In the field of construction machinery, the undercarriage parts of excavators are the key to the stable and safe operation of the equipment, and the level of storage management directly affects its performance, life and subsequent maintenance costs. The following is a set of detailed and specific operation steps, from warehouse planning to outbound management, to ensure that each ekskavatör alt takım parçaları can be stored in the best condition, extend the service life and reduce maintenance costs.
Warehouse design and environmental control
- Warehouse site selection and layout planning
- Site selection requirements: Choose an area away from humid and highly corrosive environments, and give priority to factory areas or warehouse areas with good ventilation and convenient transportation.
- Regional division: Divide the area according to the type of parts (such as heavy components, precision components) and storage environment requirements (temperature, humidity); set up acceptance areas, storage areas, inspection areas, outbound areas and safety monitoring areas.
- Environmental control facilities
- Temperature and humidity system: Install temperature and humidity sensors and automatic control equipment to ensure stable temperature (for example, 18℃~25℃) and moderate relative humidity (40%~60%) in the warehouse.
- Ventilation and dust prevention: Arrange high-efficiency filtering ventilation equipment and air purification systems, clean the filter regularly; use dustproof doors and sealed packaging to reduce external pollution.
Physical protection
- Reasonable support and fixing design
- Special brackets and shelves: According to the weight and volume of parts, standardized pallets and shockproof brackets are used to ensure that the parts are not deformed due to their own weight or external forces during long-term storage.
- Partition storage: Undercarriage parts of different specifications and materials should be stored in partitions, which is convenient for quick positioning and can avoid mutual collision and damage.
- Anti-collision and anti-shock measures
- Anti-collision protection: Reserve enough space in the warehouse layout, install anti-collision pads or buffer devices to reduce mechanical shock during transportation.
- Anti-seismic facilities: Especially for precision components, anti-seismic packaging materials and anti-seismic bottom plates are required to reduce micro-damage caused by vibration during transportation and storage.
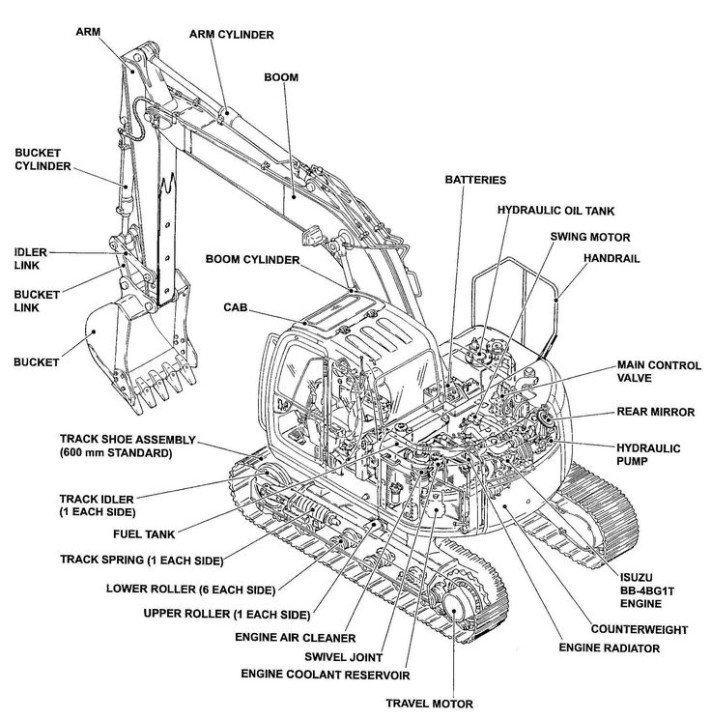
Warehouse operation process
Receiving and acceptance stage
- Receiving inspection
- Record information: After receiving the parts, record the cargo number, arrival date, part specifications, quantity and outer packaging status.
- Appearance inspection: Check the anti-rust coating, packaging integrity and whether there is any transportation damage to ensure that the status of the parts meets the warehousing standards.
- Data entry
- Digital management: Register to the ERP or WMS system through barcode or RFID scanner to realize information tracking.
- Take photos and keep records: Take photos of defective or questionable parts to provide a basis for subsequent processing.
Cleaning and pretreatment
- Cleaning treatment
- For parts with stains or slight rust on the surface, use professional cleaning agents and tools to clean them.
- After cleaning, dry them to avoid secondary rust caused by residual moisture.
- Protective measures
- Apply anti-rust oil or preservatives, and apply secondary protective coating to parts prone to corrosion.
- For precision parts, use anti-static packaging materials and sealed bags for packaging.
Classification and identification
- Partition storage
- Classify and store according to part type, model, weight and size. Heavy parts are placed on the lower shelf, and precision components are arranged in areas with stricter environmental control.
- Each storage area should have a clear sign to facilitate quick identification by operators.
- Labeling and Coding
- Paste a barcode or RFID tag on each part or package. The label content includes the part code, arrival date, storage location and protection information.
- Enter the warehouse management system to ensure that each part can be located and tracked in real time.
Storage and Placement
- Physical Placement
- Use standardized shelves, pallets and shockproof brackets to place parts reasonably according to the size of the parts. Ensure that the shelf load-bearing capacity is reasonable and heavy parts are evenly distributed on the pallet.
- Precision components use shockproof packaging boxes and cushioning materials are placed on the pallet to avoid direct contact with the hard bottom plate.
- Fixation and Protection
- For parts that are prone to displacement, use straps, brackets or anti-slip pads for auxiliary fixation.
- Ensure that there is enough safety distance between parts to prevent damage caused by collision.
Warehouse Environment Management
- Real-time Monitoring
- View the warehouse temperature, humidity and ventilation status in real time through the central monitoring system, and automatically alarm when abnormal.
- Arrange special personnel to patrol daily, check the equipment operation status and environmental data records, and ensure that all control equipment is working properly.
- Regular maintenance
- Maintain and calibrate temperature and humidity sensors, ventilation systems and dehumidification equipment every week, and clean dust prevention facilities regularly.
- Develop and implement warehouse safety inspection plans, and regularly inspect fire equipment, monitoring equipment and access control systems.
Regular inspection and maintenance
- Inventory count
- Develop a detailed periodic inventory count plan (such as once a month), check the warehouse management system data with the actual inventory, and make timely adjustments if abnormalities are found.
- Check the status of parts that have been stored for a long time, and take cleaning and secondary protection measures immediately if rust or deformation is found.
- Environmental records
- Generate environmental monitoring reports daily, weekly and monthly, record temperature and humidity changes, protective equipment use, etc., and form a closed-loop management record.
- Hold warehouse management meetings regularly to evaluate operating procedures and discuss improvement measures.
Outbound management
- Order processing
- Retrieve the corresponding parts information from the system according to customer orders, and arrange outbound delivery after confirming the inventory status.
- Perform a final appearance inspection before outbound delivery to ensure that the part status meets the transportation requirements.
- Packaging and distribution
- Re-pack the outgoing parts with protective packaging (such as shockproof and moisture-proof packaging), and indicate the outgoing date and customer information on the packaging.
- Arrange a dedicated person to supervise the outgoing loading process to ensure that the parts will not be damaged by collision or vibration during loading and unloading.
- Update the inventory information in the ERP/WMS system to achieve real-time synchronization of data.
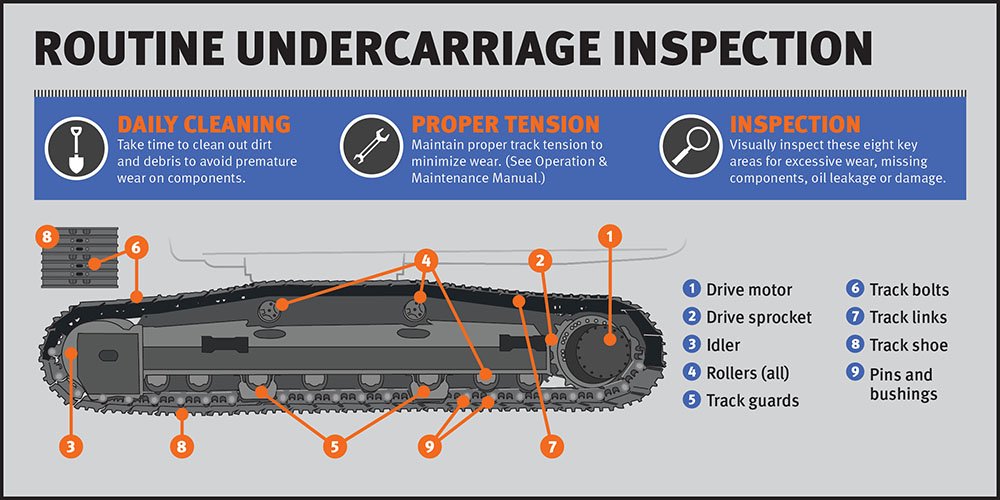
Warehouse safety and emergency management
- Safety protection
- Install 24-hour surveillance cameras, access control systems and alarm devices to prevent theft and accidents.
- Develop a fire emergency plan, organize fire drills every quarter, and ensure that all warehouse personnel are familiar with the emergency evacuation process.
- Emergency plan
- Set up a rapid response mechanism for emergencies such as abnormal temperature and humidity, fire, etc., and assign responsibilities to individuals.
- Establish an accident reporting and handling mechanism to ensure that every emergency situation is recorded, and formulate preventive measures to prevent recurrence.
Intelligent and information management
- Warehouse management system (WMS)
- Real-time management of inventory data, storage location and operation records, and realize automatic replenishment warning and abnormal situation feedback.
- The system supports barcode/RFID scanning to help staff quickly locate and retrieve part information.
- Data Analysis
- Use system data to analyze the frequency of parts entering and leaving the warehouse, storage time and environmental data, and optimize warehouse layout and management processes.
- Generate data reports regularly as a basis for decision-making on warehouse safety, efficiency improvement and inventory optimization.
- Training and Feedback
- Regularly conduct professional training for warehouse operators to ensure that all processes and system operations are accurate.
- Establish an internal feedback mechanism to promptly collect problems found during operation and continuously improve warehouse management processes.
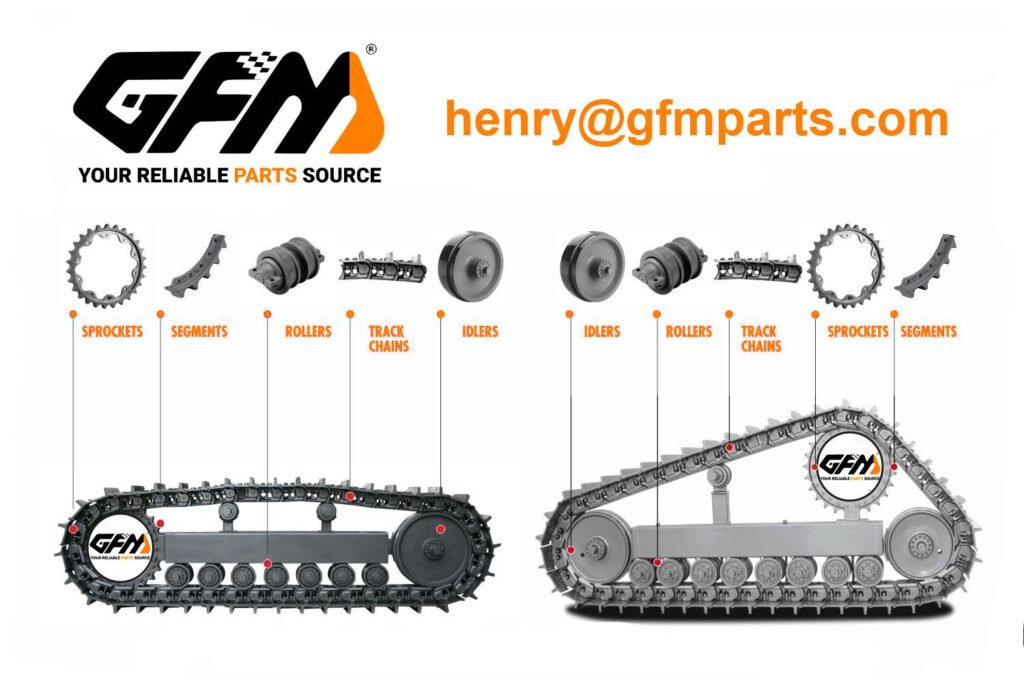
Selection of storage equipment
- Storage facilities
- Automated stereoscopic warehouse: The application of modern automation systems not only saves labor costs, but also improves the efficiency and accuracy of parts storage and retrieval.
- Intelligent environmental control system: Integrate temperature and humidity monitoring, alarm and control equipment to ensure that the warehouse environment always meets storage requirements.
- Customized protection tools
- Anti-corrosion and anti-rust technology: Apply special anti-corrosion coatings on the surface of parts, and use anti-rust oil and protective covers to further isolate environmental factors during storage.
- Special handling equipment: Use robotic arms, automatic guided vehicles (AGVs) and other equipment to reduce the risk of collision during handling and ensure that parts are safe and intact.
Hızlı ve ücretsiz bir teklif alın | E-posta: henry@gfmparts.com | Whatsapp: +86 17705953659 |
The storage quality of excavator undercarriage parts can be greatly improved through clear and detailed warehouse design, partitioned storage, strict warehousing and outbound processes, and intelligent management systems. Standardized operating procedures not only protect parts from environmental and physical damage during storage, but also significantly reduce corporate operating costs and improve overall service quality. GFM excavator parts manufacturer can rely on this system to create an efficient, safe, and digitally managed warehouse environment to provide customers with more reliable spare parts support and service guarantees.
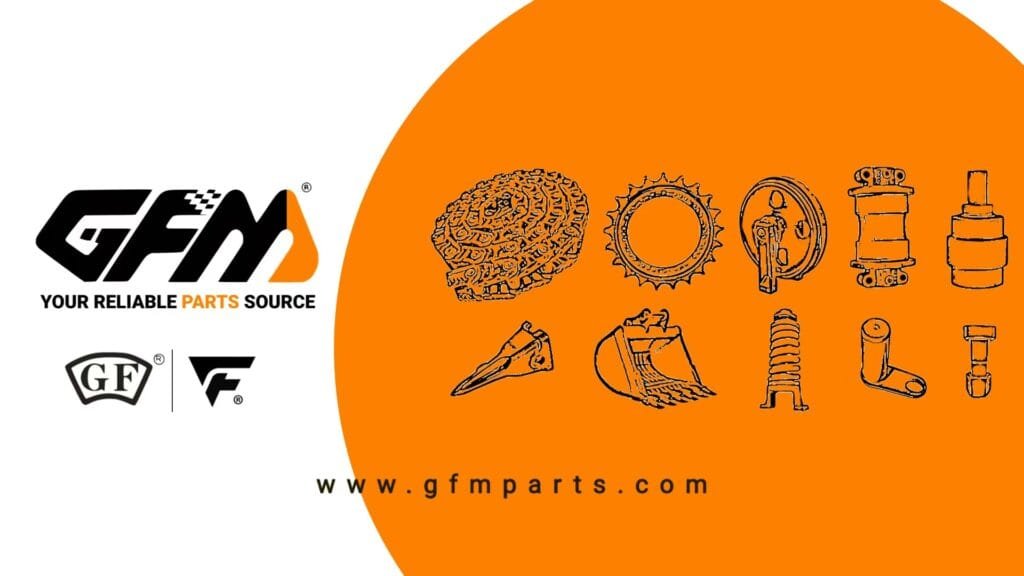