Table of contents
- Excavator Site Risk Assessment and Preparation
- Safety inspection process before excavator operation
- Recommendations for personal protective equipment and safety tools for excavators
- Tips for safe operation of excavator construction sites
- Excavator emergency response and rescue plan
- Excavator safety training and continuous improvement experience sharing
In the world of excavators, every shovel, every take-off and landing is full of the power of the operator’s skills and equipment. But no matter how experienced or safe we are, we cannot ignore the possibility of “accidents happening inadvertently”. As a manufacturer of ekskavatör alt takım parçaları, GFM has many years of experience in parts manufacturing, has witnessed the risks in various operating environments, and has accumulated first-line safety practical skills.
In this safety guide, we will use the most friendly way to accompany you from assessment preparation, inspection process, personal protection, to operating skills, emergency rescue, and training improvement, to build your “zero accident” defense line in all aspects. Whether you are a novice who has just entered the industry or an old driver who has been driving for many years, you can find easy-to-learn and easy-to-use practical suggestions here, making every operation of yours safer and more efficient than yesterday.
Excavator Site Risk Assessment and Preparation
Before any excavator operation begins, a comprehensive risk assessment of the site must be conducted. This step not only protects the operator and ground workers, but also effectively reduces the accident rate. According to OSHA data, the number of worker deaths caused by collapse in the United States in 2023 dropped from 39 in 2022 to 15, a decrease of nearly 70%. Here are two key links to help you be foolproof in the “Excavator Site Risk Assessment”:
- Pre-task plan
- Use the official PTP template or CPWR tool list to confirm each work process and potential hazard one by one.
- Analyze the geological conditions (such as soil type, groundwater level) and the surrounding environment (high-voltage lines, pipe networks) to develop targeted plans.
- Site inspection and marking
- Use 3D laser ranging or drone aerial photography to quickly obtain a three-dimensional model of the site.
- Draw fluorescent warning lines in high-risk areas and set up movable safety warning stakes to remind all personnel to keep a safe distance.
- Develop an emergency plan
- Prepare an “escape route map” and a “rescue flow chart” for common risks such as landslides, water surges, and cable ruptures.
- Clarify the emergency responsible person and contact information to ensure that any abnormality can be supported in the first time.
Through these preparations, your team can foresee and control more than 80% of common on-site risks in advance, making “excavator on-site safety” no longer just a slogan, but a real and feasible action.
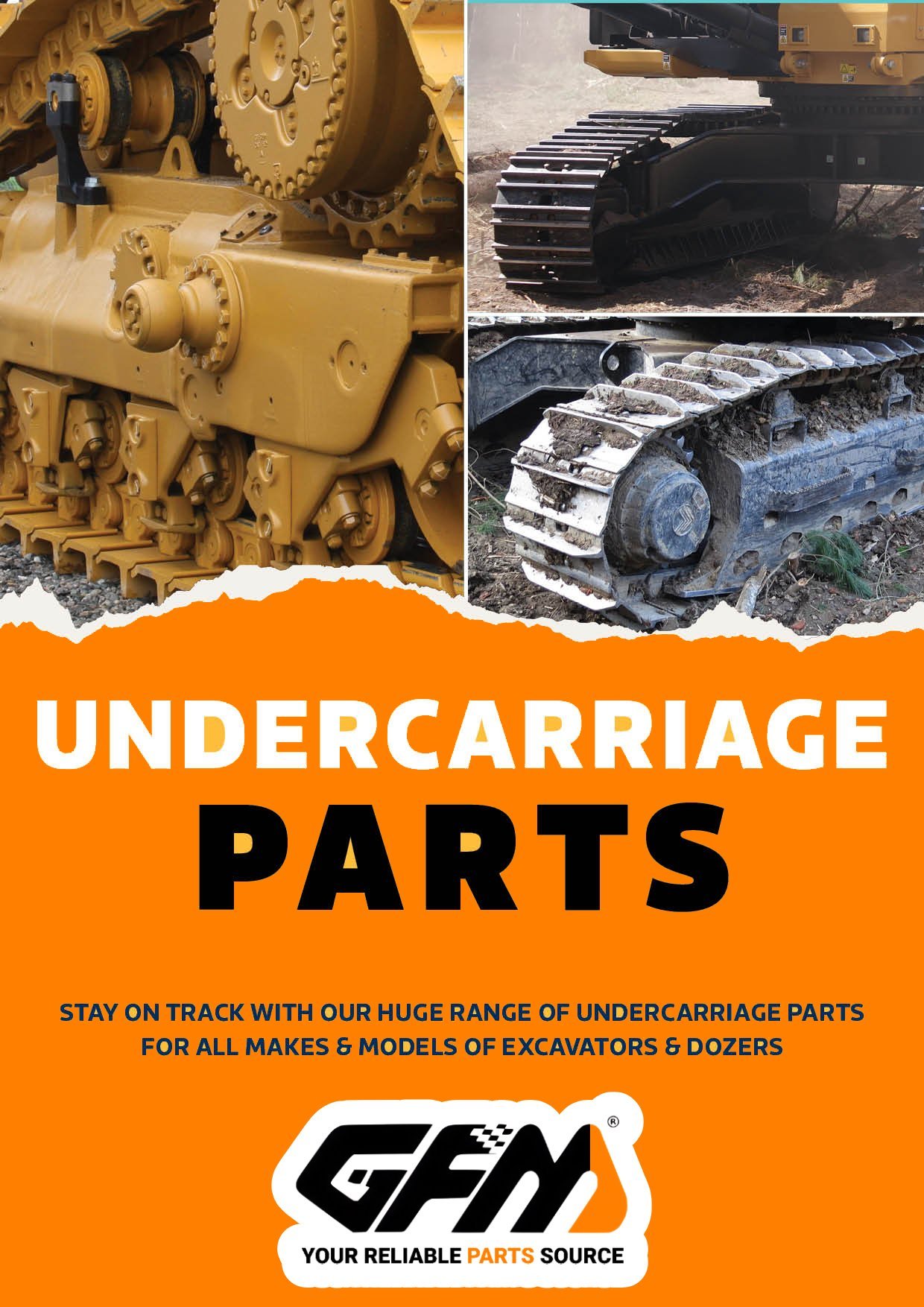
Safety inspection process before excavator operation
“Thorough inspection, safe operation” is the core rule of excavator on-site safety. The following “five-step inspection method” can help you know every step before “excavator operation” to avoid equipment failure or safety hazards:
- Hydraulic system detailed inspection
- Measure the oil level and oil temperature to ensure that the hydraulic oil is not emulsified or contaminated.
- Use a pressure gauge to compare the manufacturer’s standard value, and replace the filter element or upgrade the seal in time if abnormalities are found.
- Engine and transmission system inspection
- Check the status of the engine oil and coolant, and pay attention to whether the water tank is corroded or leaking.
- Listen to the engine idle speed, pay attention to shaking, abnormal noise or abnormal exhaust color.
- Lubrication of hinges and pins
- Apply high-performance lithium-based grease to ensure smooth operation of components such as booms and buckets.
- Check for cracks, looseness or metal fatigue, and replace pins or strengthen welding if necessary.
- Safety device and warning system test
- Press the emergency stop button to confirm that the hydraulic system is quickly cut off from oil;
- Check whether the reversing buzzer, warning lights and cameras are operating normally.
- Electronic circuit and lighting system verification
- Ensure that there is no fault light on the dashboard and the data is read accurately;
- Before working at night, test all headlights, taillights and site lights.
Recording each inspection in an electronic log or mobile APP is not only convenient for subsequent tracing, but also provides data support for manufacturer maintenance and parts replacement. In this way, the “excavator safety inspection process” becomes the “safety key” for you to communicate with the equipment.
Click to learn more about the excavator work safety guide: DEVAMINI OKU
Recommendations for personal protective equipment and safety tools for excavators
“Wear the right equipment and use the right tools” is the basic protection principle for every machine operator and ground worker. At the level of “excavator personal protective equipment”, the following list will help you build a comprehensive protection barrier:
- Head protection
- Safety helmets that meet the EN397/GB2811 standard;
- Add ear protection and mask accessories to prevent noise and splash injuries.
- Body and sight safety
- High-visibility reflective vests with built-in multi-pocket design are convenient for carrying commonly used tools;
- Protective goggles or full-face protective masks to isolate flying chips and dust.
- Hand and foot protection
- Abrasion-resistant and cut-resistant gloves, as well as pressure-resistant steel-toed safety boots;
- Anti-puncture soles that have passed the steel sheet insertion and extraction test.
- Professional safety tools
- Portable gas detectors: monitor the concentration of gases such as carbon monoxide and methane to prevent poisoning incidents.
- Adjustable three-legged safety support: acts as an emergency support or climbing ladder when working in deep trenches or slopes.
- Laser rangefinder: measures trench depth and obstacle distance in real time to improve measurement accuracy.
These “standard protective equipment” are not only recommended by the industry, but also the most direct and effective investment to ensure “excavator site safety”. Spending a little less may save one more life; spending a little more is responsible for the team.
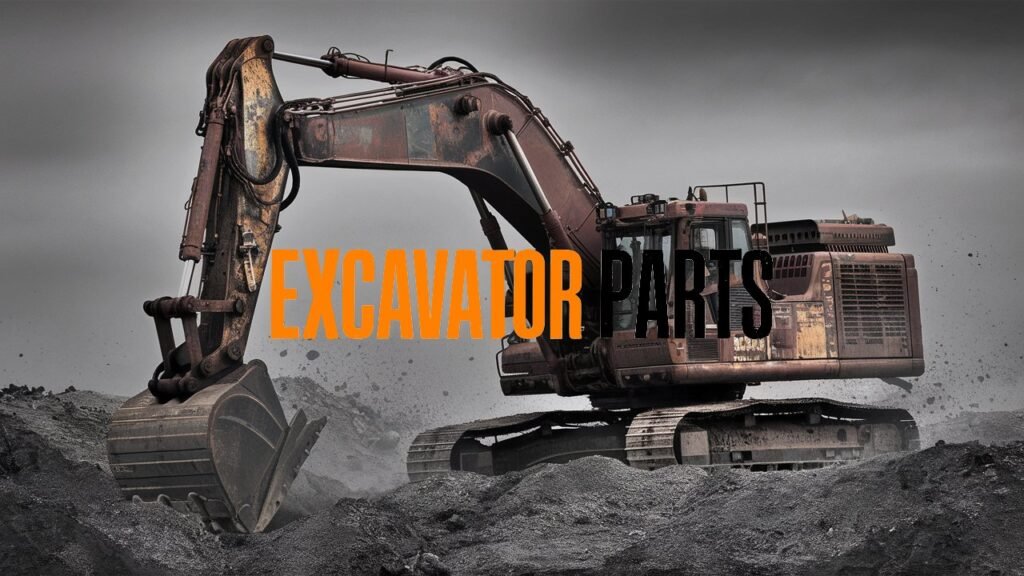
Tips for safe operation of excavator construction sites
After mastering the inspection process and equipment, the next step is “explorer construction site safety operation skills”, which are like “safety secrets” that can make your operation efficient and safe:
- Smooth start and stop to reduce inertial impact
- The engine speed increases smoothly from low to high, and then slowly releases the clutch.
- When stopping, first neutralize, tighten the handbrake, and finally turn off the engine.
- Dig in layers to prevent soil wall collapse
- The depth of each excavation is controlled at 0.5-0.7 meters.
- Unload the soil in layers and clean it up in time to keep the slope stable.
- Blind spot management and signalman cooperation
- Install a 360° panoramic camera system to reduce the side and rear blind spots.
- Equip professionally trained signalmen to guide the operator through walkie-talkies or gestures.
- Safety radius and obstacle warning
- Set up guardrails or mobile warning posts outside the operating radius of the excavator.
- Turn on the sound and light alarm to warn in time when people or equipment approach the dangerous area.
- Maintain a good field of vision and trench drainage
- Clear the lighting blind spots before operation and wipe the lens and lampshade regularly.
- When working in deep trenches or after rain, use a water pump to remove accumulated water to prevent mud and sand from softening the soil wall.
Flexible use of these “excavator safety operation skills” will not only allow you to navigate complex terrain with ease, but also greatly reduce the risk of work-related injuries.
Excavator emergency response and rescue plan
Even if everything is foolproof, you may encounter danger suddenly. Mastering the “excavator emergency response” process can ensure life safety at critical moments:
- One-button emergency stop and energy cut-off
- Immediately press the red emergency stop button to disconnect the hydraulic and power supply.
- Then pull down the main power switch to avoid malfunction of secondary equipment.
- Rapid personnel evacuation
- Guide the operator and on-site personnel to evacuate according to the evacuation route arranged in the plan.
- Turn off the power supply of other heavy machinery to reduce the secondary risks in the surrounding area.
- Initial rescue on site
- Use the on-board tripod support and safety rope for temporary support and rescue.
- If necessary, switch to hydraulic demolition tools to open an escape route for trapped personnel.
- First aid treatment and medical docking
- The on-site first aid kit is equipped with hemostasis, bandaging, and cardiopulmonary resuscitation equipment.
- Use the intercom or mobile phone positioning function to quickly call 120 or a professional ambulance.
- Accident investigation and knowledge accumulation
- Protect the traces on the scene, take photos, record videos, and record time, personnel, weather, etc.
- Write an “accident investigation report” afterwards, summarize lessons, and update risk assessment and training materials.
Through the standardized “excavator emergency rescue process”, injuries can be minimized within a limited time and valuable data can be provided for future continuous improvement.
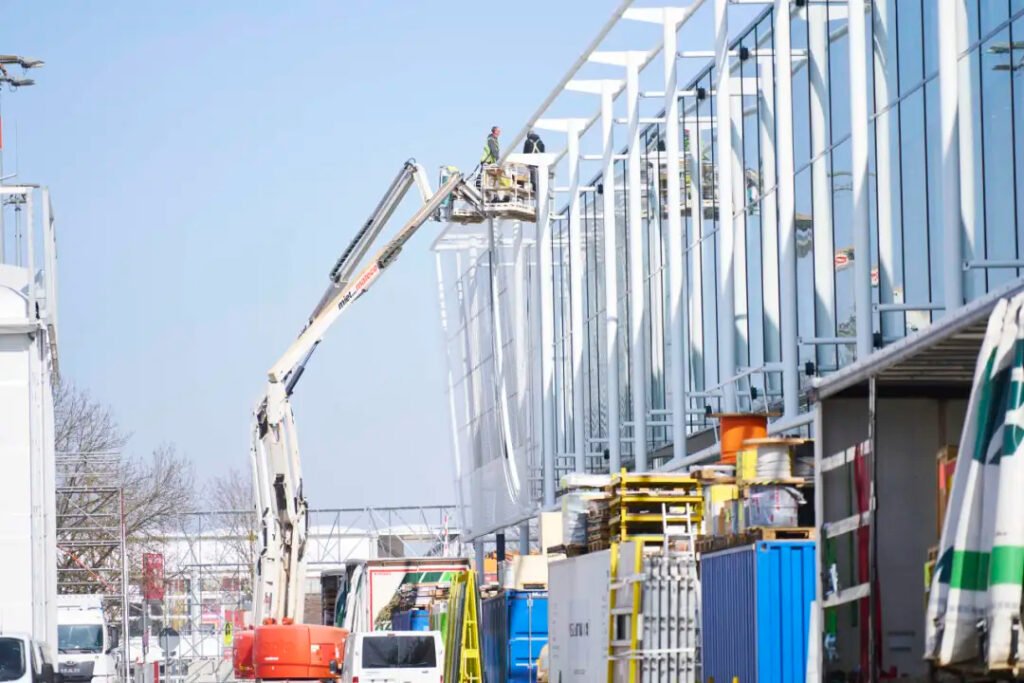
Excavator safety training and continuous improvement experience sharing
The construction of safety culture is inseparable from the continuous investment of “excavator safety training and experience sharing”. The following methods can help your team form a closed loop of “learning-practice-evaluation-correction” and continuously improve the safety level:
- Regular safety drills and simulations
- Organize a simulation drill with full participation every quarter, covering landslides, leakage, fire, etc.
- Combined with VR or AR technology, let novices practice in a virtual environment to reduce the risk of misoperation by beginners.
- External resources and standards docking
- Pay attention to the latest OSHA regulations (such as 29 CFR 1926.652) and update the operation guide in a timely manner.
- Invite industry experts or third-party safety assessment agencies to conduct regular audits and make improvement suggestions.
- Performance appraisal and incentive mechanism
- Incorporate zero accidents or the adoption of safety suggestions into personal performance, and give bonuses or honorary certificates.
- Establish a “Safety Star” commendation system to encourage employees to actively discover and report hidden dangers.
- Experience closed loop and knowledge base construction
- After each training and drill, a concise “safety work summary” is generated and uploaded to the internal knowledge base.
- Through monthly safety meetings, real cases and improvement results are shared to allow experience to settle within the team.
Hızlı ve ücretsiz bir teklif alın | E-posta: henry@gfmparts.com | Whatsapp: +86 17705953659 |
Through the above methods, you can not only improve the execution of “excavator site safety”, but also establish the brand image of GFM excavator parts manufacturer as a professional and reliable partner in the industry. Let us start from today and regard every training and drill as an important step towards the goal of “zero accidents”!
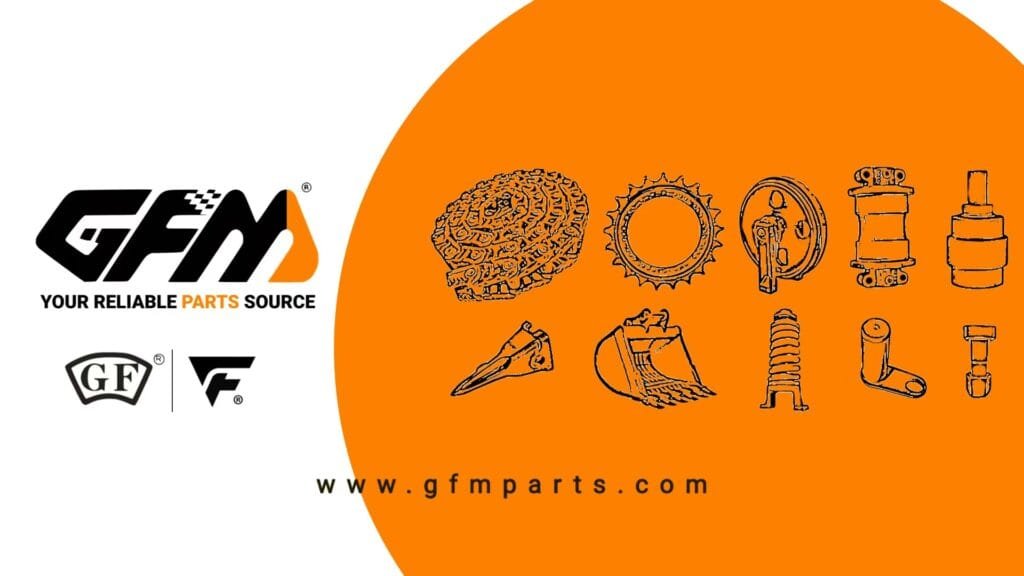