The excavator undercarriage part is the core component that bears the weight of the equipment and the impact of the operation. According to statistics, chassis system failures account for more than 35% of the total failures of excavators, and 80% of the failures are caused by failure to detect component wear in time. As an equipment manager, mastering the method of judging chassis wear can significantly reduce maintenance costs and extend service life.
Hazards and detection significance of excavator undercarriage wear
Excavator undercarriage part are subjected to ground impact, sand erosion and high-load friction for a long time. If the wear problem is not handled in time, it will lead to:
- The risk of track derailment increases by more than 40%
- The load of the travel motor increases, and the energy consumption increases by 15%-25%
- The balance of the whole machine decreases, and the upper structure is damaged
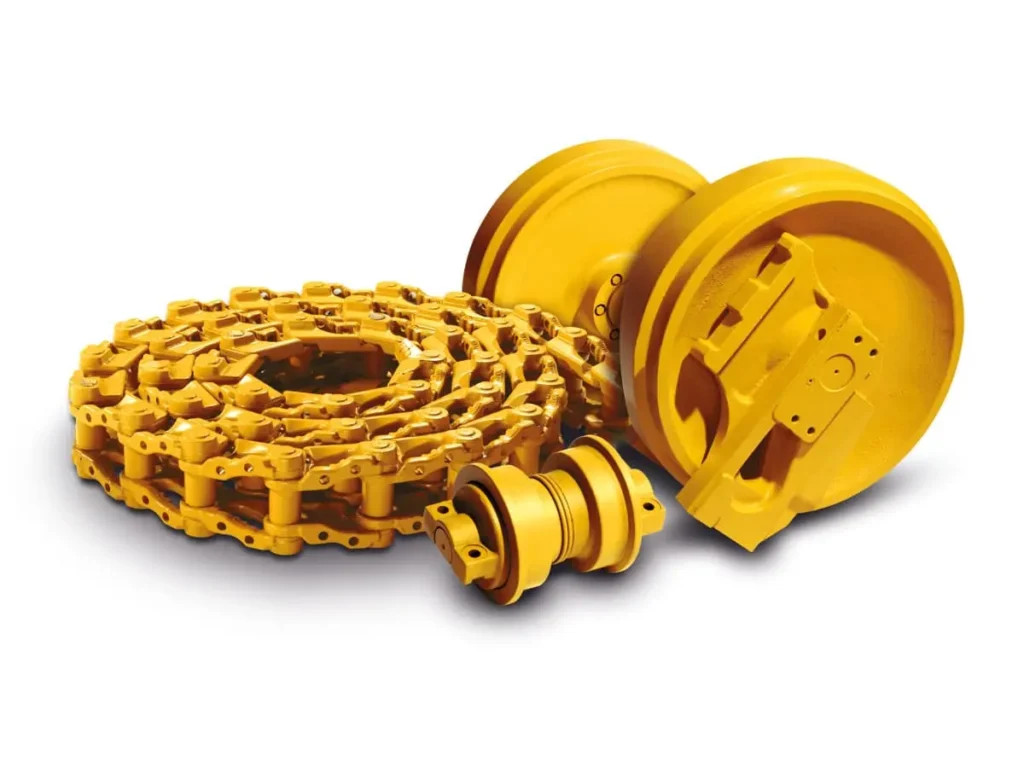
7 key components wear judgment and treatment solutions
Zincir dişlisi
Wear characteristics:
- The thickness of the tooth tip decreases by more than 30% of the original size (measured with a caliper)
- The tooth shape is asymmetrical, and obvious “hook-shaped” deformation appears on one side
- Metal scraping sound when the chain is engaged
Treatment plan:
- Replace the drive sprocket in pairs (to avoid mismatching between the new and old gears)
- Check whether the chain pitch exceeds the standard and replace the worn chain synchronously
Taşıyıcı Silindir
Wear characteristics:
- Rim thickness < standard value 8mm (refer to the equipment manual) Axial clearance > 2mm (shaking test)
- Periodic abnormal noise occurs when rotating
Solution:
- Use hydraulic jack to lift the chassis and then disassemble for inspection
- Replace the sealing assembly and add high-temperature lithium-based grease
- Replace the same-side supporting rollers in groups (it is recommended to check every 2000 hours)
Raylı Silindir
Wear judgment skills:
- The crack of the rubber guard ring exceeds 1/3 of the circumference
- Dents with a depth of >5mm appear on the surface of the wheel body
- The rotation resistance increases significantly during the idling test
Maintenance points:
- Clean up foreign objects such as gravel stuck in the wheel groove
- Use laser cladding technology to repair local wear (cost is 60% lower than replacement)
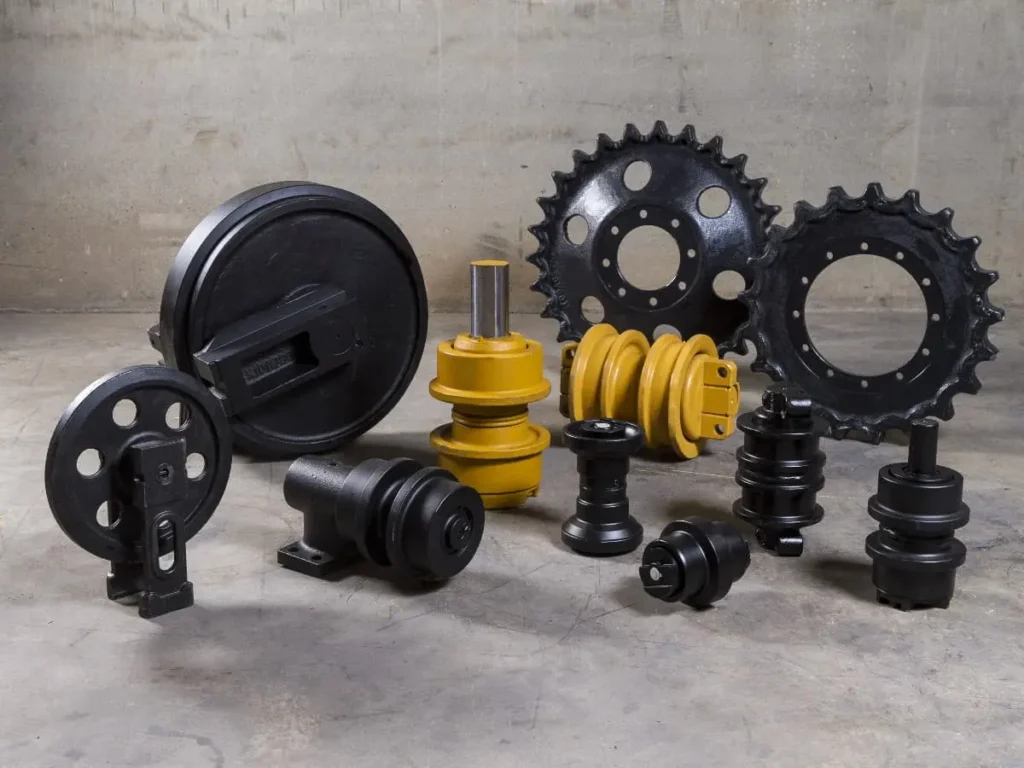
Koşu ayakkabısı
Wear classification standard:
- Light wear: The height of the grounding bar is reduced by <15% Moderate wear: The ovality of the pin hole is >3mm
- Severe wear: Penetrating cracks appear on the plate body
Adjustment suggestions:
- Turn over the track shoe regularly (applicable to double-sided design models)
- Use the track tension measuring instrument to keep the droop at 30-50mm
Idler Wheel
Abnormal signs:
- The wear on the inner side of the wheel rim is greater than twice the wear on the outer side
- The adjustment screw has reached the limit position but still cannot be tightened
- The temperature of the wheel shaft bearing exceeds 80℃ (detected by infrared thermometer)
Solution:
- Correct the installation flatness of the guide wheel bracket (error <0.5mm/m)
- When replacing, give priority to upgraded models with wear-resistant coatings (such as GFM’s WC-Co tungsten carbide coated guide wheels)
Drive Wheel
Failure warning signs:
- Radiating cracks appear at the root of the gear teeth
- The peeling area of the tooth surface hardening layer is greater than 10%
- High-frequency vibration occurs when meshing with the chain
Technical specifications:
- It is forbidden to mix drive wheels from different batches
- A 50-hour running-in period monitoring is required after installation
Undercarriage Frame
Structural damage detection:
- Use magnetic particle inspection to detect cracks (focus on the heat affected zone of welding)
- Diagonal size deviation > 3mm/m (need to be measured with a total station)
- Fixing bolt preload loss > 20%
Repair specifications:
- Cracks exceeding 5mm must be repaired by welding
- Use stress release tooling to prevent secondary deformation
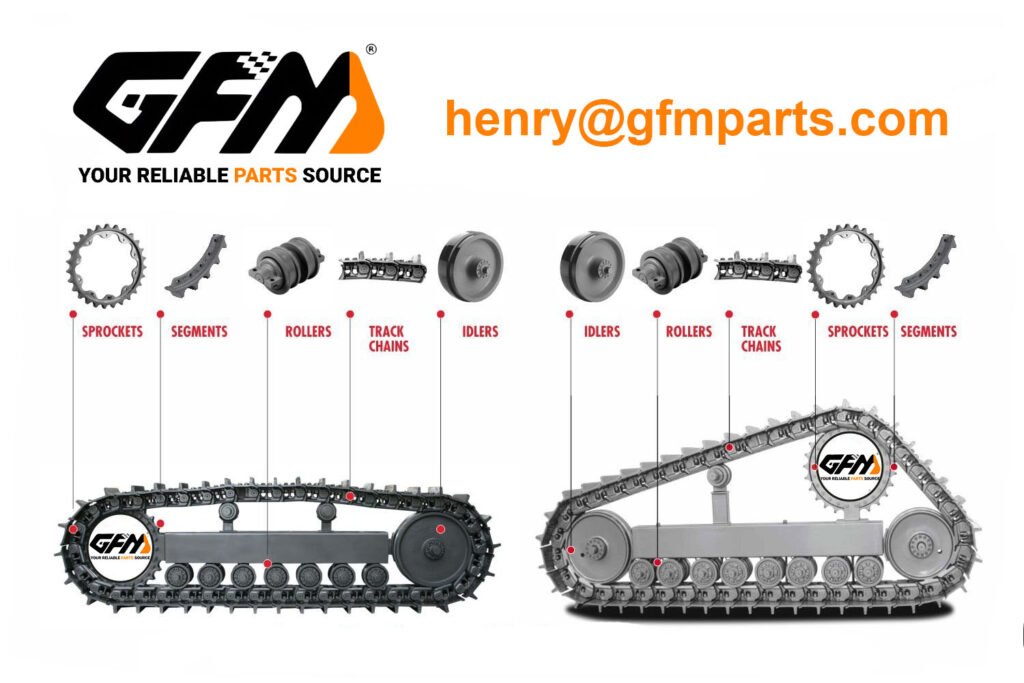
3 golden rules to extend the life of the undercarriage
Three-level maintenance system
- Daily inspection (8 hours/time) + monthly lubrication + annual comprehensive disassembly and inspection
Working condition matching principle:
- Use reinforced sealed support wheels for rocky working conditions
- Widened track shoes for swamps (more than 900mm)
Data management
- Establish a replacement file for worn parts and use IoT sensors to monitor real-time loads
Hızlı ve ücretsiz bir teklif alın | E-posta: henry@gfmparts.com | Whatsapp: +86 17705953659 |
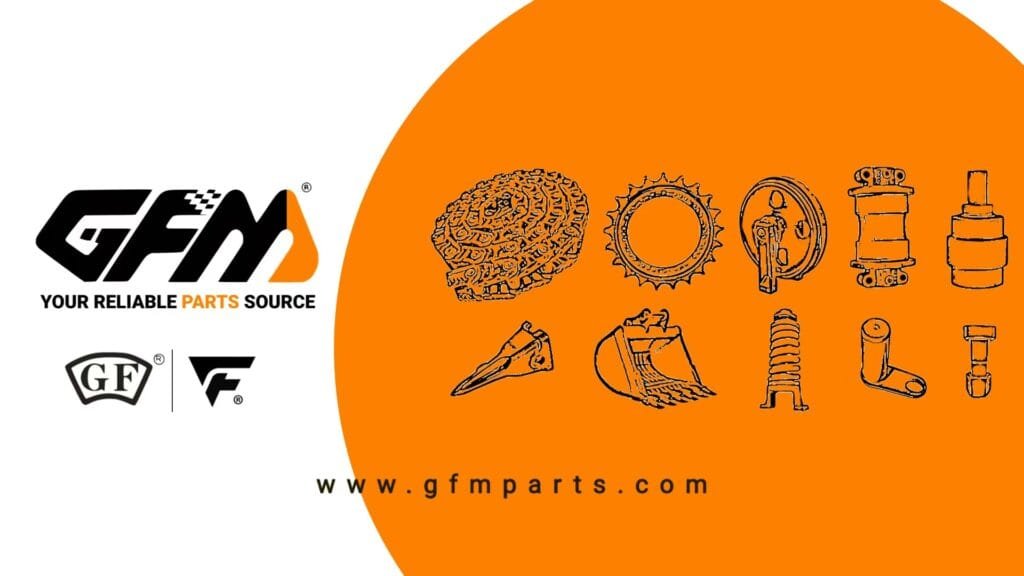