Table of contents
- Common safety hazards in excavator operation
- Safety inspection steps before excavator work
- Required qualifications and training for excavator operators
- Key measures to effectively prevent excavator operation accidents
- Safety management strategy for excavator work sites
- Emergency handling process for excavator safety accidents
- Summary: The road to continuous improvement in excavator safety work
In construction and engineering projects, excavators are important representatives of heavy machinery and equipment, and their safe operation is directly related to the life safety of workers and the smooth progress of projects. According to the 2023 Machinery Industry Production Safety Accident Analysis Report, there were 310 production safety accidents in the machinery industry, killing 294 people, among which mechanical injuries, object strikes and falls from heights were the most common types of accidents. This article will comprehensively explore the key aspects of excavator work safety, including safety hazard identification, preventive measures and necessary training requirements, to help relevant practitioners establish safety awareness and reduce accident risks.
Common safety hazards in excavator operation
As a large-scale construction machinery, there are many safety hazards in the operation of excavators. Understanding these potential risks is the first step to prevent accidents. The following are several aspects that need to be focused on:
Risk of boom operation: The boom of the excavator is one of the parts that are most likely to cause personal injury. When operating an excavator, in order to prevent workers from being hit by the boom, the operator should rotate the boom at a safe speed. In addition, the blind spot of the boom is also an important risk point. The operator’s line of sight may not cover all working areas, increasing the risk of collision.
Mechanical injury risk: According to accident statistics in 2023, mechanical injuries account for the highest proportion of accidents in the machinery industry. The crawler, hydraulic system and other moving parts of the excavator may cause injuries such as squeezing and entrapment. Especially when repairing or inspecting equipment, the risk will be greatly increased if the energy is not properly locked or the dangerous parts are not isolated.
Rollover and stability issues: There is a risk of rollover when the excavator is operating on uneven ground, slopes or soft soil. Such accidents usually have serious consequences and may cause the operator to be trapped or seriously injured. Improper load distribution and overloading operations also increase the possibility of rollover.
Electrical and underground facility hazards: Excavators may come into contact with underground or overhead cables during work, causing electric shock accidents. According to accident statistics, electric shock is the fourth type of accident in the machinery industry, and it is particularly necessary to be vigilant in excavator operation.
Risks in auxiliary operations: Equipment inspection and maintenance operations are the link with the highest accident rate in the auxiliary production process. This is mainly due to the nature of temporary operations, the lack of fixed safety processes, and insufficient hazardous energy control measures. In the process of excavator maintenance, related risks need special attention.
Identifying and understanding these safety hazards is the basis for developing effective safety measures. Only by fully recognizing the potential risks can targeted prevention and training be carried out to reduce the accident rate.
Safety inspection steps before excavator work
Before starting to operate the excavator, a systematic safety inspection is a key link in preventing accidents. The following is a comprehensive set of safety inspection steps before excavator work, which should be strictly followed by every operator:
Equipment basic inspection: First, a comprehensive inspection of the excavator itself is required, including checking whether there are leaks in the hydraulic system, confirming whether the fuel and lubricating oil levels are normal, checking the cooling system function, checking the condition of the tracks or tires, and confirming that all protective covers and safety devices are intact. These basic inspections can timely detect hidden dangers that may cause equipment failure.
Operation control system inspection: Test the sensitivity and responsiveness of all control levers and buttons, ensure that the braking system functions properly, verify that the indicator lights and warning systems are working properly, test the effectiveness of the horn and reversing alarm device, and check whether the movement of the excavator boom and bucket is smooth and unobstructed. The reliability of the control system is directly related to the accuracy and safety of the operation.
Work environment assessment: Clear obstacles and unnecessary personnel from the work area, mark the location of underground pipelines and cables, assess ground conditions (pay special attention to high-risk areas such as soft soil and slopes), check the work area for overhead obstacles such as wires or branches, and ensure that the work area has adequate lighting and appropriate safety signs. Environmental assessment can prevent accident risks related to external factors.
Safety protection equipment inspection: Confirm that the fire extinguisher in the cab is in good condition and easy to access, check whether the first aid kit is complete, ensure that personal protective equipment is complete (such as hard hats, reflective vests, etc.), verify that the seat belts are functioning properly, and check whether the communication equipment is working properly. These equipment are the last line of defense to protect the operator’s safety in the event of an accident.
Document and qualification verification: Confirm that the operator’s manual is available on the machine, check the latest maintenance records of the equipment, confirm that the operator has a valid operating certificate, check the necessary safety work permits, and review the relevant safety operating procedures. Document and qualification inspections can ensure that the operation is compliant and the operator has the necessary capabilities.
Making these inspection steps into a standardized checklist and requiring the operator to confirm each item one by one before each operation can effectively prevent missed inspections and negligence. Managers should review inspection records regularly to ensure that inspections are not perfunctory. By strictly implementing these safety inspection steps, equipment failure and operation risks can be significantly reduced, laying a solid foundation for safe operation.
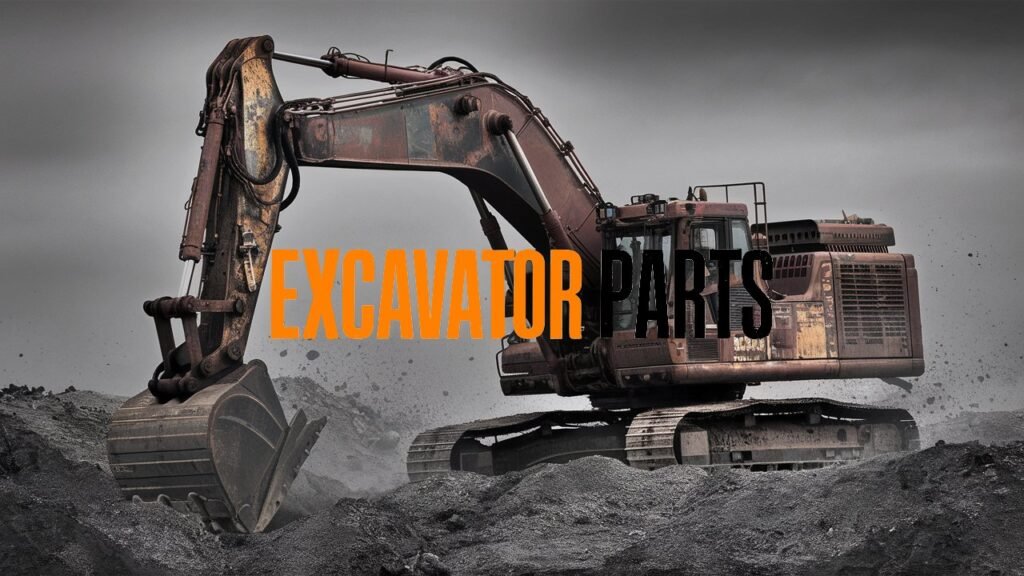
Required qualifications and training for excavator operators
Excavator operation is a job that requires professional skills and safety awareness. Appropriate qualification requirements and training systems are essential to prevent accidents. The following are the qualifications and training requirements that excavator operators must have:
Basic qualification requirements: Excavator operators must be at least 18 years old and hold a valid relevant certificate. This is not only a legal requirement, but also a necessary condition to ensure that operators have basic maturity and sense of responsibility. In addition, operators need to pass a physical health examination to ensure that their vision, hearing and other aspects meet the requirements for safe operation, and they need to have basic mechanical knowledge and understanding.
Professional skills training content: Operator training should cover a detailed understanding of the structure and functions of the excavator components, the operating skills and response characteristics of various control devices, the operating skills under different working conditions (such as slopes, soft ground, etc.), professional knowledge of special operations (such as lifting, fine excavation, etc.), and the identification and basic troubleshooting methods of common equipment failures. This professional knowledge is the basis for safe and efficient operation.
Focus of safety awareness training: Safety training should emphasize the ability to identify hazardous areas at work, effective communication methods and signal systems with ground staff, correct response procedures in emergency situations, knowledge of the use and maintenance of safety devices, and the impact of weather and environmental factors on equipment operation. Safety awareness training helps operators establish a “safety first” work philosophy.
Accumulation of practical operation experience: After theoretical training, operators need to complete sufficient actual operation time under the supervision of experienced instructors, master the practical application of standard operating procedures, conduct simulation training under different working conditions and environments, acquire practical experience in daily maintenance and inspection of equipment, and participate in actual combat drills for emergency response. Practical experience is a necessary process for converting theoretical knowledge into practical operation capabilities.
Continuous education and skills update: Operators should regularly participate in safety refresher training and new technology training, learn the latest safety standards and operating specifications in the industry, analyze and learn typical accident cases, master the operating characteristics and safety requirements of new equipment, and regularly conduct operation skills assessment and certification updates. Continuous learning ensures that the operator’s knowledge and skills keep pace with the times.
Bir profesyonel olarak excavator parts manufacturer, GFM recommends that companies establish a systematic training system, including on-the-job training, job training, regular refresher training, and skill improvement training. A complete training system can not only improve the operator’s skill level, but also cultivate their safety awareness and sense of responsibility, and prevent safety accidents from the source.
Key measures to effectively prevent excavator operation accidents
Preventing excavator operation accidents requires the coordinated implementation of multiple safety measures. The following is a series of effective preventive measures that can significantly reduce the safety risks in excavator work:
Operational safety control: Excavator operators should rotate the boom at a safe speed and avoid sudden and rapid movements. Before operation, a comprehensive assessment of the work area should be conducted to identify potential hazards. Strictly follow the excavator load limit to avoid overweight operations. When working under poor visibility conditions, a signal commander should be equipped. It is prohibited to stand or pass within the working radius of the excavator. Stay focused during operation and avoid distraction. These basic operating rules are the first line of defense to prevent accidents.
Work environment safety management: Add fences in the excavator operation area to prevent workers from entering the operating range. Clearly mark the boundaries of the work area and safe passages, and set up sufficient warning signs and signs. Ensure that the work site is well drained to avoid stability problems caused by water accumulation on the ground. Provide adequate lighting when working at night, clean the work environment regularly, and remove obstacles that may cause accidents. Good environmental management can create conditions for safe operations.
Supervision and management measures: Arrange special personnel to supervise the operators and workers to ensure that they follow safety measures. Establish clear operating processes and safety regulations, and implement a work permit system, especially for high-risk work tasks. Conduct safety inspections and risk assessments regularly, and establish incentive mechanisms to encourage safe behavior and report potential hazards. The effective implementation of management measures depends on the attention and support of management.
Technical protection innovation: Ensure that the excavator is equipped with complete safety devices, such as rollover protection structures (ROPS). Install rearview cameras and alarm systems to reduce the risk of visual blind spots. Use intelligent anti-collision systems to automatically detect surrounding objects and personnel. Regularly maintain and update equipment safety components, and use accessories and consumables that meet safety standards. Technical protection measures can provide additional safety guarantees in the event of human negligence.
Personal protection and health protection: Ensure that the operator and surrounding staff wear appropriate personal protective equipment. Provide noise protection equipment to protect the operator’s hearing. Take heatstroke prevention and cooling measures when working in a hot environment. Equipped with appropriate communication equipment to ensure effective communication in emergency situations. Require all personnel to wear high-visibility clothing to increase the chance of being discovered. Personal protection is an indispensable component of the safety management system.
Training and awareness enhancement: In addition to basic operation training, safety awareness enhancement training should be organized regularly to share accident cases and lessons learned. Establish a “safety first” work culture and encourage operators to actively identify and report safety hazards. Organize safety knowledge competitions and skill competitions to increase employees’ enthusiasm for participating in safety management. Training and awareness enhancement are the key to long-term and effective accident prevention.
Comprehensive implementation of these preventive measures, and adjustment and improvement according to the specific working environment and conditions, can create a multi-level safety protection system, effectively reduce the risk of accidents in excavator operations, and ensure the safety of personnel and the integrity of equipment.
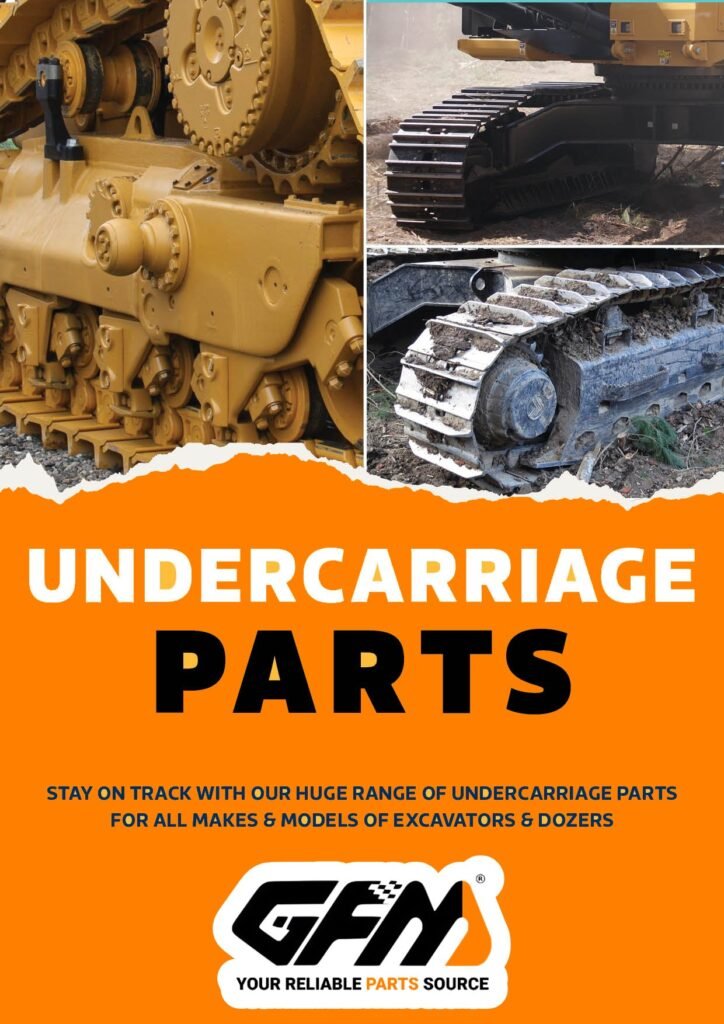
Safety management strategy for excavator work sites
Effective on-site safety management is a key component in preventing excavator work accidents. The following is a set of systematic on-site safety management strategies that can help companies establish a safe and efficient excavator operating environment:
Construction of a safety responsibility system: clarify the safety responsibilities of managers and operators at all levels, and establish a system for signing safety production responsibility letters. Implement safety performance appraisals, link them with compensation and promotion, and ensure that each job position has a clear safety responsibility statement. Establish an accountability mechanism for safety violations to form a top-down safety responsibility chain. This responsibility system is the basic framework for safety management.
Risk assessment and hierarchical control: conduct a comprehensive risk assessment before the start of each project, and conduct special safety analysis for high-risk work tasks. Develop targeted risk control measures, update risk assessment results regularly, and adapt to changes in the working environment. Establish a risk level management system and take corresponding measures for different risks. Scientific risk management can foresee potential dangers and intervene in advance.
Optimization of communication and coordination mechanisms: ensure good communication with operators, understand and comply with all signals. Hold safety meetings regularly to discuss safety issues and improvement measures. Establish a coordination mechanism between excavator operators and ground staff, using standardized hand signals or wireless communication equipment. Set up a safety information bulletin board to issue safety reminders and requirements in a timely manner. Effective communication can prevent accidents caused by misunderstandings.
Inspection and supervision system improvement: Implement a daily safety inspection system for excavators and record the inspection results. Establish regular and irregular safety inspection mechanisms and arrange special personnel to supervise the operation process of the excavator. Regularly check the intact state of safety protection facilities and warning signs, and establish a safety hazard reporting and rectification tracking system. Strict supervision and inspection can timely discover and eliminate safety hazards.
Emergency plans and drills: Develop special emergency plans for excavator operations, clarify the handling procedures and responsible persons for various emergencies. Organize emergency drills regularly to improve the ability to respond to emergencies. Equip with necessary emergency rescue equipment and materials, and establish an accident reporting and investigation and analysis system. Summarize lessons learned from accidents and continuously improve safety management. Perfect emergency preparation can minimize losses when accidents occur.
Safety culture cultivation: Starting from the management level, establish the concept of “safety first” and encourage all employees to participate in safety management and improvement. Establish a safety suggestion and reward system to create an environment and atmosphere for open discussion of safety issues. Improve the safety awareness of all employees through safety publicity and education. A positive safety culture can encourage employees to consciously abide by safety regulations.
Technical support and resource guarantee: Invest sufficient resources in the purchase and maintenance of safety equipment, and use advanced safety technology and equipment to improve the level of intrinsic safety. Ensure that safety managers receive professional training and have the necessary safety management capabilities. Establish a safety information sharing platform to promote the exchange of safety experience. Adequate resource guarantee is a necessary condition for the implementation of safety management.
Through the systematic implementation of these safety management strategies, enterprises can establish a comprehensive, dynamic, and continuously improved safety management system, which can not only effectively prevent excavator operation accidents, but also improve work efficiency, reduce downtime and losses caused by safety accidents, and create a safe and efficient working environment.
Emergency handling process for excavator safety accidents
Even if comprehensive preventive measures are taken, safety accidents may still occur. Establishing an effective emergency handling process is the key to reducing accident losses. The following is the standard emergency handling process when an excavator safety accident occurs:
Emergency response and on-site control: After discovering the accident, the first witness should immediately notify the on-site person in charge and relevant personnel, and stop all related operations to ensure that no secondary injuries will be caused. According to the type of accident, quickly cut off the relevant power supply, fuel or hydraulic system, assess the safety of the scene, and ensure the safety of the rescuers. If necessary, evacuate non-essential personnel from the dangerous area, and set up a cordon to prevent irrelevant personnel from entering the accident area.
Rescue and medical assistance for the injured: Quickly assess the condition of the injured, determine the severity of the injury, and perform necessary emergency treatment on the injured, but avoid blindly moving the injured who may have spinal injuries. Call a professional medical rescue team, provide accurate location and injury information, and assign someone to guide the rescuers to the scene. Save the personal belongings and documents of the injured, and prepare follow-up medical information. Life safety is always the primary consideration for emergency treatment.
Site protection and evidence collection: Protect the accident site and do not move or change the site status at will, which is crucial for subsequent accident investigation. Take photos or videos of the scene to record the environment and equipment conditions when the accident occurred. If it involves the leakage of hazardous materials, take control measures in time to prevent the expansion of pollution. Collect equipment operation records, maintenance logs and other documents related to the accident to provide necessary information support for the accident investigation.
Accident reporting and information notification: Report the accident to the superior department and relevant regulatory agencies in accordance with the prescribed procedures, and provide accurate information on the time, location, casualties and equipment losses of the accident. Preliminary analysis of the cause of the accident, but avoid uninvestigated speculation. Notify affected parties, such as customers, partners, etc. Arrange a dedicated person to communicate with the media and the public to ensure that the information is accurate and consistent, and avoid panic or misunderstanding caused by false information.
Accident investigation and root cause analysis: Set up an investigation team, including safety experts, technicians and managers, to collect evidence, including equipment records, operation logs, eyewitness testimonies, etc. Analyze the direct and root causes of the accident and evaluate the defects and deficiencies of the existing safety management system. Write a detailed accident investigation report, including facts, analysis and conclusions. A thorough accident investigation is the basis for improving safety management and preventing similar accidents from happening again.
Implementation of recovery and improvement measures: Develop equipment repair and work recovery plans, implement necessary safety improvement measures, and prevent similar accidents from happening again. Retrain relevant personnel or strengthen safety awareness education, and revise safety operating procedures and emergency plans. Track the implementation effect of improvement measures to ensure continued effectiveness. Learning from mistakes and improving is the core concept of safety management.
Experience sharing and safety culture reinforcement: Incorporate accident cases and lessons into safety training materials, share accident experiences within the company, and improve the safety awareness of all employees. Participate in industry safety information exchanges to help other organizations prevent similar accidents. Review accident cases regularly, maintain safety vigilance, and continuously evaluate and improve the safety management system. Experience sharing can transform the lessons of an accident into safety wealth for the entire industry.
Effective emergency handling can not only reduce the direct impact of the accident, but also learn from the accident and continuously improve safety management. Every accident, no matter how big or small, should be seen as an opportunity to improve safety, not just a problem to be dealt with. Through systematic emergency management and experience summary, the safety level of excavator operations can be continuously improved.
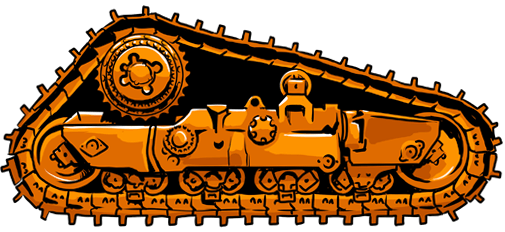
Summary: The road to continuous improvement in excavator safety work
The professional quality of operators is the cornerstone of safety work. Qualified operators not only need to master technical operation skills, but also need to have a strong sense of safety and responsibility. Establishing a systematic training system, including theoretical learning, practical operation and regular retraining, is an effective way to improve the quality of operators.
The comprehensive implementation of preventive measures is the key to reducing the risk of accidents. From equipment inspection before work, to safe operating procedures during operation, to management and control of the working environment, every link cannot be ignored. It is especially important that when operating an excavator, in order to prevent workers from being hit by the boom, safety measures should be taken such as rotating the boom at a safe speed, adding fences to prevent workers from entering the operating range, and supervising the operator and workers to ensure that they comply with safety measures.
The effective operation of the safety management system is the guarantee for the sustainable development of safety work. A clear responsibility system, scientific risk management, unimpeded communication channels and strict supervision and inspection together constitute the basic framework of safety management. Establishing a positive safety culture and making safety a conscious action for everyone is the highest level of safety management.
Improving emergency response capabilities is an important means to reduce accident losses. Even the most perfect safety system cannot completely eliminate the risk of accidents. Therefore, it is necessary to establish an effective emergency plan and conduct regular drills to ensure that rescue and disposal work can be carried out quickly and orderly when an accident occurs, so as to minimize casualties and property losses.
With the continuous development of mechanical technology and safety management concepts, the safety of excavator work is also continuously improving. New safety technologies such as intelligent anti-collision systems and remote monitoring systems are constantly being applied in practice, providing new technical support for safety work. At the same time, the concept of safety management is also changing from passive response to active prevention, and from simple rule compliance to safety culture construction.
Hızlı ve ücretsiz bir teklif alın | E-posta: henry@gfmparts.com | Whatsapp: +86 17705953659 |
Bir profesyonel olarak ekskavatör alt takım parçaları üreticisi, GFM not only pays attention to the performance and quality of products, but also attaches more importance to the safety performance of products. We believe that only by integrating safety into the entire process of design, production and use can the safety and reliability of excavator work be truly realized.
Safety is an eternal theme that requires us to continue to learn, explore and practice. Let us work together to make unremitting efforts to build a safer working environment and escort the safety of every excavator operator and engineering builder.
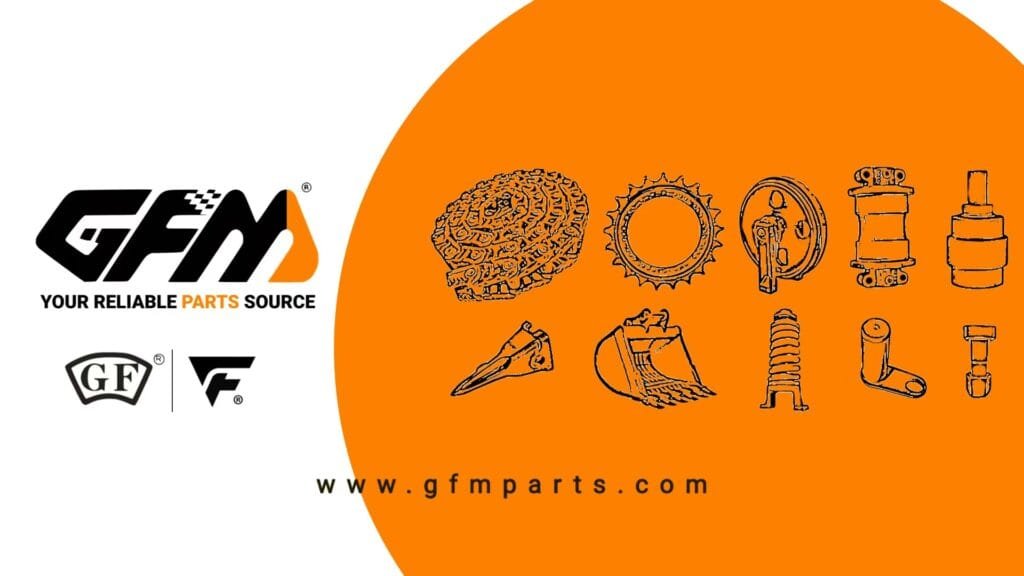