Material analysis of excavator track bolts: Why is high-strength alloy steel the first choice?
Mainstream material types
- Carbon steel: economical choice, suitable for low-load parts (such as cover fixing).
- Alloy steel: add chromium and molybdenum elements, tensile strength ≥1200MPa, used for high-stress parts such as walking mechanism and slewing bearing.
- Stainless steel: strong corrosion resistance, suitable for humid or salty environment (such as coastal operating equipment).
Yüzey işleme süreci
- Dacromet coating: salt spray resistance for more than 1000 hours, rust prevention ability is better than ordinary galvanizing.
- Hot-dip galvanizing: low cost, suitable for conventional working conditions.
- Phosphating treatment: improve lubricity and reduce assembly friction.
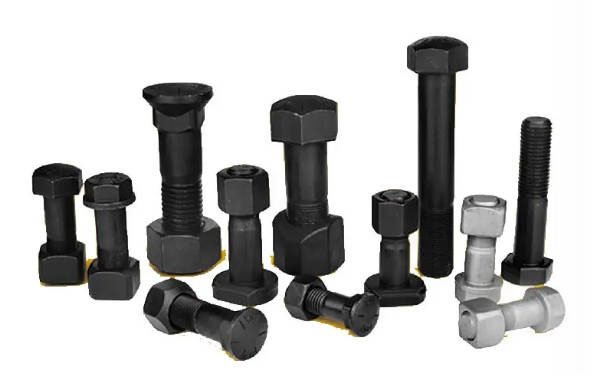
Bolt and nut quality identification: 5 steps to identify inferior accessories
Appearance inspection
- Genuine: clear laser engraving (brand LOGO + strength level), thread without burrs.
- Counterfeit: ink printing is easy to fall off, thread spacing is uneven.
Sertlik testi
- Using Rockwell hardness tester, the hardness of 10.9 grade bolts must reach HRC32-39.
Salt spray test report
- Suppliers are required to provide third-party test reports (such as SGS certification).
Data support
- GFM bolts can withstand 1200 hours of salt spray test (the average of peers is 800 hours)
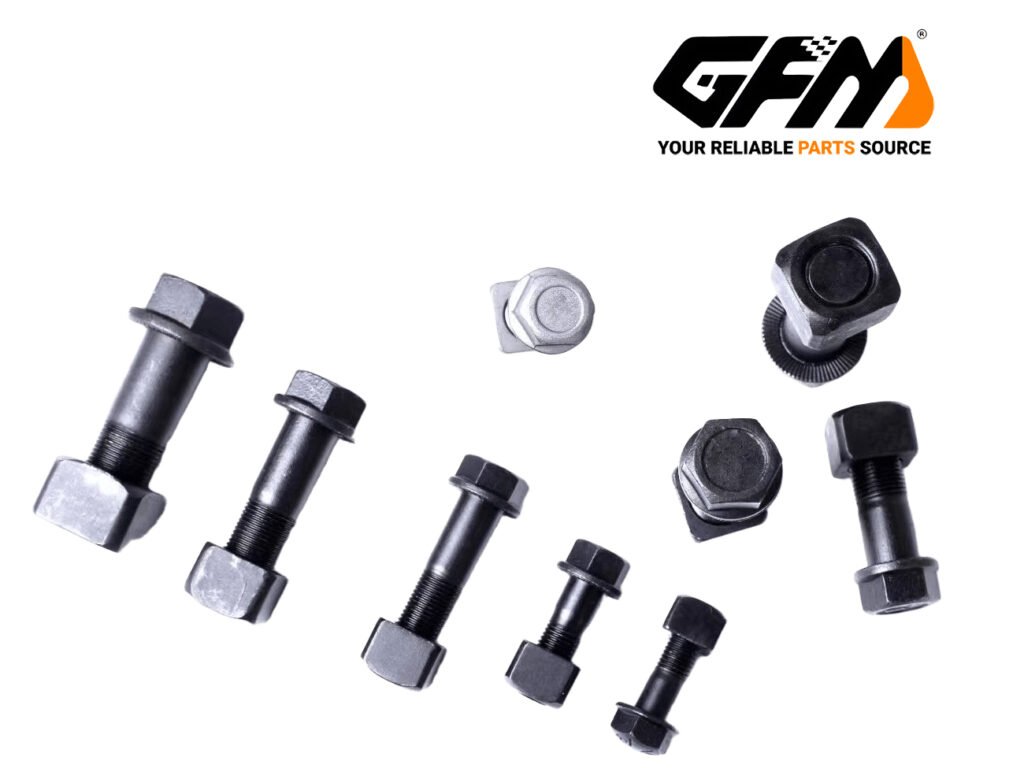
Bolt and nut classification specifications and corresponding application parts
Bolt type | Application part | Torque requirement |
Hexagon head bolt | Engine bracket, track shoe connection | 980-1200N·m |
Flange bolt | Slewing bearing mounting seat | 1500-1800N·m |
T-bolt | Cab floor fixing | 160-200N·m |
Tip: The chassis bolts of Komatsu PC200 and Caterpillar 320 cannot be mixed. The difference in thread angles leads to the risk of bite failure!
How to choose bolts and nuts correctly? Four principles of working condition matching
Vibration level matching
- Lock nuts with nylon locking rings must be used in high-frequency vibration parts (such as breaker hammer connections).
Preload calculation
- Formula: T=K×D×F
- (T=torque, K=friction coefficient 0.2, D=bolt diameter, F=preload)
Extreme environment response
- Mining equipment: Dacromet bolts with a coating thickness of ≥8μm are preferred.
- Alpine areas: Materials with a low-temperature impact energy of -50℃ ≥27J are required.
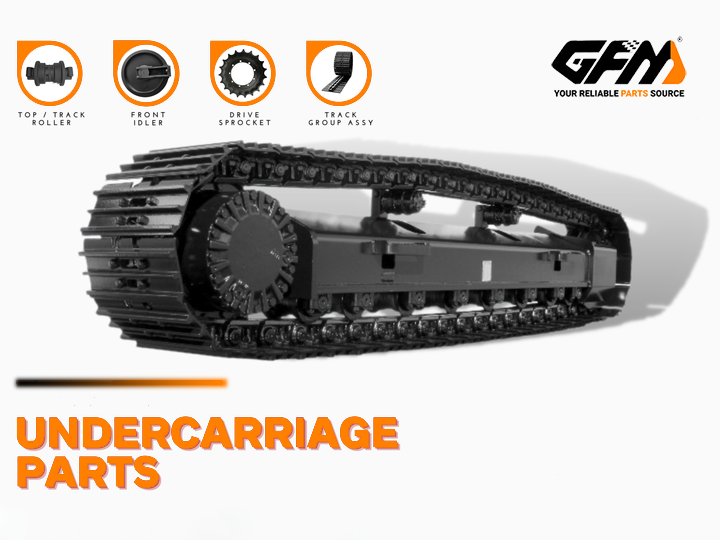
Frequently Asked Questions
Q1: Is bolt breakage a quality problem or an installation problem?
A: According to ISO 898-1, 80% of breakages are caused by loosening fatigue caused by insufficient preload.
Q2: Can ordinary bolts be used to replace original parts?
A: Wrong! Non-standard bolts may cause stress concentration and cause cracking of structural parts.
Hızlı ve ücretsiz bir teklif alın | E-posta: henry@gfmparts.com | Whatsapp: +86 17705953659 |
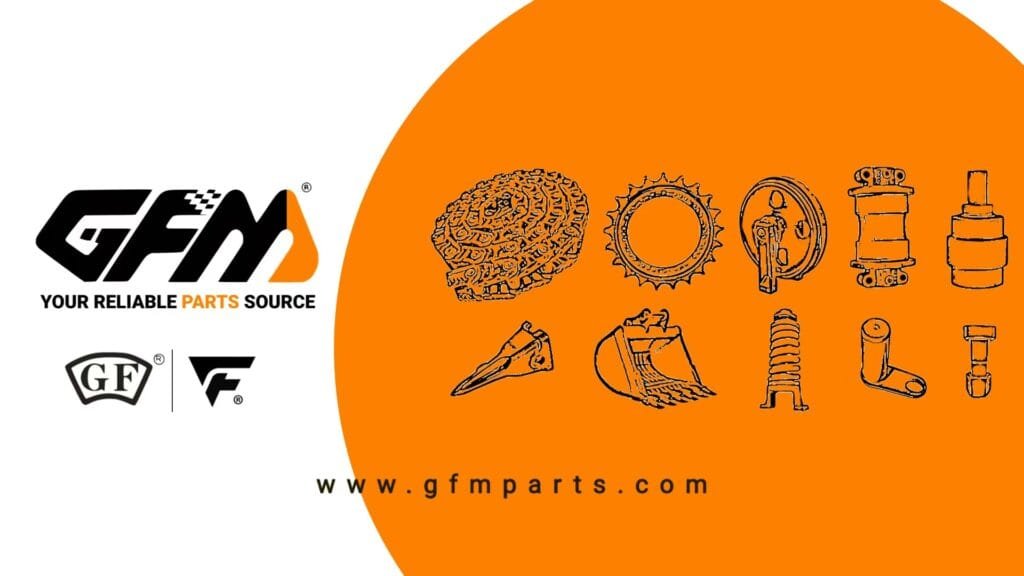