In the field of modern engineering machinery, excavators are not only the core equipment on the construction site, but their efficient operation ability is directly related to the progress and cost control of the project. GFM is an excavator parts manufacturer with 14 years of experience in the industry. We have unique insights into excavators. Welcome to contact us to learn more about ekskavatör alt takım parçaları and excavators.
In-depth analysis of the working principle of excavators
Hydraulic transmission and energy conversion
The core of the excavator lies in the hydraulic system, which efficiently converts the mechanical energy generated by the internal combustion engine into hydraulic energy to drive the boom, dipper and bucket. The basic process of the hydraulic system includes:
- Engine output and hydraulic pump conversion:
- The power generated by the engine after combustion drives the hydraulic pump through the transmission system, and the hydraulic pump pressurizes the hydraulic oil. The high-pressure oil is transported to each working actuator (hydraulic cylinder and hydraulic motor) through the pipeline. In this process, the efficiency of the hydraulic system is affected by factors such as the volumetric efficiency of the hydraulic pump, the oil flow rate and the temperature. In actual engineering, computational fluid dynamics (CFD) is also used to simulate the internal flow of the hydraulic system to optimize the pump body design and pipeline layout, thereby reducing energy loss.
- Coordination between actuator movement and mechanical structure:
- Hydraulic cylinders and hydraulic motors convert high-pressure oil energy into linear or rotary motion, driving the mechanical arm and bucket to operate. Mechanical structure design (such as connecting rods, brackets and rotary joints) is crucial to the motion accuracy and stability of energy transmission. Modern excavators often use finite element analysis (FEA) to perform stress and fatigue life analysis on mechanical structures to ensure long-term operation stability and safety.
- Feedback and control system:
- Advanced electronic control units (ECUs) and sensor networks monitor hydraulic pressure, oil temperature and actuator displacement in real time to form a closed-loop feedback system to accurately control the speed and strength of each action. The combination of data acquisition and algorithm optimization can not only dynamically adjust the hydraulic system parameters, but also provide a strong basis for subsequent preventive maintenance and fault prediction.
Collaboration between mechanical design and electronic systems
- Mechanical structure design:
- The collaborative work between the various components of the excavator is the key to the design. Reasonable arm and dipper angles can ensure the best operating range and radius, while reducing mechanical shock and vibration. Structural design optimization often uses computer-aided design (CAD) tools to simulate stress distribution under different working conditions to ensure sufficient safety factor in extreme environments.
- Electronic control and intelligent adjustment:
- The electronic control system not only realizes the precise regulation of hydraulic components, but also combines GPS, acceleration sensors and tilt sensors to realize all-round monitoring of the working status of the excavator. By analyzing data through intelligent algorithms, operating parameters can be optimized in real time, energy waste can be reduced, and energy saving and consumption reduction can be achieved.
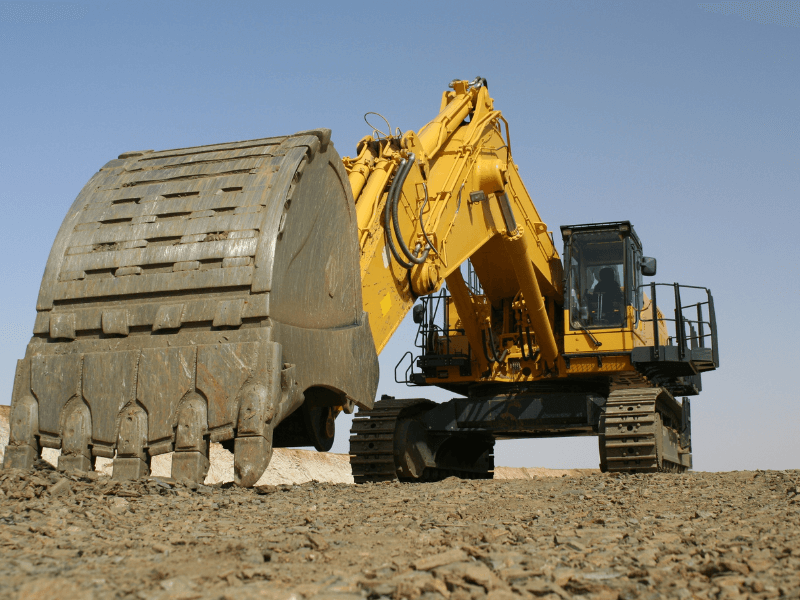
Multi-dimensional analysis of factors affecting excavator efficiency
Design and manufacturing quality
- Structural optimization and material selection:
- High-quality design requires not only structural optimization and reduced deadweight, but also the selection of advanced materials that are wear-resistant, corrosion-resistant and fatigue-resistant. Reasonable material selection and fine manufacturing process can reduce component wear and improve the life and efficiency of the whole machine.
- Manufacturing process and assembly accuracy:
- Precision assembly process can reduce mechanical clearance and energy loss. For example, high-precision CNC machining technology is widely used in the manufacturing of key components, and its matching degree directly affects the stability and response speed of hydraulic transmission.
Dynamic performance of hydraulic system
- Oil characteristics and temperature control:
- The viscosity, cleanliness and anti-oxidation performance of hydraulic oil directly affect the transmission efficiency and system life. A reasonable temperature control system can keep the oil within the optimal working temperature and avoid the loss of efficiency caused by overheating of the oil.
- Matching of pumps, valves and cylinders:
- The matching degree between each hydraulic component (such as flow rate and pressure tolerance) determines the response speed and stability of the system. Engineers often adjust design parameters through test data and simulation analysis to achieve the optimal working state.
Operator technology and training
- Operation proficiency and experience accumulation:
- The efficient use of excavators depends not only on hardware performance, but also on the operator’s deep understanding of equipment characteristics. Advanced simulation training systems and virtual reality (VR) technology are gradually being applied to operator training, improving operation accuracy and safety awareness through simulation exercises.
- Data feedback and improvement mechanism:
- Through real-time data collection and big data analysis, operators can continuously adjust operating parameters. For example, by monitoring workload and energy consumption data, deviations in operation can be discovered in time, and targeted training can be carried out to improve overall efficiency.
Environmental factors and working conditions
- Terrain and soil changes:
- There are obvious differences in the operating efficiency of excavators under different terrains and soils. In soft soil or high humidity environments, the equipment is easily affected by mud or sinking, which affects the stability of operation. It is particularly important to optimize the hydraulic system adjustment parameters and operation strategies for different working conditions.
- Climate and temperature influence:
- High or low temperature environments will affect the performance of hydraulic oil and the thermal expansion and contraction of metal parts of equipment. Scientifically formulated environmental adaptability operation plans and seasonal maintenance plans can ensure that the equipment maintains efficient operation under various extreme climate conditions.
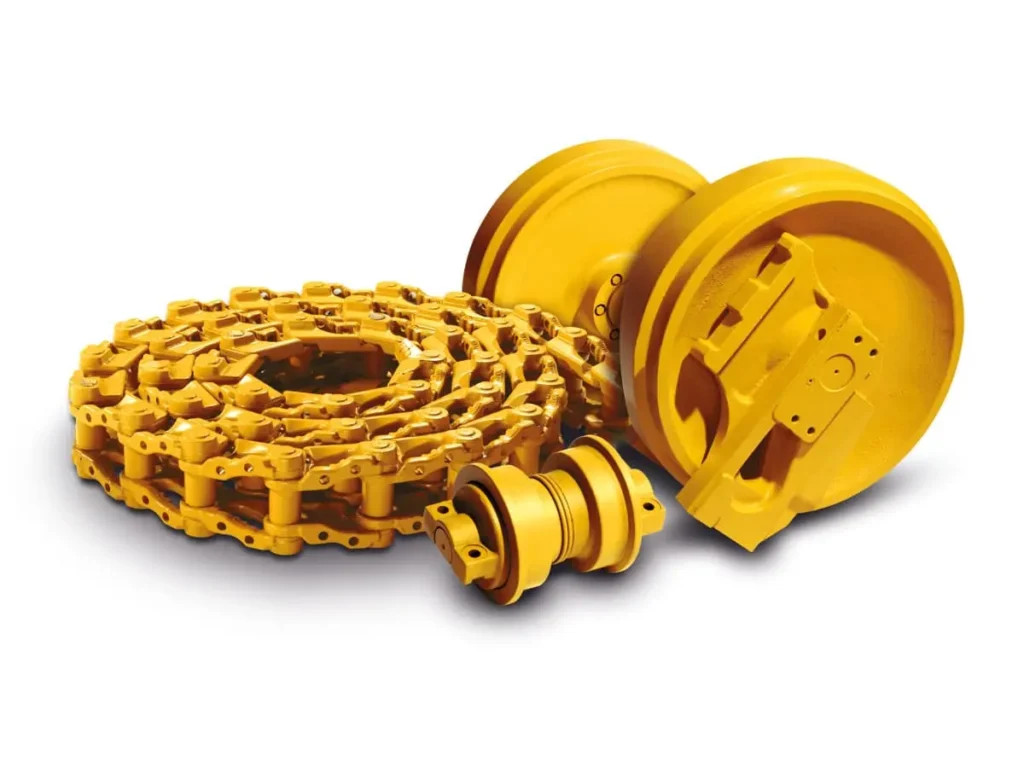
In-depth solutions to improve the working efficiency of excavators
Optimize equipment selection and customized configuration
- Multi-dimensional parameter optimization:
- According to the actual needs of the project, comprehensively consider parameters such as excavation radius, operating depth, load capacity, etc., and select equipment with optimized structure and hydraulic system design. Through software simulation and engineering testing, the optimal matching of different models of equipment in specific environments is achieved.
- Customized upgrade:
- For specific working conditions, high-efficiency hydraulic valves, wear-resistant buckets and intelligent control units can be customized. For example, by improving the bucket tooth design and using high-hardness alloy materials, not only can the working efficiency be improved, but also the service life can be extended.
Operator skill improvement and information training
- Systematic training system:
- Establish a complete operator training system, use simulators and VR technology to provide comprehensive training from basic operations to advanced working conditions. The training content covers the principles of hydraulic systems, electronic control logic and emergency handling of faults, ensuring that operators can quickly make correct judgments in various working environments.
- Data-driven operation feedback:
- With the help of a real-time data monitoring platform, the key parameters of each operation (such as oil pressure, flow, operation time, load status, etc.) are recorded, and operational problems are promptly fed back through data analysis, and improvement suggestions are formed to achieve refined management.
Intelligent monitoring and system tuning
- Internet of Things and remote monitoring:
- Using the Internet of Things technology, various hydraulic components and sensors are connected to the Internet to achieve real-time monitoring of various parameters of the excavator. The remote control system can automatically adjust the operating parameters when an abnormality is found, reducing errors and delays caused by human intervention.
- Predictive maintenance and AI tuning:
- Apply big data and artificial intelligence algorithms to predict the wear trend and potential failures of key components through historical data and real-time monitoring. Through intelligent tuning, maintenance plans are made in advance to reduce unexpected downtime and improve overall production efficiency.
Systematic comprehensive maintenance strategy
- Combination of periodic and preventive maintenance:
- Develop a maintenance cycle table based on working hours, load conditions and environmental impacts, and distinguish between daily maintenance, regular inspections and deep maintenance. Preventive maintenance not only reduces the failure rate, but also maintains the best working condition by adjusting the hydraulic system and cleaning each component.
- Technical manual and operation record management:
- Establish a detailed maintenance manual and fault record database to provide standardized operating procedures and troubleshooting solutions for engineering and technical personnel. Through the analysis of historical maintenance data, the maintenance plan is continuously optimized to improve the overall reliability of the equipment.
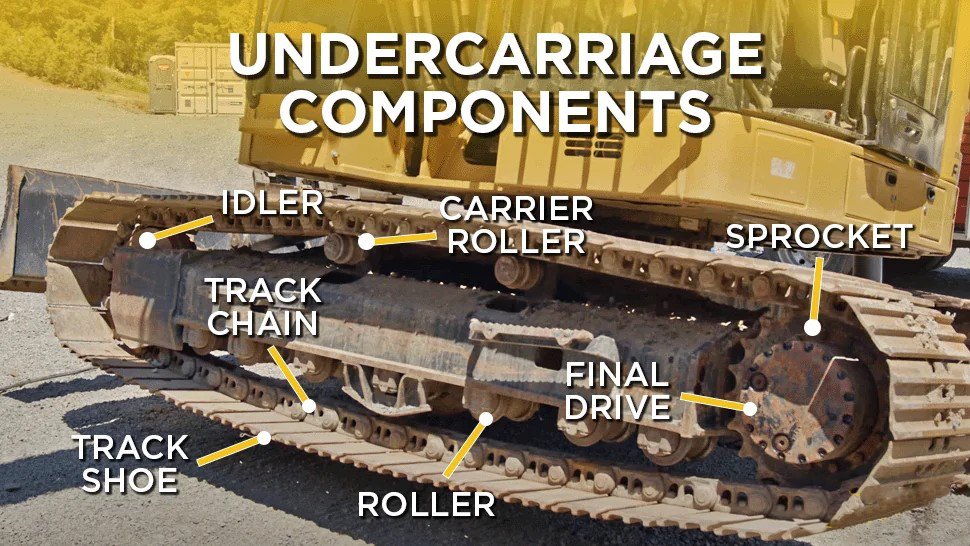
Safety and efficiency management during the use of excavators
Safe operation specifications
- Strictly abide by the operating procedures:
- Each excavator should be inspected in detail before use to ensure that all sensors, hydraulic lines and control systems are operating normally. Operators must strictly follow standard operating procedures to prevent equipment damage or safety accidents caused by misoperation.
- Emergency handling and accident prevention:
- Equipped with a complete emergency plan and regular safety drills. Through the intelligent monitoring system, equipment abnormalities are detected in real time, and automatic alarms are issued when potential problems are found to ensure that timely measures are taken before accidents occur.
Environmental adaptation and load control
- Overload protection mechanism:
- During the operation, the load status of the equipment should be monitored in real time through sensors to avoid long-term overload operation. Overload operation will not only accelerate the wear of parts, but also cause abnormal temperature of the hydraulic system and shorten the life of the equipment.
- Working condition adaptability adjustment:
- According to the actual on-site environment (such as terrain slope, soil moisture, etc.), timely adjust the hydraulic parameters and operating angles to ensure that the equipment operates under the optimal load. The data feedback system can automatically record environmental changes and provide a basis for subsequent parameter tuning.
Excavator comprehensive maintenance manual: technical details and practical guide
To ensure that the equipment is always in an efficient operating state, it is recommended to carry out maintenance work at the following levels:
Daily inspection and maintenance
- Hydraulic system inspection:
- Regularly check the oil level, oil quality and viscosity of the hydraulic oil to ensure that there are no impurities or deterioration.
- Observe whether the hydraulic pipeline has oil leakage, swelling or aging.
- Check the working condition of the hydraulic pump and valve, and monitor whether the oil circuit pressure is stable within the set range through the pressure gauge.
- Mechanical component inspection:
- Check the tightness of each connection, hinge and shaft to prevent vibration or abnormal noise caused by looseness.
- Check the hydraulic cylinder seals regularly and replace them when necessary to avoid energy loss caused by seal failure.
- Lubrication system maintenance:
- Ensure that high-quality lubricants are added to each moving part and key connection in a timely manner as required to reduce friction and wear.
- For easily worn parts, preventive lubrication and cooling treatment can be carried out regularly.
Regular maintenance and deep repair
- Deep inspection of hydraulic components:
- Disassemble and clean the hydraulic filter, hydraulic pump and cylinder at regular intervals to ensure that there is no sediment and particles inside.
- Use testing instruments to monitor the sealing, response time and output efficiency of the hydraulic system, and adjust or replace parts with performance degradation in time.
- Electronic control system verification:
- Regularly update the control software and calibrate the sensor to ensure the accuracy of data feedback.
- Perform pressure tests on key control modules to ensure stable operation under high load.
Seasonal and special working condition maintenance
- Winter antifreeze and preheating:
- For low temperature environments, use special low-temperature hydraulic oil and lubricating oil, and preheat the equipment in advance if necessary to ensure smooth start-up.
- Check the performance of the battery and electronic control system at low temperatures to prevent the sensor response from being affected by low temperatures.
- Summer heat dissipation and cooling:
- Strengthen the cleaning and inspection of the cooling system (such as radiators, fans and coolant lines) to prevent hydraulic oil deterioration and engine overheating due to high temperature.
- Monitor the temperature of the hydraulic system in real time, and reduce the risk of continuous high-load operation by adjusting the working rhythm and intermittent rest.
- Preparation before long-term shutdown:
- For equipment that is not used for a long time, clean the whole system, rust-proof it and apply necessary protective coating.
- Start and run the equipment regularly for a short time to check whether each system is normal to ensure that it is in good condition when it is used again.
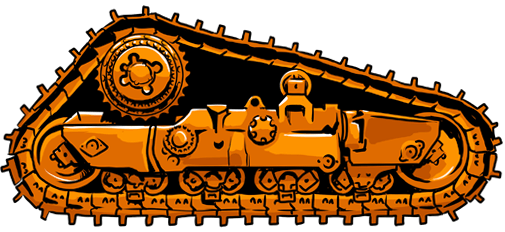
Future development trend
Intelligent and Internet of Things application
- Equipment interconnection and data collection:
- With the development of Internet of Things and 5G technology, excavators are gradually realizing the interconnection of various systems. Through real-time data collection and remote monitoring platform, managers can control the equipment status from a macro perspective, find problems in time and implement remote control.
- Artificial intelligence and predictive maintenance:
- Through the accumulation of massive operating data and combined with machine learning algorithms, the system can predict the wear and failure trends of key components, perform preventive maintenance in advance, reduce downtime rate and extend the service life of equipment.
Energy saving and environmental protection and hybrid technology
- Fuel injection and energy efficiency management:
- The application of a new generation of fuel injection system and hybrid technology enables excavators to significantly reduce energy consumption and emissions while operating efficiently. Optimizing combustion efficiency and power transmission not only meets environmental protection standards, but also improves operating efficiency.
- New materials and lightweight design:
- Using high-strength lightweight materials to reduce the weight of the equipment while ensuring safety, thereby reducing energy consumption and increasing mechanical response speed. This is not only conducive to construction efficiency, but also in line with the trend of green manufacturing.
Full life cycle management and information platform
- Digital full life cycle management:
- Using the enterprise resource planning (ERP) system and big data platform, the entire process of excavators from procurement, installation, use to maintenance is digitally managed to achieve precise control of cost and efficiency.
- Virtual reality and simulation technology:
- Through virtual reality, augmented reality (AR) and simulation platforms, engineers can simulate the operation of equipment under different working conditions in a virtual environment, thereby providing a scientific basis for design improvement and operation training.
Hızlı ve ücretsiz bir teklif alın | E-posta: henry@gfmparts.com | Whatsapp: +86 17705953659 |
Improving the efficiency of excavators is a systematic project involving equipment design, hydraulic and control systems, operating skills, environmental adaptation and comprehensive maintenance. By deeply analyzing the working principle, comprehensively evaluating various influencing factors, and combining intelligent monitoring and data management, accurate tuning and predictive maintenance can be achieved, which can not only improve operating efficiency, but also extend equipment life and reduce operating costs. For enterprises, focusing on customized equipment upgrades, technological innovations, and full life cycle management will be an important strategic direction to meet future competition in the construction machinery market.
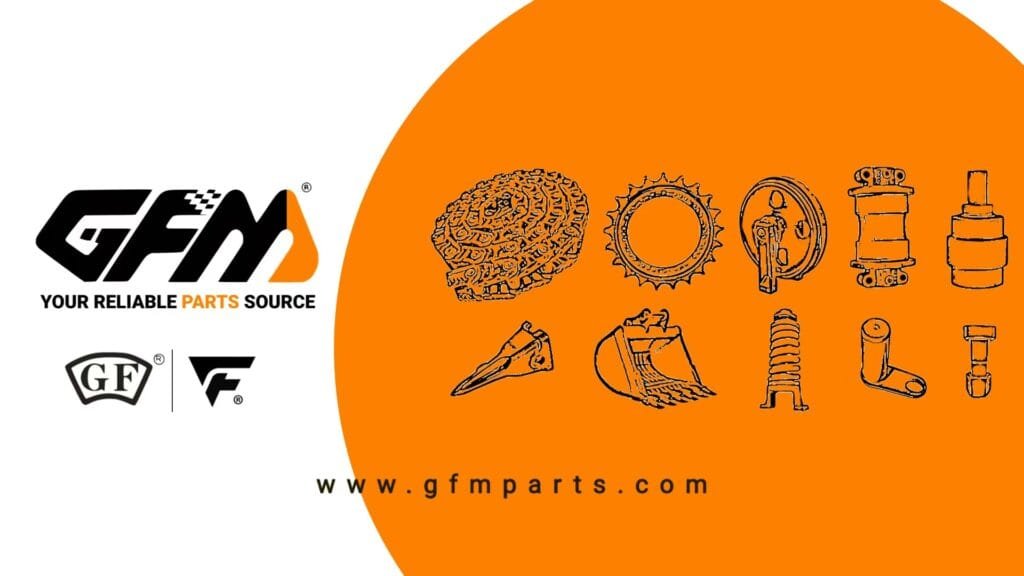