Ağır makine ve ekipmanlarda, buldozerin alt takım sistemi, tüm aracın çalışma ve işlevinin temeli ve çekirdeğidir. İster fabrika dolumu, ister su tasarrufu veya ağır nakliye işlemleri olsun, alt kapak her zaman baskın bir şekilde hareket eder. Ancak, buldozer alt takım parçaları, buldozerdeki en kolay aşınan ve hasar gören bileşenlerdir ve aynı zamanda birçok operatörün yeterince dikkat etmediği bir parçadır.
İçindekiler
Buldozer iniş takım sistemini anlayın
Buldozer alt takım parçalarının bileşimi
Buldozer şase parçaları temel olarak beş bölümden oluşur:
- Palet gergisi: İtme işlevini tamamlar ve yürüyüş takımının kalbidir.
- Palet zinciri: Tüm parçaları birbirine bağlar ve güç kanalına dönüşür.
- Zincir dişlisi: Kayış zincirini aşağıya doğru iter ve üst zincir halkasını iter.
- Kılavuz silindir: Kayış zincirinin büzülmesini sağlamak ve eksenel konumlandırmayı gerçekleştirmek için kullanılır.
- Alt silindir: Aracın tüm ağırlığını taşıyan ve en çok aşınan parçadır.
Bu bileşenler, tıpkı insan vücudunun kemikleri ve eklemleri gibi, çalışırken komple bir alt takım yüksek basınçlı hareket sistemi oluşturur. Herhangi bir parçadaki herhangi bir sorun, tüm aracın arızalanmasına neden olabilir.
Alt takım aşınması yaygındır
Şasi sistemi uzun süre kil, çimento, kum, çakıl, fırınlar ve ağır basınçlı yollarda çalıştığı için, aşınma, kolon darbesi ve yağmur suyu nedeniyle sıklıkla kirlenir. Güç şaftının çalışmasıyla birlikte, gerilim ve ısı enerjisi keskin bir şekilde artarak silindir aksının hızla aşınmasına neden olur. Günlük bakım yapılmazsa, küçük bir sorun binlerce yuan gibi düşük bir maliyete yol açabilir.
GFM Buldozer Alt Takım Parçaları Üreticisi
İnşaat sektöründe buldozerler hayati önem taşıyan ekipmanlar haline gelmiştir ve alt takım bileşenlerinin kalitesi, ekskavatörlerin performansını ve iş verimliliğini doğrudan etkilemektedir. Profesyonel bir buldozer alt takım parçaları Üretici GFM, iş verimliliğinizi artırmanıza ve bakım maliyetlerinizi düşürmenize yardımcı olmak için bir dizi yüksek kaliteli, dayanıklı, yüksek performanslı şasi parçası sağlar.
Kalite mi arıyorsunuz? buldozer parçaları En iyi fiyata mı? Doğru yerdesiniz. Müşterilerimize mükemmel ürünler sunmaya ve en iyi değeri sunmaya kararlıyız. Memnuniyetiniz bizim motivasyonumuzdur. E-posta gönderin henry@gfmparts.com Şimdi buldozer alt takım uzmanlarımız size hizmet vermekten mutluluk duyacaktır.
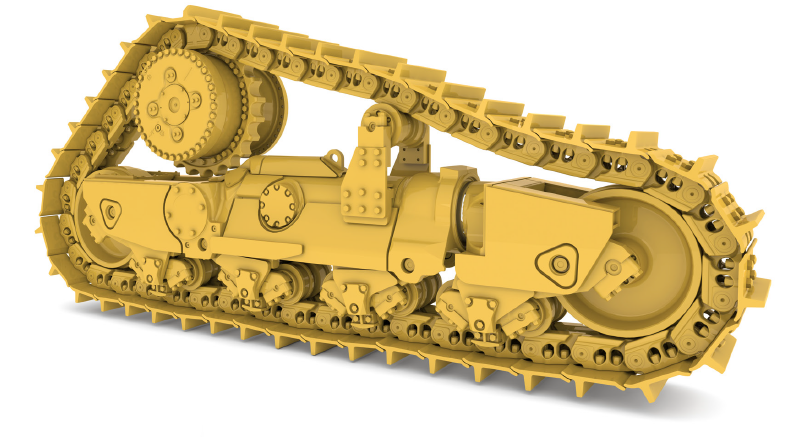
Buldozer alt takım parçalarının günlük bakımı ve onarımı
İnşaat makineleri alanında, buldozerin alt takım sistemi bir insanın "ayakları" gibidir. Tüm ekipmanın ağırlığını taşır ve engebeli arazi ve karmaşık ortamın neden olduğu büyük aşınma ve darbeleri taşır. Günlük bakım yapılmazsa, alt takım parçalarındaki sorunlar yalnızca iş verimliliğini etkilemekle kalmaz, aynı zamanda beklenmedik arızalar ve artan maliyetler gibi ciddi sonuçlara da yol açabilir. Alt kapak parçalarının bilimsel ve düzenli bakımı, ekipmanın uzun vadede istikrarlı çalışmasının anahtarıdır.
Çalışmadan önce ve sonra kontrol edin
Birçok alt takım parçasının hasarı aniden değil, uzun süreli birikim sonucu meydana gelir. Her gün işe gitmeden önce ve sonra basit bir görsel inceleme yapmak için birkaç dakikanızı ayırmak, erken hasarın yayılmasını etkili bir şekilde önleyebilir. Örneğin:
- Raylarda taş, çamur veya herhangi bir takılma olup olmadığını kontrol edin. Bunlar zamanında temizlenmezse, bu kalıntılar zincir baklası ile dişli arasına sıkışarak gereksiz sürtünmeye neden olur.
- Palet makarası, alt silindir ve kılavuz silindiri çevresinde anormal yağ lekeleri olup olmadığını kontrol edin. Yağ sızıntısı belirtileri varsa, bu durum iç conta halkasının eskidiğini veya yatağın hasar gördüğünü gösterebilir ve bu sorun en kısa sürede giderilmelidir.
- Silindirin gevşek olup olmadığına, anormal bir eğim veya belirgin bir sallanma olup olmadığına dikkat edin; bu, gevşek bağlantı elemanlarının, hasarlı braketlerin vb. erken bir işareti olabilir.
- Rayları hafifçe iterek gerginliğini hissedin. Çok sıkı olması parçaların zorlanmasına, çok gevşek olması ise kolayca raydan çıkmasına veya zincirin atmasına neden olur.
Bu inceleme maddeleri basit görünebilir, ancak sorunları önceden tespit etmenize ve büyük onarımlara yol açabilecek hasarları önlemenize yardımcı olabilir.
Düzenli olarak temizleyin
Buldozerler genellikle çamur, çakıl ve kırık tuğla gibi karmaşık ortamlarda çalışır ve şasi parçaları kolayca çamur ve çakılla kaplanır. Bu kirlilikler zincir ile silindir arasına uzun süre yapışırsa, metal yüzeyi "zımpara kağıdı" gibi sürekli olarak parlatır ve parçaların aşınmasını hızlandırır.
Bu nedenle, her çalışmadan sonra şasinin yüksek basınçlı su tabancasıyla iyice durulanması çok önemlidir. Özellikle yağmurlu günlerde veya sığ sularda çalıştıktan sonra, paslanmayı, sıkışmayı veya donmayı önlemek için zamanında temizlenmeli ve kuru tutulmalıdır.
Ayrıca, dişli çark ile alt silindir arasında genellikle ince çakıl birikir ve bu da silindirin dönüşünü kolayca engelleyebilir. Parçaların esnekliğini korumak için, her temizlikten sonra kalan kalıntıları bir tornavida veya tahta bir çubuk kullanarak nazikçe temizlemeniz önerilir.
Yağlama ve bakım
Alt takım parçalarındaki aşınma ve yıpranmanın çoğu, kalitesizlikten değil, yağlama eksikliğinden kaynaklanır. Palet makarası, zincir dişlisi ve alt silindir, rulmanlar, yağ keçeleri, burçlar ve diğer bileşenlerden oluşur. Bu parçaların, metal ile metal arasındaki doğrudan teması azaltmak, sıcaklık artışını ve uzun süreli çalışma sırasında sürtünmeyi azaltmak için greslenmesi gerekir.
Farklı ortamların yağlamaya yönelik farklı gereksinimleri vardır:
- Kumlu ve tozlu bir inşaat ortamında gres, tozla kolayca karışır ve yağlama etkisini kaybeder.
- Yüksek sıcaklıktaki çalışma alanlarında yağın seyrelmesi ve kaybolması kolaydır.
Bu nedenle, ortama göre düzenli olarak yeni gres eklenmeli, ne çok fazla ne de çok az olmalıdır. Ayda bir kontrol etmek daha güvenilir bir sıklıktır, özel ortamlarda ise daha sık kontrol edilmelidir.
Yağlama yaparken, eski yağ dışarı atılana kadar gres memesinden gres girmesini sağlamak için özel bir gres tabancası kullanmaya dikkat edin. Bu, iç boşluğun doldurulduğu ve yağlamanın gerçekten etkili olduğu anlamına gelir.
Ray gerginliği
Paletin makul bir gerginlik durumunda olup olmadığı, tüm makinenin dengesini ve stabilitesini doğrudan etkiler. Palet çok gevşekse, dönüş, tırmanma ve diğer eylemler sırasında paletin kayması kolaydır. Çok sıkıysa, her zincir halkası gergin durumdadır ve bu da zincir piminin kolayca kırılmasına ve uzun vadede alt silindirin aşınmasının artmasına neden olur.
Deneyimli operatörler, sıkılığın uygun olup olmadığını genellikle palet eğiminin eğimine göre değerlendirir. Paletin ortası hafifçe eğimli olsa da, genellikle normal olan zeminde sürüklenmez. Emin değilseniz, üreticinin sağladığı standart ölçüm yöntemiyle de ayarlayabilirsiniz. Ayarlama yaparken kaba kuvvet kullanmayın, gerdirme silindiri veya vida ayar mekanizmasını kullanarak işlemi yavaş ve dikkatli bir şekilde tamamlayın.
Yeni bir palet veya zincir halkası değiştirildiğinde, stabiliteyi sağlamak için gerginliğin yeniden ayarlanması ve bir süre çalıştıktan sonra tekrar kontrol edilmesi gerektiğini hatırlatmakta fayda var.
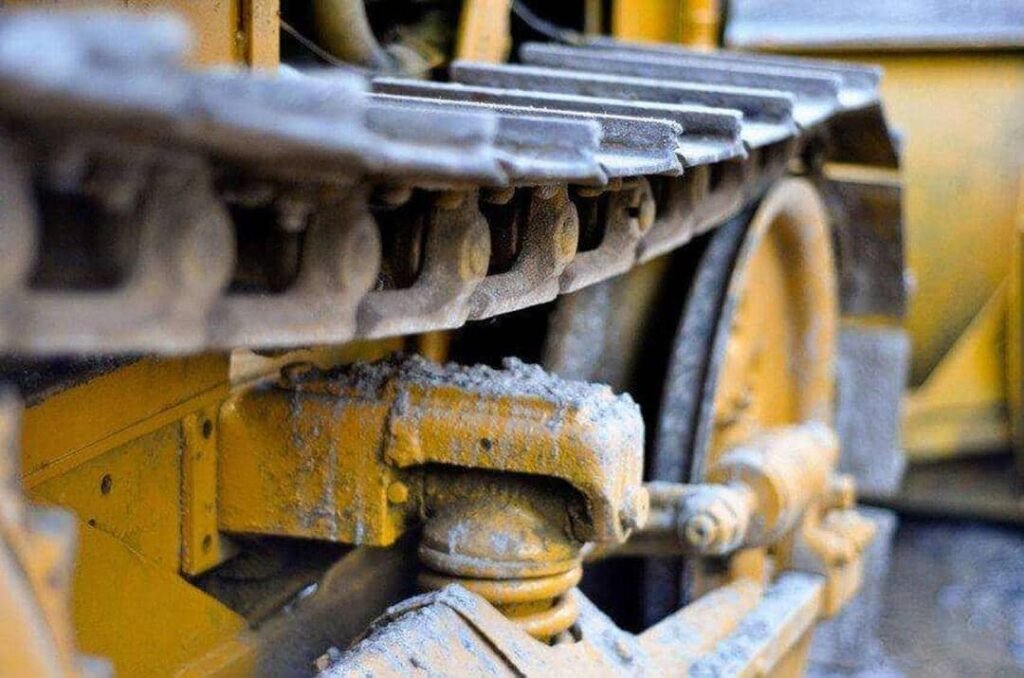
Farklı çalışma koşullarında bakım odağı
Buldozerin alt takım parçaları yapı olarak benzer olsa da, karşılaştıkları çalışma ortamı büyük ölçüde farklılık gösterebilir ve bakım yöntemleri de farklı olmalıdır:
Madenler gibi ağır yük koşullarında:
Şasi sık sık kayalardan etkilenecektir ve silindirler ile braketler çok kolay deforme olup aşınabilir. Bu durumda, yüksek mukavemetli çelik, entegre dövme yapı gibi güçlendirilmiş malzemeler kullanılması ve silindir gövdesinin kalınlığının artırılması önerilir. Günlük kullanımdan sonra çatlak ve deformasyon olup olmadığını kontrol etmek, özellikle braket ve silindir aksının merkezleme hassasiyetinin ofset olup olmadığına dikkat etmek çok önemlidir.
Bataklık veya sulak alan ortamlarında:
Islak çamur, palet ve silindir gövdesini kolayca sararak parçaların dönmesini engelleyebilir ve hatta tüm makinenin batmasına neden olabilir. Bu tür ortamlarda, zeminle temas alanını artırmak için genişletilmiş palet pabuçları kullanılmalı ve çamur birikimini azaltmak için çamur kazıyıcılar takılmalıdır. İşlemden sonra, metal parçaların paslanmasını önlemek için paletler hemen temizlenmeli ve iyice kurutulmalıdır.
Yüksek sıcaklık plato alanlarında:
Metal yüksek sıcaklıklarda genleşir, gres inceltir ve parçaların aşınma oranı önemli ölçüde artabilir. Bu durumda, yüksek sıcaklık gresinin kullanılması ve yağlama durumunun sık sık kontrol edilmesi gerekir. Silindirlerin sıcak olduğu veya hafif bir yanık kokusu olduğu tespit edilirse, yağlama yetersiz demektir ve makine derhal durdurulup kontrol edilmelidir.
Parça değişimi için karar kriterleri
Birçok kullanıcı "bozulduklarında değiştirmeye" alışkındır, ancak buldozerler genel mekanik ekipmanlardan farklıdır. Alt takım sistemleri arızalandığında, genellikle tüm ekipmanın durmasına ve hatta inşaatın ilerlemesinin etkilenmesine neden olur. Bu nedenle, alt kapak parçalarını değiştirmek için makul süreyi bilmek çok önemlidir.
Aşağıdaki durumlar parçaların değiştirilmesi gerekebileceğini gösterir:
- Palet pabuçlarında belirgin çatlaklar veya deformasyonlar mevcut olup, bağlantı parçaları gevşek olup, genel yapıyı etkilemektedir.
- Palet makarasının dişleri keskinleşir, silindir gövdesi incelir ve anormal sesler oluşur.
- Zincir halkaları gevşektir, zincir pimleri artık sağlam bir şekilde bağlanamaz ve kaynak onarım etkisi iyi değildir.
- Dişli veya alt silindir düzgün dönmüyor ve sallanma veya anormal ses var.
- Ray silindiri ofsetlidir ve ray ile hizalanamaz, bu da çalışma sırasında sık sık raydan çıkmaya neden olur.
Bu olguları hafife almayın. Parçalarda arıza meydana geldiğinde, bu durum doğrudan inşaatın aksamasına yol açacak ve bakım ve işçilik maliyetleri büyük ölçüde artacaktır.
GFM buldozer alt takım parçaları: yüksek yoğunluklu çalışma koşulları için tasarlandı
Deneyimli bir kişi olarak alt takım parçaları tedarikçileriGFM, buldozer kullanıcılarının temel taleplerinin farkındadır. Sağladığımız alt kapak parçaları, tasarım açısından gerçek uygulama senaryolarına daha yakın olmakla kalmayıp, aynı zamanda malzeme seçimi, işleme teknolojisi, montaj doğruluğu ve diğer konularda da mükemmelliği hedeflemektedir.
- Malzeme: Yüksek manganezli çelik ve yüksek karbonlu çelik gibi aşınmaya dayanıklı alaşımlar kullanıyoruz ve mukavemeti ve tokluğu arttırmak için ikincil ısıl işleme tabi tutuyoruz.
- İşlem: CNC işleme, her bir parçanın tüm makinenin çalışma gereksinimlerini tam olarak karşılamasını sağlamak için kullanılır.
- Güçlü uyum yeteneği: İster küçük bir buldozer, ister bir sulak alan makinesi, isterse madenciliğe adanmış büyük ölçekli bir ekipman kullanın, GFM özelleştirilmiş yürüyüş takımı parçaları çözümleri sağlayabilir.
- Hızlı servis yanıtı: yeterli stok, hızlı teslimat ve dünya çapında parça eşleştirme hizmetleri için en uygun yer.
Hızlı ve ücretsiz bir teklif alın | E-posta: henry@gfmparts.com | Whatsapp: +86 17705953659 |
Şasi parçaları, buldozerin temelini oluşturur. Buldozerin dengeli yürüyüp yürüyemeyeceğini, verimli çalışıp çalışamayacağını ve kritik anlarda zincirden düşüp düşmeyeceğini belirlerler. Günlük bakımını iyi yapmak zor değildir ve pahalı ekipman veya aletler gerektirmez. Sadece biraz titiz gözlem ve ekipmana karşı sorumlu bir tutum gerektirir.
Şasiyi ekipmanın "ilk savunma hattı" olarak gördüğünüzde ve bilimsel bakım alışkanlıklarına bağlı kaldığınızda, daha az arıza, daha uzun ömür ve daha düşük maliyetlerle güveninizi kazanacaktır. Ekipmanın gerçek anlamda "ayaklarının yere basmasını" ve yüksek yoğunluklu, yüksek frekanslı ve yüksek yüklü mühendislik operasyonlarında etkinliğini sürdürmesini sağlamak için bilimsel ve sistematik bir bakım, inceleme, yağlama ve ayarlama işlemlerinin yapılması gerekir.
Yüksek kaliteli alt takım parçalarının seçilmesi, bilimsel bakım planlarının uygulanması ve zamanında onarım ve değişim yapılması, buldozerinizin işletme maliyetlerini düşürecek, kullanım ömrünü uzatacak ve daha yüksek işletme verimliliği sağlayacaktır. GFM ayrıca, istikrarlı, verimli ve kalıcı işletme garantileri oluşturmak için küresel mühendislik makinesi kullanıcılarıyla birlikte çalışmaya isteklidir.
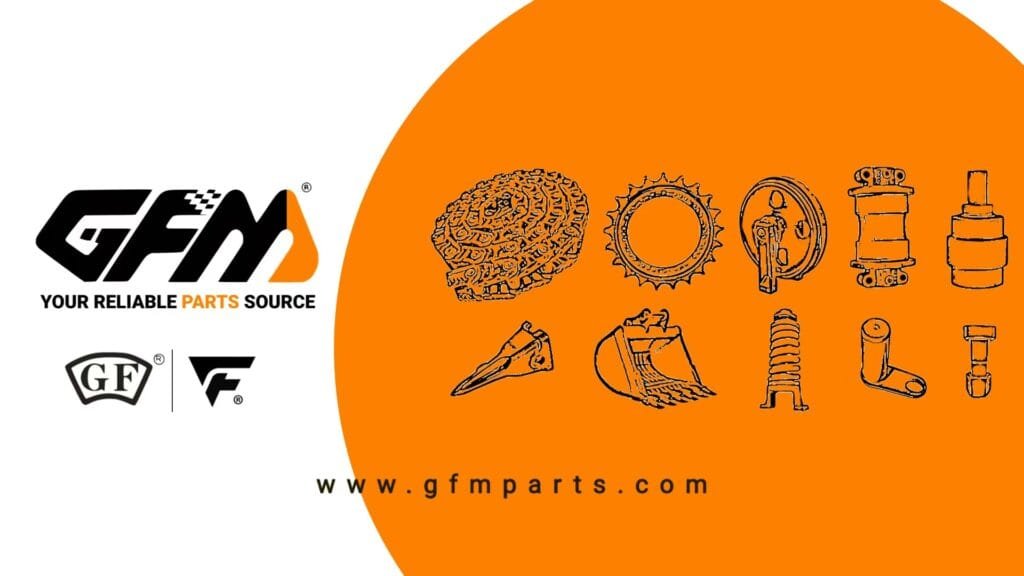