
E-posta: henry@gfmparts.com
Whatsapp: +86 17705953659
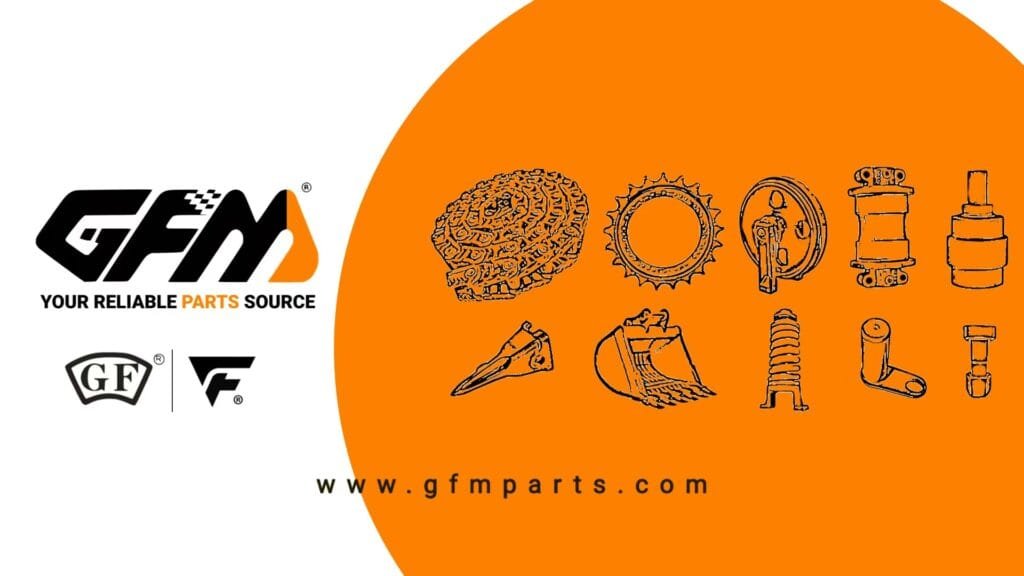